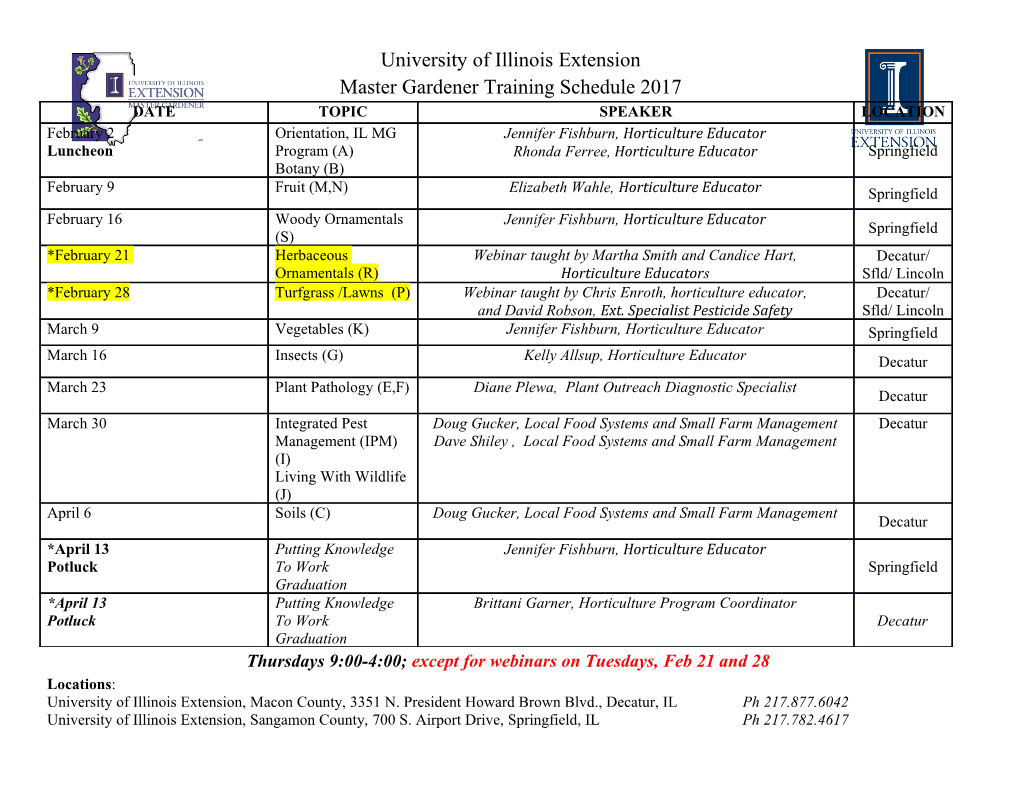
David Markovitz GXP Compliance–Start with the Basics David Markovitz “GXP Training Tips” provides ideas and suggestions associated with the planning, management, and execution of training programs for regulated industries. Reader comments, questions, and suggestions are requested. Case stud- ies illustrating training applications submitted by readers are most welcome. Please send your comments, questions, and suggestions to column coordinator David Markovitz at [email protected] or managing editor Susan Haigney at [email protected]. IMAGES GETTY Key points The following key points are discussed: ORESBY/ • Discipline to follow policies and procedures is key to GXP M compliance • Reminding people of GXP basics helps to create a habit of ARCUS M compliance • GXP training should be conducted on an ongoing basis • Fundamental GXP topics are suggested. INTRODUCTION The late John Wooden, legendary coach of University of California-Los Angeles’ (UCLA) champion basketball teams in the 1960s and ‘70s, stressed the basics. The first lesson during the first practice of each sea- son was how to put your socks on and how to tie your shoes. The new players were often surprised at this and would complain with phrases like, “Coach, we learned that in kindergarten” and “We already know how to do that.” But Coach Wooden would insist they do it his way, as he had proof that his way reduced the chance of blisters and reduced the chance of tripping on a loose shoelace during a game. Essentially Coach Wooden had a standard operating procedure (SOP) for putting on one’s socks and shoes. He often cited this as one of the major reasons for his record string of championship teams. This was important not only for the two reasons cited above, but also it created the discipline among the players to follow the playbook and listen to their coach. So much of following GXPs in our organizations is the discipline to follow our policies and procedures—our playbook. Most companies that run into trouble with GXP violations with the US Food and Drug Administration and other regulatory bodies find that it is that discipline that is lacking. The policies are in place. The procedures are written and in place. But, for a variety of reasons, people in the organization do not follow the policies or procedures. Reminding people of the basics of GXP is a good place to start in creating a habit of GXP compliance within the organization. Certainly new personnel need to know the basics. But reminding everyone on a regular basis reinforces the importance of GXP compliance. 74 SPECIAL EDITION: A Roadmap to GMP Compliance Part 2 David Markovitz Creating a Culture of Quality and GXP Compliance David Markovitz “GXP Training Tips” provides ideas and suggestions associated with the planning, management, and execution of training programs for regulated industries. Reader comments, questions, and suggestions are requested. Case studies illustrating training applications submitted by readers are most welcome. Please send your comments to column coordinator David Markovitz at david@gmptraining- systems.com or to coordinating editor Susan Haigney at [email protected]. Actions speak louder than words, and some of the best training occurs by IMAGES example. Establishing a culture of quality within an organization, starting GETTY with upper most management, creates an environment that inspires em- ployees to take pride in their work and, therefore, follow good practices. ORESBY/ Companies that follow GXP regulations understand this concept. Some M companies have a culture of quality…and some don’t. To create your own culture of quality, take a look at the companies that are successful, and the ARCUS M ones that are not, to see how it’s done. THOSE WHO DON’T HAVE IT AND DON’T GET IT One generalization we can come to about the companies found in the “Don’t Have It” column is that they do not have a culture of quality in their organization. They have not made GXP a lifestyle. GXP is not part of the fabric of these organizations. These companies can be observed by visiting the US Food and Drug Administration’s website. Companies who don’t put an emphasis on qual- ity are more likely to receive negative attention from FDA. FDA’s website provides information on companies that have run afoul of GXP (1). FDA Warning Letters FDA Commissioner Dr. Margaret Hamburg, in a speech delivered on Au- gust 6, 2009, stated, “The FDA must be vigilant, the FDA must be strategic, the FDA must be quick, and the FDA must be visible. We must get the word out that the FDA is on the job” (2). Commissioner Hamburg highlighted the following six initial steps de- signed to hone the effectiveness and timeliness of the FDA’s regulatory and enforcement system (2): • Set post-inspection deadlines • Take responsible steps to speed the warning letter process • Work more closely with FDA’s regulatory partners • Prioritize follow-up on warning letters and other enforcement ac- tions • Be prepared to take immediate action in response to public health risks • Develop and implement a formal warning letter “close-out” process. These six steps express FDA’s commitment to the warning letter pro- cess. It is in a company’s best interest to review other companies’ warn- SPECIAL EDITION: A Roadmap to GMP Compliance Part 2 77 David Markovitz After-Action Reviews—Turning Problems into GXP Learning Points David Markovitz “GXP Training Tips” provides ideas and suggestions associated with the plan- ning, management, and execution of training programs for regulated industries. Reader comments, questions, and suggestions are requested. Case stud- ies illustrating training applications submitted by readers are most welcome. Please send your comments, questions, and suggestions to column coordina- tor David Markovitz at [email protected] or coordinating editor Susan Haigney at [email protected]. IMAGES INTRODUCTION GETTY Many companies conduct GXP training on a schedule based on the calendar, usually on an annual basis. This approach to training is good, ORESBY/ but it is not good enough. Annual training may not take advantage of M events or episodes where GXP training can be made more relevant and more meaningful. Training sessions should also be conducted when ARCUS M the occasion arises apart from the scheduled training. Training sessions that are more relevant and meaningful will become more memorable, and our GXP programs will become more effective. caPA Occasions like problems, mix-ups, and errors provide an opportunity for meaningful and memorable discussions. When problems occur, we often invoke caPA. Most of us know the term CAPA (corrective action and preventive action), but by revising the term to “caPA,” the rela- tive importance of preventive action compared to corrective action is emphasized. One important aspect often left out of a caPA project is to use the problem or issue as a learning tool for everyone involved. Do- ing so can lead to a better understanding of the process under review by everyone working on or working in the problem process. After-Action Review One useful method for gaining additional benefit from our caPA activi- ties and turning them into learning points is through the use of an after-action review. The after-action review is defined as an assessment conducted after a project or major activity that allows employees and leaders to discover and better learn what happened and why. It may be considered a professional conversation about an event that enables employees to understand why things happened during the progression of the process and, most important, to learn from that experience. Here’s how you might use an after-action review as part of the GXP training process. Gather the “right people” to thoroughly discuss the project. This includes the people who work “in the process” (i.e., the operators and other people who actually do the work), along with those people who work “on the process”—the subject matter experts (SMEs) and other people who are expert on the problem situation. Convene all members of the entire group in a comfortable conference room or train- 80 SPECIAL EDITION: A Roadmap to GMP Compliance Part 2 David Markovitz It’s All About Trust David Markovitz “GXP Training Tips” provides ideas and suggestions associated with the plan- ning, management, and execution of training programs for regulated industries. Reader comments, questions, and suggestions are requested. Case stud- ies illustrating training applications submitted by readers are most welcome. Please send your comments, questions, and suggestions to column coordina- tor David Markovitz at [email protected] or coordinating editor Susan Haigney at [email protected]. IMAGES INTRODUCTION GETTY “Have a safe flight.” This is what I hear from my wife whenever I leave on a trip that ORESBY/ M involves an airplane. These are the last words from her mouth when we part. I wish she wouldn’t say that, because I can’t think of a response ARCUS that would leave her feeling comfortable. So I just grin and nod my M head to acknowledge her. The only words I can think of to say are these: “I’ll make sure to buckle my seat belt.” “I’ll be sure that my tray table is raised and locked.” “I’ll have my seat in its upright position.” Those are the only things that are in my control as an airline passen- ger to help ensure a safe flight. Competence–All The Time Consider for a moment the airline industry. What’s the worst thing that can happen when there’s a product failure? The worst thing that can happen is the airplane crashes and people die or are injured. Having a safe flight is really in the hands of the pilot, co-pilot, and the rest of the crew, in the air and on the ground.
Details
-
File Typepdf
-
Upload Time-
-
Content LanguagesEnglish
-
Upload UserAnonymous/Not logged-in
-
File Pages13 Page
-
File Size-