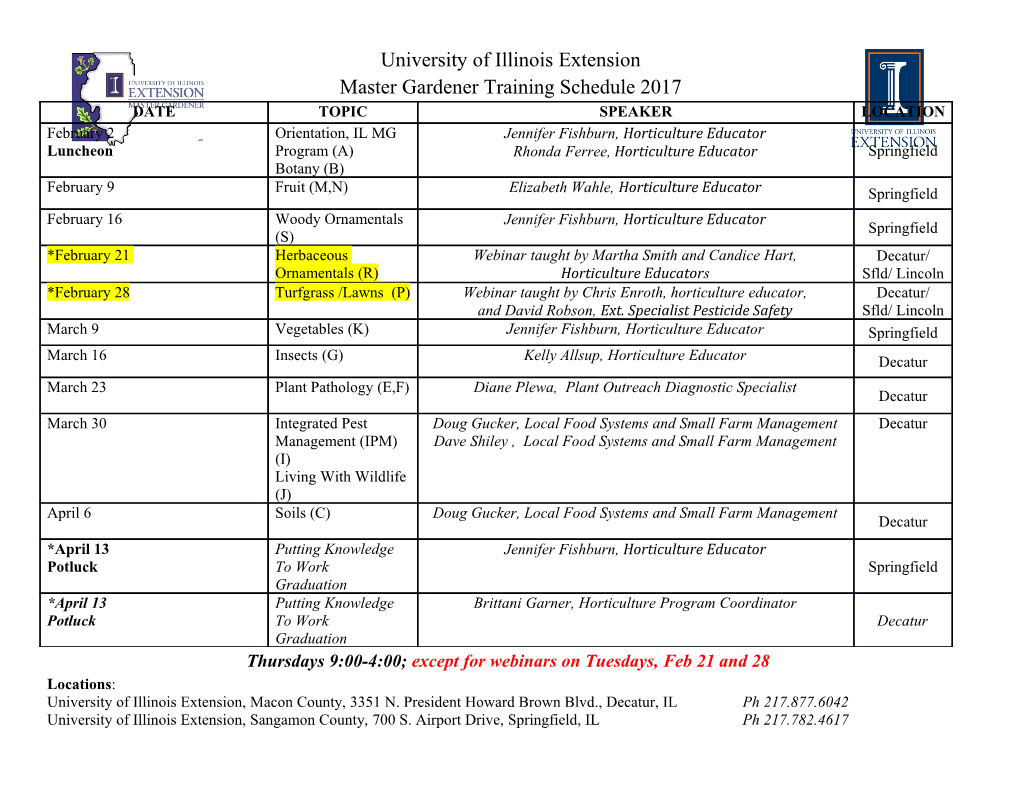
2008:052 CIV MASTER’S THESIS Process Study on Compression Moulding of SMC using Factorial Design Jimmy Olsson MASTER OF SCIENCE PROGRAMME Engineering Physics Luleå University of Technology Department of Applied Physics and Mechanical Engineering Division of Fluid Mechanics 2008:052 CIV • ISSN: 1402 - 1617 • ISRN: LTU - EX - - 08/052 - - SE Preface The work presented in this report has been carried out at SICOMP and in a collaboration with the department of applied physics and mechanical engineering at Lule˚aUniversity of Technology. First, I would like to thank my supervisors, Staffan Lundstr¨omat Lule˚a university of technology, Kurt Olofsson at SICOMP, and Joakim Petterson at ABB Plast. For giving me the opportunity to do this work, and also for giving me support when problem have occurred. I would specially like to thank Ake˚ Westerlund at ABB Plast for all his expertise help, with both theoretical and practical problems. I would also like to thank Kerstin V¨annman at Lule˚aUniversity of tech- nology for a brief explanation about the basics in factorial design. Finally, I would like to thank everybody at SICOMP who have helped me with all kind of problems and also for making my time in Pite˚anice. Jimmy Olsson Pite˚a,2008 I Abstract During compression moulding of sheet moulding compounds, voids are formed that can deteriorate the surface finish of the final product as well as its prop- erties such as the electrical insulation. A large number of processing and material parameters can however be tuned in order to reduce the amount of voids in the final product. There is no profound investigation coupling such parameters to the void content. Hence, factorial design is here used to plan an experimental series where material as well as processing conditions are varied. In particular vacuum assisted compression moulding is used in a circular shaped mould. The experimental series is evaluated by counting the number of surface voids on the plates and by measurement of their electrical insulation. One result is that the latter can be considerably improved by choosing optimal processing conditions. II Contents Preface ................................. I Abstract ................................. II 1 Introduction 1 1.1 Background ............................ 1 1.2 Aim and Objective ........................ 1 1.3 Previous work ........................... 2 1.4 Description of project ...................... 2 1.5 Outline of this thesis ....................... 2 2 Theory 5 2.1 Sheet Molding Compound, SMC ................ 5 2.1.1 Raw materials ...................... 8 2.2 Statistical Design ......................... 9 2.2.1 The 2k Factorial Design ................. 10 2.2.2 Analysis with MODDE ................. 11 2.3 DETECT ............................. 12 2.3.1 Speckle Pattern ...................... 12 2.3.2 Correlation Analysis ................... 13 2.4 High Voltage Insulation Test .................. 13 3 Method 15 3.1 Experiments ............................ 15 3.1.1 Preparing the samples .................. 15 3.1.2 Displacement of charges ................. 15 3.1.3 Vacuum Tool ....................... 17 3.2 Measurements to quantify the quality ............. 18 3.2.1 Surface defects with DETECT ............. 18 3.2.2 Surface defects with painting method ......... 21 3.2.3 Image Analysis of the Weld line ............. 22 3.2.4 Electrical Insulation ................... 23 3.2.5 Microscopic Analysis of Voids .............. 23 3.3 Analysis with MODDE ...................... 24 3.4 Vacuum Treatment of Prepreg ................. 25 4 Results 29 4.1 Effect of air exposion on prepreg ................ 29 4.2 Experimental run 1, Vacuum Assisted Moulding. ....... 29 4.2.1 Factorial design ...................... 29 4.2.2 Results .......................... 31 4.2.3 Comparison of DETECT and Paint .......... 42 4.3 Experimental run 2 ........................ 43 4.3.1 Factorial design ...................... 43 III CONTENTS 4.3.2 Results .......................... 44 4.3.3 Comparison of DETECT and Paint .......... 45 4.4 Experimental run 3 ........................ 46 4.4.1 Factorial design ...................... 46 4.4.2 Results .......................... 46 4.4.3 Comparison of DETECT and Paint .......... 49 4.5 Experimental run 4 ........................ 50 4.5.1 Factorial design ...................... 50 4.5.2 Results .......................... 50 4.5.3 Comparison of DETECT and Paint .......... 52 4.6 The effect of aged prepreg .................... 53 4.6.1 Factorial Design ..................... 53 4.6.2 Results .......................... 54 4.6.3 Comparison of DETECT and Paint .......... 56 4.7 The effect of changing prepreg ................. 57 4.7.1 Factorial Design ..................... 57 4.7.2 Results .......................... 58 4.7.3 Comparison of DETECT and Paint .......... 61 4.8 Microscopical analysis of void contents ............. 62 4.9 Vacuum treatment for prepreg ................. 69 5 Conclusions and Future Work 71 A Appendix 75 A.1 Raw data experimental run 1 .................. 75 A.2 Raw data experimental run 2 .................. 76 A.3 Raw data experimental run 3 .................. 77 A.4 Raw data experimental run 4 .................. 78 A.5 CAD drawing of Vacuum tool .................. 78 IV 1 Introduction 1.1 Background Due to mechanical properties and costs, the use of fibre reinforced polymer composites have increased during the last decades. There exist several meth- ods for manufacturing these materials. One method with potential for large scale productions of lightweight vehicle components is called sheet moulding compound (SMC). One example of SMC-product in the vehicle industry can be seen in figure 1.1. The main reason why it has not come into wider use in the vehicle industry is the unsatisfactory condition of the surface finish. Many improvements of the technique have been made since the beginning in the 1950s; however, some further improvements need to be done. Figure 1.1: Lightweight vehicle component of SMC. 1.2 Aim and Objective The main ambition of this project is to establish the factors that have the highest influence on the quality of the compression moulded SMC product, 1 CHAPTER 1. INTRODUCTION both as independent factors and in combination with other factors, by using factorial design methodology. Secondly, use the recently developed measure- ment tool DETECT, which also is a part of the FYS (F¨orb¨attrade Ytor i SMC-produkter) project, to quantify the condition of the surfaces. Further- more, log the data from the experiments and send them to LTU in order for them to use the data to optimize a CFD-model (Computational Fluid Dynamics)for SMC. 1.3 Previous work Over the years, many have tried to define processing conditions to create ”class A” surfaces for SMC. It is commonly known that vacuum assisted moulding (VAM) is the superior method to create ”class A” surfaces [1][2] [3], but no one of the reports that was found in the literature search had any experimental data which supported their thesis. ”Class A” surface is not strictly defined and depends on several parameters like surface roughness, defects, optical phenomena, etc. The most used instrument for detecting defects in the industry is probably the human eye. Several methods have been developed to provide more quantitative data. The DETECT system, which is a result of previous work carried out at SICOMP, will be used to quantify the quality of the surfaces in this project. Furthermore, method and result from previous experimental work carried out at SICOMP, by Greger Nilsson, in order to decrease void amount in prepreg by means of vacuum assisted prepreg manufacturing, will be presented in this report. 1.4 Description of project In this project the SMC process will be investigated by using factorial design methodology. For analysis and setup of experimental plan, the software MODDE 7.0 will be used. Among the altered factors, the vacuum level inside the moulding tool is probably the most interesting. To quantify the quality of the samples, different techniques will be utilized. The surfaces will be studied with DETECT, image analysis, and simulation of the painting process by using a paint that is not suitable for SMC materials. Hence, defects that should have been hidden with a good coating will in this case create a blowout that is easy to detect with the human eye. An electrical insulting test, developed by ABB Plast, will be used to quantify the material quality of the samples. 1.5 Outline of this thesis First, a theoretical part will be given. Which includes the SMC-process, factorial design, the DETECT tool, and the insulation test. The methods, 2 1.5. OUTLINE OF THIS THESIS including previous experimental studies with vacuum assisted prepreg man- ufacturing, are then presented in the second part. Thirdly, a chapter with experiment descriptions and results, including previous accomplished results with vacuum assisted prepreg manufacturing. Finally, it follows a chapter for discussion and conclusions for the entire project. 3 2 Theory 2.1 Sheet Molding Compound, SMC SMC is a compression moulding process where the material used is SMC prepreg, which contains fibres, resin and additives. The basic idea behind SMC is simple, but the whole process from raw materials to a finished prod- uct is very complex. First, the prepreg can be created in numerous ways by varying the raw material setup. Hence, different properties can be achieved in the created SMC product. One example is fire retardant products. Sec- ondly, the properties of the prepreg are changed in
Details
-
File Typepdf
-
Upload Time-
-
Content LanguagesEnglish
-
Upload UserAnonymous/Not logged-in
-
File Pages84 Page
-
File Size-