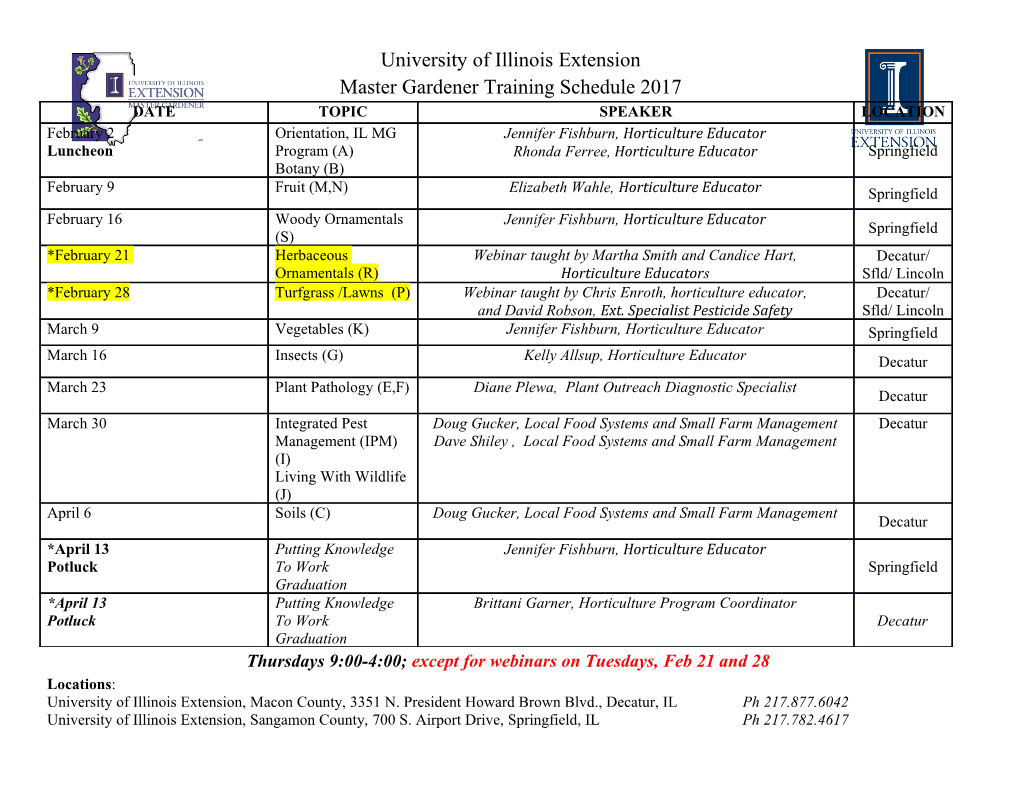
BeyondBitsIssue 8 MOTOR CONTROL EDITION Motor Control Introducing Motor Control Motor control and motor drive solutions With a rich history of innovation in motor control, Freescale is dedicated to continue our commitment to understand and solve the current roadblocks developers face with a comprehensive portfolio of solutions. The latest edition of Beyond Bits captures the attention of both novice and advanced motor control developers looking to: • Reduce development time by jump starting their effort with reference designs, application notes and a global support team • Increase power efficiency by using the most advanced control techniques available through differentiated hardware platforms and peripherals, motor control libraries, and unique tools to optimize these systems • Decrease system costs via a best-in-class portfolio of high-performance, low-power MCUs capable of very flexible, innovative control implementations • Comply with safety and energy mandates via complimentary libraries and advanced algorithms Beyond Bits provides a brief glimpse into the breadth and scope of the Freescale motor control portfolio, much of it unique and built over decades of research and development. We discuss the advantages of different motor types and the methods of control, followed by a portfolio overview and a helpful selection guide. Next, we provide application examples and techniques we’ve implemented using our solutions, and we close with our software and development tools offerings. Solutions such as reference designs, application notes, software, tools and MCU families are listed at the end of each article to help you get started right away on your next design. Freescale continues to partner with innovators to make motors quieter, more efficient, smaller and to reduce mechanical vibration, and hopefully we can help you make them even smarter. To refine your motor skills, visit freescale.com/motorcontrol or contact your local Freescale field applications engineer. Regards, Geoff Lees Vice President and General Manager, Industrial and Multi-Market Microcontroller Business Freescale Semiconductor freescale.com/motorcontrol 1 Introduction 4 Motor Types and Their Control 7 An Introduction to Freescale MCUs 8 Control Wizard in the Freescale Solution Advisor Market Trends 10 BLDC Motor Control 13 Permanent Magnet Synchronous Motor Control 15 AC Induction Motor Control 17 Switched Reluctance Motors 19 Encoder Signal Processing 21 Three-Phase Current Measurement Application Examples 25 Select Freescale Solutions for Your Application 27 Motor Applications for Small Appliances 29 Digital Control of Switched Reluctance Motor Drives 31 Industrial/Appliance Consumer Ceiling Fan 34 Household Washing Machines 36 Dual Motor Control for Air Conditioning with 100 MHz/32-bit DSC 38 Industrial/Appliance PMSM Drive 40 Industrial Drives 43 Digital AC Drive Control 45 Servo Robots for Industrial Applications: PMSM with Encoder 47 Continuous Positive Airway Pressure (CPAP) Machine 49 BLDC Motor Control for Respirators 51 Motor Control Using MQX RTOS Enablement 53 Freescale Motor Control Boards 55 Freescale Embedded Software Libraries 56 Motor Control Development Toolbox 59 Motor Application Tuning Wizard 60 FreeMASTER Summary Table of Contents Table of Contents Introduction Introduction Motor Types and Their Control Summary of key motor types and control Overview Motor types that most effectively sensor wiring, sensor power supply Freescale provides comprehensive meet these requirements include AC and increases reliability. Still, there motor control solutions for almost all induction motors (ACIM), permanent are applications where higher cost of electric motor topologies. magnet synchronous motors (PMSM), sensors is not as important as higher brushless DC motors (BLDC) and position resolution. The most common Motor Control Application switched reluctance motors (SR). speed/position sensors are: Requirements The following pages will cover their • Tachogenerators • Minimize energy losses main characteristics, types of control, • Hall sensors • Prevent environment pollution advantages and typical applications. • Encoders • Decrease acoustic noise and Digital Motor Control power harmonics • Resolvers Digital control allows more efficient • Increase system performance- Applications requiring the motor to motor control with variable speed and versus-cost ratio operate with a required speed (pumps, sensorless control. The term sensorless fans, compressors, etc.) are speed • Increase productivity, flexibility control means that there is no position/ controlled. In variable frequency drives, and robustness velocity sensor on the motor shaft, so motor speed is typically proportional • Increase safety and reliability the rotor position/velocity is calculated to frequency. The actual motor speed • Reduce system size and weight from measured current and voltage. is maintained by a speed controller • Growth of digital control and The sensorless control provides a to reference speed command. reducing usage of analog cost-effective and reliable solution that Speed control offers low dynamic components and total system cost eliminates the position/velocity sensor, performance. For high dynamic and Figure 1: Electric Motor Type Classification Electric Motors AC DC Asynchronous Synchronous Variable Reluctance Induction Sinusoidal Brushless Reluctance SR Stepper Permanent Magnet Surface PM Interior PM Wound Field 4 Beyond Bits Motor Control Edition stability performance, speed control This requires additional connections Permanent Magnet with inner current loop (cascade to the motor, which may not be Synchronous Motor control) is required. The majority of acceptable in some applications. variable speed drives are controlled by Also, the additional cost of the cascade control. Most complex drives position sensors and the wiring (servos, industrial robots, linear motors) may be unacceptable. The physical require additional position control. connection problem could be solved Applications requiring the motor by incorporating the driver in the motor to operate with a specified torque body, however, a significant number regardless of speed (hand tools, electric of applications do require a sensorless power steering, traction, vehicles, etc.) solution due to their low-cost nature. employ torque control. Most BLDC sensorless techniques Brushless DC Motor are based upon extracting position information from the back EMF voltage of the stator windings while the motor is spinning. Those techniques could be Similar to BLDC motors, PMSMs used from 5 percent of nominal speed, have a three-phase stator and a when back EMF is measurable. BLDC rotor with surface/interior-mounted back EMF sensorless techniques permanent magnets. can be used without complex control A PMSM provides rotation at a fixed algorithms, due to back EMF voltage speed in synchronization with the sensing in unexcited motor phase. frequency of the power source. PMSMs Advantages are therefore ideal for high-accuracy • Heat generated in stator is easy fixed-speed drives. Boasting very high- to remove power density, very high efficiency and high response, the motor is suitable for • High torque per frame size BLDC motors have a three-phase most sophisticated applications in the • Reliability due to absence of brushes stator winding and a rotor with industrial segment. It also has a high and commutator surface-mounted permanent magnets. overload capability. A PMSM is largely A BLDC motor does not have a • Highest efficiency maintenance free, which ensures the commutator and is more reliable than • Good high-speed performance most efficient operation. a DC motor. The digital control and • Precise speed monitoring and Synchronous motors operate at power electronics replace the function regulation possible an improved power factor, thereby of the commutator and energize the improving the overall system power proper winding. They are used in home Drawbacks factor and eliminating or reducing utility appliances (such as refrigerators, • Rotor position sensing required for power factor penalties. An improved washing machines and dishwashers), commutation power factor also reduces the system’s pumps, fans and other devices that • Torque ripple voltage drop and the voltage drop at require high reliability and efficiency. • Position sensor or sensorless the motor terminals. In the BLDC motor, the rotor position technique is required for motor Advantages must be known to energize the phase operation • Heat generated in stator is easy pair and control the phase voltage. • Difficult to startup the motor for to remove variable load using sensorless If sensors are used to detect rotor • High torque per frame size position, then sensed information must technique • Reliability due to absence of brushes be transferred to a control unit. and commutator • Highest efficiency • Synchronous operation makes field orientation easy freescale.com/motorcontrol 5 Introduction • Good high-speed performance Advantages tries to minimize the reluctance (air gap • Precise speed monitoring and • Low cost per horsepower distance) of the magnetic circuit. The regulation possible (no permanent magnets) magnetic field creates a force on the rotor so that its poles line up with the • Smooth torque • Inherent AC operation (direct connection to AC line) poles of stator phase. Drawbacks • Very low maintenance (no brushes) • Rotor position sensing required Advantages and rugged construction • Low cost resulting from simple • Position sensor or sensorless •
Details
-
File Typepdf
-
Upload Time-
-
Content LanguagesEnglish
-
Upload UserAnonymous/Not logged-in
-
File Pages64 Page
-
File Size-