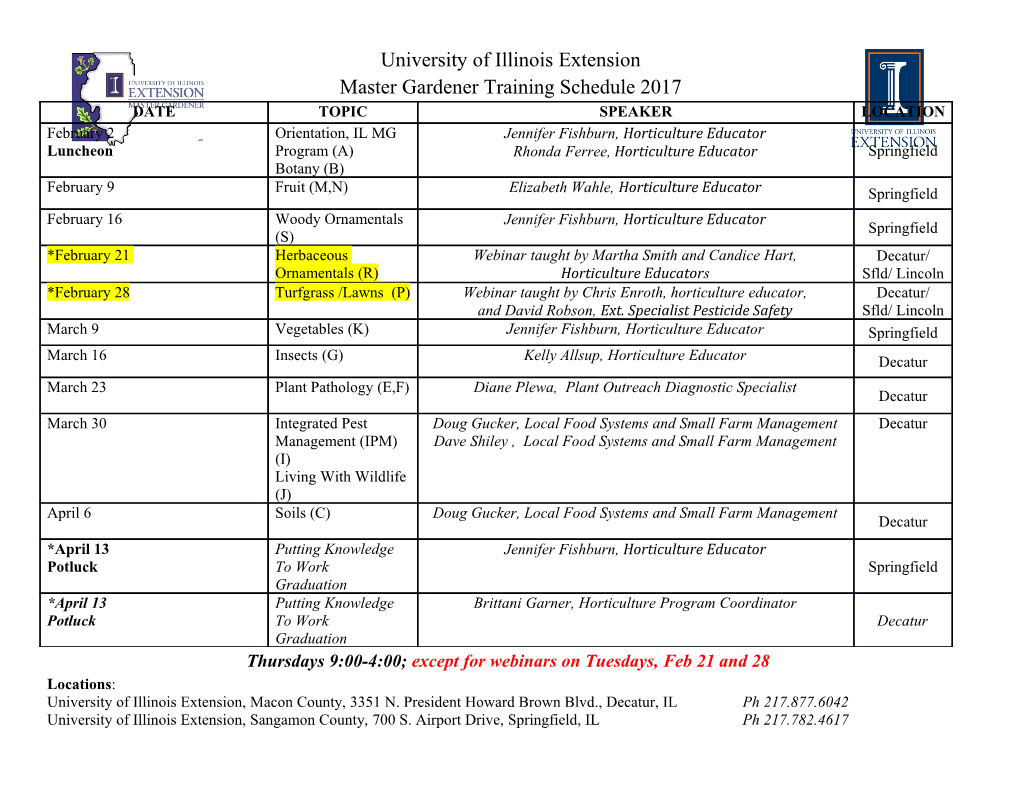
Metrology Studies and Baseplate-Pixel Sensor Gluing of the Pixel Strip Modules for the CMS II Phase Upgrade Supervisors: Author: James Keaveney Jem Aizen M. Guhit Marino Missiroli Abstract The upcoming High-Luminosity (HL) upgrade to the Large Hadron Collider (LHC) has set in motion the Central Muon Solenoid (CMS) Phase II Upgrade on its silicon tracker. To withstand the problems the current tracker cannot solve, such as the increase in data rates, pile up, and radiation damage, a new module with two silicon sensors closely spaced in a sandwhich configuration is capable of discriminating between high and low transverse momentum. This configuration allows the tracker to provide information in the first level trigger decision. In order to prolong the lifetime of the modules during operation, an efficient cooling system has to be embedded within the components. This report outlines the advances and improvement made on the gluing techniques between the baseplate and pixel sensor of the pixel strip (PS) modules. The techniques were tested and produced promising results. Also, another important studies made was on the alignment of the silicon sensors. Methods on Metrology were developed using the capabilities of the newly commissioned microscope in the Detector Assembly Facility (DAF) at DESY. A relative angular tilt was found between the XY Stage and the microscope, which was then analytically calculated and was used as a correction to the measured values. These measurements were compared to the previous SmartScope Data. Table of Contents 1 Introduction 3 1.1 The Large Hadron Collider . 3 1.2 HL - LHC . 3 1.3 CMS Experiment . 4 1.4 CMS Phase II Tracker Upgrade . 4 1.5 Pixel Strip Module . 5 1.5.1 Baseplate-Pixel Sensor Gluing . 5 1.5.2 Metrology . 6 2 Equipment and Software 6 3 Baseplate-Pixel Sensor Gluing 7 3.1 Previous Method . 7 3.2 New Proposed Method . 8 4 New Method Trials 9 4.1 Trial 1 . 9 4.1.1 Trial 1: Results and Observations . 10 4.2 Trial 2 . 10 4.2.1 Trial 2: Results and Observations . 12 4.3 Trial 3 . 13 4.3.1 Trial 3: Results and Observations . 14 5 Metrology 15 5.1 Horizontal and Vertical Method . 15 5.1.1 Results . 16 5.2 Diagonal Method . 16 5.2.1 Results . 17 5.3 Problems and Calibration . 17 5.4 Corrections . 18 5.5 Misalignment Angles . 22 5.5.1 Horizontal and Vertical Line Method . 22 5.5.2 Diagonal Line Method . 23 6 Conclusion 24 7 Next Steps 24 2 1 Introduction 1.1 The Large Hadron Collider The Large Hadron Collider (LHC) is one of the worlds largest and powerful particle acceler- ator. The LHC can accelerate different particles ranging from protons and heavy ions, and has facilitated collisions such as protons (p-p), lead ions (Pb-Pb), and protons on lead ions (p-Pb). With the current capabilities of the LHC, the collision rate of p-p collisions increased steadily, with instantaneous luminosities of up to 2:1 × 1032cm−2s−1 in 2010, continuing to 7:7 × 1033cm−2s−1 in 2012, and finally to 1:5 × 1034cm−2s−1 in 2016, which exceeded the LHC's initial design luminosity value of 1:0 × 1034cm−2s−1. [1] Figure 1: The Large Hadron Collider at CERN and its experiments [2] 1.2 HL - LHC Due to the excellent performance of the LHC and its experiments, as shows in Figure 1, a proposal has been made and approved to upgrade the accelerator to instantaneous peak luminosities of 5 × 1034cm−2s−1. The HL-LHC upgrade will greatly expand the physics potential of the LHC, in particular for rare and statistically limited standard model (SM) and beyond standard model (BSM) processes. Figure 2 shows LHC's timeline of runs, shutdowns, and scheduled upgrade. Figure 2: High-Luminosity LHC Timeline [3] 3 1.3 CMS Experiment The Compact Muon Solenoid (CMS) Experiment is a general-purpose detector designed in the LHC to observe physics phenomena. CMS can be likened to a camera, which take photographs of particle collisions from all directions at a frequency of 40 MHz [4]. Even though particles produced in the primary collisions are unstable, they quickly transform into stable particles (photons, electrons, and hadrons) that can be detected. The identification of stable particles per collision, measurement of momenta and energy are needed to reconstruct the image of the collision. Figure 3: The CMS Detector and its dimen- Figure 4: A Transverse Slice through sions [5] the CMS Detector [6] In Figure 3, it can be observed that the CMS detector is compact for the material it contains with dimensions 15 metres high and 21 metres long. It is also is designed to detect muons accurately and consists of a large solenoid magnet with a magnetic field of 4 Tesla. On the other hand, Figure 4 shows a transverse slice of the detector which shows the individual components that have different purposes: Bending of Particles, Identifying Tracks, Measuring Energy, and Detecting Muons [4]. 1.4 CMS Phase II Tracker Upgrade Due to the increase in luminosity, the current tracker of the CMS would experiences some problems: • Increase in Data Rates: the current tracker cannot handle the increased event rates and readout of data • Increase in Pile-Up: Occurs due to multiple interations because of the increase in collisions • Radiation Damage: the current tracker would deteriorate exponentially and cannot withstand the demands of high luminosity Therefore, the upgrade needs a new tracker that can provide information for the first level trigger decision at the hardware level. The Pixel Strip (PS) Modules are currently being researched, commissioned, and prepared for the upcoming HL-LHC upgrade in 2024. [1] 4 1.5 Pixel Strip Module Figure 5: Exploaded view of the Figure 6: Triggering at Hardware Pixel Strip (PS) Module [7] Level [7] The Pixel Strip (PS) Module is composed of two closely spaced silicon sensors in a sandwhich configuration that allows the module to measure track momentum, as shown in Figure 5. It is designed with two silicon sensors on top of each other separated by a spacer and attached to readout electronics. This configuration can do tracking at a hardware level, as shown in Figure 6, the red lines called "stubs" represent the momentum of a particle. Due to the strong solenoid magnet of the CMS, the bending of particle is characterized by its momentum, high transverse momentum bend less than low transverse momentum particles. Hence, the PS Module can discriminate between high and low transverse momenta. 1.5.1 Baseplate-Pixel Sensor Gluing To meet the demands of the high-luminosity upgrade, the PS Module must sustain a long lifetime. In order to prolong the operation of the modules, efficient cooling is crucial within the components. The basic idea is when an ionized particle hits the silicon detector, it disrupts the silicon's crystal lattice structure which produces electron-hole pairs. With the silicon sensor's built in applied voltage (band gap) and electric field, it produces a leakage current that hits either the pixel or strip electrode which are then known as readouts of the particle being detected. However, due to the silicon's crystal lattice structure, the bonds are only intact when the temperature is 0 Kelvin. However, that is not always the case. Therefore as the temperature increases, even there is no charged particle hitting the silicon sensors, there will be production of electron-hole pairs and will produce more leakage current at the electrodes. However, increase in leakage current generates more heat, which becomes a cycle shown in Figure 7. Figure 7: Radiation damage on silicon sensors and relationship to cooling The contact in between the cooling the component is mediated by a glue layer. Therefore, a gluing technique has to be developed in order to produce a good thermal contact between the components of the module. A good thermal contact can be characterized as a thin glue layer with minimal air bubbles, because thin layer increases the amount of dissipated heat and the presence of air bubbles inhibits cooling. 5 1.5.2 Metrology Another important aspect of the PS Module is the alignment of the components. The Detector Assembly Facility (DAF) in DESY has commissioned a new microscope that can be used to measure the relative angular alignment between the two silicon sensors. The goal of the metrology study is to test the new microscope and compare the calculations from the SmartScope Machine (the machine previously used to measure the alignment of the sensors). 2 Equipment and Software For the baseplate-pixel sensor gluing, an automated assembly has been commissioned for building the PS Modules. The hardware as shown in Figure 8 is operated by a developed computer software. Figure 8: Automated Assembly Hardware Parts Figure 9: Rotational Stage Parts Important parts that were used: • Mechanical Arm: controls z-axis movements • Vacuum Pick-Up Tool: attached to the mechanical arm that is responsible for holding the sensors • Motion Stage: responsible for movements in the X and Y axis • Air Table: suppress vibrations and other external movements • Rotational Stage: responsible for holding the baseplate and also has its own vacuum system. For the metrology studies, the microscope as shown in Figure 10 has the following features, • Different lighting setups • Measurement Schemes: In particular the XY Planar Measurements 6 • 200 - 200x Magnification • HDR Imaging and Recording Figure 10: New commissioned microscope for the metrology studies The new microscope is beneficial for the PS Module Metrology because the large magni- fication range creates more precise measurements. Also, the edge detection option in the XY Planar Measurement automatically detects the corner of the reference object which increases the efficiency of measuring time.
Details
-
File Typepdf
-
Upload Time-
-
Content LanguagesEnglish
-
Upload UserAnonymous/Not logged-in
-
File Pages25 Page
-
File Size-