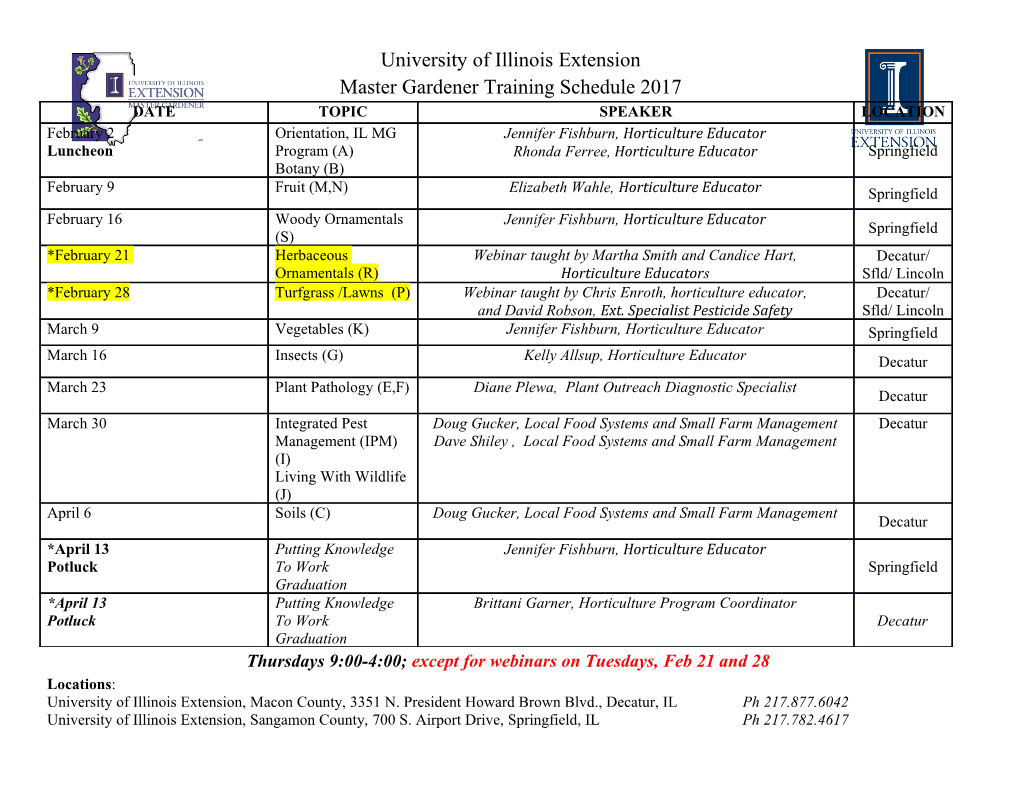
United States Patent (19) 11) Patent Number: 4,873,041 Masui et al. 45 Date of Patent: Oct. 10, 1989 54 PROCESS FOR PRODUCING A 2,847,712 8/1958 Pollard et al. ...................... 264/259 MULTLAYERMOLDED ARTICLE FOREIGN PATENT DOCUMENTS 75) Inventors: Syohei Masui, Kyoto; Masahito Matsumoto, Ibaraki; Nobuhiro Usui, 1137713 6/1986 Japan ................................... 264/259 Takatsuki, all of Japan Primary Examiner-Jan H. Silbaugh 73 Assignee: Assistant Examiner-Kelley M. Sidwell Sumitomo Chemical Company, Attorney, Agent, or Firm-Birch, Stewart, Kolasch & Limited, Osaka, Japan Birch (21) Appl. No.: 238,857 57 ABSTRACT 22 Filed: Aug. 31, 1988 A multilayer molded article having improved appear 30 Foreign Application Priority Data ance and feeling is produced by wetting a skin material Aug. 31, 1987 JP Japan ................................ 62-218457 including a fabric or a thermoplastic resin sheet as an Aug. 31, 1987 JP Japan ................................ 62-218.458 outermost layer with at least one liquid material which 5) Int. Cl.' ..................... B29C 43/04; B29C 43/18; is water, an aqueous solution, a volatile material which B29C 43/20; B32C 27/00 is liquid in an ordinary state, or a solution including the 52 U.S. Cl. .................................... 264/135; 264/130; volatile material as a medium, supplying the wet skin 264/136; 264/257; 264/266 material between male and female molds, supplying a 58 Field of Search ............... 264/135, 136, 257, 266, thermoplastic resin melt between the molds and closing 264/130, 511 the molds to form the multilayer molded article includ ing the integrally adhered skin material and the thermo 56) References Cited plastic resin. U.S. PATENT DOCUMENTS 2,509,499 5/1950 Higgins ............................... 264/134 6 Claims, 1 Drawing Sheet / M N U.S. Patent Oct. 10, 1989 4,873,041 F. G. Ezzzzzzzzazza 2 Y 2 4,873,041 1. 2 When the plastic foam alone is interposed between the PROCESS FOR PRODUCING AMULTILAYER skin material and the thermoplastic resin, the cells of the MOLDED ARTICLE foam are broken by heat and pressure from the resin melt, whereby distinct uneveness is formed on a surface BACKGROUND OF THE INVENTION 5 of the foam which contacts the skin material and the 1. Field of the Invention unevenness is transferred to the surface of the skin mate The present invention relates to a process for produc rial so that not only the appearance, but also the feeling ing a multilayer molded article. More particularly, the of the molded article are impaired. When the packing present invention relates to a process for producing a material which has stiffness and comparatively small multilayer molded article comprising a thermoplastic 10 elongation such as paper or dense plastic foam is inter resin and a skin material having good appearance, posed between the skin material and the thermoplastic which is used as an automobile interior material and a resin, it may be partially broken or warp in the case of part of an electric equipment. a molded article having a complicated shape, whereby 2. Description of the Related Art the appearance of the article is impaired. Hitherto, molded articles on which a skin material is 15 Further, it was proposed to use askin material having laminated to improve their beauty, softness and the like a protective layer made of the same plastic as the ther so as to make their grade higher were widely used. moplastic resin of the article (cf. Japanese Patent Kokai To produce such molded articles having the skin Publication Nos. 71161/1979, 109759/1981 and material, there is a process known which comprises 109760/1981). It was also proposed to use a skin mate molding a thermoplastic resin by one of the conven 20 rial on a back surface of which a foam layer is adhered tional molding methods such as injection molding and or welded and a packing material (cf. Japanese Patent then molding the skin material onto the molded article Kokai Publication No. 212342/1985). by vacuum molding and the like or simultaneously It is possible to maintain the appearance (or feeling) molding the thermoplastic resin and the skin material of the skin material to some extent by these methods, wherein the skin material is adhered to the molded resin 25 but further improvement is desired. with an adhesive to laminate the skin material onto the molded resin. SUMMARY OF THE INVENTION Another known process comprises placing the skin An object of the present invention is to provide a material in a mold, closing the mold and then injecting process for producing a multilayer molded article the hot thermoplastic resin melt through a gate into the 30 mold to laminate the resin onto the skin material, cool which highly maintains the appearance (feeling) and has ing the mold and removing the multilayer molded arti a skin material comprising a fabric or a thermoplastic cle is also known. resin sheet as the outermost layer. A further known process comprises placing the skin According to the present invention, there is provided material between the upper and lower molds, supplying 35 a process for producing a multilayer molded article the thermoplastic resin melt while the molds are un which comprises the steps of wetting a skin material closed, closing the molds to integrate the thermoplastic comprising a fabric or a thermoplastic resin sheet as the resin and the skin layer together. outermost layer with at least one liquid material se However, each of the conventional processes has its lected from the group consisting of water, an aqueous respective drawbacks. 40 solution, a volatile material which is liquid in an ordi Since the first process uses the adhesive to laminate nary state and a solution comprising said volatile mate the molded resin and the skin material, the steps become rial as a medium, supplying the wet skin material be complicated and in turn a production cost of the molded tween male and female molds, supplying a thermoplas article becomes high, and a solvent or a dispersant con tic resin melt between the molds and closing the molds tained in the adhesive will pollute the environment. 45 to form the multilayer molded article comprising the In the second process, since the resin melt which is integrally adhered skin material and the thermoplastic pressurized at a high temperature is injected into the resin. mold, so that the resin melt contacts and presses the skin When the skin material comprises the outermost layer material strongly against the mold wall, the surface of of the fabric, it is preferably wetted with an aqueous the skin material is discolored, a pattern of the skin 50 solution of a surfactant, particularly a cationic surfac material is deformed or the appearance of a fabric with tant. raising is deteriorated, due to flatting or flowing of the raising. Further, in some cases, the resin melt impreg BRIEF DESCRIPTION OF THE DRAWINGS nates or penetrates into the skin material so that the FIGS. 1, 2 and 3 schematically show vertical cross commercial value of the molded article is impaired. 55 sections of the molding apparatus of various stages in The drawbacks of the second process can be over the process of the present invention. come by the third process to some extent so that, ac cording to a type of skin material (a kind, quality, etc.), DETALED DESCRIPTION OF THE a good multilayer molded article can be obtained. How INVENTION ever, the quality of the molded article is still unsatisfac 60 The skin material comprising the fabric as the outer tory. most layer includes a single piece of a woven fabric or To overcome the above described drawbacks or to non woven fabric which may be optionally lined with a prevent deterioration of the softness of a skin material, packing agent, a laminate of such woven or nonwoven it was proposed to interpose a plastic foam between the fabric with a plastic film, a plastic foam, a composite skin material and the thermoplastic resin or to use a 65 sheet of a plastic film and a plastic foam or a cloth. packing material such as paper or a dense plastic foam Examples of fibers which constitute said woven or as a heat insulator or a resin barrier (cf. Japanese Patent nonwoven fabric are natural fibers (e.g., cotton, wool, Kokai Publication Nos. 212343/1985 and 29436/1982). silk and hemp) and synthetic fibers (e.g., polyamide and 4,873,041 3 4. polyester). From a single or mixed yarn of these fibers, In the case of the skin material having the fabric the woven fabrics such as plain weave, moquette and outermost layer, the outermost layer is wetted with the tricot, knitted webs and nonwoven fabrics formed by liquid material an, increase of the temperature of the needle punching can be made by conventional methods. skin material, particularly at the fabric side, is prevented The skin material comprising the fabric as the outer when the thermoplastic resin melt contacts the fabric or most layer loses its appearance or feeling due to heat, the lining so that not only is the flatting or flowing of pressure and elongation, and the fabric may be broken the raising prevented but also the elongation is sup at a corner of the molded article or the resin melt tends pressed so that the breakage at the corner is prevented. to ooze out through the fabric. Therefore, when the Further, the presence of the liquid material prevents skin material and the thermoplastic resin melt are inte 10 penetration of the resin melt in the fabric layer and grated in the mold, it is important to keep the tempera oozing out of the resin melt onto the surface side.
Details
-
File Typepdf
-
Upload Time-
-
Content LanguagesEnglish
-
Upload UserAnonymous/Not logged-in
-
File Pages6 Page
-
File Size-