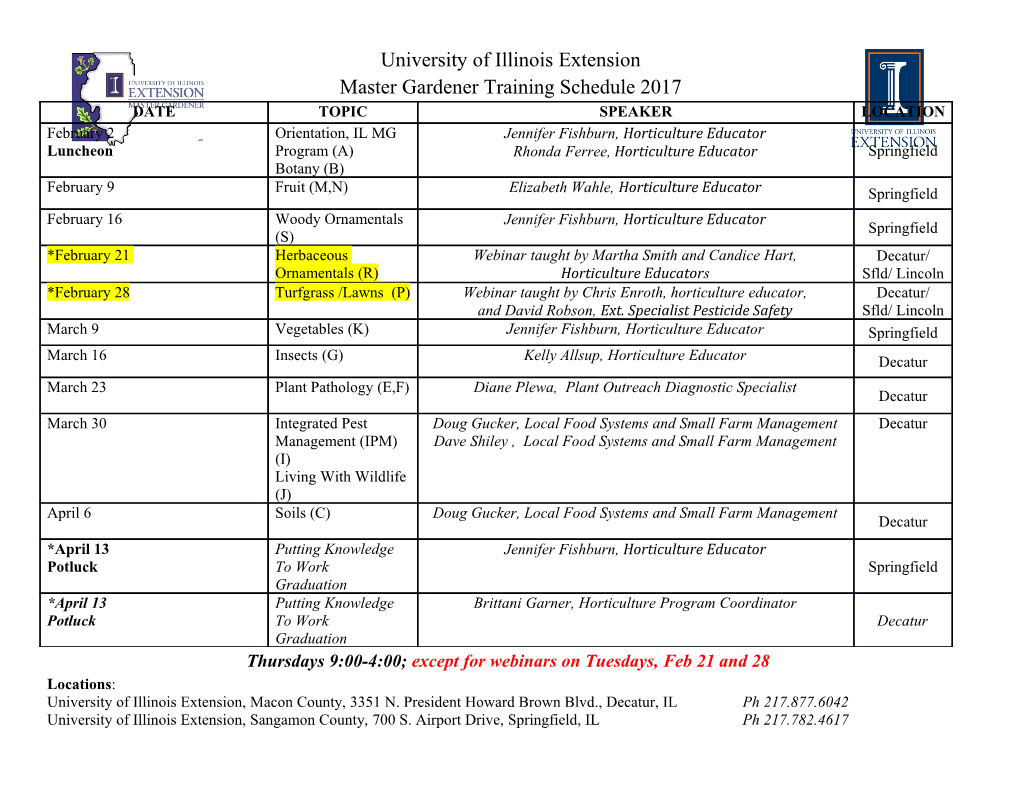
Quintino---11/01 10/12/01 3:32 PM Page 261 Laser Beam Welding of Automobile Hinges A laser welding procedure for joining hinges to the reinforcement structure of car doors is evaluated BY L. QUINTINO, P. VILAÇA, R. RODRIGUES, AND L. BORDALO ABSTRACT. Since the establishment of a welding process was initiated. The ex- second set was performed on the actual C O2 laser beam as a heat source for perimental work was carried out on a lap door reinforcement structure. The results welding, its application has moved into joint with dissimilar thicknesses and were compiled and analyzed from the se- new areas, replacing existing joining types of parts. The hinge, was made of lection of the best welded reinforcement processes. This paper presents an auto- cast steel, with a thickness increasing lin- structures for structural integrity testing. motive application of laser beam welding early from 4.9 to 6.4 mm (0.193 to 0.252 This testing evaluated not only local joint for joining hinges to the reinforc e m e n t in.). The reinforcement structure wa s strength but also ove rall hinge perfor- structure of car doors. The objectives of made of rolled steel, 2 mm (0.079 in.) mance. The tests included shear, peeling, the investigation were to increase pro- thick, as seen in Fig. 1. bending, and fatigue tests that simulated d u c t iv i t y, improve repeatability, and One of the major difficulties in weld- normal wear and tear on doors over a maintain overall joint quality, while sat- ing these parts was lap joint accessibility. long period of service. isfying the needs for a perfect surface ap- The weld could only be performed from p e a rance and the structural reliability the top surface of the joint on the thicke r Laser Industrial Applications achieved with the gas metal arc welding hinge material. This constraint existed be- (GMAW). Experiments were carried out cause when the hinge was joined to the re- Demands for improved production in two distinct phases. The first dealt with i n f o rcement structure, the door was al- q u a l i t y, productiv i t y, and flexibility are technological feasibility and the second re a d y assembled, and thus access from the constantly enlarging the field of laser examined the influence of the main laser inside was prevented, as seen in Fig. 2. welding applications (Refs. 1–4). Th i s welding parameters on the quality of the To obtain adequate penetration and process is being used for an extensive va- joint. At the end of each phase, nonde- stability of the laser welding keyhole, it is riety of applications in the automotive , structive X-ray and metallographic analy- easier to perform the weld from the sur- s e m i c o n d u c t o r, and electronic indus- ses were applied, allowing the selection face of the thinner part. Normally, where tries. More recently, it has been used in of the best overall laser welding condi- possible, joints are designed that way. s u ch diverse fields as medical instru- tions. These conditions were then imple- Two other challenges were pre- ments manufacturing, where heart pace- mented to evaluate the structural in- sented. Lap joint welding was not easy makers and dental instruments are laser tegrity of the joints by means of typical due to the inherent root opening be- welded, and nuclear and naval equip- automotive industry tests. tween the parts. Also, the ove rall thick- ment, where containers and sheet metal ness from 6.9 to 8.4 mm (0.272 to 0.331 are also laser welded (Ref. 5). Introduction in.) was greater than typical automotive Laser beam welding applications in b o dy welding applications. the automotive industry include welding In a particular automotive plant, The first set of experiments was per- the roof to the side-panels by a car man- hinges were joined to the reinforcement formed on plain steel sheets, while the ufacturer in Ghent, Belgium (Ref. 6). Ad- structure of car doors by GMAW. How- vantages over spot welding were the for- ever, the process did not deliver particu- mation of a continuous watertight weld, larly good results. Poor weld appearance no post treatment required, and less dis- was the result of a great amount of spat- placed material resulting in better body t e r. Often the process resulted in non- a c c u ra cy. In addition, the problem of conformities in quality tests and breaks in KEY WORDS welding the zinc-coated material wa s production. over come by carefully selecting weld pa- In order to increase productivity, re- Laser Beam Welding rameters. Other car manufacturers (Ref. 7) p e a t a b i l i t y, and ove rall joint quality, Automotive Application use a laser system to assemble gear tran s - while maintaining the structural reliabil- Lap Joint mission shafts, and a particular company ity, an evaluation of the CO laser beam Dissimilar Materials (Ref. 8) laser welds automobile roofs 2 Shielding Gases using 5-axis CO2 5-kW laser equipment. Porosity Companies that produce automotive L. QUINTINO, P. VILAÇA, R. RODRIGUES, components have also been attracted to and L. BORDALO are with Instituto Superior laser beam welding for its ability to weld Técnico (STM), Portugal. WELDING RESEARCH SUPPLEMENT | 261-s Quintino---11/01 10/12/01 3:32 PM Page 262 Table 1 — Mechanical Characteristics and Norm Specifications of the Parts Parts Material Specification Yield Tensile Strength Strength (N/mm2) (N/mm2) Door Reinforcement Fe P03A DIN EN 10130:1995 <210 270–350 Hinge St 52-3 DIN EN 10025:1990 <355 490–630 Fig. 1 — Geometry of the lap joint between the hinge (cast steel) and the sheet metal (rolled steel) of the door reinforcement pillar. Fig. 3 — The machined hinge geometry intended to overcome the difficulties posed by the original thickness differences of the parts. Fig. 2— Schematic of the hinge assembly in the reinforcement pillar of the door structure. premachined precision components with The method of production of each part increase of output power over that wh i ch restricted heat input and minimal distor- influenced the joint fitup. While the would be obtained with single-mode op- tion. The advantages are single-sided ac- hinge was cast, the steel sheet was rolled e ration, but with a partial loss of beam cess, reduced flange widths and mass, and then stamped to produce the door re- c o h e r e n c e . smaller heat-affected zones, less ther- inforcement. The hinge casting produced The copper nozzle, used for plume mal distortion, increased structura l a rough finish, with a roughness value, Rz suppression conducting the flux of strength, high-speed automated process- (average peak-to-valley height) of about shielding gas, had an outer diameter of ing, and good design flexibility. Gener- 44 µm, resulting in a gap value between 40 mm (1.57 in.), posing a difficult ac- ally, a number of CO2 laser welding ap- the overlapped parts varying from 0 to cessibility challenge due to the geomet- plications are now in production for the about 51 µm. Thus, in order to analyze rical configuration of the hinge and rein- welding of components such as radiator the gap influence in some hinges, surface f o rcement door structure. As for the supports, door window frames, rear shelf preparation was done by grinding it with handling system, the beam focusing and panels, and side panels (Ref. 8). 1200-grade silicon carbide. The resulting propagation optics were mounted on a roughness Rz of about 14 µm is equiva- Z - t ravel axis and the parts to be welded Experimental Procedure lent to a fine surface finish of machining were positioned on an X-Y gantry mo- processes. tion system. Welding trials were first performed on The mechanical ch a racteristics and As illustrated in Table 3, the first set of steel sheets and hinges using original chemical composition of the materials to experiments was made, with hinges and hinge geometry (as distinguished from a be welded are shown in Tables 1 and 2, plain sheets, using either helium or argon machined hinge geometry used later), to respectively. shielding. Using an existing gantry at the investigate different interface preparation Welds were executed using CO2 l a s e r work site, a clamping device wa s conditions. This was followed by trials equipment capable of generating an out- adapted to prevent misalignments and to performed on the actual door reinforce- put power of 6000 W. In practical terms, eliminate the gap between the two pieces ment using the best established interface this produced a beam net power of ap- as much as possible. condition and two different hinge proximately 4550 W, with a beam deliv- The first step was to prove the feasibil- geometries. The selection of the welding ery efficiency h = 76%, a focal length of ity of laser beam welding to join the parts parameters was based on visual, nonde- 150 mm (5.905 in.), and a focal diame- present in this specific application. As s t r u c t ive (ra d i o g raphic), and metallo- ter of 0.4 mm (0.016 in.). The laser stated before, one of the main problems g raphic analyses. The most promising s o u rce was operated with continuous was related to the surface finish of the cast conditions were selected for a final test wavelength and with multimode TEM, hinge, wh i ch considerably augmented phase aimed at assessing the structura l wh i ch produced an output that com- the joint root opening at the interface.
Details
-
File Typepdf
-
Upload Time-
-
Content LanguagesEnglish
-
Upload UserAnonymous/Not logged-in
-
File Pages7 Page
-
File Size-