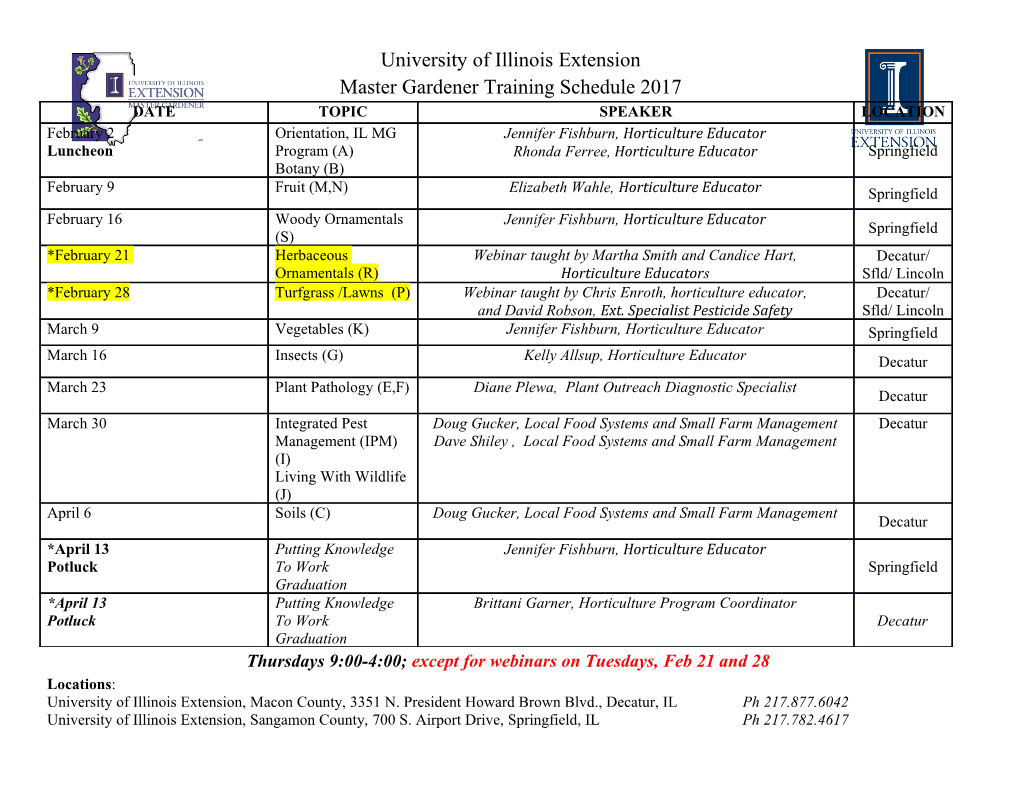
Chapter 2: Basic Manufacturing Processes • Manufacturing processes refer to the processes of producing articles of definite shape, size and properties • In this unit, manufacturing processes involving forging are discussed Mechanical working of metals • Mechanical working of metal refers to plastic deformation of a metal under the action of mechanical pressure to change dimensions, properties and or surface conditions. • Mechanical working processes include a number of processes like Rolling, forging, extrusion, drawing and press working • The stress induced in the part are greater than the yield strength and less than the fracture strength of the material except in sheet metal works like shearing, piercing and blanking Objectives of Mechanical Working of metals 1. To reduce the original block to the finished dimensions. 2. To improve the mechanical properties. 3. Refinement at grain structure. 4. Directional control of "flow lines". 5. Break up and distribution of unavoidable inclusions. Types of Mechanical working 1. Hot working 2. Cold working Hot Working • The working of a metal above their recrystallization temperature at which new grains are formed is called hot working. • The hot working should be carried above the recrystallization temperature but below the melting point. Advantages of hot working • Refinement of grain structure is achieved. • Elimination of porosity and blow holes in steel. • Greater flexibility in chaning shape and size due to reduction in elastic limit. • A uniformity is established due to proper distribution of impurities throughout the mass. • Improved mechanical properties like, ductility, toughness, elongation etc. • The power required to finish the part from ingot is less. • Directional property resulting from a fibre structure is obtained Disadvantages of hot working • Poor surface finish by rapid oxidation or scaling due to high temperature. • Close tolerance cannot be maintained due to poor surface finish. • Reduced tool life due to high temperature. • Tooling and handling costs are high. Hot working processes • Hot rolling • Hot forging • Hot extrusion • Hot piercing • Hot drawing • Hot spinning • Piping and Tube production. Cold working Process • The working of a metal below their recrystallization temperature is known as cold working. • Most of the cold working processes are performed at room temperature. • When material is cold worked the resulting change in material shape causes changes in grain structure. • The effect of cold working on the structure of steel is to distort or elongate the grain in the direction of flow of metal. Advantages of cold working process 1. Improved surface finish. 2. Scale free and bright surface. 3. Closer dimensional tolerances. 4. Increased strength and hardness of metal. 5. Recrystallization temperature for steel is raised Disadvantages of cold working 1. Only small sized components can be cold worked as it requires greater forces. 2. Residual stresses are setup in the metal. 3. Grain structure is distorted. 4. Higher costs 5. Metals having less ductility cannot be cold worked at room temperature. Cold working processes list 1. Cold rolling. 2. Cold forging. 3. Cold drawing, embossing. 4. Cold bending. 5. Cold shearing, trimming, notching, punching, blanking. 6. Cold spinning. 7. Cold bulging. 8. Cold extrusion. 9. Cold squeezing. 10. Cold seaming. 11. Cold rivetting stamping. 12. Cold peening. 13. Cold sizing, coining and hobbing. Rolling Process • Rolling is a metal forming process in which the metal is passed between the rolls to get a desired shape by plastic deformation. • Rolling may be classified into hot rolling and cold rolling depending upon the temperature at which the metal is rolled Hot Rolling Process 1. Hot rolling process is done above the recrystallization temperature. 2. For hot rolling of metals they are first cast into ingots moulds of suitable form. 3. The hot rolling consists of compressing and lengthening the metal as it is fed between two rolls. 4. The flow of metal during rolling is continuous and almost entirely in longitudinal in direction. Cold rolling process 1. Cold rolling process occurs below the recrystallization temperature. 2. For cold rolling the sheets, hot rolled metal is used 3. Before cold rolling the metal is properly cleaned by immersing in an acid solution, washed in water and dried. 4. the metal at room temperature is fed in between two rolls in which the squeezing action of the rolls gives the desired thickness and shape 5. Cold rolling gives smooth and bright surface finish and desired tensile strength, stiffness and hardness is achieved. 6. Cold rolling is generally used for bars, rods, sheets and strips Rolling mill Rolling can be done by using rolling mills. Rolling mills are of the following types : 1. Two high rolling mill. 2. Three high rolling mill. 3. Four high rolling mill. Two High Rolling Mill Non - Reversing Reversing • It consists of two rolls placed top and bottom with constant direction of rotation about the horizontal axis • These rolls are supported by bearings in housing and placed over a rigid stand. The direction of the roller is fixed and cannot be reversed. • For second pass, the stock is returned to the entrance of the rolls by carrying it back • This method of reduction is in only one direction which slows down the process, • An alternative procedure is to use the two high reversing mill in which the direction of rotation of the rolls is reversed after each pass Three high rolling mill • A three high rolling mill consists of three rolls mounted one over the other as shown in figure • This arrangement eliminates the disadvantages of two high rolling mill and-also need of reversing the rolls. • ln this case the top and bottom rollers are drive rolls which revolve in the same direction and middle one rotates by friction in opposite direction. • The workpiece is passed between upper and middle rolls in one direction and then passed in reversed direction between middle and lower rolls. • Lifting stands are provided on one or both the sides of the stand to raise and lower the bar after each pass. • All the three rolls rotate continuously in a same fixed direction and are never be reversed. Four high rolling mill • A four high rolling mill consists of four horizontal rolls, two bigger in size and two smaller in size two smaller in size. • Smaller size rolls initiate the rolling operation and the bigger rolls back up the rolling operation by the two smaller rolls. • This arrangement reduces the tendency of smaller rolls to deflect during rolling • This is used for both hot rolling and cold rolling Drawing principle • Drawing is pulling the metal through a die or a set of dies to achieve reduction in diameter. • The material to be drawn is reduced in diameter for a short distance at one end by swaging to permit it into the die orifice and gripped in jaws • This process requires a very large forces in order to pull the metal through the die. • To reduce the frictional force between the die and the metal, the die is kept well lubricated. Wire drawing • The principle of wire drawing operation consists of extruding a rod through a die thereby causing reduction in cross-sectional area of rod • The wire is drawn by pulling the rod through several dies of decreasing diameter in order to obtain very thin wire. • For wire drawing, the rod obtained from hot rolling process is cleaned and lubricated and then fed into the wire drawing dies held in casing. • The end of the rod is pulled by tongs on the other end to reduce the thickness, depending upon the thickness to be reduced Deep drawing • Deep drawing is defined as a Process of making cup shaped parts from sheet metal blanks. • The blank is first heated to working temperatures to provide sufficient plasticity. • The heated blank is then placed in position over the die • The punch is hammered over the heated blank which pushes the metal through die to form a cup. The process may be repeated through a series of successively smaller dies and punches Extrusion • Extrusion is a process of pushing the heated billet through the metal orifice with high pressure to produce the desired shape • A large force is required in extrusion, so most of the metals are hot extruded. • However, some metals can also be cold extruded • Force may be applied mechanically or hydraulically Uses of extrusion 1. Used for production of rods, tubes etc. 2. Used for production of lead covered cables. 3. Produces uniform cross section of profile 4. Used for cylinder, tubes, shock absorbers Direct or forward extrusion • Ln this method a press operated ram and a cylinder through which the hot workpiece is placed and pushed by the ram. • The metal first plastically fills the cylindrical shape, and it is then forced through the die opening until a small amount remains in the corner • The size of extrusion can be controlled by die adjustment and extrusion point. Indirect or backward extrusion • Indirect extrusion is similar to direct extrusion except that the extruded part is forced through the hollow ram • It involves no friction between the metal billet and container walls, because the billet does not move in the container and less total force is required as compared to direct extrusion • The equipment used is more complicated to accommodate the passage of the extruded shape through the center of the hollow ram Tube extrusion • It is a form of direct extrusion process but uses a mandrel to shape the inside of the tube • The die containing the mandrel is placed in position by the die holder at the extruding point. The hot metal is placed into the container as shown in fig. • The ram is then made to move slowly with a uniform Pressure/ which extrudes the metal through the die and around the mandrel to produce the required tube Forging • Forging is a process by which metals and alloys are plastically deformed to the desired shape by the application of the compressive force • Forging can be done either hot or cold, but mostly hot forging is employed.
Details
-
File Typepdf
-
Upload Time-
-
Content LanguagesEnglish
-
Upload UserAnonymous/Not logged-in
-
File Pages17 Page
-
File Size-