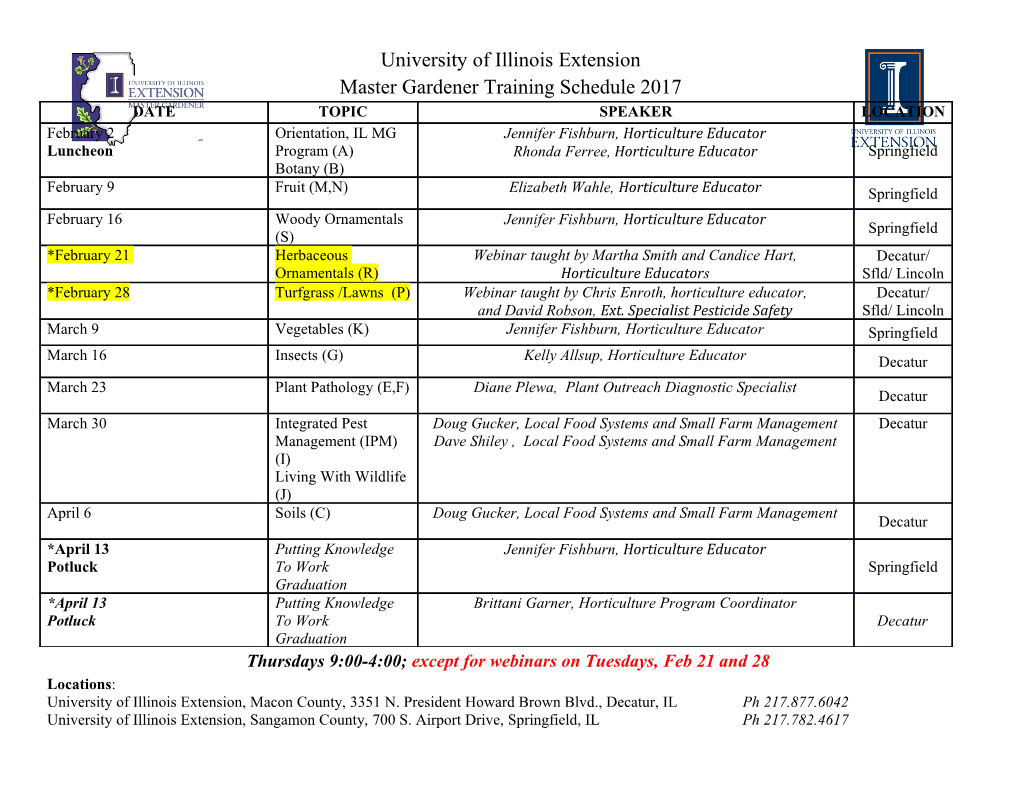
All-SiC telescope technology at EADS-Astrium Big step forward for space optical payloads Jacques Breysse / Didier Castel Earth Observation & Science, Michel Bougoin Optical Instruments Directorate Boostec, a company of Mersen group Astrium Satellites Bazet, France Toulouse, France [email protected] [email protected] [email protected] Abstract—Ceramic mirrors and structures have become Thus, the optics needs to be larger and larger to achieve higher extremely attractive for high precision light weighted opto- spatial resolution, accuracy or light flux collection when mechanical applications. Developments over the past years by observing Earth or the Universe. That is why, it was mandatory Boostec and EADS-Astrium have demonstrated the feasibility to find and develop materials with very good optical, thermo- and versatility of the Sintered SiC material for numerous mechanical, and lightweight properties such as Silicon Carbide applications. The incomparable properties of the Boostec® Silicon Carbide material combined with more than 20 years to meet ambitious mission requirements. efforts to develop a large range of joining processes, allows for Recent EADS-Astrium developments have shown the large size light weighed space applications and systems. In the growth potential of the SiC technology. If originally S-SiC framework of earth and scientific observation, high and very applications were limited to small size instruments and mirrors, high-resolution optical payloads have been developed by EADS- recent payload developments, have allowed demonstrating the Astrium and its partner Boostec. Since the beginning of this new ability of this technology to achieve the more and more century, seven SiC instruments have been launched; they are demanding performances for the on-going and future successfully operating in space. More than ten instruments are programs. SiC manufacturing processes and manufacturing under development, most of them being already tested and qualified. It means the manufacturing and testing of more than facilities, at Boostec premises, have also evolved to comply 150 SiC mirrors and structural parts for space applications with the current and future very large space instrument and under environmental conditions varying from 300 K to a few mirrors needs. They are currently able to produce mirrors and Kelvin. This unique experience acquired by EADS-Astrium and structures up to 3.8 meters diameter, i.e. close to the limitation its partner allows now to propose the Boostec® SiC technology provided by the largest launcher fairings for the benefit of a large and complete range of space-based S-SiC has become a new generation space material. This system for optical observation. paper provides an overview of the S-SiC properties, its manufacturing processes for mirrors and structures, and its Index Terms—Ceramic, Sintered Silicon Carbide, large optical application on space optical payloads. payloads, lightweight mirrors and structures. I. INTRODUCTION II. BOOSTEC® SIC KEY PROPERTIES Over the past twenty years EADS-Astrium has developed the Sintered Silicon Carbide (S-SiC) technology for Space Sintered SiC mechanical and thermal properties presented Applications in collaboration with a ceramic manufacturer: in the Figure 1 highlight its high stiffness and its high thermo- Boostec company (Tarbes, France). Its unique thermo- mechanical stability. S-SiC provides a number of technical mechanical properties, associated with its polishing capability, advantages, as a result of superior material properties. make S-SiC an ideal material for building ultra-stable Boostec® SiC has outstanding properties. The main lightweight space based telescopes or mirrors. S-SiC is a cost features and advantages of SiC are as follows: effective alternative to Beryllium and the ultra-lightweight A fundamental reason for the success obtained with ULE/Zerodur technologies. In complement to the material Boostec S-SiC material is that the material is extremely manufacturing process, EADS-Astrium has developed several homogeneous, featuring very low in-built stresses and assembly techniques (bolting, brazing, bonding,…) to a single-phase crystalline microstructure. Performances manufacture large and complex SiC assemblies[2]. reproducibility from batch to batch secures the Nowadays, the necessity to always go further in the development of space instruments. S-SiC has also exploration of the Space requires the observation instruments isotropic properties (Isotropic characteristics of CTE, sent in the Space to continuously improve their performances. thermal conductivity and mechanical properties) facilitating optical payloads dimensioning and behavioral prediction. This is in a large part due to the fine grained SiC powder used and cold isostatic pressing (CIP) technique; the combination of both III. RECALL OF MANUFACTURING PROCESS gives a higher degree of homogeneity and isotropy Silicon Carbide (SiC) is a compound of Silicon and than obtained in other competing types of SiC; Carbon. It is obtained from the chemical reaction between furthermore, after sintering, the density is close to that silica sand and coke carbon at very high temperature. of pure SiC. Contrary to reaction bonded SiC, no Nowadays, SiC is industrially manufactured for many secondary operations are required such as high applications. The major manufacturing steps of a Sintered SiC temperature silicon infiltration (that can result in an blank are recalled below. anisotropic and an inhomogeneous material) or sand- Boostec® SiC raw material is a premix of fine SiC powder blasting for surface molten SiC removal (that can (< 1 µm grain size), sintering additives and temporary binders. introduce surface defects). This material is isostatically pressed (pressure > 1400 bars) at Its low specific density (< 3.2 g/cm³) associated to a room temperature into a machinable blank. The so called green very high stiffness (420 GPa) and a high bending body shows quite no internal stress. strength (>350 MPa) allows stiff, very lightweight This green body is then machined with the help of high optical systems to be produced. It also makes simple speed CNC milling machines. This near-net-shape the zero-g testing. manufacturing process allows complex, light-weighted optical Its low coefficient of thermal expansion (CTE: 2.2 x and structural elements to be produced with very little post- 10-6K-1 at room temperature and near zero below machining. During the last ten years, BOOSTEC has 100K) combined with a very high thermal conductivity continuously improved the reliability and also the speed of its (~ 180W/m.K) and high thermal capacitance (Cp > 650 process. Software for programming the CNC milling machines J/kg.K) allows visible quality imaging in the presence and also to verify the machining programs has been invested, of stressing, and changing thermal loads condition. allowing the green machining of very complex 3D shapes. It This makes it a reference material to achieve the therefore provides significant schedule advantages compared to stringent thermo-elastic performances of space optical the state-of-the-art for low expansion glass-ceramics. These payloads over a broad operating temperature range technical and manufacturing advantages become even more from a few K (cryogenic) to 300 K or even higher for significant as the payload aperture increases, and/or as the high energy applications (~1800K) unlike composites number of units increases. S-SiC is uniquely well suited to and glass. Passive a-thermal systems have been address future needs associated to very large space produced, demonstrating the ability of the material to applications. provide high quality imaging, without the need of Then the machined green body is pressure-less sintered at actively controlled focus adjust mechanisms. about 2000 °C under protective atmosphere. Organic binders Its stability over time: Insensitive to space radiations are removed during sintering process and the material is made (no degradation for 200Mrad Gamma rays), no aging of > 98.5% SiC. This is the reason why S-SiC properties are or creep deformation under stress, no moisture very homogeneous thus enabling both a good size control and sensitivity, no outgassing, no residual stresses, high an easy polishing. The sintering gives an isotropic shrinkage of fatigue, corrosion and abrasion resistance making it SiC parts. Nevertheless, the uncertainty on the size of the reliable for long term space mission and allowing rapid sintered component remains below 0.4%. on-orbit data acquisition. When deemed necessary, fine grinding, optionally lapping the interfaces or polishing the optical faces is performed after S-SiC Béryllium Zerodur HB CeSiC Si3N4 Aluminium sintering phase. class 0 Alloy 6061 Boostec Brushwellman Schott ECM-Melco FCT Mechanical proof-testing, final check and cleaning is 2879235030070 Young modulus : E GPa 420 performed prior S-SiC part delivery. 3 Density: kg/dm 3,2 1,9 2,6 3,0 3,3 2,7 To achieve the development of the Herschel telescope, CTE :.10-6 m/m-K 2,2 11,3 0,02 2,3 1,0 23,0 Thermal conductivity: W/m-K 180 216 2 145 25 167 Boostec has enlarged and validated S-SiC manufacturing Specific heat : Cp J/kg-K 680 1900 810 710 [710] 900 facilities, from the SiC powder preparation up to the final Specific rigidity : E/ 131 155 36 118 92 26 grinding. Therefore, processes and facilities are now fully Thermal steady state : / 82 19 80 63 25 7 Thermal diffusivity : ( xCp) x 1000 83 611 691169 qualified
Details
-
File Typepdf
-
Upload Time-
-
Content LanguagesEnglish
-
Upload UserAnonymous/Not logged-in
-
File Pages9 Page
-
File Size-