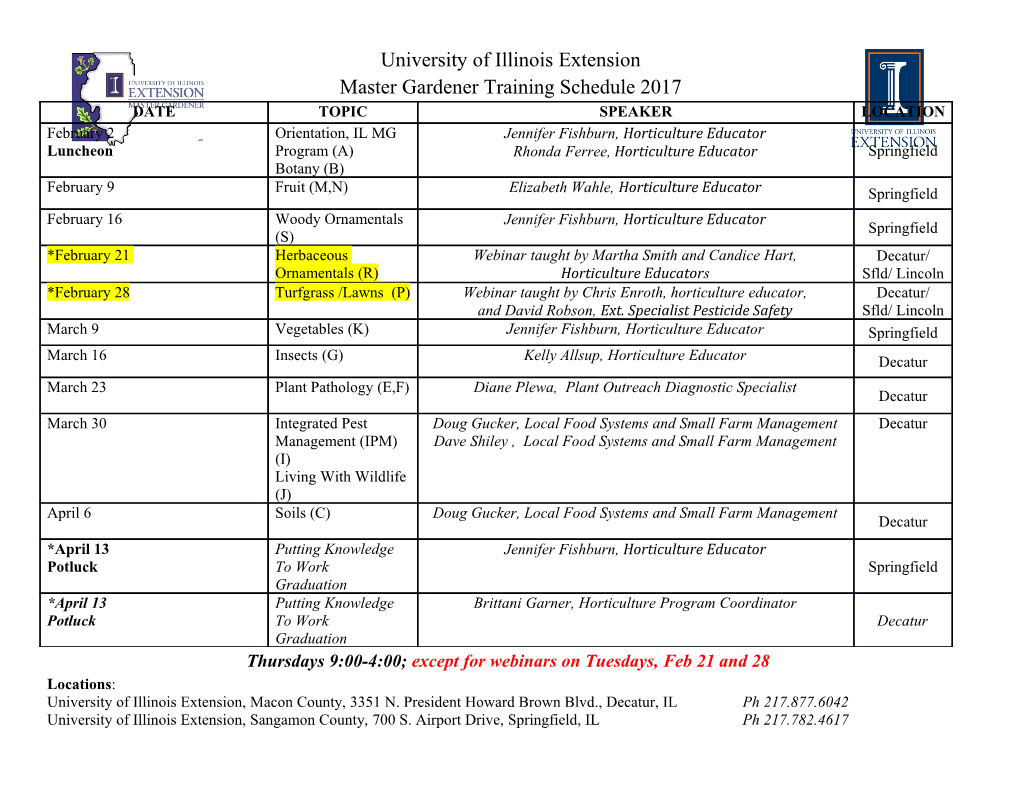
Ti-2007 Science and Technology, edited by M. Ninomi, S. Akiyama, M. Ikeda, M. Hagiwara, K. Maruyama The Japan Institute of Metals (2007) Progress on Titanium Spring Baoliang Bai, Jianchao Yang, Quan Hong Northwest Institute for Nonferrous Metal Research, Xi'an 710016, China For years the automotive industry has shown interest in titanium alloys for many automotive components. One of the limiting factors in titanium's acceptance over the years has been its relatively high price compared to standard materials. However, as the design engineers strive for lighter weight vehicles with improved performance and the materials manufacturers developed ways to reduce the cost and streamline processing, titanium has become more attractive. Titanium alloys offer weight savings, strength, corrosion resistance and modulus advantages over steels used for automotive applications. This paper addresses the current and potential uses for titanium alloys in spring application. Selected comparisons with conventional alloys are presented. Typical weight and performance advantages as well as a discussion relative to cost will also be made. Attention should be concentrated on the following three areas in the near future: (1) development of lower cost alloys; (2) exploration of low cost manufacturing methods; (3) evaluation of treatments to enhance wear resistance if necessary. Keywords: titanium(Ti), spring, progress, low cost 1. Introduction engineers can reduce the free height of the spring to 50-80% Uniquely among engineering alloys, titanium and titanium that of a comparable steel spring. This can translate into greater alloys possess the strength, density and modulus to make the styling and structural design freedom as well as improved ‘ideal’ spring for almost every application1~3). The key to passenger compartment and payload space design flexibility. successful spring design is to optimize the saving of weight and Several design concepts for cars, across the range of future space. Modulus of Ti is only about 36.9GPa, and which of steel models, have space constraints that cannot be met using steel is about 79.3GPa, so Ti is approximately twice as "springy" as springs. steel. Since the density of titanium is about half that of steel, These properties combine to allow a spring designer to utilize a titanium springs are smaller and typically 60-70% lighter than larger wire diameter and many fewer coils to provide a spring steel equivalents, and the lower weight improves suspension rate that is equivalent to the steel spring being replaced. The dynamics and response. At the same time titanium has 75% of resulting titanium spring is both significantly lighter and will the strength of steel, tensile strength of Renton Spring Grade provide 1.2 in more travel due to having fewer coils (the travel Titanium is around 1270MPa, and which of Chrome Silicon of Ti spring is 6.4 in., and that of steel spring is only 5.2 in.). Spring is 1720MPa or so4). This gives the titanium springs the characteristic "open spaced Spring weight for a given load and spring rate is proportional to coil" look. The corrosion resistance of titanium alloys is an the product of the shear modulus and density of the alloy added benefit to service life for springs on equipment, even if it divided by the square of the allowable stress. Weight is is only occasionally operated in aggressive conditions5). minimized when titanium is used because of its low shear Since the Ti alloys are very proper to manufacture springs, modulus and density combined with high allowable stress. At more and more attention has been paid on these kind of alloys the same time, spring deflection is inversely proportional to [1~3]. In this paper, progress on Ti springs are reviewed, shear modulus and is therefore high for titanium, so fewer including Ti spring materials, application of Ti springs, and the active coils are needed, permitting a reduction of free height way to lower the cost are also presented. (by 50-80% of a comparable steel spring), with further weight reduction and a 44% higher natural frequency, from 2. Titanium Spring Materials 127Hz to 88Hz, as shown in Table 1. A wide range of titanium alloys are suitable for making springs Table l. Comparison between Titanium and steel spring4) for virtually any weight- or space-sensitive application. Good performance has been achieved with Ti-6Al-4V and other alpha-beta alloys, but much better results are obtained from the higher strength beta alloys, which are more easily drawn into wire and cold fabricated to springs. Beta-C (Ti-3Al-8V-6Cr- 4Mo-4Zr), which has been used in the aerospace industry over ten years in spring applications6,7). The expense of producing Beta-C has precluded its use in automotive applications. By altering the alloy formulation through the use of a much less expensive Fe-Mo master alloy, Timetal LCB (Low Cost Beta, Ti-6.8Mo-4.5Fe-1.5Al) was developed primarily for automotive springs and can be formulated at as little as half the cost of typical existing beta alloys, e. g. Beta-C8,9). Ti-B20 was one kind of beta Ti alloys developed in The low modulus and low mass of titanium springs enable them to be designed for smaller spaces so that 1411 Northwest Institute for Nonferrous Metal Research (NIN), available from Timetal LCB alloy in comparison with other China. The ultimate strength for the alloy treated at 780°C is titanium alloys at ambient temperature. From the table, it can 919 ~1003 MPa, the yield strength equals to 875 ~ 990 MPa, be seen that Timetal LCB and Ti-B20 alloy possess favorite and the elongation varies from 16% to 18%, the area of comprehensive properties, which are quite suit for reduction varies from 48% to 53%. The properties after aging is manufacturing high performance springs. shown in Table 2, Table 2 also shows the properties. Table 2. Mechanical properties of several Ti alloys at ambient temperature (STA) Springs made with Timet LCB do not require as many turns as Table 3. Properties of Timetal springs vs. steel equivalents4) a steel spring because of its low shear modulus, and low density12), as shown in Figure 1. The strength, density, shear modulus and relative weight of this alloy are compared with those of steel of similar tensile strength in Table 3. This table represents the optimum comparison for steel, because it is not uncommon to apply an allowance for corrosion to the diameter of the steel spring, making it even heavier and more bulky. No such allowance is required for titanium, nor is there normally Timetal LCB spring wire can be supplied hot rolled, or hot any need to apply paints or other protective coatings or rolled and cold drawn, (normally up to 20% cold reduction), or anticorrosion treatments. Beta alloys as a class offer designers hot rolled and solution treated9). LCB can be either cold wound many options to select a final combination of properties for or hot wound at 700-760°C. If hot wound, springs would be fan specific applications. Characterization of springs made from air cooled and aged. Cold wound springs may pass directly for Timetal LCB is in hand to establish the safe upper limit for aging typically at 510-540°C for up to two hours. Finishing of allowable stress. This will be closer to the tensile strength than springs manufactured by either method would be blasting and for other spring alloys, an essential requirement for the springs pickling followed by shot peening, typically to 16-18A of lowest weight and least cost. From the table, it can be also intensity7). seen that the density of titanium is about half that of steel, Fatigue13) is a likely failure mechanism for all types of springs titanium can perform the same task as steel springs in most (compression, extension, torsion, leaf, presswork, spiral, applications while weighing 60-70% less. Even if the two constant force, disc, etc.) as well as for all spring sizes(fatigue materials have the same density, the titanium spring would be occurs in springs made from materials 0.1 mm thick to 80 mm lighter because it does not use as much material. diameter). In standard salt-spray exposure fatigue tests, the typical fatigue strength of a steel spring, coated or uncoated, is reduced by up to 50% over that of the same spring tested in air. In the same tests, the life of the titanium springs in salt spray was reduced by less than 4% over the tests done in air5). Unlike steel springs, titanium springs do not require protective coatings. Corrosion fatigue is the probable cause of the majority of steel suspension spring failures in car, motor vehicles. Springs are invariably manufactured from high-strength materials, the most important of which are carbon steels, low- alloy steel, stainless steels, and nickel, cobalt, copper, and Figure 1. Comparison of mass difference of Timetal LCB springs with a titanium alloys, and all are susceptible to fatigue failure. Table conventional steel spring of the Volkswagen Lupo FSI 4 shows the fatigue endurance limit for several Ti alloys. From the table, it can be seen that Timetal LCB alloy possesses favorite fatigue strength both for smooth specimen and notched ones. 1412 Table 4. Fatigue endurance limit for several Ti alloys, MPa 3. Application Springs made by the Timetal LCB are typically 30 percent Titanium has found many application for springs. The use of lighter than the steel springs on the comparable 2005 model TIMET Exhaust Grade titanium for the exhaust system of the and weigh 1.1 lb (500 g) less than their steel counterparts. 2001 Corvette Z6 was the first significant appearance of Ultimate Performance Grade (UPGTM) Beta titanium material titanium on a volume production car (covered in AEI in made by Dynamet Incorporated has been used in the drive October 2000).
Details
-
File Typepdf
-
Upload Time-
-
Content LanguagesEnglish
-
Upload UserAnonymous/Not logged-in
-
File Pages4 Page
-
File Size-