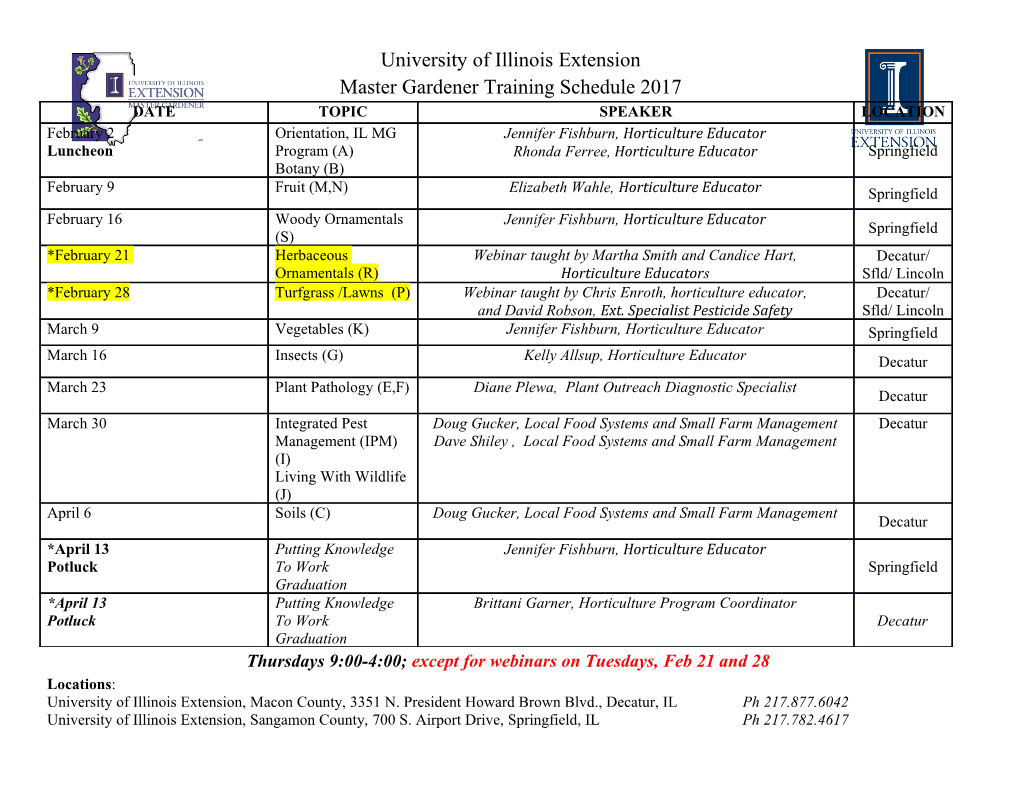
Sådhanå Ó (2021) 46:76 Indian Academy of Sciences https://doi.org/10.1007/s12046-021-01584-6Sadhana(0123456789().,-volV)FT3](0123456789().,-volV) Rocket nozzles: 75 years of research and development SHIVANG KHARE1 and UJJWAL K SAHA2,* 1 Department of Energy and Process Engineering, Norwegian University of Science and Technology, 7491 Trondheim, Norway 2 Department of Mechanical Engineering, Indian Institute of Technology Guwahati, Guwahati 781039, India e-mail: [email protected]; [email protected] MS received 28 August 2020; revised 20 December 2020; accepted 28 January 2021 Abstract. The nozzle forms a large segment of the rocket engine structure, and as a whole, the performance of a rocket largely depends upon its aerodynamic design. The principal parameters in this context are the shape of the nozzle contour and the nozzle area expansion ratio. A careful shaping of the nozzle contour can lead to a high gain in its performance. As a consequence of intensive research, the design and the shape of rocket nozzles have undergone a series of development over the last several decades. The notable among them are conical, bell, plug, expansion-deflection and dual bell nozzles, besides the recently developed multi nozzle grid. However, to the best of authors’ knowledge, no article has reviewed the entire group of nozzles in a systematic and comprehensive manner. This paper aims to review and bring all such development in one single frame. The article mainly focuses on the aerodynamic aspects of all the rocket nozzles developed till date and summarizes the major findings covering their design, development, utilization, benefits and limitations. At the end, the future possibilities of development are also recommended. Keywords. Rocket nozzle; aerodynamics; thrust; expansion ratio; nozzle contour; shock wave; method of characteristics; efficiency. 1. Introduction divided by the area of throat). Lesser design complexity and weight, maximum performance, and ease of manufacture The nozzles were invented with a primary motive to change are some of the main desirable features of a rocket nozzle. the flow characteristics such as velocity and pressure. In The development of novel rocket nozzles [10] for launch 1890, Carl Gustaf Patrik de Laval developed a convergent- vehicles faces a challenging design problem. In order to divergent (CD) nozzle that had the ability to increase a steam meet the performance of nozzle at higher altitudes, the jet to a supersonic state [1, 2]. A typical CD nozzle and the nozzles are designed with high area ratios. However, this variation of velocity, temperature, pressure across the length would generate over-expanded flow conditions when oper- of nozzle is shown in figure 1. This nozzle was termed as a de ated at sea level. A nozzle is said to be an over-expanded Laval nozzle and was later used for rocket propulsion. An one when its exit pressure is less than the ambient pressure. American engineer Robert Goddard was the first to integrate These conditions lead to an unsteady internal flow separa- a de Laval nozzle with a combustion chamber, thereby tion resulting in the generation of side loads which may increasing the rocket efficiency and attaining the supersonic cause damage to the whole launch system. The generation of velocities in the region of Mach 7 [2, 3]. high magnitude side loads inside the nozzles is one of the For space propulsion, the rocket [4, 5] is the main system most important issues under consideration in designing the that stores its own propellant mass and ejects this mass at reusable, robust, and efficient launch vehicles [11–13]. high speed in order to provide thrust. A rocket engine [6–9] generates this thrust by accelerating the exhaust gases to the desired speed and direction. In simple words, the nozzle 1.1 Brief overview utilizes the pressure generated inside the combustion Rocket nozzles comes in a variety of configurations like chamber to enhance the magnitude of thrust by accelerating ideal, conical, bell, plug, expansion-deflection (E-D) and the combustion products to a high supersonic velocity. The dual bell besides the recently developed multi nozzle grid nozzle exit velocity can be controlled by the nozzle (MNG). An ideal nozzle is defined as the one that produces expansion ratio or the area ratio (i.e., the exit area of nozzle an isentropic flow (i.e., without internal shocks) and gives a uniform velocity at the exit. The contour of such a nozzle *For correspondence can be designed with the help of method of characteristics 76 Page 2 of 22 Sådhanå (2021) 46:76 The first conceptual analysis of plug nozzles was conducted in 1950s [21]. Though the performance benefits were claimed in most of the literatures, however, the plug noz- zles did not gain the hardware flight status. In the future, this might change as the rocket engine having a linear plug nozzle is foreseen as the propulsion system for the RLV X-33 concept of the Lockheed Martin Corporation [21, 24, 25]. In the E-D nozzle, the flow from the chamber is directed radially outward and away from the axis of nozzle. The flow is diverted towards the curved contour of the outer diverging nozzle wall [26]. The hot gas flow moving out of the chamber expands around a central plug. The E-D nozzle concept had been the subject of various experimental and analytical investigations. These studies revealed the poor altitude-compensation capabilities of E-D nozzle and were in fact poorer than the plug nozzles Figure 1. Variation of velocity, temperature and pressure across because of over-expansion and aspiration losses. For noz- the length of a De Laval nozzle [2]. zles with high expansion-ratio and comparatively smaller length, an E-D nozzle performs superior than a comparable [14–16] (detailed in section 2). The conical type has his- bell nozzle of equal length. This is due to the lesser torically been the most common contour for rocket nozzles divergence losses as compared to the bell nozzle [24]. In a because of its design simplicity and ease of manufacture dual bell nozzle, two shortened bell type of nozzles are [16, 17]. In a conical nozzle, the exit velocity is essentially joined into one with an inflection point between them. In one-dimensional (1D) corresponding to the area ratio, but 1949, Cowles and Foster were the first to introduce the dual the flow is not in an axial direction across the outlet area bell concept, and it was patented by Rocketdyne in 1960s leading to performance loss due to flow divergence [27–29]. It is still in the conceptual stage but seems to be a [17, 18]. In the late 1930s and early 1940s, German sci- strong candidate for future rocket engines [30]. In recent entists performed extensive nozzle research [16, 19]by times, a newer concept of Multi Nozzle Grid (MNG) came considering all aspects of designing. They opined that there into the limelight where a thin and lightweight plate with was no major benefit in using contours with high com- multiple small nozzles can be used instead of a lengthy and plexities. However, this was applicable only for low area heavy single nozzle. The saving in length is in direct pro- ratio nozzles like V-2 rocket [16, 17]. Because of its high portion to the square root of the number of small nozzles divergence losses, the conical type short nozzles find their (nozzlettes) in MNG (i.e., MNG with hundred nozzlettes is application in small thrusters and solid rocket boosters, ten times smaller than an equivalent single nozzle) [31–33]. where simple fabrication is desired over aerodynamic per- formance [17]. On increasing the cone angle, the thrust loss of a conical nozzle gets enhanced due to flow divergence. 1.2 Present objective This thrust loss can be minimized by contouring the nozzle wall and this type is referred to as the bell nozzle. This is As evident from above, various shapes of rocket nozzles because, by doing this, the flow can be made to turn closer have been evolved over the past 75 years, however, there is to the axial direction [18]. Usually, the calculus of varia- not a single article that gives a comprehensive review of all tions is the simple and direct approach for designing the the types of nozzles developed till date. The present article nozzle contours [14, 18]. Guderley and Hantsch [20] mainly deals with the aerodynamic features of ideal, coni- investigated the problem of finding the nozzle exit area and cal, bell, plug, expansion-deflection, dual bell, and multi its contour to generate the optimum thrust for given values nozzle grid type rocket nozzles. The review summarizes all of ambient pressure and nozzle length. However, the the facts and figures in a systematic way incorporating method was not accepted widely until a simplified tech- several features of rocket nozzles such as design, devel- nique, as detailed later, was proposed by Rao [14]. In opment, utilization, benefits and limitations along with Ariane 5 Vulcan or Space Shuttle Main Engine (SSME), recommendations. the conventional bell-type nozzle was used to expand the propellant products [21]. On the other hand, the plug nozzle is an altitude-compensating type rocket nozzle, where a 2. Ideal nozzle traditional CD nozzle expands the flow to a fixed area ratio regardless of the freestream conditions. The free jet When there is a parallel uniform flow with the exit pressure boundary that acts as a virtual outer wall on a plug nozzle matching with the ambient pressure at the nozzle exit, the expands to match the freestream ambient pressure [22, 23]. nozzle thrust becomes maximum. Such type of nozzle is Sådhanå (2021) 46:76 Page 3 of 22 76 termed as an ideal nozzle.
Details
-
File Typepdf
-
Upload Time-
-
Content LanguagesEnglish
-
Upload UserAnonymous/Not logged-in
-
File Pages22 Page
-
File Size-