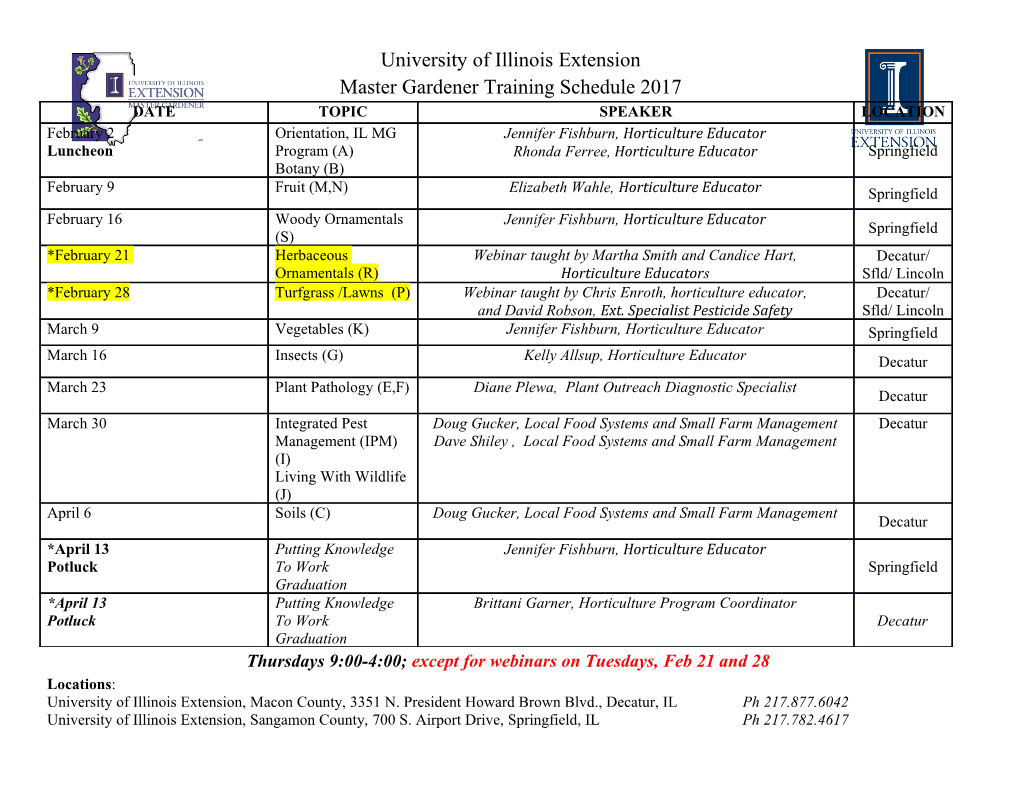
Novel Designs and Geometry for Mechanical Gearing by Erasmo Chiappetta School of Engineering, Computing and Mathematics Oxford Brookes University In collaboration with Norbar Torque Tools ltd., UK. A thesis submitted in partial fulfilment of the requirements of Oxford Brookes University for the degree of Doctor of Philosophy September 2018 Abstract This thesis presents quasi-static Finite Element Methods for the analysis of the stress state occurring in a pair of loaded spur gears and aims to further research the effect of tooth profile modifications on the mechanical performance of a mating gear pair. The investigation is then extended to epicyclic transmissions as they are considered the most viable solution when the transmission of high torque level within a compact volume is required. Since, for the current study, only low speed conditions are considered, dynamic loads do not play a crucial role. Vibrations and the resulting noise might be considered negligible and consequently the design process is dictated entirely by the stress state occurring on the mating components. Gear load carrying capacity is limited by maximum contact and bending stress and their correlated failure modes. Consequently, the occurring stress state is the main criteria to characterise the load carrying capacity of a gear system. Contact and bending stresses are evaluated for multiple positions over a mesh cycle of a contacting tooth pair in order to consider the stress fluctuation as consequence of the alternation of single and double pairs of teeth in contact. The influence of gear geometrical proportions on mechanical properties of gears in mesh is studied thoroughly by means of the definition of a domain of feasible combination of geometrical parameters in order to deconstruct the well-established gear design process based on rating standards and base the defined gear geometry on operational and manufacturing constraints only. From this parametric study, suitable suggestions for enhancing the load carrying capacity of the tooth flank are made by showing that the use of non-standard geometric parameters can improve the performance of gears. As this study also aims to improve the performances of epicyclic gearings specifically for low speed-high torque operating conditions, the optimum parameters found in the preliminary parametric analysis were applied to this category of systems. The design procedure based on the area of existence of gear geometry was extended to this case which required the determination of the domain of feasible combination for gears in internal mesh with the addition of constraints addressed to epicyclic I configurations. Three epicyclic systems with same boundary design conditions but different combination of geometrical parameters have been modelled and analysed by means of quasi-static FEA. The results have shown that the improvements found for the case of two mating spur gears are also valid for the case of higher order systems in which multiple contacts are simultaneously occurring. Based on these results, suitable suggestions are made for the design of gears working in epicyclic systems for an enhanced torque capacity and a volume reduction for applications characterized by low speed and high loads conditions. An alternative solution to geared systems that guarantees compactness and high torque transmission capabilities has also been investigated; it consists of a cycloidal transmission system. The parametric equations for the cycloidal profile have been determined and an executive design, then manufactured, has been produced. The preliminary quasi-static Finite Element analysis has predicted the load sharing and stress distribution among multiple components confirming the mechanical advantage of this category of transmission systems. II Acknowledgments With sincere respect and gratitude, I would like to thank my principal supervisor Professor Denise Morrey for all the support, encouragement and most valuable guidance throughout the duration of the Ph.D. To Norbar Torque Tools ltd. and particularly Neill Brodey, Managing Director, for supporting this work financially and Richard Radini, Engineering Manager, for providing the technical expertise and support. I am grateful to my second supervisor, Professor John Durodola, for his helpful discussion and encouragement. I would like to extend my thanks and appreciation to all my friends and colleagues at Oxford Brookes University. To Davide, Fabrizio, Miguel and Mohamed, you have been my family for these four unforgettable years that I will never forget; Thank you! Special thanks are due to Peppe, Kara, Nino and Glenda for making me feel home with their warm friendship. My deep love goes to my parents, my beloved grandparents and my friends Salvo, Mapi and Stella for their continuous support and motivation to believe in myself and give my best to bring this study to an end. Finally, to my love Marghe, for all the understanding and the enduring and loving support. Without the valuable contribution of each one of you this work would not have been possible. III Publications from this thesis This research has produced a considerable amount of results on many design and performance aspects of mechanical transmission systems. The outcomes are currently being collated for publications. Published Papers: 1. Chiappetta, E., Morrey, D., Non-Standard spur gear tooth profiles for improved epicyclic gear system performance in low speed applications. International Conference on Gears 2017. Technical University of Munich, Munich, Germany. 2. Chiappetta, E., Morrey, D., High pressure Angle Spur Gears for epicyclic Gear Trains. BGA – British Gear Association, GEARS 2016 - Technical Awareness Seminar, November 2016, Birmingham University. Submitted Papers: Chiappetta E., Morrey D., Parametric FE Analysis of Tooth Contact Stress for a Spur Gear Pair. Measurement, 2018. Papers under preparation: Parametric FE Analysis of Tooth Bending Stress for a Spur Gear Pair. Design and analysis of a planetary gear set by means of blocking contour approach and numerical techniques. IV Table of Contents Abstract I List of Figures XII List of Tables XXIII List of Symbols XXIV Abbreviations XXVIII 1 Introduction 1 1.1 Background 1 1.2 Technical Terms 2 1.3 Motivation 6 1.4 Research Objectives 7 1.5 Research Methodology 8 1.6 Originality and contribution of this research 9 1.7 Thesis outline 11 2 Literature Review 13 2.1 Design Space 16 2.2 Stress Analysis of gears 26 2.2.1 Root Bending stress analysis 27 2.2.2 Tooth flank contact stress analysis 31 V 2.2.3 Combined Contact and Bending analyses 35 2.3 Coaxial drives: epicyclic and cycloidal systems 37 2.3.1 Planetary drives 41 2.3.2 Cycloidal drives 44 2.4 Available Design Standards 52 2.5 Knowledge gaps in literature review 53 3 Gear tooth geometry 56 3.1 Involute tooth geometry 58 3.1.1 Involute curve 59 3.1.2 Trochoidal curve 62 3.2 Spur gear design parameters 65 3.2.1 Addendum factor 68 3.2.2 dedendum factor 69 3.2.3 Profile shift 70 3.2.4 Pressure angle 75 3.2.4.1 Instantaneous radius of curvature 76 3.3 Manufacturing and operational boundaries 78 3.3.1 Undercutting 78 3.3.2 Top land thickness 82 VI 3.3.3 Tip/root interference 85 3.3.3.1 Path of contact 87 3.3.4 Contact ratio 90 3.3.5 Summary 94 3.4 FEA background 95 3.4.1 Static and Quasi-static Analyses 100 3.4.2 Non-linear structural analysis 101 3.4.3 Non-linear solution method 101 3.4.4 Solution of Structural contact problems 103 3.5 Conclusion 106 4 Parametric multi-dimensional design space 107 4.1 Multi-dimensional contour plots 112 4.1.1 Influence of pressure angle 114 4.1.2 Influence of addendum length 117 4.2 Conclusion 120 5 Spur gear pair performance analysis 121 5.1 KISSsoft® 122 5.2 Gear Modelling 123 VII 5.3 ISO 6336 Method B 125 5.4 FEA methodology and analysis settings 128 5.4.1 Load Inertia 130 5.4.2 Plane stress/strain 131 5.4.3 Finite Element Mesh 132 5.4.3.1 Mesh settings for gear performance analysis 133 5.4.3.2 Mesh convergence study 134 5.4.4 Finite element Contact Model 138 5.4.4.1 Contact settings for gear performance analysis 139 5.4.5 Time step Controls 141 5.4.6 Boundary conditions 142 5.4.7 Validation of numerical results 142 5.5 Evaluation of Contact Stress for a spur gear pair 143 5. 5.1 Load distribution 145 5.5.2 Influence of reference pressure angle 146 5.5.3 Area of contact Ac 148 5.5.4 Influence of profile shift coefficient x on tooth flank contact 149 stress 5.5.5 Influence of addendum factor ha on tooth flank contact stress 152 5.6 Evaluation of root bending stress for a spur gear pair 154 VIII 5.6.1 Effect of pressure angle 155 5.6.2 Effect of profile shift coefficient on root bending stress 158 5.6.3 Effect of dedendum factor hf on root bending stress 160 5.6.4 Effect of addendum factor ha on root bending stress 161 5.7 Conclusion 162 6 High pressure angle planetary drives 165 6.1 Geometrical arrangement of epicyclic drives 166 6.1.1 Meshing and assembly requirements 167 6.2 Internal gears geometry definition 169 6.2.1 Internal gearing geometrical and operational boundaries 171 6.2.1.1 Geometrical Interference 171 6.2.1.2 Top land thickness and root space between adjacent teeth 173 6.2.1.3 Contact ratio in internal gears 176 6.3 Case study 179 6.3.1 Design process 180 6.3.2 Geometry-based external/internal contour plots 184 6.4 Planetary drive modelling 194 6.5 Finite Element Analysis 195 6.5.1 Time step Controls 196 IX 6.5.2 Boundary conditions 196 6.6 Results and Discussion 197 6.6.1 Bending stress 199 6.6.2 Contact stress 204 6.7 Conclusion 209 7 Design
Details
-
File Typepdf
-
Upload Time-
-
Content LanguagesEnglish
-
Upload UserAnonymous/Not logged-in
-
File Pages301 Page
-
File Size-