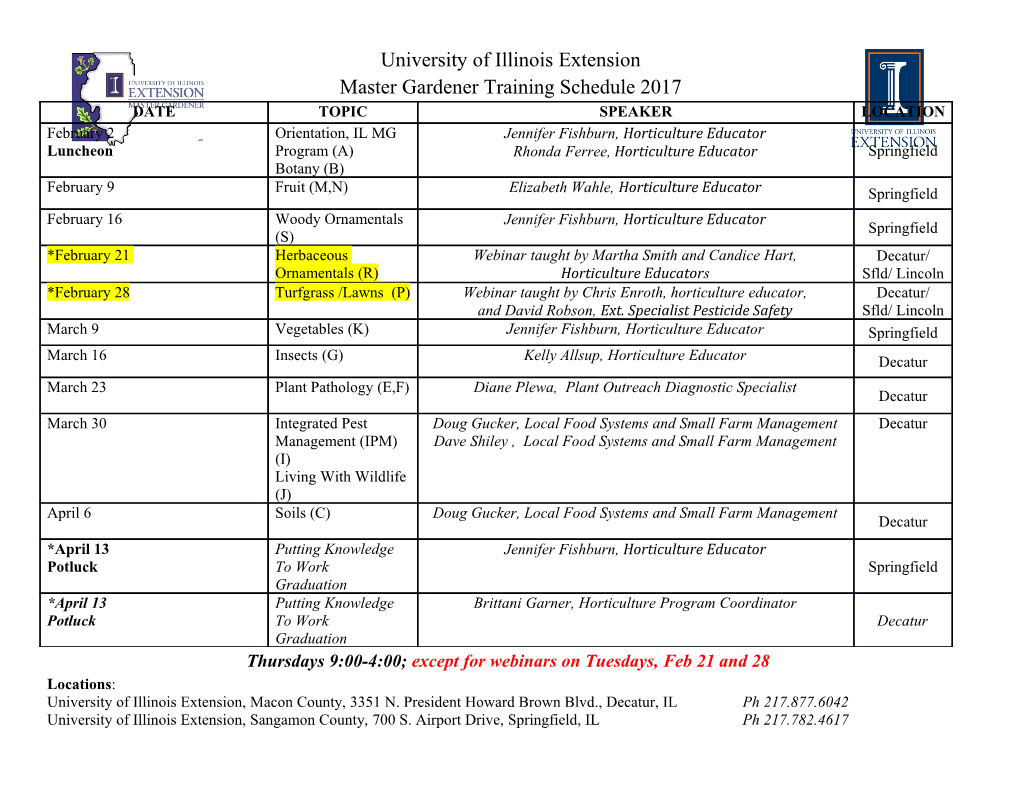
Florida State University Libraries 2016 Nanocarbon Foam/Polymer Composite Muhamad Shahrizan Jamal Follow this and additional works at the FSU Digital Library. For more information, please contact [email protected] FLORIDA STATE UNIVERSITY COLLEGE OF ENGINEERING NANOCARBON FOAM/POLYMER COMPOSITE By MUHAMAD SHAHRIZAN JAMAL A Thesis submitted to the Department of Industrial and Manufacturing Engineering in partial fulfillment of the requirements for the degree of Master of Science 2016 Muhamad Shahrizan Jamal defended this thesis on June 7, 2016. The members of the supervisory committee were: Mei Zhang Professor Directing Thesis Okenwa Okoli Committee Member Abhishek Shrivastava Committee Member The Graduate School has verified and approved the above-named committee members, and certifies that the thesis has been approved in accordance with university requirements. ii ACKNOWLEDGMENTS I would first like to thank my thesis advisor Dr. Mei Zhang for the continuous support of my graduate study. The door to her office was always open whenever I had a question about my research. Her guidance helped me in all the time of research and writing of this thesis Next, I would to thank my thesis committee members: Dr. Okenwa Okoli and Dr. Abshishek Shrivastava, for their astute comments and suggestions in helping me complete my research. Their suggestions helped me to gain a different perspective of my research. I thank my fellow coworkers at the High-Performance Materials Institute for the exciting discussions, continuous help and fun that we have had working together in the past two years. Last and most importantly, I would like to thank my family and friends for their moral support throughout my graduate studies and my life in general. iii TABLE OF CONTENTS List of Tables ...................................................................................................................................v List of Figures ................................................................................................................................ vi List of Symbols .............................................................................................................................. ix Abstract ............................................................................................................................................x 1. INTRODUCTION ......................................................................................................................1 2. PROBLEM STATEMENT AND RESEARCH OBJECTIVES .................................................4 2.1 Problem Statement ...............................................................................................................4 2.2 Research Objectives .............................................................................................................5 3. LITERATURE REVIEW............................................................................................................7 3.1 Carbon Foam ........................................................................................................................7 3.2 Composite Foam ................................................................................................................13 3.3 Summary ............................................................................................................................17 4. FABRICATION PROCESS .....................................................................................................18 4.1 Nanocarbon Foam ..............................................................................................................18 4.2 Nanocarbon Foam/Polymer Composite .............................................................................20 5. RESULTS AND DISCUSSIONS .............................................................................................24 5.1 Nanocarbon Foam ..............................................................................................................24 5.2 Nanocarbon Foam/PMMA Composite ..............................................................................30 5.3 Nanocarbon Foam/SEBS Composite .................................................................................46 6. CONCLUSION .........................................................................................................................51 References ......................................................................................................................................52 Biographical Sketch .......................................................................................................................57 iv LIST OF TABLES Table 1: Summary of reported strength by various authors in literature ...................................... 17 Table 2: Resistance of composite foams with varying density ..................................................... 44 Table 3: Resistivity of composite foams with varying density ..................................................... 45 v LIST OF FIGURES Figure 1: Traditional honeycomb structure ..................................................................................... 1 Figure 2: Graphical illustration on the difference between open cell foam and closed cell foam .. 2 Figure 3: Ashby plot of strength against density of various materials available to date. The unattainable material space is defined by Hashin bound. Adapted from Youssef.[15] .................. 4 Figure 4: Stress-strain curves and Transmission Electron Microscopy (TEM)images for foams made by Bradford et.al with varying post growth treatment time [18] .......................................... 8 Figure 5: Stress strain curve of multi cycle compression and the SEM image of the ultra- lightweight foam by Sun et.al [21] ................................................................................................. 9 Figure 6: (a – c)SEM images of foam fabricated using dichlorobenzene supply rate of 0.1 mL/min, 0.3 mL/min and 0.7 mL/min. (d) Different types of welded junction within the foam [22] ................................................................................................................................................ 10 Figure 7: The aerogel being compressed up to 90% strain and the resulting stress strain curve [25] ................................................................................................................................................ 12 Figure 8: Graphical illustration of the infiltration process in foam composite fabrication .......... 14 Figure 9: PAN oxidation process during the heat treatment at 300oC in air................................. 18 Figure 10: Graphical summary of the nanocarbon foam fabrication process ............................... 19 Figure 11: Graphical summary of the composite foam fabrication process ................................. 21 Figure 12: Foam infiltration process ............................................................................................. 22 Figure 13: Rotational drying to ensure uniformity in polymer infiltration ................................... 23 Figure 14: A) Illustration on how the CNTs are held together at the joint by PAN in the nanocarbon foam and how polymer coats the CNTs in the composite foam B) Image of two nanocarbon foam stacked on top of one another .......................................................................... 23 Figure 15: SEM images at different magnification level showing the structure of the nanocarbon foam. The magnification levels are: A) X350 B) X2000 C) X5000 D) X10000 .......................... 24 vi Figure 16: Stress-strain curve of the nanocarbon foam with a density of 26.42 mg/cm3 at different strain ............................................................................................................................... 26 Figure 17: The strength of the nanocarbon foam as compared to other materials ........................ 26 Figure 18: The fatigue test of the nanocarbon foam after multiple consecutive compression to 70% strain. .................................................................................................................................... 27 Figure 19: The heating and cooling between room temperature and 130°C of a curved nanocarbon foam to demonstrate its heat transfer effectiveness. ................................................. 28 Figure 20: Temperature change of nanocarbon foams with varying thickness when placed on surface heated to 200°C ................................................................................................................ 29 Figure 21: SEM images showing the structure of the foam before and after polymer infiltration 30 Figure 22: SEM images showing polymer concentration at different location within the composite foam ............................................................................................................................. 31 Figure 23 : Stress-strain curve for composite foam made from 1 wt% polymer concentration which has a density of 41 mg/cm3 ................................................................................................ 32 Figure 24 : Stress-strain curve for composite foam made from 3 wt% polymer concentration which has a density of 60 mg/cm3 ................................................................................................ 33 Figure 25: Stress-strain curve for composite foam made from 5 wt% polymer concentration which has a density of 88 mg/cm3 ...............................................................................................
Details
-
File Typepdf
-
Upload Time-
-
Content LanguagesEnglish
-
Upload UserAnonymous/Not logged-in
-
File Pages68 Page
-
File Size-