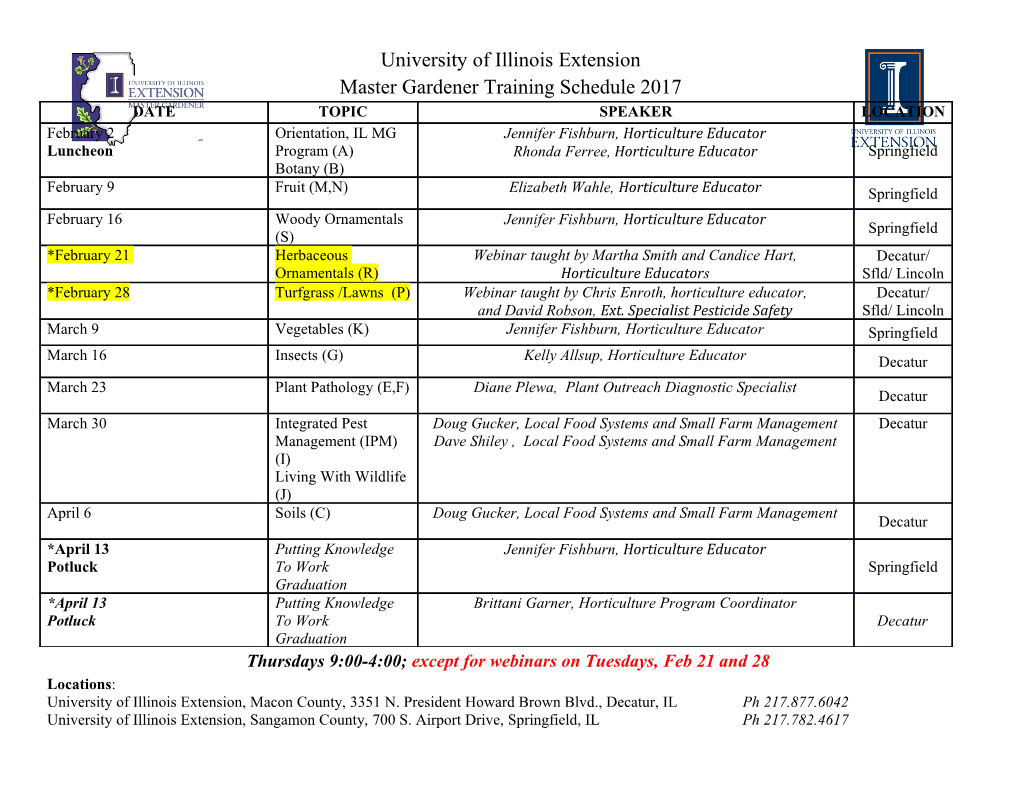
In Proceedings of the 9th ESA Workshop on Advanced Space Technologies for Robotics and Automation 'ASTRA 2006' ESTEC, Noordwijk, The Netherlands, November 28-30, 2006 Electroactive Polymers in Space: Design Considerations and Possible Applications Maarja Kruusmaa(1), Paolo Fiorini(2) (1)Intelligent Materials and Systems Laboratory Tartu University Institute of Technology Nooruse 1, 50411 Tartu, Estonia Email: [email protected] (2)Department of Computer Science, University of Verona Ca' Vignal 2 - Strada Le Grazie 15, 37134 Verona, Italy Email: [email protected] ABSTRACT This paper gives an overview of the technology of Electroactive Polymer (EAP) materials. We focus specifically on ionic conductive polymer materials (IPMC) as a rapidly maturing technology with first commercial applications available, which have also been considered for space applications for almost a decade. We briefly describe their properties and their working principle. Next, we describe IPMC materials working as sensors and actuators and their potential of use in biomimetic devices. In the following we briefly discuss the challenges of IPMC sensor and actuator control. Finally, we envision some possible applications of these materials to space systems. INTRODUCTION The robotic applications developed and exploited so far use almost exclusively electromechanical actuators. The technology of electromechanical devices is very well established, and has thorough theoretical background, control methods and reliable applications demonstrated during several decades. This technology has obviously reached its maturity and therefore its limits have also become visible. Devices using this technology need rigid links to connect the rotating joints, gears and bearings and they are therefore unavoidably complex, rigid and noisy. At the current state of development it is hard to reduce the size and energy consumption of these devices. This paper gives an insight to another, alternative method, of actuating robotic devices, by means of shape-changing materials. Electroactive polymers (EAP) change their shape and size in response to an electric stimulus (see [1] for an overview). Compared to electromechanical devices, EAPs have many complimentary advantages. They are lightweight, soft and flexible, easy to miniaturize, and permit distributed actuation and sensing. The behaviour of the EAP materials in the electric field somewhat resembles the performance of biological muscles, therefore EAP materials are considered to be good candidates for building biomimetic devices [2]. However, compared to the technology of electromechanical devices, EAPs have many drawbacks typical to developing technologies such as low output force or small strain (depending on the material used), high energy consumption and lack of well-established control methods. In the following, we give a short overview of EAP materials, their properties and the estimate of the maturity of their technology and then concentrate on ionic conductive electroactive polymers (IPMC) as a relatively mature technology in the EAP domain, which has been considered for space applications for more than a decade. The technology of EAPs is often proposed as a promising alternative to overcome the drawbacks of bulky, noisy, rigid electromechanical devices. The idea we envision in this paper is, instead of opposing these two alternatives, to combine their complementary advantages into a new device. As an example, we propose a bio-inspired design concept of a flexible, compliant manipulator with distributed actuation and sensing. The manipulator has a DC-motor driven semi-rigid plastic backbone surrounded by the layer of IPMC artificial muscle bundles. The DC-motor driven backbone permits precise positioning of the manipulator, holds the manipulator in the steady position and guarantees a sufficient amount of output force and torque. At the same time the IPMC materials in a form of artificial “skin” and “muscles” provide softness and flexibility and distributed sensing and actuation. We surmise that in contact with an object this kind of manipulator is capable of sensing the object, and the distributed actuation would permit fine manipulation and grasping. ELECTROACTIVE POLYMER MATERIALS There are many types of electroactive polymers with various properties and with various types of reaction to electrical stimuli. By and large, EAP materials can be divided into few major groups. Electronic polymers are driven by electric field or Coulomb forces. Materials like dielectric EAPs, electrostictive elastomers and ferroelectric polymers belong into this group [3]. They shrink and expand when electric stimulation is applied. Electronic polymers can operate at room conditions, have a low response time, can hold strain under activation and they are relatively strong. These polymers require high voltage (several kV) at very low current for operation. Electronic polymers have been used in robotic applications such as a biologically inspired hexapod robot [4] and a micro-robot mimicking annelid animals [5]. The electroactive properties of ionic polymers are caused by mobility or diffusion of ions. EAP materials of this group include carbon nanotubes, conductive polymers, ionic polymer gels and ionic polymer metal composites (IPMC). Ionic polymers bend when electric stimulation is applied. Opposite to electronic polymers they produce large displacement when stimulated and operate at low voltages. At the same time their response is relatively slow, they produce small actuation force and usually need a wet environment for operation. Because of the dynamic processes inside the materials they can not keep the strain but relax after a while to the initial configuration. Therefore the applications of ion conducting polymers are usually inspired by aquatic animals. For example, they mimic motion of the caudal fin [6], pectoral fins [7], a mollusk [8] or a tadpole [9]. Conductive polymers are able to displace large loads (around an order or magnitude larger than ionic polymers) with moderate displacements (around 2%) [10]. They can hold the strain without consuming energy. Like other types of EAPs, conductive polymers are considered to be possible implementations the areas of bionic devices, robotics and tactile interfaces [11]. The problems to overcome are mainly focused around increasing their displacement and long term stability. This paper focuses on potential applications and challenges of ionic conducting polymer metal composites (IPMC), a configuration of ionic conducting polymer materials. These materials have been investigated and developed for space applications for almost a decade by NASA JPL and applications such as a dust wiper for a planetary rover have been proposed [12]. IONIC CONDUCTIVE POLYMER METAL COMPOSITES Fig. 1 shows a stripe of IPMC material clamped between the contacts with the lower part moving freely. The photo in the middle shows the IPMC sheet in its initial configuration, with no electric stimulus applied [13]. When the electric field is applied between the contacts, then it causes bending of the material to the left or right, depending on the polarity of the electric field. These materials cannot hold the strain but after a while (usually few seconds) relax back to the initial configuration. As an example of material performance, an IPMC developed using the latest techniques exhibits a huge bending deformation (up to 180º) when activated by a low voltage signal (ca. 2 V). Current consumption depends on the required force output (typically 100-200 mA). The material is flexible and bends without fatigue up to 107 cycles when adequate measures have been taken to control the solvent inside the membrane, e.g., by coating. Forces can be generated to allow lifting of 10 times their own weight [14]. A sheet of IPMC material requires some care in manufacturing since it will require the integration of stripes of EAP and conductive materials, to ensure proper activation and control. Fig. 1. An IMPC sheet in a bent configuration with the opposite driving voltage polarity (A and C) and an initial configuration with no electric stimulus applied (B). Ionic polymer materials are made of a highly porous ion fluorinated polymer, like Nafion®, Flemion®, Teflon® and their modifications, filled with ionic conductive liquid. During material fabrication the proton connected to the terminal group (the chemical unit in the end of a polymer chain), is replaced with a metal ionic cat-ion (Na+, Li+). These cat-ions will dissociate in water, so that terminal groups will have a negative charge and at the same time there will be an excess of free cat-ions in the material (see Fig. 2, to the left). A sheet from this kind of material is then covered with a metal coating, usually platinum or gold. The metal covered polymer is called ion-polymer metal composite (IPMC). Since water molecules are dipoles, they orient themselves in electromagnetic field and get attached to the free metal cat-ions. An applied electric field causes an electric current and the cat-ions start to move to one side of the material causing expansion of the material on that side and contraction on the other side (Fig.2, in the middle). The bent conformation is an imbalanced situation. Water starts to diffuse in the opposite direction and the polymer sheet relaxes after some time (Fig. 2, to the right). These materials do not keep their position under direct current. At the same time, their action length is remarkable and they operate at low voltage (1.2 – 7V). At the
Details
-
File Typepdf
-
Upload Time-
-
Content LanguagesEnglish
-
Upload UserAnonymous/Not logged-in
-
File Pages7 Page
-
File Size-