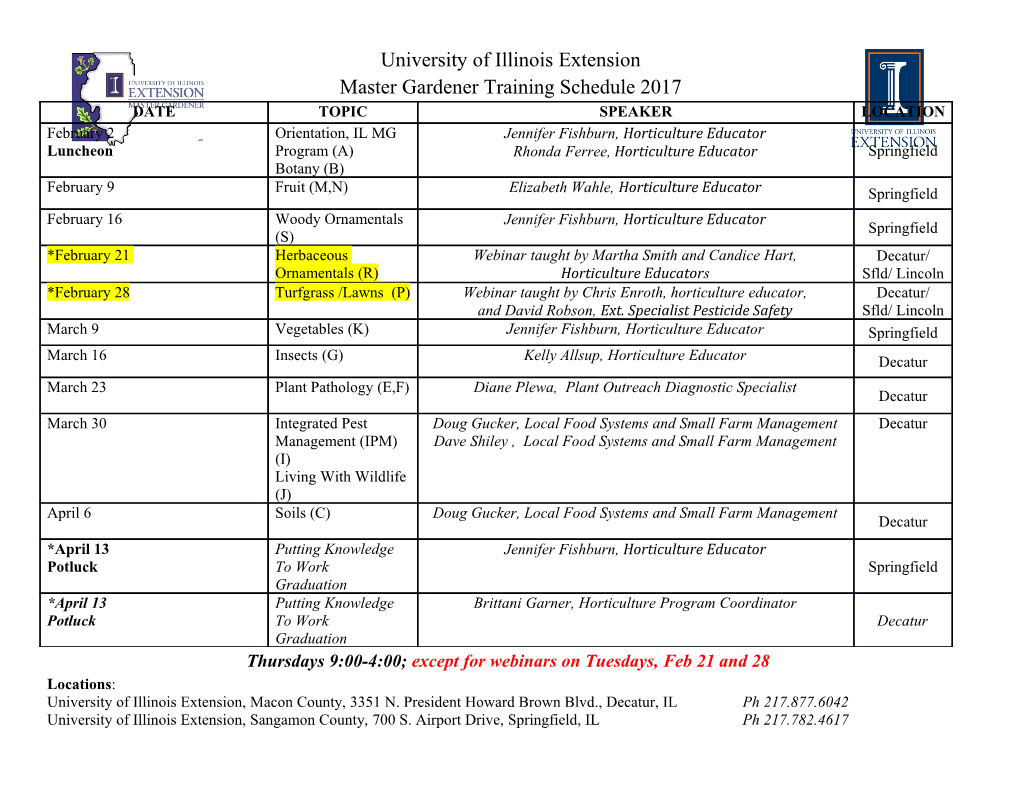
Implementing Total Productive Maintenance at B.A.T. Niemeyer Menno Burkunk Master Thesis University of Groningen Faculty of Economics and Business Technology Management Author: Menno Burkunk Student Number: 1271059 Company: British American Tobacco Niemeyer First Supervisor: Drs. J. Veldman Second Supervisor: Dr. Ir. W. Klingenberg Company Supervisor: Willy Smink (Quality Manager) Date: September 2009 The author is responsible for the content of this report; the copyright of the report is vested in the ownership of the author. Preface This research report that is written for British American Tobacco Niemeyer in Groningen and forms the final Master Thesis of my study Technology Management at the Rijksuniversiteit Groningen. BAT Niemeyer is a producer of shag and the company is exporting shag to more than 120 countries all over the world. Samson, Lucky Strike, Javaanse Jongens and Pall Mall form their driving brands. The research was interesting, challenging, sometimes complex but above all very instructive. Moreover, the research let me experience the pleasant and open business culture of BAT Niemeyer in which I quickly felt at home. From BAT Niemeyer I would like to thank Willy Smink (Quality & Product Assurance Manager) and Hugo Timmerman (Business Services Manager) for giving me the opportunity to conduct this research. They supplied me with all the necessary resources I needed to do my research. In my own office with the great view I already felt like a manager. Willy, in spite of his tight schedule, always found time, energy and patience to give me useful feedback and have long and fruitful discussions with me. When I was inclined to take the wrong direction on the road of my research he sent me the right way. Furthermore, I would like to thank my colleagues at the Business Services Department for being a very nice company during my stay. They were always very interested and provided me with the necessary information and pleasant distraction. From the manufacturing site I would like to thank all the employees who were willing to cooperate and provide me with the needed information. Without their help this research could not succeed. Finally, I would like to thank all other colleagues at BAT Niemeyer I did not mention or forgot to mention. From the university I would like to thank Jasper Veldman and Warse Klingenberg for being my mentors during this research. Jasper, who guided and supported me during the whole research, always provided me with clear, accurate and quick feedback and learned me how to do academic research and to stay critical. He helped me to stay focused and work in a structured manner. Thanks for that! Finally, I want to thank my friends and family. In particular my sister, Jurriaan and off course my girlfriend for their support and trust in me. A special last thanks goes to my parents, who unconditionally support and coach me. By finalizing my thesis a fantastic time as a student in Groningen has ended. Menno Burkunk Groningen, September 2009 Implementing Total Productive Maintenance at BAT Niemeyer 3 Executive Summary In spite of the initiation of a TPM program at BAT Niemeyer the results are not as expected. The equipment-efficiency measured by BAT Niemeyer hardly increased since the start of the program. Now, the reorganization, “Horizon”, has been carried out the focus will be on the TPM implementation again. In order to focus the research on the biggest shortcomings of BAT Niemeyer within TPM an assessment is done in a preliminary investigation. The TPM principles ‘cultural awareness’ and ‘elimination of losses’ were indicated with the lowest scores. The objective of the main investigation is to expose the causes of the low scores on these principles and subsequently formulate recommendations in order to achieve an structural improved implementation of these principles. The improvement will result in an increase in the Overall Equipment Efficiency. The creation of employee commitment turned out to be essential within ‘cultural awareness’. By creating commitment, the behavior of employees will change in such a manner that it will align with the rules of TPM. Intangible factors such as involvement, ownership, and understanding are the key issues in obtaining commitment. Hansson and Backlund (2003) identified ‘enabling activities’ that influence intangible factors and affect commitment. A survey, based on the model, was carried out under 38 shop floor workers in order to determine the current level of TPM commitment and the current performance of the ‘enabling activities’. The current level of TPM commitment at BAT Niemeyer is insufficient (2,8 on 1-5 scale). The enabling activities turned out to be underperformed (means between 2,4 and 3,6 on 1-5 scale) by middle- and top management. Measuring & Evaluation, Communication & Information and Empowerment activities were statistically proven to be of significant influence on employee commitment by a Multiple Regression Analysis. In order to create employee commitment the results and the progression of the TPM implementation have to be measured and evaluated more strictly on team level. Clear and quantifiable goals, e.g. in terms of an OEE increase, have to be set and evaluated in formal meetings with middle management. In this way a sense of importance will be created on shop floor level and progression will be experienced. Furthermore, misunderstandings about the goals and guidelines of TPM at BAT Niemeyer have to be taken away by clear and open communication. As a result of the relatively low level of education some shop floor workers do not see the benefits and the exact meaning of the concept which influences motivation negatively. Clear information about desirable behavior in their daily tasks is necessary. Finally, the team responsibility has to be extended, besides production goals, Implementing Total Productive Maintenance at BAT Niemeyer 4 to improvement goals. By setting their own goals for improvement responsibility will increase. Bad behavior must not be tolerated by management and achieved goals have to be rewarded. Causes of a low integration of ‘elimination of losses’ principle were searched in shortcomings in the performance of the defined steps in the elimination of losses process. First, the use of model machine can be very useful for BAT Niemeyer. Resources for improvement can be focused on one machine instead of using a ‘big bang’ strategy. Quick and visible benefits will increase the motivation and trust in TPM. The machine can form the guideline for the replication of improvements over the factory to the other, mainly similar, machines. Furthermore, the measurement of the OEE needs to be improved. It is inaccurate and labor intensive. The employees do not trust the OEE output and are unmotivated to work with it. The current OEE measurement cannot form the basis for actions of improvement. A cross-functional so called Focused-Improvement team (FI-team) has to be formed which will drive improvements in the factory. It is in charge of leading the improvement plans and is responsible for establishing lines of action, priorities and tracking activities related to the TPM master plan. The production-, quality- or TPM manager coordinates or leads the group. The FI-team aims at maximal engagement of all area employees and links the knowledge existing within the different teams. Finally, working processes have to be defined in Standard Operating Procedures (SOP). Structural losses have a frequent existence and their causes are locked in the organization’s structure which is made up out of standards. By defining work processes in SOP’s a certain situation can be fixed. Which means that a certain level of equipment-efficiency can be fixed. Then, by using creativity and innovation ability these standards can be improved and embedded in the organization by defining a new standard. In this way frequently executed activities like e.g. a tobacco set-up can be optimized and losses of expensive production time will be minimized. A central database with SOP’s has to be created and kept up-to-date. Besides, these improvements it is essential to take down the workload and take care of covering manpower. Due to the recent reorganization the pressure of workload is relatively high and now and then manpower is insufficient. By taking down the workload pressure the focus can be placed more on TPM again. Finally, further investigation within group development can be interesting for the optimization of the team performance. Implementing Total Productive Maintenance at BAT Niemeyer 5 Table of Contents Preface ...................................................................................................................................3 Executive Summary ...............................................................................................................4 Table of Contents ...................................................................................................................6 Abbreviations ........................................................................................................................9 1 Introduction ..................................................................................................................10 1.1 The history of British American Tobacco Niemeyer B.V. ..................................................... 10 1.2 BAT Niemeyer’s mission and characteristics ...................................................................... 12 1.3 Production process ...........................................................................................................
Details
-
File Typepdf
-
Upload Time-
-
Content LanguagesEnglish
-
Upload UserAnonymous/Not logged-in
-
File Pages87 Page
-
File Size-