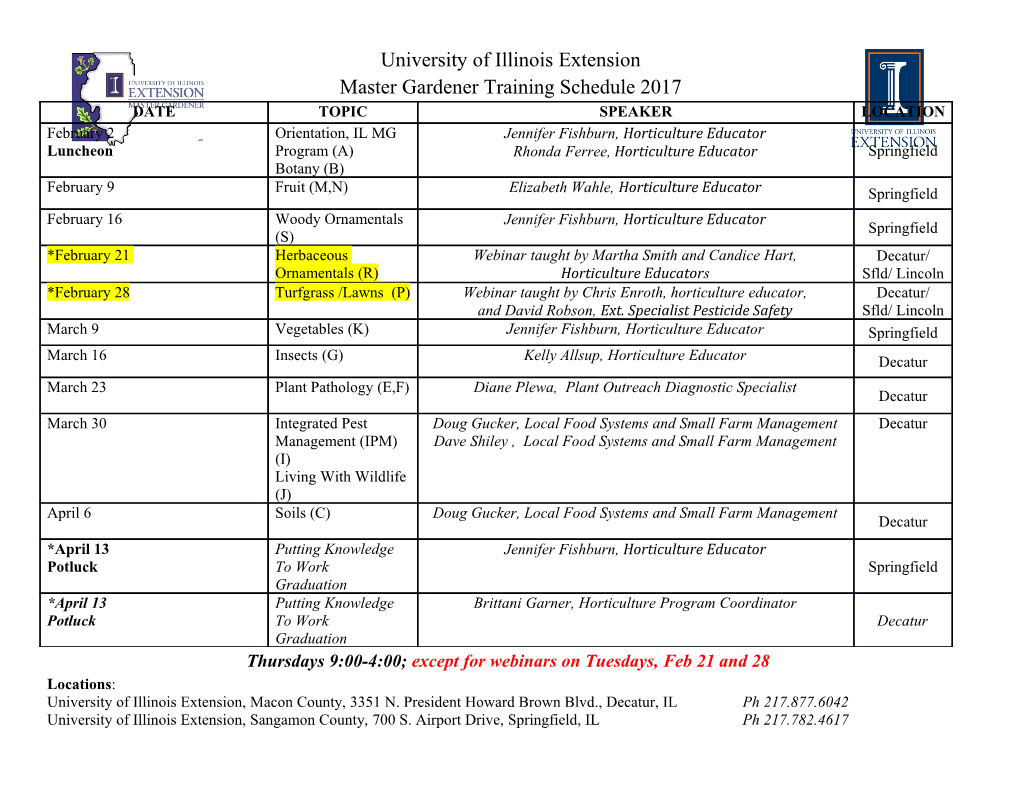
AREVA’s Technology for Safety Improvement Marina Welker Company: AREVA GmbH Address: Henri-Dunant-Str. 50, 91058 Erlangen, Germany Phone: +49 (0) 9131 900-95606 Email: [email protected] Summary – Mitigation of severe accidents in nuclear power plants (NPPs) focuses on protection of the public, the operators and plant structures/ systems. Apart from pressure reduction in the containment, also monitoring systems are required to provide the status of the plant and its equipment / systems. In addition, during severe accidents monitoring systems support the operator and authorities in making the right decisions and timely initiate the appropriate measures to mitigate the impact of a severe accident. Based on more than 30 years of experience in this field AREVA offers nuclear operators high-performance products and services to guarantee the safety of their plants. 1. INTRODUCTION Severe accidents in NPPs are linked with serious impacts on the plant itself, plant operators, the environment and the public. As Fukushima showed, they could lead to political decisions impacting the macroeconomic situation. This is another reason to pay special attention to measures which improve the safety of the plant and mitigate possible implications. In the unlikely case of a severe accident, the ability to monitor critical plant parameters and manage events becomes essential for plant operators and authorities. AREVA has developed and installed a number of dedicated technical solutions to address this need. 2. USEFUL TECHNICAL SOLUTIONS IN CASE OF SEVERE ACCIDENT 2.1. Hydrogen in the containment: generation and control In 1979 the nuclear accident of Three Miles Island directed the attention to the adverse effect on containment integrity by high H2-concentration after DBA. After the Chernobyl accident in 1986 the discussion was extended additionally taking into account severe accidents. High production of hydrogen in the reactor containment leads to a high concentration of combustible gas which might ultimately affect the integrity of the containment. The hydrogen concentration has to be kept within certain limits even under severe accident conditions. Knowing the concentration of hydrogen and reducing it is the key success factor to maintain the integrity of the containment. When considering long-term accident mitigation, passive safety systems are advantageous as they require neither operator action nor power supply. AREVA has developed passive components to reduce hydrogen, based on the principles of catalytic oxidization. There are two principles available: recombination and ignition. Historically, the igniter was the first product on the market, but the following years showed that there was more interest in the recombiners, being the safer technique. However, passive igniters as well as a combination of passive igniters and recombiners can also be provided. Page 1 of 7 The AREVA Passive Autocatalytic Recombiner (PAR) features a gas-treating capacity of up to 1500 m3/h per PAR unit and a simple, cost-effective design which is easy to integrate into existing NPPs. The PAR design is based on thin stainless steel plates coated with catalyst at a large reaction surface. It allows for low start temperatures and has proved to be very efficient in severe accident conditions. To promote natural convection the PAR has a metal housing with a gas inlet at the bottom and a lateral gas outlet at the top. Upon contact with the catalyst in the lower part of the housing, the gas mixtures containing hydrogen are recombined. The heat from this reaction causes a reduction in gas density that leads to buoyancy-driven flow, thus supplying the catalyst with a large amount of hydrogen that ensures a highly efficient recombination. The AREVA PAR is available in different sizes, which allows for the best possible arrangement in the various compartment areas. To date, AREVA has delivered and installed PAR-based H2 control systems in more than 140 NPPs worldwide, including equipment for testing and maintenance. Excellent test results were achieved even under adverse conditions such as oil fire or oil aerosols from the main coolant pump, boric acid, or a significant high concentration of organic carbon-hydrogen compounds. The AREVA PAR has been subject to extensive and long-term testing in order to evaluate it for various accident scenarios in both PWR and BWR. The most important qualification test was performed during the PHEBUS FPT3 (Fission Product Test 3) in Cadarache (France) by a third party group with participation of various authorities, research institutes and different PAR suppliers. Catalysts of various manufacturers were tested under real severe accident conditions with a degraded core for the first time. Within the scope of the EC/IRSN Core Melt Program PHEBUS (with real molten core), AREVA’s PAR showed the best performance concerning very fast start-up, highest efficiency and absolute constant hydrogen depletion rates. 2.2. Detailed information about the situation inside the containment Monitoring of the containment atmosphere, e.g., the level of hydrogen and other combustible gases, is required in case of severe accident in order to timely provide the baseline decisions for mitigating actions, e.g., filtered venting. All containment atmosphere monitoring systems from AREVA are fully qualified for BDBA conditions but can be used for normal operation as well. For hydrogen monitoring inside the containment AREVA offers the Containment Atmosphere Hydrogen Monitoring System WS85. WS85 safely measures the H2 concentrations at different locations in the containment during normal operation as well as under severe accident conditions. Thus it is possible to continuously and simultaneously monitor the area and time distribution of H2 concentrations during accident progression. The WS85 system can be installed in all types of reactors. The areas to be monitored and the position of the sensors are individually assessed for each different NPP layout. If in addition to the hydrogen concentration the oxygen concentration must be determined as well, the WS85 system can be extended to a WS85 Plus solution: in addition severe accident proven O2 sensors will be installed together with H2 sensors in this case. If more parameters (e.g., H2, O2, CO, CO2, steam concentration) must be detected, the AREVA HERMETIS Monitoring System can be installed as it is proven to operate under core melt Page 2 of 7 accident conditions. HERMETIS provides the following critical information for the severe accident management / emergency operations: released hydrogen quantities distribution of hydrogen distribution of steam containment atmosphere combustion regime (locally) potential of hydrogen combustion efficiency of hydrogen countermeasures such as recombiners / igniters occurrence of global convection indication of molten core concrete interaction / failure of reactor pressure vessel The system works with in-situ micro sampling based on capillary pipe technology. Thus, only fully metallic components are placed in harsh environment, and the entire measuring equipment is installed outside of the containment and easily accessible for operators. The superheated micro samples are transported to the analysis module placed outside the containment. With the analysis module being located outside the containment measurement errors are significantly reduced. No containment isolation valves are required due to the use of capillary technology. The system needs no operator action and allows easy maintenance and in-service inspection. The system measures the concentration of, e.g., hydrogen, oxygen, CO (and CO2, if needed) and steam. For the management of further progressing severe accidents a precise understanding of nuclide-specific radioactivity inside the containment is essential. In this situation, the atmosphere of the containment may be mixed with radiolysis products (hydrogen, oxygen), steam, noble gases, radioactive aerosols and iodine. The activity of the containment atmosphere is dominated by the noble gas activity. To estimate the potential risk to the environment in case of containment pressure release, the aerosols and iodine concentration must be determined in addition to the noble gas activity. The AREVA Post-Accident Sampling System PASS is designed to provide representative gaseous and liquid samples from the containment atmosphere and in-containment refuelling water storage tank (IRWST) or sump / wetwell following a DBA or BDBA event. The potentially highly radioactive samples are diluted to permit further analysis with normal laboratory equipment. The analysis of the samples will provide details on the containment situation, the core damage state and potential risk for the environment. An in-situ sampler collects the aerosol and elemental iodine in a scrubbing liquid. The iodine and aerosol sample is flushed to a dilution module (located outside containment) and a sample box where it can be taken for laboratory analysis. The in-situ sampling technology makes the samples transportable over long distances without significant sample measurement errors. Noble gases and organic iodine are also flushed to the outside sample module. The different samples taken from the containment atmosphere contain: aerosol bound radionuclides non-aerosol bound (gaseous) iodine isotopes radioactive noble gases Page 3 of 7 Liquid samples from the IRWST (sumps / wetwell) contain suspended and dissolved fission products. Furthermore, the information about activity of the IRWST spray water
Details
-
File Typepdf
-
Upload Time-
-
Content LanguagesEnglish
-
Upload UserAnonymous/Not logged-in
-
File Pages7 Page
-
File Size-