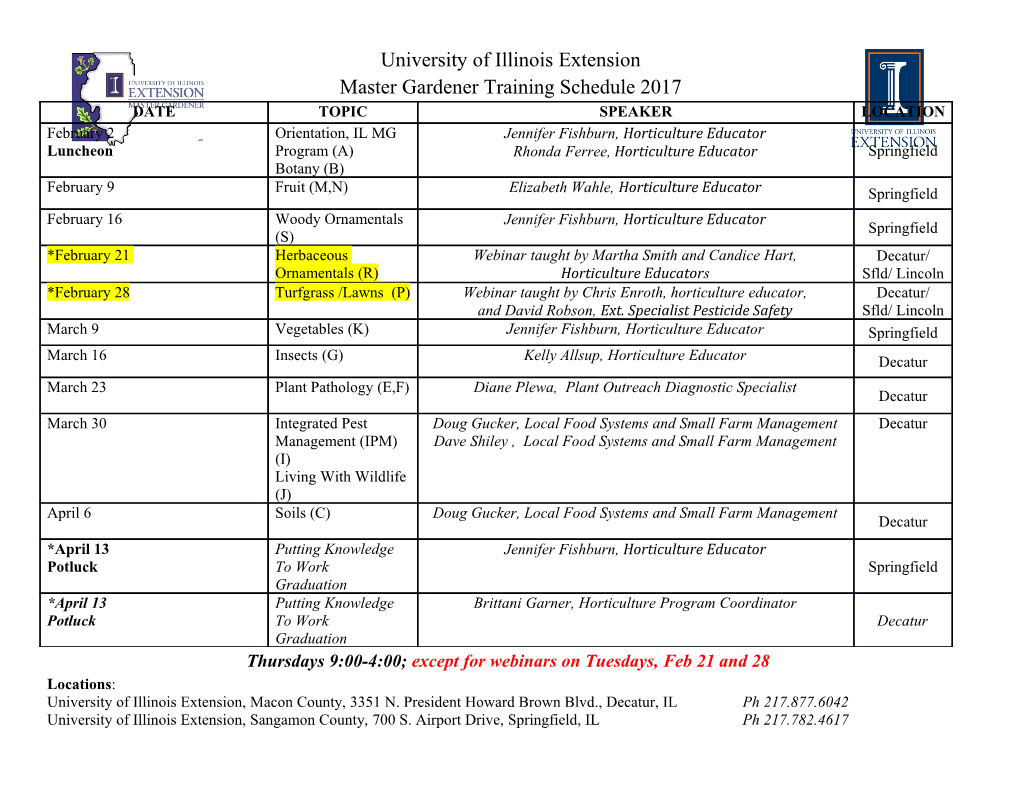
Feasibility Study of Spatial-Phase-Locked Focused-Ion-Beam Lithography by Anto Yasaka M.Eng., Nuclear Engineering, Tokyo Institute of Technology, 1983 B.S., Applied Physics, Tokyo Institute of Technology, 1981 Submitted to the Department of Materials Science and Engineering in partial fulfillment of the requirements for the degree of Master of Science in Materials Science and Engineering at the MASSACHUSETTS INSTITUTE OF TECHNOLOGY June, 1995 © 1995 Massachusetts Institute of Technology. All rights reserved. Signature of Author ............... ...eJ ' ..v.. .............. ....................... Department of Marials Science and Engineering May 12, 1995 Certified by ........................................... Henry I. Smith Professor of Electrical Engineering Thesis Advisor CertifiedC ertifi ed bby........... y ......................................... .. .. A.. Carl V. Sompson II Professor of Electronic Materials Thesis Advisor Accepted by ............................................................................ Carl V. Thompson II Professor of Electronic Materials ;?.: usErrsINSTrbhair, Departmental Committee on Graduate Students OF TECHNOLOGY JUL 2 01995 Sciencp LIBRARIES Feasibility Study of Spatial-Phase-Locked Focused-Ion-Beam Lithography by Anto Yasaka Submitted to the Department of Materials Science and Engineering in partial fulfillment of the requirements for the degree of Master of Science in Materials Science and Engineering Abstract It is known that focused-ion-beam lithography has the capability of writing extremely fine lines (less than 50 nm line and space has been achieved) without proximity effect. However, because the writing field in ion-beam lithography is quite small, large- area patterns must be created by stitching together the small fields. The precision with which this can be done is much poorer than the resolution, typical stitching errors are -100 nm. A spatial-phase-locking method has been proposed to reduce stitching errors and provide both pattern placement accuracy and precision. The fundamental flaw in conventional particle-beam (electron and ion) lithography, which gives rise to most of the stitching error, is that the beam location is not directly monitored. The stage position is monitored via laser interferometer, but the beam location is not. Thus, the beam can drift from its assumed position due to thermal expansion, charging, or any other error sources. The spatial-phase-locking enables direct monitoring of beam location and closed loop beam positioning. Spatial-phase-locking will be done by providing a global fiducial grid on the substrate itself, that is transparent to the exposing beam but which enables a control computer to keep track continuously of the beam location and correct any drift. The grid consisting of a polymer grid pattern on a thin metal film (e.g., 20 nm thick Al) will be created by interferometric lithography, which ensures long-range spatial-phase coherence. As the beam is scanned across the grid pattern the secondary-electron emission is strongly modulated since the secondary yields of Al and polymer differ significantly. This periodic signal is used by the control computer as a beam-position signal against which the pattern writing can be locked. In this study, ion induced electron emission yields from various materials such as Al, Si, and PMMA has been investigated to evaluate the feasibility of spatial-phase-locked focused-ion-beam lithography and to optimize the substrate configuration for ion beams. Thesis advisor: Henry I, Smith Title: Professor of Electrical Engineering Thesis Advisor: Carl V. Thompson II 'Title: Professor of Electronic Materials 2 Acknowledgment I would like to take this opportunity to thank those who have given me the support to carry out this research. First of all, I am indebted to my advisor, Prof. Henry I. Smith, for his invaluable advice and support. I would like to thank my co-advisor, Prof. Carl V. Thompson, for helpful suggestions. I am particularly grateful to Mr. Scott Silverman for helpful suggestions in carrying out this research and for reading the entire manuscript and making a number of critical comments. I am thankful to Mr. Sergey Etchin for his kind assistance in the FIB operation. I am also grateful to Mr. Mark Mondol for providing me with the samples. All members of the NSL staff and students deserve many thanks: Jim Carter, Vincent Wong, Juan Ferrera, Martin Burkhardt, Nitin Gupta, Euclid Moon, Satyen Shah, Tim Savas, Tom Murphy, for their kindness and encouragement. Special thanks go to my employer, Seiko Instruments Inc., for giving me this exciting opportunity to study at MIT. I will always be grateful to my family for all their love and support. I hope to be able to repay them someday. 3 Contents 1 Introduction 9 1.1 Optical Lithography ................................................................ 9 1.2 Electron Beam Lithography ..................................................... 13 1.3 Focused Ion Beam Technology ....................... 16 1.3. 1 Liquid Metal Ion Sources .......................................... 17 1.3. 2 FIB Optics ...... ..... ........................... 18 1.3. 3 FIB Applications . ... ....... .............................................. 22 1.4 Spatial Phase Locking Method ...................................... ........... 28 1.5 Objectives.. ...................... .. .... .........................................32 2 Experiment 3 4 2.1 Focused Ion Beam System ........ ................................... 34 2.2 Secondary Electron Measurement .... ...... ....................................36 2.3 SamplePreparation ............................................................... 37 3 Results and Discussion 39 3. 1 Results on Si Target .. ... .... .... .....................................39 3.2 Results on Al Target . ....... .......................................... ........... 46 3.3 Results on PMMA Target ............. ......................................55 3.4 Feasibility of Detection of a Fiducial Grid .............. ........... 59 3.5 Evaluation of Sputtering and Oxidation Effects on Secondary Electron Em ission........................................................................... 62 4 Summary 6 5 References 66 4 List of Figures 1. 1 Schematic of exposure and development processes using positive and negative resists...................................................................................... 10 1.2 High pressure mercury-arc spectrum .................................................. I11 1.3 Exposure technology roadmap by Semiconductor Industry Association.......... 12 1.4 Schematic of an electron beam lithography system .................................. 14 1.5 Monte Carlo simulation of trajectories of 100 electrons scattered in a 0.4gm PMMA film coated on a silicon substrate ............................................. 15 1.6 Schematic of liquid metal ion source with enlarged view of tip showing liquid pulled into a cusp by the electric field ................................................ 17 1.7 Schematic of the low voltage focusing column without mass separator ........... 19 1.8 Schematic of the high voltage focusing column with mass separator .............. 19 1.9 (a) The calculated current density distribution for a FIB system at two different states of focus [30]. (b) Natural log plot of the measured current density distribution (squares) with Gaussian (center peak) and exponential (tails) fittings ........................................................................................... 21 1.10 Schematics of (a) FIB milling and (b) FIB induced deposition .................... 23 1. 11 SIM image showing channeling contrast of Al grains ............................... 25 1. 12 Illustration of procedure to form cross sectioning by FIB .......................... 26 1.13 Cross sectioning SIM image of microelectronic device ............................. 26 1. 14 A Monte Carlo simulation of the trajectories of ions (50 keV protons) and electrons in PMMA. Note the difference in scale and the fact that the ions scatter far less than electrons .................................................................... 27 1. 15 Exposure characteristics of PMMA and negative novolak resist by ions and electrons. The vertical axis shows the percentage of thickness remaining after development.............................................................................. 27 1. 16 Illustration for explanation of field stitching and three types of stitching errors.. 29 1. 17 Configuration of interferometric lithography system ................................ 31 5 1. 18 (a) Cross-sectional schematic of a global fiducial grid configuration. (b) Top view of the global fiducial grid ................................................................. 32 2. 1. Schematic of focused ion beam system used in this research .... ............. 35 2.2. Typical mass spectrum of ions extracted from Au/Si alloy source ................... 36 2.3. Schematic of the quotient method for secondary electron yield measurement ...... 37 3. 1 Secondary electron yields from Si induced by 120 keV Si2+ as a function of irradiation time. Each line corresponds to a different scanning magnification ..... 40 3.2 Secondary electron yields from Si induced by 180 keV Si2+ as a function of irradiation time. Each line corresponds to a different scanning magnification ..... 41 3.3 Secondary electron yields from Si induced by 240 keV Si2+ as a function of irradiation time. Each line corresponds to a different scanning
Details
-
File Typepdf
-
Upload Time-
-
Content LanguagesEnglish
-
Upload UserAnonymous/Not logged-in
-
File Pages68 Page
-
File Size-