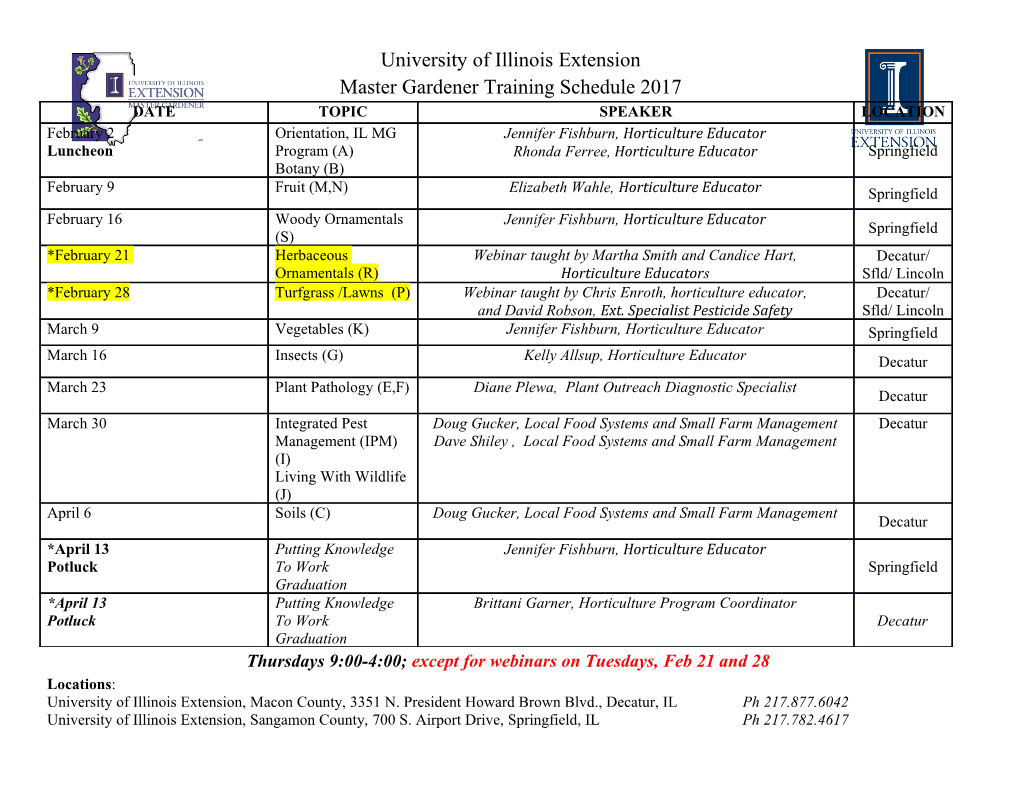
Environmental Protection Agency Pt. 438, App. B MISCELLANEOUS METAL PRODUCTS Miscellaneous Fabricated Wire Products Miscellaneous Metal Work Miscellaneous Repair Shops & Related Services Miscellaneous Transportation Equipment APPENDIX B TO PART 438—OILY (1) Alkaline cleaning is performed to re- OPERATIONS DEFINITIONS move foreign contaminants from parts. This operation usually is done prior to finishing NOTE: The definitions in this appendix (e.g., electroplating). shall not be used to differentiate between the (2) Emulsion cleaning is an alkaline clean- six ‘‘core’’ metal finishing operations (i.e., ing operation that uses either complex Electroplating, Electroless Plating, Anod- chemical enzymes or common organic sol- izing, Coating (chromating, phosphating, and vents (e.g., kerosene, mineral oil, glycols, coloring), Chemical Etching and Milling, and and benzene) dispersed in water with the aid Printed Circuit Board Manufacture) and of an emulsifying agent. The pH of the sol- forty ‘‘ancillary’’ process operations listed at vent usually is between 7 and 9, and, depend- 40 CFR 433.10(a). ing on the solvent used, cleaning is per- Abrasive Blasting involves removing surface formed at temperatures from room tempera- ° ° film from a part by using abrasive directed ture to 82 C (180 F). This operation often is at high velocity against the part. Abrasive used as a replacement for vapor degreasing. blasting includes bead, grit, shot, and sand Alkaline Treatment Without Cyanide is a blasting, and may be performed either dry or general term used to describe the application with water. The primary applications of wet of an alkaline solution not containing cya- nide to a metal surface to clean the metal abrasive blasting include: Removing burrs on surface or prepare the metal surface for fur- precision parts; producing satin or matte fin- ther surface finishing. ishes; removing fine tool marks; and remov- Aqueous Degreasing involves cleaning metal ing light mill scale, surface oxide, or welding parts using aqueous-based cleaning chemi- scale. Wet blasting can be used to finish frag- cals primarily to remove residual oils and ile items such as electronic components. greases from the part. Residual oils can be Also, some aluminum parts are wet blasted from previous operations (e.g., machine cool- to achieve a fine-grained matte finish for ants), oil from product use in a dirty envi- decorative purposes. In abrasive blasting, the ronment, or oil coatings used to inhibit cor- water and abrasive typically are reused until rosion. Wastewater generated by this oper- the particle size diminishes due to impacting ation includes spent cleaning solutions and and fracture. rinse waters. Adhesive Bonding involves joining parts Assembly/Disassembly involves fitting to- using an adhesive material. Typically, an or- gether previously manufactured or rebuilt ganic bonding compound is used as the adhe- parts or components into a complete metal sive. This operation usually is dry; however, product or machine or taking a complete aqueous solutions may be used as bonding metal product or machine apart. Assembly/ agents or to contain residual organic bond- disassembly operations are typically dry; ing materials. however, special circumstances can require Alkaline Cleaning for Oil Removal is a gen- water for cooling or buoyancy. Also, rinsing eral term for the application of an alkaline may be necessary under some conditions. cleaning agent to a metal part to remove oil Burnishing involves finish sizing or smooth and grease during the manufacture, mainte- finishing a part (previously machined or nance, or rebuilding of a metal product. This ground) by displacing, rather than removing, unit operation does not include washing of minute surface irregularities with smooth the finished products after routine use (as point or line-contact, fixed or rotating tools. defined in ‘‘Washing (Finished Products)’’ in Lubricants or soap solutions can be used to this appendix), or applying an alkaline cool the tools used in burnishing operations. cleaning agent to remove nonoily contami- Wastewater generated during burnishing in- nants such as dirt and scale (as defined in clude process solutions and rinse water. ‘‘Alkaline Treatment Without Cyanide’’ in Calibration is performed to provide ref- this appendix and ‘‘Alkaline Treatment With erence points for the use of a product. This Cyanide’’ in appendix C of this part). Waste- unit operation typically is dry, although water generated includes spent cleaning so- water may be used in some cases (e.g., pump- lutions and rinse waters. ing water for calibration of a pump). Water 397 VerDate Sep<11>2014 09:55 Oct 02, 2014 Jkt 232178 PO 00000 Frm 00407 Fmt 8010 Sfmt 8002 Y:\SGML\232178.XXX 232178 rmajette on DSK2TPTVN1PROD with CFR Pt. 438, App. B 40 CFR Ch. I (7–1–14 Edition) used in this unit operation usually does not tives. Rinse waters typically are assimilated contain additives. into the working fluid or treated on site. Corrosion Preventive Coating involves apply- Heat Treating involves modifying the phys- ing removable oily or organic solutions to ical properties of a part by applying con- protect metal surfaces against corrosive en- trolled heating and cooling cycles. This oper- vironments. Corrosion preventive coatings ation includes tempering, carburizing, include, but are not limited to: Petrolatum cyaniding, nitriding, annealing, aging, nor- compounds, oils, hard dry-film compounds, malizing, austenitizing, austempering, solvent-cutback petroleum-based com- siliconizing, martempering, and pounds, emulsions, water-displacing polar malleablizing. Parts are heated in furnaces compounds, and fingerprint removers and or molten salt baths, and then may be cooled neutralizers. Corrosion preventive coating by quenching in aqueous solutions (e.g., does not include electroplating, or chemical brine solutions), neat oils (pure oils with lit- conversion coating operations. Many corro- tle or no impurities), or oil/water emulsions. sion preventive materials also are formu- Heat treating typically is a dry operation, lated to function as lubricants or as a base but is considered a wet operation if aqueous for paint. Typical applications include: As- quenching solutions are used. Wastewater in- sembled machinery or equipment in standby cludes spent quench water and rinse water. storage; finished parts in stock or spare Impact Deformation involves applying im- parts for replacement; tools such as drills, pact force to a part to permanently deform taps, dies, and gauges; and mill products or shape it. Impact deformation may include such as sheet, strip, rod and bar. Wastewater mechanical processes such as hammer forg- generated during corrosion preventive coat- ing, shot peening, peening, coining, high-en- ing includes spent process solutions and ergy-rate forming, heading, or stamping. rinses. Process solutions are discharged Natural and synthetic oils, light greases, and when they become contaminated with impu- pigmented lubricants are used in impact de- rities or are depleted of constituents. Corro- formation operations. Pigmented lubricants sion preventive coatings typically do not re- quire an associated rinse, but parts are include whiting, lithapone, mica, zinc oxide, sometimes rinsed to remove the coating be- molybdenum disulfide, bentonite, flour, fore further processing. graphite, white lead, and soap-like mate- Electrical Discharge Machining involves re- rials. These operations typically are dry, but moving metals by a rapid spark discharge be- wastewater can be generated from lubricant tween different polarity electrodes, one the discharge and from rinsing operations associ- part and the other the tool, separated by a ated with the operation. small gap. The gap may be filled with air or Iron Phosphate Conversion Coating is the a dielectric fluid. This operation is used pri- process of applying a protective coating on marily to cut tool alloys, hard nonferrous al- the surface of a metal using a bath con- loys, and other hard-to-machine materials. sisting of a phosphoric acid solution con- Most electrical discharge machining proc- taining no metals (e.g., manganese, nickel, esses are operated dry; however, in some or zinc) or a phosphate salt solution (i.e., so- cases, the process uses water and generates dium or potassium salts of phosphoric acid wastewater containing dielectric fluid. solutions) containing no metals (e.g., man- Floor Cleaning (in Process Area) removes ganese, nickel, or zinc) other than sodium or dirt, debris, and process solution spills from potassium. Any metal concentrations in the process area floors. Floors can be cleaned bath are from the substrate. using wet or dry methods, such as Machining involves removing stock from a vacuuming, mopping, dry sweeping, and hose part (as chips) by forcing a cutting tool rinsing. Non-process area floor cleaning in against the part. This includes machining offices and other similar non-process areas is processes such as turning, milling, drilling, not included in this unit operation. boring, tapping, planing, broaching, sawing, Grinding involves removing stock from a shaving, shearing, threading, reaming, shap- part by using abrasive grains held by a rigid ing, slotting, hobbing, and chamfering. Ma- or semirigid binder. Grinding shapes or chining processes use various types of metal- deburrs the part. The grinding tool usually is working fluids, the choice of which depends a disk (the basic shape of grinding wheels), on the type of machining being performed
Details
-
File Typepdf
-
Upload Time-
-
Content LanguagesEnglish
-
Upload UserAnonymous/Not logged-in
-
File Pages4 Page
-
File Size-