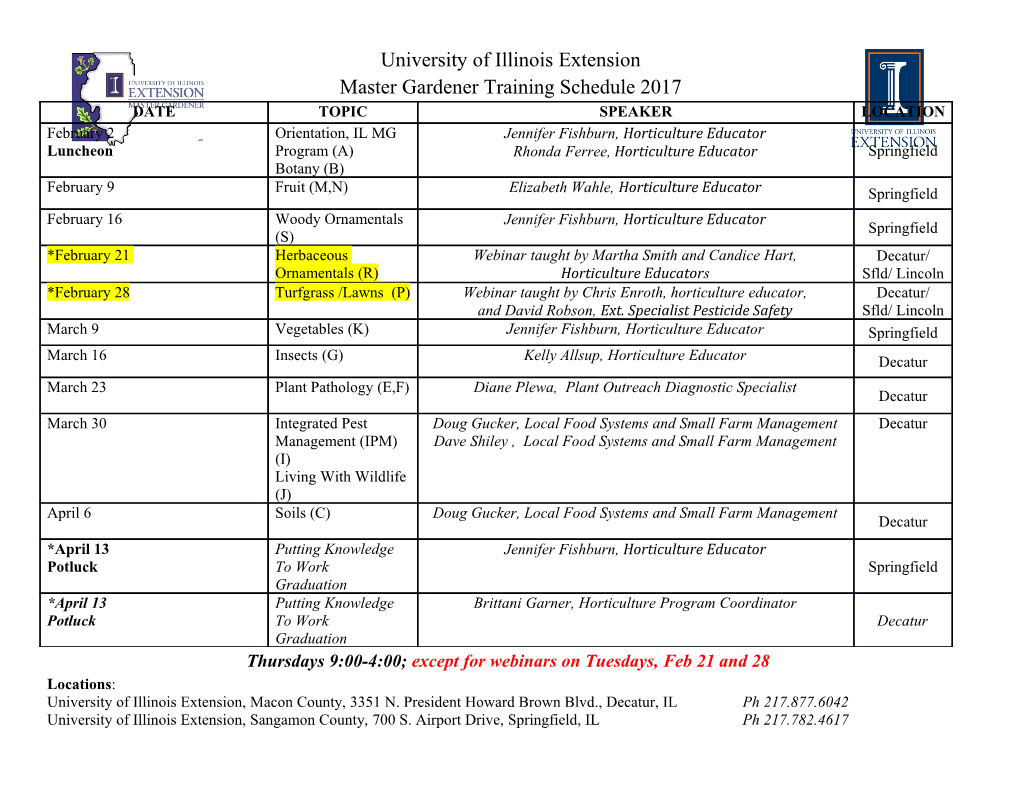
catalysts Article Microwave-Assisted Homogeneous Acid Catalysis and Chemoenzymatic Synthesis of Dialkyl Succinate in a Flow Reactor Laura Daviot 1, Thomas Len 1, Carol Sze Ki Lin 2 and Christophe Len 1,3,* 1 Centre de Recherche de Royallieu, Université de Technologie Compiègne, Sorbonne Universités, Cedex BP20529, F-60205 Compiègne, France; [email protected] (L.D.); [email protected] (T.L.) 2 School of Energy and Environment, City University of Hong Kong, Tat Chee Avenue, Kowloon Tong, Hong Kong, China; [email protected] 3 Institut de Recherche de Chimie Paris, PSL Research University, Chimie ParisTech, CNRS, UMR 8247, Cedex 05, F-75231 Paris, France * Correspondence: [email protected]; Tel.: +33-144-276-752 Received: 12 February 2019; Accepted: 8 March 2019; Published: 16 March 2019 Abstract: Two new continuous flow systems for the production of dialkyl succinates were developed via the esterification of succinic acid, and via the trans-esterification of dimethyl succinate. The first microwave-assisted continuous esterification of succinic acid with H2SO4 as a chemical homogeneous catalyst was successfully achieved via a single pass (ca 320 s) at 65–115 ◦C using a MiniFlow 200ss Sairem Technology. The first continuous trans-esterification of dimethyl succinate with lipase Cal B as an enzymatic catalyst was developed using a Syrris Asia Technology, with an optimal reaction condition of 14 min at 40 ◦C. Dialkyl succinates were produced with the two technologies, but higher productivity was observed for the microwave-assisted continuous esterification using chemical catalysts. The continuous flow trans-esterification demonstrated a number of advantages, but it resulted in lower yield of the target esters. Keywords: continuous flow; dialkyl succinates; homogeneous catalysis; lipase Cal B; succinate 1. Introduction With the depletion of oil-based resources, wood-based biomass and especially plant waste rich in lignocellulosic feedstocks appear to be the main alternatives for the production of platform molecules. Among them, succinic acid (SA) as a linear C-4 dicarboxylic acid is considered as one of the top 12 prospective building blocks derived from sugars by the US Department of Energy. SA is mainly produced via a chemical catalytic route starting from maleic acid and maleic anhydride. The use of furan-derived SA at laboratory-scale using chemical process, as well as via biotechnological process (i.e., by fermentation) have also been studied [1]. SA can be used as a precursor to produce different chemical intermediates [2], such as tetrahydrofuran [3], γ-butyrolactone [4], and 1,4-butanediol [5]. Particularly, SA ester products can be used in the chemical industry as a green solvent, or plastic and fuel additive, as well as in the pharmaceutical and cosmetic industries [6]. Different processes using chemical homogeneous catalysis [7–10], heterogeneous catalysis [11–21], and chemo-enzymatic reaction [22] have been reported in batch process, but few reports have described continuous flow dialkyl succinate synthesis [21,23]. Among the dialkyl succinates with value-added properties, dimethyl-, diethyl-, di-isobutyl-, and dioctyl succinates can be used as green solvents; dibutyl-, didecyl-, diamyl-, and diisoamyl succinates can be used as plastic and fuel additives; tocopherol, estriol, chloramphenicol, and hydrocortisone succinates as pharmaceutical ingredients; and dipropyl, diethoxyethyl, or diethylhexyl succinates in cosmetic application [1]. Processes for the production of dialkyl succinates in a batch Catalysts 2019, 9, 272; doi:10.3390/catal9030272 www.mdpi.com/journal/catalysts Catalysts 2019, 9, 272 2 of 10 Catalysts 2018, 8, x FOR PEER REVIEW 2 of 11 reactor were developed in 2010 (Table1). Among them, the use of sulfonic acid was the most described [ingredients;8–11,14–17 and], followeddipropyl, diethoxy by carboxylicethyl, or diethylhexyl acid [18] succinates and phosphoric in cosmetic acidapplication [19]. [1]. It is difficult to compareProcesses each result for the since production the processes of dialkyl weresuccinates conducted in a batch inreactor different were developed conditions in 2010 by different(Table groups. 1). Among them, the use of sulfonic acid was the most described [8–11,14–17], followed by Nevertheless,carboxylic the use acid of[18] alcohol and phosphoric as both acid solvent [19]. It isand difficult reagent to compare was each often result in since excess the processes at temperature in ◦ the range ofwere 25–160 conductedC forin different 25 h. Dialkyl conditions succinates by different weregroups. produced Nevertheless, in the yields use of higher alcohol thanas both 66%. Al2O3 was describedsolvent as and a heterogeneous reagent was often catalystin excess at temperat 25 ◦C forure 48in the h forrange the of synthesis25–160 °C for of 25 dimethyl h. Dialkyl ester 2b in succinates were produced in yields higher than 66%. Al2O3 was described as a heterogeneous 70% yield [catalyst20]. Among at 25 °C for the 48 recent h for the reports, synthesis Zhang of dimethyl et al. ester described 2b in 70% yield the continuous[20]. Among the flow recent synthesis of diesters 2a,reports,2b, and Zhang2d in et the al. presencedescribed the of “man-made”continuous flow heterogeneoussynthesis of diesters catalyst 2a, 2b in, and quantitative 2d in the yield [21]. Moreover,presence Fabian of et “man-made” al. described heterogeneous the use ofcatalyst batch in quantitative microwave yield radiation [21]. Moreover, as alternative Fabian et al. tool for the esterificationdescribed of SA the [14 use]. To of thebatch best microwave of our radiation knowledge, as alternative the chemoenzymatic tool for the esterification production of SA [14]. of To diesters 2a–i the best of our knowledge, the chemoenzymatic production of diesters 2a–i using both pure SA (1) using bothand pure pure SA dimethylester (1) and pure 2b as dimethylester reactants has never2b beenas reactants reported. Nevertheless, has never beenDelhomme reported. et al. used Nevertheless, Delhommecrude et al. fermentation used crude broths fermentation produced from broths recombinant produced Escherichia from coli recombinant for the synthesisEscherichia of 2h in the coli for the synthesis ofpresence2h in theof lipase presence Cal B [22]. of lipase Cal B [22]. Table 1. Selected catalysts reported for the conversion of succinic acid (1) to dialkylsuccinates 2. Table 1. Selected catalysts reported for the conversion of succinic acid (1) to dialkylsuccinates 2. Entry Reactor Catalyst Reaction conditionsReaction a 2 YieldYield of 2 (% of) 2 Ref Entry Reactor Catalyst a 2 Ref 1 batch H2SO4 nd:2:110:18Conditions 2g 69 (%) [8] 2 batch H2SO4 nd:2.3:110:18 2f 78 [9] 1 batch H2SO4 nd:2:110:18 2g 69 [8] 3 batch H2SO4 nd:2.3:110:18 2h 70 [9] 2 batch H SO nd:2.3:110:18 2f 78 [9] 4 batch OPP-SO3H-12 4 10:50:70:6 2b 88 [15] 35 batchbatch SS-0.010 H 2SO4 10:2:100:6.5nd:2.3:110:18 2a 2h 94 70[16] [9] 46 batchbatch Glu-TsOH OPP-SO 3H-1100:80:80:4 10:50:70:6 2a 2b 100 88[17] [15] 57 batch b CH3SO3H@Al SS-0.0102O3 332,000:2:80:8 10:2:100:6.5 2b 2a 97 94[14] [16] 68 batch b CH3SO3H@Al Glu-TsOH2O3 332,000:2:80:8 100:80:80:4 2a 2a 97 100[14] [17] 9 batch bb CH3SO3H@Al2O3 332,000:2:80:8 2c 97 [14] 7 batch CH3SO3H@Al2O3 332,000:2:80:8 2b 97 [14] 10 batch bb CH3SO3H@Al2O3 332,000:2:80:8 2i 97 [14] 8 batch CH3SO3H@Al2O3 332,000:2:80:8 2a 97 [14] 11 batch C2(Mim)2HSO4 2:3:60:3 2b 76 [10] 9 batch b CH SO H@Al O 332,000:2:80:8 2c 97 [14] 12 batch C3(Mim)3 2HSO3 4 2 3 2:3:60:3.5 2a 68 [10] b 1013 batchbatch C4(Mim)CH3SO2HSO3H@Al4 2O3 2:4:60:4332,000:2:80:8 2c 2i 74 97[10] [14] 11 batchN-Butyl-2,4-dinitro-anilini C2(Mim)2HSO4 2:3:60:3 2b 76 [10] 14 batch 1:2:99:25 2h 93 [7] 12 batchum p-toluenesulfonate C3(Mim)2HSO 4 2:3:60:3.5 2a 68 [10] 1315 batchbatch nano-SO C4(Mim)4 2-/TiO22 HSO4 5:3:160:22:4:60:4 2g 2c 97 74[11] [10] 16 batch N-Butyl-2,4-dinitro-aniliniumTSA3/MCM-41 0.1:3:80:14 2a 66 [18] 14 batch 1:2:99:25 2h 93 [7] 17 batch TSAp-toluenesulfonate3/MCM-41 0.1:3:80:14 2d 90 [18] 18 batch TPA2/MCM-41 100:3:80:8 2d 68 [19] 15 batch nano-SO4 2-/TiO2 5:3:160:2 2g 97 [11] 19 batch TPA2/MCM-41 100:3:80:8 2f 68 [19] 16 batch TSA3/MCM-41 0.1:3:80:14 2a 66 [18] 20 batch TPA2/MCM-41 100:3:80:8 2h 73 [19] 17 batch TSA /MCM-41 0.1:3:80:14 2d 90 [18] 21 batch Al2O3 50:1.6:25:48 2b 70 [20] 1822 batchflow TPAPIL-A2 /MCM-415:1.2:85:5 100:3:80:8 2b 2d 100 68[21] [19] 1923 batchflow TPAPIL-A2 /MCM-415:1.2:87:4 100:3:80:8 2a 2f 100 68[21] [19] 2024 batchflow TPAPIL-A2 /MCM-415:1.2:100:3.5 100:3:80:8 2d 2h 100 73[21] [19] 21a Reaction batch conditions: amount Al 2ofO3 catalysts (% w/w, in50:1.6:25:48 some cases unit is2b mg):mole ratio70 of [20] 22alcohol/succinic flow acid:reaction temperature PIL-A (°C):reaction time 5:1.2:85:5 (h). b Microwave-assisted2b esterification.100 [21] 23 flow PIL-A 5:1.2:87:4 2a 100 [21] 24 flow PIL-A 5:1.2:100:3.5 2d 100 [21] a Reaction conditions: amount of catalysts (% w/w, in some cases unit is mg):mole ratio of alcohol/succinic ◦ b acid:reaction temperature ( C):reaction time (h).
Details
-
File Typepdf
-
Upload Time-
-
Content LanguagesEnglish
-
Upload UserAnonymous/Not logged-in
-
File Pages10 Page
-
File Size-