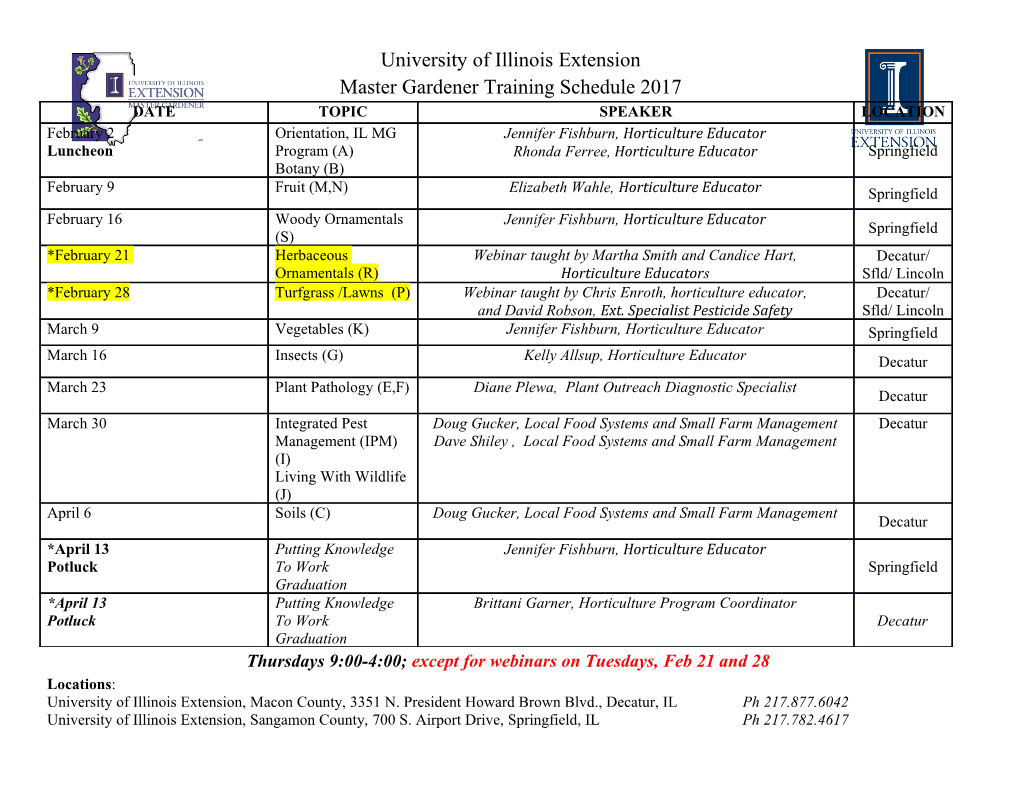
Fundamentals of Turboexpanders “Basic Theory and Design” Edited Date: September 16, 2015 Presented By: Mr. James Simms Simms Machinery International, Inc. 2357 “A” Street Santa Maria, CA 93455 U.S.A. About the Author In a Gas Processing Plant, the purpose of the James (Jim) Simms has been involved with the Turboexpander is to efficiently perform two (2) design, manufacture, and service of Turboexpanders distinctly different, but complimentary, functions in and other Cryogenic Rotating Machinery since 1969. a single machine. The primary function is to He worked in the Engineering Department of various efficiently generate refrigeration in the process gas Turboexpander manufacturing companies until he stream. This is done by the Expansion Turbine end founded Simms Machinery International, Inc. in efficiently extracting the potential heat energy from 1988. The company primarily focuses on LNG Boil-off the gas stream, causing it to cool dramatically. This Gas Compressors aboard LNG Tankers (Ships). In extracted energy is converted to mechanical energy 1994 he, along with others, founded Gas Technology to rotate the Shaft to the Booster Compressor end of Turbomachinery Services, Inc. to service the Turboexpander, which partially recompresses Turboexpanders, primarily used in Gas Processing the residue gas stream. The Turboexpander Plants. operates according to the thermodynamic and aerodynamic laws of physics. When designed Introduction/Description properly, the Turboexpander can yield very high efficiencies at the "Design Point" and reasonable The term "Turboexpander", Figure 1, is normally efficiencies at other, or "Off-Design", Points. used to define an Expander/Compressor machine as a single unit. It consists of two (2) primary Application components; the Radial Inflow Expansion Turbine and a Centrifugal (Booster) Compressor combined as The typical Turboexpander process installation is an assembly. Its Wheels are connected on a single shown in Figure 2, Simplified Process Schematic. Shaft. The Expansion Turbine is the power unit and High pressure, moderately cold gas flows into the the Compressor is the driven unit. Expander section of the Turboexpander. The gas flows through the Expander Variable Inlet Nozzles Figure 1 (Guide Vanes) and then through the Wheel, Turboexpander (Expander/Compressor) exhausting at a lower pressure and at a substantially Assembly Cross-Section Drawing colder temperature. Gas flows from the Expander to the Demethanizer, where condensate is removed. It should be noted that the Expander Nozzles are used to control the gas flow rate in order to maintain the pressure in the Demethanizer. The Residue Gas from the Demethanizer Tower flows through the Feed Gas Heat Exchanger and then to the Booster Compressor end of the Turboexpander. The efficiency of the Booster Compressor is very important, as it can improve the expansion process for more refrigeration as well as more efficiently use the power extracted by the Expander. While the engineering process to properly design a high efficiency Turboexpander is very complex, requiring change of energy, or Δh, with units of btu/lb, both in computerized analytical tools, the basic initial sizing the Ideal Process (Isentropic, or 100% efficient) and process can be simplified by using certain basic in the Actual Process, or real terms. equations and assumptions. Figure 3 Figure 2 Expansion Process Typical Turboexpander Process Schematic (Simplified) Preliminary Size Calculations The Turboexpander operation is best described as a dynamic system which responds to the Process Stream variations. To start the initial sizing design These have been designated Δh's and Δho, process, a fixed set of Process Stream parameters, or respectively. The ratio of these is the definition of "Design Point", must be established. This "Design the Isentropic efficiency, ηe, of the Expander Point" is normally set by the plant process engineer's (i.e., ηe = Δho / Δh's ). For example, if system analysis in the case of new plants. In the Δho = 34 btu/lb, and Δh's = 40 btu/lb, then: case of a Turboexpander re-design in an existing ηe = 34 / 40 = .85 or 85% plant, the actual operating condition will dictate the new "Design Point". With the Δh's and ηe values known, we then only The parameters required to size the Turboexpander need the gas mass flow rate, w, to calculate the are: Horsepower developed by the Expander. Since the mass flow rate is normally given by the process Gas Composition engineer, we now have enough information to Flow Rate calculate the Horsepower with the following Inlet Pressure formula: Inlet Temperature HPExpander = (778 / 550) x Δh's x w x ηe Normally, the Expander Outlet Pressure is 778 / 550 = 1.4145 determined by the performance of the Booster Compressor's efficiency through a complex iterative (This is the constant value to change btu units into analysis. For this simplified sizing exercise, we will Horsepower terms) assume the value of the Expander Outlet Pressure. We will assume the mass flow rate, w = 20 Energy Extraction lbs/second. So, if Δh's = 40 btu/lb, w = 20 lbs/second, and ηe = .85, then: Where does the energy come from? With reference to Figure 3, which shows the typical Expansion HPExpander = 1.4145 x 40 x 20 x .85 = 961.9 Process Graph, we see the process in terms of 2 Horsepower Balance rise, Δh', is lower than the actual Head Rise, Δho, required to achieve the Discharge Pressure, the ratio The HP developed by the Expander must be of Δh' / Δho = efficiency of the Compressor, or ηc. absorbed in order to prevent over-speeding. The Bearings and the Compressor absorb this power to Figure 4 Compression Process create a balance. The Horsepower Balance formula is: HPExpander = HPCompressor + HPBearings Example Let's assume that the Bearings consume a total of 30 Horsepower, which is subtracted from the Expander Horsepower. If we rearrange the formula above, then the available Horsepower to the Compressor is: HPCompressor = HPExpander - HPBearings = 961.9 - 30 = 931.9 Horsepower How Does the Booster Compressor Use Horsepower to Create Pressure? The pressure rise through the Compressor is a function of the adiabatic Δh', or Head Rise, developed by the Compressor and its efficiency, ηc, We will assume a mass flow rate, w, through the to satisfy the Horsepower balance formula. The Compressor, of 27.0 lbs/second and solve the Horsepower formula for the Compressor is similar to formula: the Expander, but slightly different as it is consuming ퟗퟑퟏ.ퟗ 퐱 .ퟕퟓ power. The formula is: Δh' = Adiabatic ퟏ.ퟒퟏퟒퟓ 퐱 ퟐퟕ.ퟎ ퟏ.ퟒퟏퟒퟓ 퐱 횫퐡′퐀퐝퐢퐚퐛퐚퐭퐢퐜 퐱 퐰 HPCompressor = = 18.30 btu/lb 훈퐂 The value of 1.4145 is, again, the constant to convert Discharge Pressure Calculation the units into Horsepower, just the same as the Expander formula. Δh'Adiabatic is the ideal Head Rise, Now, having calculated the Δh'Adiabatic, we can or energy change, from the Inlet Pressure to the calculate the pressure rise through the Compressor Discharge Pressure of the Compressor. The units are by the following formula: btu/lb of gas flow. W is the symbol for mass flow through the Compressor, and the units are 횫퐡′ 후 / 후−ퟏ Pout = 퐏퐢퐧 × [ퟏ + ] lbs/second. 퐂퐩퐓ퟏ퐙 The mass flow rate, w, for the Compressor, is usually Definition of Terms: given by the process engineer. With the available Pout = Discharge Pressure, PSIA Compressor Horsepower known, we can rearrange Pin = Inlet Pressure, PSIA the Compressor Horsepower formula to calculate Cp = Specific heat at constant pressure T1 = Inlet temperature, °R (°R = °F + 459.69) the Δh'Adiabatic, Head Rise, as follows: Z = Compressibility Factor 퐇퐏 퐱 훈퐜 γ = Greek Symbol "Gamma", stands for the Ratio Δh' = 퐂퐨퐦퐩퐫퐞퐬퐬퐨퐫 Adiabatic ퟏ.ퟒퟏퟒퟓ 퐱 퐰 of specific heats We start by assuming a reasonable efficiency, ηc, on the Compressor, such as 75%. Figure 4 shows a typical Compression Process in which the ideal head 3 To be accurate, the values of Cp, Z, and γ are best derived by a good equation of state computer Co = √ ퟐ × 퐠 × 퐉 × √횫퐡′퐬 program; however, for this exercise, we will assume certain values for these (T1 = 60°F, Cp = .54, Z = .98, = √ ퟐ × ퟑퟐ. ퟐ × ퟕퟕퟖ × √ퟒퟎ and γ = 1.3) and solve the above formula. = √ ퟓퟎퟏퟎퟑ. ퟐ × √ퟒퟎ So, to repeat the formula for the Compressor if the Inlet Pressure equals 145 PSIA, the Discharge = ퟐퟐퟑ. ퟖ × ퟒퟎ Pressure will be calculated: √ = 1415 ft/sec 횫퐡′ 후 / 후−ퟏ Pout = 퐏퐢퐧 × [ퟏ + ] 퐂퐩퐓ퟏ퐙 Since the term U, Wheel Tip Speed, needs to be 0.7 ퟏퟖ.ퟑퟎ ퟏ.ퟑ/.ퟑ of Co, then: = ퟏퟒퟓ × [ퟏ + ] .ퟓퟒ ×(ퟔퟎ+ퟒퟓퟗ.ퟔퟗ)× .ퟗퟖ U = .7 x Co = 145 x [ 1.0665 ] 4.333 = .7 x 1415 = 145 x 1.322 = 990 ft/sec = 191.7 PSIA Definition of Terms: How is the Turboexpander Design Speed U = Tip Speed of Wheel, ft/sec Determined? Co = Spouting Velocity, ft/sec g = 32.2 ft/sec2 This is done by using the term Specific Speed, or Ns, J = 778 ft-lb/btu of the Expander Wheel: The term, U, is the peripheral velocity of the 퐍 퐱 √퐀퐂퐅퐒 N = ퟐ Expander Wheel (tip speed) which is calculated by: s (ퟕퟕퟖ 퐱 횫퐡′ ).ퟕퟓ 퐒 퐃퐢퐚퐦퐞퐭퐞퐫 (퐢퐧퐜퐡퐞퐬) 퐱 퐑퐏퐌 U = From earlier pages, Δh's = 40 btu/lb ퟐퟐퟗ.ퟐ Assume a Specific Speed, Ns = 75 for good efficiency Assume, ACFS2 = 25.0 (ACFS2 is the Actual Cubic So, to rearrange the formula to solve for the Wheel Feet per Second of volumetric flow at the outlet of Diameter: the Expander). 퐔 × ퟐퟐퟗ.ퟐ Rearrange the formula and calculate the speed, N: Diameter = 퐑퐏퐌 .ퟕퟓ 퐍퐬 × (ퟕퟕퟖ × 횫퐡′퐒) ퟗퟗퟎ × ퟐퟐퟗ.ퟐ N = = √퐀퐂퐅퐒ퟐ ퟑퟓ,ퟏퟒퟔ ퟕퟓ × (ퟕퟕퟖ × ퟒퟎ).ퟕퟓ = 6.46 inches = √ퟐퟓ How to Approximate the Compressor Wheel ퟕퟓ ×ퟐퟑퟒퟑ = ퟓ Diameter = 35,146 RPM The following formula can be used to approximate the Compressor Wheel Diameter: How to Approximate the Expander Wheel Diameter 푼ퟐ× 횿 Δh'Adiabatic = 퐠 × 퐉 First, for good efficiency, the term U/C should equal o From previous pages, we calculated the Compressor about 0.7.
Details
-
File Typepdf
-
Upload Time-
-
Content LanguagesEnglish
-
Upload UserAnonymous/Not logged-in
-
File Pages8 Page
-
File Size-