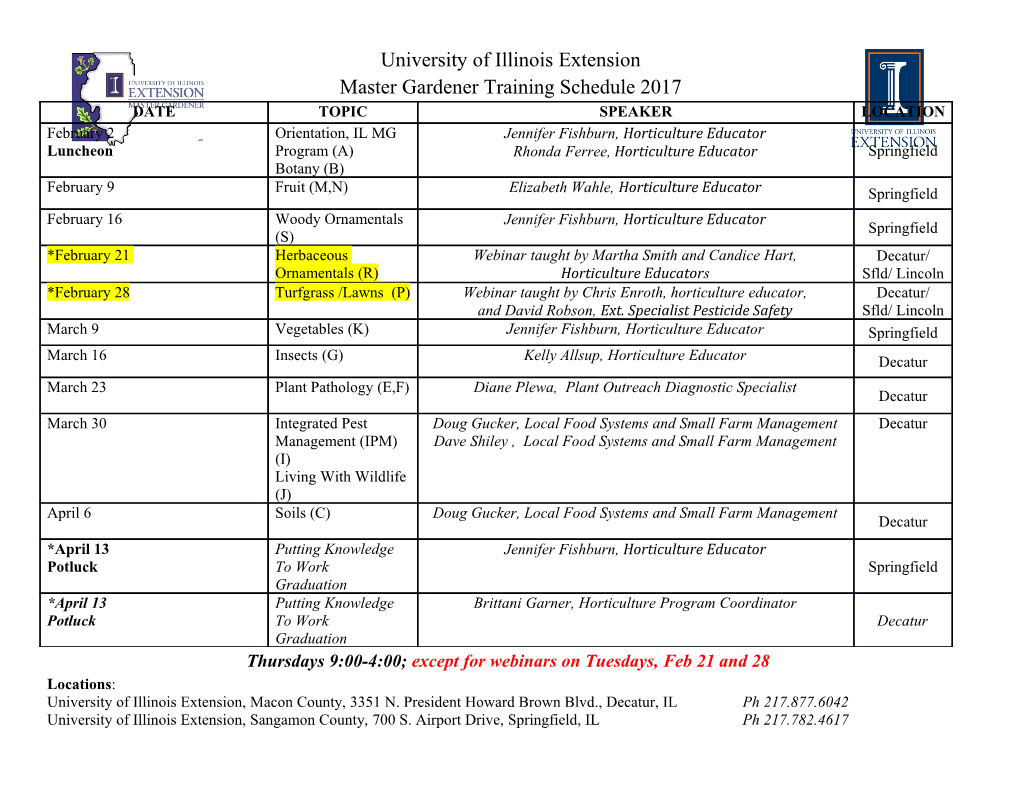
The Institution of Engineers (India) All India Seminar on BEST PRACTICES AND APPLICTIONS OF TQM IN INDUSTRY AND ACADEMIA 16-17 November 2019 Organized by The Institution of Engineers (India) Karnataka State Centre Under the Aegis of Production Engineering Division Board, IEI In association with IEI, Belagavi Local Centre & Department of Mechanical Engineering S. G. BALEKUNDRI INSTITUTE OF TECHNOLOGY, BELAGAVI Venue Seminar Hall-1 Department of Mechanical Engineering S. G. BALEKUNDRI INSTITUTE OF TECHNOLOGY, BELAGAVI Shivabasavanagar, Belagavi 590010 All India Seminar on BEST PRACTICES AND APPLICTIONS OF TQM IN INDUSTRY AND ACADEMIA, Karnataka State Centre, 16-17 November 2019 PAPERS PRESENTED IN THE ALL INDIA SEMINAR A STRUCTURED APPROACH FOR IMPLEMENTATION OF INTEGRATED MANAGEMENT SYSTEMS Dr CKB Nair Member, Production Engineering Division Board, IEI Email: [email protected], Mobile +919482048324 Website : www.bravee.net Some of the generic ISO standards currently used in the industrial units across the globe are the ISO 9001:2015 for Quality Management Systems, ISO 14001:2015 for Environmental Management systems, ISO 27001:2013 for Information security management systems, ISO 45001:2018 for Occupational Health and Safety Management Systems and ISO 50001:2018 Energy Management Systems. Leadership, Involvement of personnel, Process approach, Systematic approach to management, Factual approach to decision making and Continual improvement are some the main basic principles for these standards. These standards help the organisations to have a common mode of communication for dealing with all stakeholders and merge with the global economy. Instead of implementing all these five standards individually, an integrated approach for implementation can save time and efforts. For this a standard methodology using flow charts and a simple software is developed to help facilities get certified by checking whether the management systems comply with the required standards. This software can be a guiding tool for all stakeholders to understand requirements of various standards. This work also includes building a database in the software to store all the documents and records in an organized manner as required in the standard. This database would make the auditing process of documents and records simpler for both the auditor and organization. 1 All India Seminar on BEST PRACTICES AND APPLICTIONS OF TQM IN INDUSTRY AND ACADEMIA, Karnataka State Centre, 16-17 November 2019 BEST PRACTICES IN AUTOMOBILE INDUSTRY IN AFTER SALES SERVICE OF PASSENGER CAR SEGMENT IN SKILL ACQUISITION OF SERVICE PERSONNEL FOR T.Q.M. Dr. D. Dave, Professor- Marketing Management, Sardar Patel University, Valabh Vidhyanagar, Anand. Er. Ravi Menaria, BE (Automobile Engg),MBA, Dip T&D. [email protected] Abstract Automobile Industry and Transport sector counts for the largest number of People employed across the Globe. In India there are 23 cars per 1000 person where as In USA : 870 Cars per 1000 person. Now it is beyond comparison that India being most Populous country and our CAGR for Automobile Industry has remained considerably higher almost touching double digit (7 ~ 9) Indian Automobile Industry consists of mainly - Two Wheeler Segment, Commercial Vehicle Segment and Passenger Car Segment. Out of these three Segments Passenger Car Segment is most lucrative in terms of Revenue generation because Indians treat their Cars as part and parcel of Family. Customer Satisfaction is confined to three parameters namely Timely Repair of Car, Genuine Services rendered and Fair charges for Repair. Training is a Quality deployment tool which can enhance Customer Retention if everything is Transparent and nothing is ambiguous. Training for Service Staff beginning from Customer Relationship Executive – Front Desk Executive – Service Advisor – Cashier – Office Boy – Gate Pass clerk and culminates at Security Staff depositing Gate Pass cum Customer Satisfaction Note. Total Quality Management is reliability of Service Provider is good and it has no errors. We have to make Customer smile and also to ensure that at each and every step form Customer Relationship Executive to Security Staff it is religiously being followed. SERV - QUAL is more applicable here. Key Words- 2 All India Seminar on BEST PRACTICES AND APPLICTIONS OF TQM IN INDUSTRY AND ACADEMIA, Karnataka State Centre, 16-17 November 2019 Automobile Industry – Labor Intensive Industry – Volume of Human Resource employed – Training Need Identification – Training Need Assessment – Customer Satisfaction – Customer Retention – Location of Workshop – Time spent on Automobile – Next Appointment – Feedback and Need for Improvement – Soft Skills – Technical Skills – Return on Investment. 3 All India Seminar on BEST PRACTICES AND APPLICTIONS OF TQM IN INDUSTRY AND ACADEMIA, Karnataka State Centre, 16-17 November 2019 TOTAL QUALITY MANAGEMENT (TQM) – ZERO EFFECT ZERO DEFECT (ZED) Suhas S D, Sharanabasappa C. Sajjan Department of Mechanical Engineering, K.L.E INSTITUTE OF TECHNOLOGY HUBLI, India. sajjansc@gmail. com [email protected] Abstract: The concept of Zero Defect Zero Effect is addressed by Honorable Prime Minister on 68th Independence Day. This concept mainly focuses on Micro Small and Medium Enterprise (MSME) that the goods they manufacture in the country with “Zero Defects” and ensure that the produced goods must have “Zero Effect” on the environment. Zero Defect focus on the customer, which has concern to zero nonconformance, noncompliance and zero waste. Zero Effect mainly focuses on society, and has concern on Air pollution, Solid Waste, Liquid Discharge (ZLD), Zero wastage of natural resources. This particular concept may be applied to all sectors of manufacturing and servicing industry. Keywords: Zero Defect, Zero Effect, Customer, Society, nonconformance, natural resources. WHAT IS TQM? Firstly TQM stands for Total Quality Management. The total quality concept and the term “total quality management” was first introduced to the western business world by Armand Feigenbaum in 1957, in the first edition of his book “Total Quality Control”. TQM has proved the most persisting management theory in industries and businesses. Quality management is a part of management aimed at achieving quality goals through planning, monitoring, assuring and improving quality. Involving all members of the organization brings us closer to total quality control (total quality management, TQM). Efficient TQM system in organization can facilitate quickly challenge in word market. Although many approaches exist for quality management, arguably, TQM is the most comprehensive approach 4 All India Seminar on BEST PRACTICES AND APPLICTIONS OF TQM IN INDUSTRY AND ACADEMIA, Karnataka State Centre, 16-17 November 2019 for quality management for all the sectors. Total Quality Management (TQM) is an organized approach for quality improvement along together with product and service specifications to customer performance. TQM is applying to target producing these specifications with zero defects. This makes a worthy cycle of constant improvement for production, customer satisfaction and profits. Total Quality Management (TQM) is not only adopted by a single person or an employee but all employees can become involved (including top management to shop floor management, in other words total or complete involvement, hence, Total) for the continuous improvement of the production of goods and services within the framework of organizations to strive for excellence in everything they do to achieve best quality standards ( customer satisfaction to the quality, hence, Quality) by its integrated well-managed (quality can and must be managed with best practiced system or tools hence, Management) system of various best practiced principles, methods. Continuous Improvement: TQM involves a better process thinking approach. It recognizes that everything done at all level is part of a process not any extra burden, it also includes how well each part of the process works and the relationship of each part to the process for constant perfection, e.g. The Plan-Do-Check-Act cycle is a continuous quest of quality, which is firmly driven in TQM. According to the need, a variety of methods are implemented for TQM. 5 All India Seminar on BEST PRACTICES AND APPLICTIONS OF TQM IN INDUSTRY AND ACADEMIA, Karnataka State Centre, 16-17 November 2019 Figure 1 http://www.drshrutibhat.com/continuous-improvement.html The need of TQM In fact earlier the concept of "mass production" was existed in which whatever goods produced became demanded in market i.e. market trend of 'sales oriented' or 'product oriented', here a manufacturer known as king , but completely the opposite scenario is seen today , the market is became "customer oriented" or 'demand oriented' where customer became a king. So, it is obvious to cope up with the various products demand with the great satisfaction of products, ease of delivery and competitive pricing, manufacturers must have to make continuous changes. MODERN INDUSTRY APPROACH FOR ZERO DEFECTS Due to economic changes the world has brought about complications and increasing day to day level of competition in each and every sector of industry. As a whole productivity is one of the most important criteria in competitive market of each sector, nation or an industry. Quality output is a state of being able to perform in this competitive world. It is related with the 6 All India Seminar on BEST PRACTICES AND APPLICTIONS OF TQM IN INDUSTRY AND ACADEMIA, Karnataka
Details
-
File Typepdf
-
Upload Time-
-
Content LanguagesEnglish
-
Upload UserAnonymous/Not logged-in
-
File Pages20 Page
-
File Size-