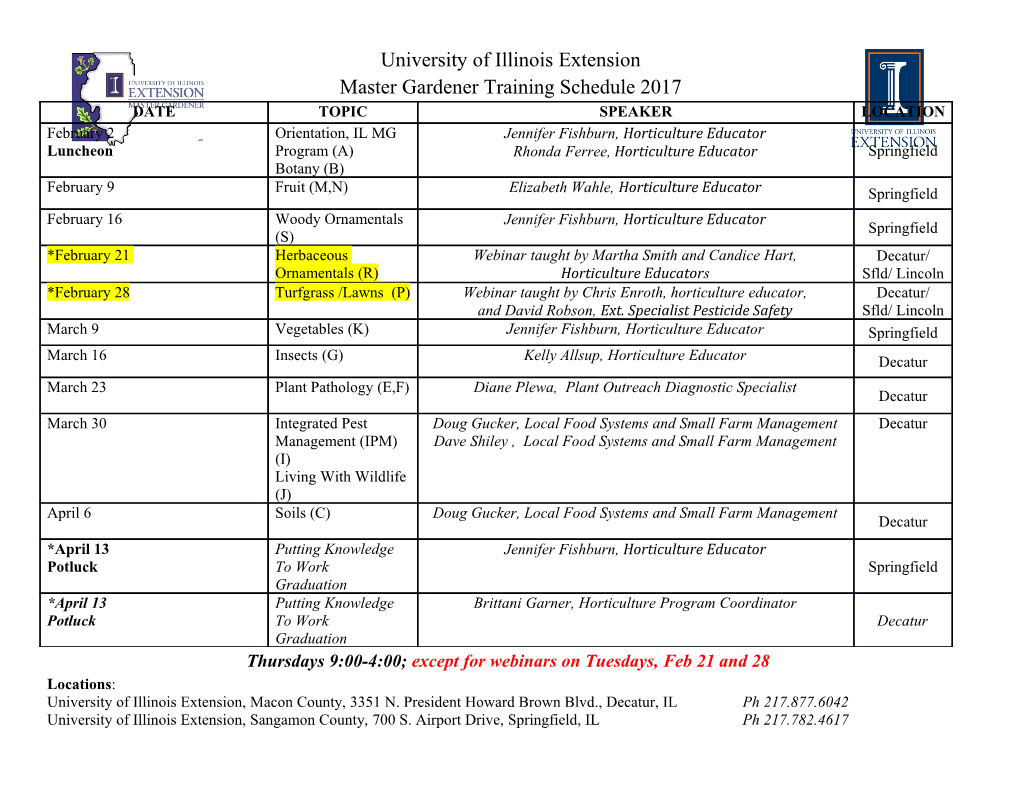
I PEGASUS<iI XL DEVELOPMENT AND L-1011 I PEGASUS CARRIER AIRCRAFT I by Marty Mosier' Ed Rutkowski2 I Orbital Sciences Corporation Space Systems Division I Dulles, VA Abstract Pegasus XL vehicle design, capability, develop­ ment program, and payload interfaces. The L- I The Pegasus air-launched space booster has 1011 carrier aircraft is described, including its established itself as America's standard small selection process, release mechanism vehicle and launch vehicle. Since its first flight on April 5, 1990 payload support capabilities, and certification pro­ Pegasus has delivered 13 payloads to orbit in the gram. Pegasus production facilities are described. I four launches conducted to-date. To improve ca­ pability and operational flexibility, the Pegasus XL development program was initiated in late 1991. Background I The Pegasus XL vehicle has increased propellant, improved avionics, and a number of design en­ The Pegasus air-launched space booster (Fig­ hancements. To increase the Pegasus launch ure 1), which first flew on April 5, 1990, provides a I system's flexibility, a Lockheed L-1 011 aircraft has flexible, and cost effective means for delivering been modified to serve as a carrier aircraft for the satellites into low earth orbit. 1 Four launches vehicle. In addition, the activation of two new have occurred to-date, delivering a total of 13 Pegasus production facilities is underway at payloads to orbit. Launches have been conducted I Vandenberg AFB, California and the NASA Wal­ from both the Eastern (Kennedy Space Center, lops Flight Facility, Wallops, Virginia. The Pe­ Florida) and Western (Vandenberg, California) gasus XL vehicle, L-1011 carrier aircraft, and Ranges. All of the vehicles launched to-date have I Vandenberg production facility will be operational been integrated using OSC's Vehicle Integration in the fall of 1993. This paper describes the Building located at the NASA Dryden Flight Re- I I .••• I I I I I Figure 1. Pegasus XL and L-1011 Carrier Aircraft. I (Copyri~hltD 1993 by Orbital Scienct:'s Corpor.Jtiun. Pllhlislk"d hy the AJ(~rican Institule I uf AeronautiC'S :and Astron:alllics,lIk'. wilh pt:'rrllis~oll.) I search Facility, Edwards AFB, California (NASA Expendable Launch Vehicle Services (SELVS) I DFRF). Three of the launches were conducted off program. The vehicle has also been selected by the coast of California within the control of the commercial customers and by foreign govern­ Western Test Range (WTR). The third mission, ments. I conducted in February 1993 forthe Brazilian SCD- 1 mission, demonstrated the Pegasus launch Baseline Vehicle Description system's exceptional flexibility. For this mission, I the vehicle was integrated at the OSC NASA The baseline Pegasus vehicle (Figure 2) is DFRF VAB and Pegasus was then carried to the 15.2 m (50 ft) long, has a diameter of 1.3 m (50 in), NASA Kennedy Space Center by the NASA B-52 and weighs 19,000 Kg (42,000 Ibs). Major compo­ and launched near the Florida coast. Seven nents include three solid-propellant rocket motors, I launches are scheduled to occur within the next 12 a delta wing, aft skirt assembly supporting three months and future annual launch rates offourto six moveable aerodynamic fins, avionics/payload sup­ missions per year are planned. port structure, a two-piece payload fairing, two I standard payload separation systems (23 and 38 Pegasus is the product of a three year privately inch diameter). an optional restartable Hydrazine ) funded joint venture of Orbital Sciences Corpora­ (N 2H4 Auxiliary Propulsion System (HAPS). and tion (OSC) and Hercules Aerospace Company. A the PegaStar<i' integrated spacecraft bus. 2 I "Turn-KeyW launch service is provided, with OSC and Hercules responsible for all hardware and The vehicle's three Solid Rocket Motors (SRMs) services necessary to deliver the payload(s) to the and payload fairing were developed specifically for I desired orbit. The standard Pegasus launch ser­ Pegasus by HerculesAerospace. The SRMs have vice includes design and production of the vehicle, carbon composite cases and use HTPB class 1.3 mission specific hardware and integration support, propellant. The 6.7 m (22 ft) carbon composite I payload integration, vehicle integration facUities, delta wing provides lift during the early phases of ground support equipment, carrier aircraft, and flight. Three foam core graphite composite fins, launch operations. The first six Pegasus missions which are controlled by electro-mechanical actua­ were funded by DARPA as part of its Advanced tors, provide aerodynamic control through the end I Space Technology Program (ASTP) through the of Stage 1 operation. Pitch and yaw control during Advanced Vehicle Systems Technology Office Stage 2 and Stage 3 burn is provided by electro­ (AVSTO). Support was also received from the mechanical thrust vector control (TVC) actuators. I NASA DFRF and the Air Force Space Division Roll control after Stage 1 separation, and three­ through agreements with DARPA. The vehicle axis control during coast phases and post orbital was selected in 1991 as the U. S. Air Force Small insertion maneuvers. is provided by 55 N (12.5 Ib) Launch Vehicle (SLV) and by NASA for the Small and 110 N (25 Ib) nitrogen cold gas thrusters I I SecondIThird Stage Separation Joint I I Stage 3 First/Second Stage I Motor Separation Joint Stage 1 Motor N2 Tank or Hydrazine Payload Fairing Auxiliary Propulsion Stage 2 Motor System (HAPS) I Figure 2. Pegasus Cutaway Drawing. I 2 I I I located on the avionics subsystem. A graphite subsonic velocity. After release, the vehicle free composite avionics structure supports the payload falls· to clear the carrier aircraft, while executing a and most vehicle avionics. A 1.3 m (50 in) outside pitch-up maneuver to achieve the proper attitude I diameter pyrotechnically separated two-piece for motor ignition. After Stage 1 ignition, the graphite composite payload fairing encloses the vehicle follows a lifting-ascent trajectory to orbit payload, avionics subsystem, and S3 motor. Two (Figure 4). standard marmon clamp type payload separation I systems (23 and 38 inch diameter) are available. Pegasus XL Concem The optional Hydrazine Auxiliary Propulsion Sys­ tem (HAPS) provides up to 73 kg (160 Ib) of N2H4 It was recognized early in the Pegasus pro­ I for orbit raising and/or precision orbital adjust­ gram that additional payload capability would be ment. When combined with the vehicle's on-board needed for some missions. While providing preci­ Global Positioning System (GPS) receiver, HAPS sion orbital insertion capability for all orbits (Figure provides autonomous precision orbit injection ca­ 5), HAPS can provide significant additional pay­ I pability. The PegaStar spacecraft bus can provide load capability only for higher orbits. To identify the extended (5 to 10 year) on-orbit payload and most cost effective means of improving payload sensor support including attitude control (three­ performance for all orbits, a series of trade studies I axis, nadir pointing or spin stabilized), orbital make­ were undertaken beginning in early 1991. The up and adjustment propulsion, data storage, elec­ ground rules for these studies were to improve the trical power, and telemetry support for a wide payload delivery capability to the maximum extent I variety of applications. 1 possible while minimizing the scope of the required modifications (to reduce development time, risk, Pegasus vehicles are currently integrated at and cost), to maintain the vehicle's overall reliabil­ asc's Vehicle Integration Building (VAB) located ity goal (currently calculated at 97%), and to mini­ I at the NASA Dryden Flight Research Facility, mize the impact on payload interfaces and envi­ Edwards AFB, CA (NASA DFRF). This 60 ft. x 80 ronments (so that existing payloads designed for ft. facility (Figure 3) is capable of processing one Pegasus could be flown on either vehicle). I vehicle at a time. Vehicle integration is performed horizontally, using custom motor handling dollies Upon completion of the trade study evalua­ and ground support equipment (GSE). During tions, a conceptual design review for the Pegasus integration all vehicle components and subsystems XL vehicle was conducted in December 1991. I are thoroughly tested using Personal Computer After reviews and discussions with NASA, the US (PC) based electrical GSE and other conventional Air Force, and other customers a final vehicle test equipment. configuration was selected and the design frozen I in February 1992. A formal system Preliminary For launch, Pegasus is carried aloft by a NASA Design Review (PDR) followed in May 92, with a DFRF B-52-008 carrier aircraft, to a nominal level­ final System Critical Design Review (CDR) in April I flight drop condition of 12,200 m (40,000 ft) at high 1993. The product of this effort (Figure 6), the Pegasus XL vehicle, is 16.8 m (55 ft) long and weighs 22.300 Kg (49.000 Ibs). I Propulsion The Solid Rocket Motors (SRMs) for the base­ I line Pegasus vehicle were originally designed us­ ing a very conservative 1.4 factor of safety. Based on the baseline vehicle SRM static fire results and flight data it was determined that margins could be I reduced to a more traditional 1.25 without compro­ mising vehicle reliability. However, simply modify­ ing the design to reduce the design factors of I Figure 3. Pegasus Vehicle Assembly safety (resulting in a decrease in vehicle's inert Building. Dryden Flight Research weight) could not provide the level of performance I Facility. Edwards AFB, CA. improvement desired. It became clear early in the I 3 I I Launch Second Stage Third Stage sec t.o Burnout Ignition h .. 11.582 m (38.oo0 tt) t.166 sec t ... 594 sec M =0.79 \ h = 208,340 m h ... 739 km (399 nmi) I (683,661 tt) Second Stagel v = 4,564 m/s (14.975 Ips) v = 5,469 m/s Third Stage 2 0 d (17.944 Ips) Coast y...
Details
-
File Typepdf
-
Upload Time-
-
Content LanguagesEnglish
-
Upload UserAnonymous/Not logged-in
-
File Pages15 Page
-
File Size-