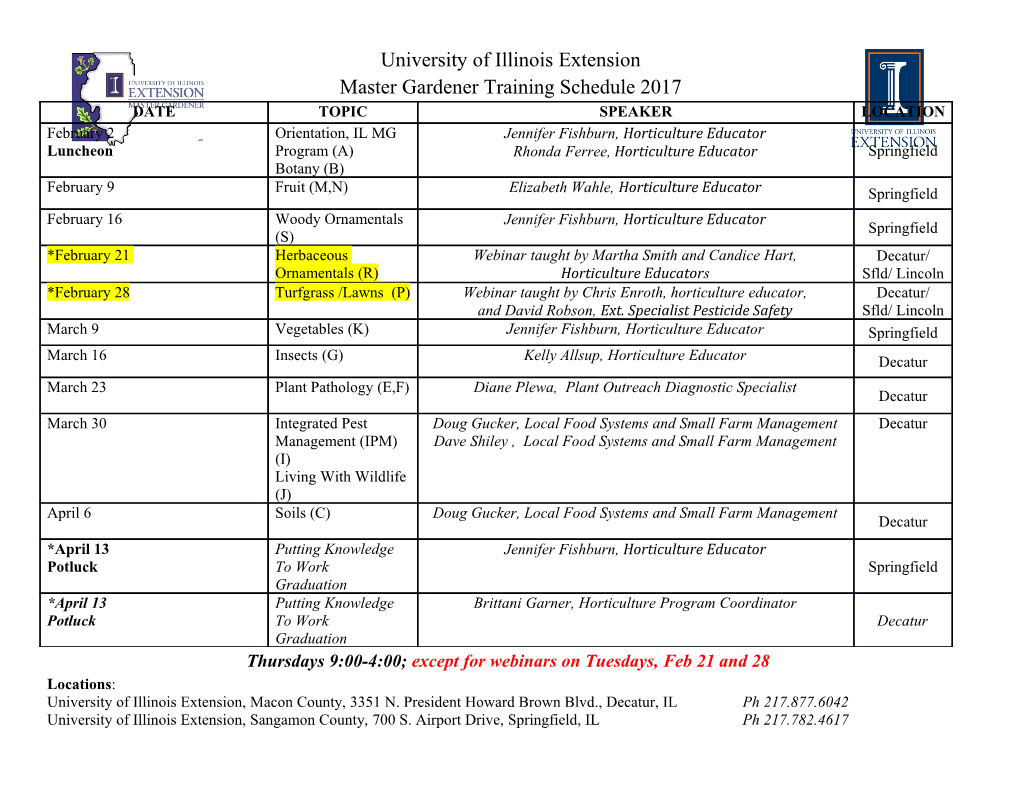
International Journal of Current Engineering and Technology ISSN 2277 - 4106 © 2013 INPRESSCO. All Rights Reserved. Available at http://inpressco.com/category/ijcet Research Article Performance Evaluation of an IC Engine in the Presence of a C-D Nozzle in the Air Intake Manifold S.Ravi Babu*a, K.Prasada Raoa and P.Ramesh Babua aDepartment of Mechanical Engineering, GMR Institute of Technology, Rajam, India Accepted 10 August 2013, Available online 01 October 2013, Vol.3, No.4 (October 2013) Abstract The present day energy crisis and ever increasing demands of energy in addition to global pollution brought us into a situation where there is an urgent need for energy conservation, efficient utilization and eco-friendly techniques to be implemented in day to day use. These needs lead us to an idea of modified design in a CI engine without any additional energy requirement and with no complicated variations in design. There are various other methods to improve the efficiency of engine such as super charging, turbo charging, varying stroke length, varying injection pressure, fuel to air ratio, additional strokes per cycle and so on. Many of them require additional design (stroke length, injection pressure etc.,) and some of them load to increase environmental effect. Here in this project affords were made to increase the velocity (physical parameter) of air entering the inlet manifold of the engine by inserting a convergent divergent nozzle at the inlet manifold. There by increasing the mixture quality of air & fuel in the combustion chamber before the initialization of ignition. The engine load tests were carried out at different loads, variation of different parameters with load was plotted. The nozzle setup was installed and then again load test were carried out at different loads and the values were plotted in comparison to former values. The emissions from the engine were also tested before and after the setup installation to estimate the environmental effects. The comparative results were also plotted. Keywords: I.C Engine, diesel engine, Performance characteristics, Emission control. 1. Introduction piezoelectric wafers in lieu of a solenoid, giving finer control of the injection event (M.chandramouli et al, 1A diesel engine (also known as a compression-ignition 2009). Variable geometry turbochargers have flexible engine) is an internal combustion engine that uses the heat vanes, which move and let more air into the engine of compression to initiate ignition to burn the fuel that has depending on load. This technology increases both been injected into the combustion chamber. The diesel performance and fuel economy. Boost lag is reduced as engine has the highest thermal efficiency of any regular turbo impeller inertia is compensated for. Accelerometer internal or external combustion engine due to its very high pilot control (APC) uses an accelerometer to provide compression ratio. Low-speed diesel engines (as used in feedback on the engine's level of noise and vibration and ships and other applications where overall engine weight thus instruct the ECU to inject the minimum amount of is relatively unimportant) can have a thermal efficiency fuel that will produce quiet combustion and still provide that exceeds 50%. Diesel engines are manufactured in the required power (especially while idling). The next two-stroke and four-stroke versions. They were originally generation of common rail diesels is expected to use used as a more efficient replacement for stationary steam variable injection geometry, which allows the amount of engines. Since the 1910s they have been used in fuel injected to be varied over a wider range (Mohan raj et submarines and ships. Use in locomotives, trucks, heavy al, 2009), and variable valve timing (see Mitsubishi's equipment and electric generating plants followed later. In 4N13 diesel engine) similar to that on petrol engines. the 1930s, they slowly began to be used in a few Particularly in the United States, coming tougher automobiles. Since the 1970s, the use of diesel engines in emissions regulations present a considerable challenge to larger on road and off-road vehicles in the USA increased. diesel engine manufacturers. Ford's HyTrans Project has As of 2007, about 50% of all new car sales in Europe are developed a system which starts the ignition in 400 ms, diesel. saving a significant amount of fuel on city routes, and As of 2013, many common rail and unit injection there are other methods to achieve even more efficient systems already employ new injectors using stacked combustion, such as homogeneous charge compression ignition, being studied. Japanese and Swedish vehicle manufacturers are also developing diesel engines that run *Corresponding author: S.Ravi Babu 1158 S.Ravi Babu et al International Journal of Current Engineering and Technology, Vol.3, No.4 (October 2013) on dimethyl ether (DME) (Asad et al, 2009). Some recent is nearly constant). At subsonic flow the gas is diesel engine models utilize a copper alloy heat exchanger compressible; sound, a small pressure wave, will technology to take advantage of benefits in terms of propagate through it. At the throat, where the cross thermal performance, heat transfer efficiency, sectional area is a minimum, the gas velocity locally strength/durability, corrosion resistance, and reduced becomes sonic (Mach number = 1.0), a condition called emissions from higher operating temperatures. choked flow. As the nozzle cross sectional area increases M.Chandramouli et al. (M.chandramouli et al, 2009) the gas begins to expand and the gas flow increases to selected a four stroke compression ignition engine with supersonic velocities where a sound wave will not power 9 H.P and rated speed 1500 rpm to investigate the propagate backwards through the gas as viewed in the performance characteristics. The swirl motion of the air is frame of reference of the nozzle (Mach number > 1.0). an important parameter in optimizing the performance of A de Laval nozzle will only choke at the throat if the the engine. In order to increase the air velocity in the inlet pressure and mass flow through the nozzle is sufficient to manifold a convergent-divergent nozzle is used. The rise reach sonic speeds, otherwise no supersonic flow is in velocity with the use of nozzle generates turbulence at achieved and it will act as a venturi tube; this requires the the exit of the manifold which facilitates for better entry pressure to the nozzle to be significantly above combustion of injected fuel. The Performance ambient at all times (equivalently, the stagnation pressure characteristics were calculated with nozzle and without of the jet must be above ambient). nozzle in the inlet manifold and compared (V.CVS Phaneendra et al, 2009). 2. Analysis of gas flow in De Laval nozzles. A de Laval nozzle (or convergent-divergent nozzle, CD nozzle) is a tube that is pinched in the middle, making The analysis of gas flow through de Laval nozzles a carefully balanced, asymmetric hourglass-shape. It is involves a number of concepts and assumptions: used to accelerate a hot, pressurized gas passing through it For simplicity, the gas is assumed to be an ideal gas. to a supersonic speed, and upon expansion, to shape the The gas flow is isentropic (i.e., at constant entropy). exhaust flow so that the heat energy propelling the flow is As a result the flow is reversible (frictionless and no maximally converted into directed kinetic energy. Because dissipative losses), and adiabatic (i.e., there is no heat of this, the nozzle is widely used in some types of steam gained or lost). turbines, and is used as a rocket engine nozzle. It also sees The gas flow is constant (i.e., steady) during the use in supersonic jet engines (Ganeshan). period of the propellant burn. The gas flow is along a straight line from gas inlet to exhaust gas exit (i.e., along the nozzle's axis of symmetry) The gas flow behavior is compressible since the flow is at very high velocities (Mach number > 0.3). 2.1 Exhaust gas velocity As the gas enters a nozzle, it is traveling at subsonic velocities. As the throat contracts down the gas is forced to accelerate until at the nozzle throat, where the cross sectional area is the smallest, the linear velocity becomes sonic. From the throat the cross sectional area then increases, the gas expands and the linear velocity becomes progressively more supersonic. The linear velocity of the exiting exhaust gases can be calculated using the following equation 1 TR 2 P [1 ] M 1 p Where Fig.1 De-laval nozzle showing approximate velocity (v), = Exhaust velocity at nozzle exit m/s together with the effect on temperature (T) and pressure T= absolute temperature of inlet gas, K (P). R= Universal gas law constant=8314.5 j/(kmol-k) M= the gas molecular mass, kg/kmol Its operation relies on the different properties of gases = isentropic expansion factor flowing at subsonic and supersonic speeds. The speed of a C = specific heat of the gas at constant pressure subsonic flow of gas will increase if the pipe carrying it p C = specific heat of the gas at constant volume narrows because the mass flow rate is constant. The gas v P= absolute pressure of exhaust gas at nozzle exit, Pa flow through a de Laval nozzle is isentropic (gas entropy 1159 S.Ravi Babu et al International Journal of Current Engineering and Technology, Vol.3, No.4 (October 2013) 3. Design of the nozzle the fuel is injected directly into the cylinder. The increased turbulence causes better cooling of the cylinder surfaces thereby reducing the heat loss to the surroundings. The heat from the cylinder walls gets absorbed by the air supplied during suction and used for reducing the delay period thereby increasing the thermal efficiency of the engine.
Details
-
File Typepdf
-
Upload Time-
-
Content LanguagesEnglish
-
Upload UserAnonymous/Not logged-in
-
File Pages6 Page
-
File Size-