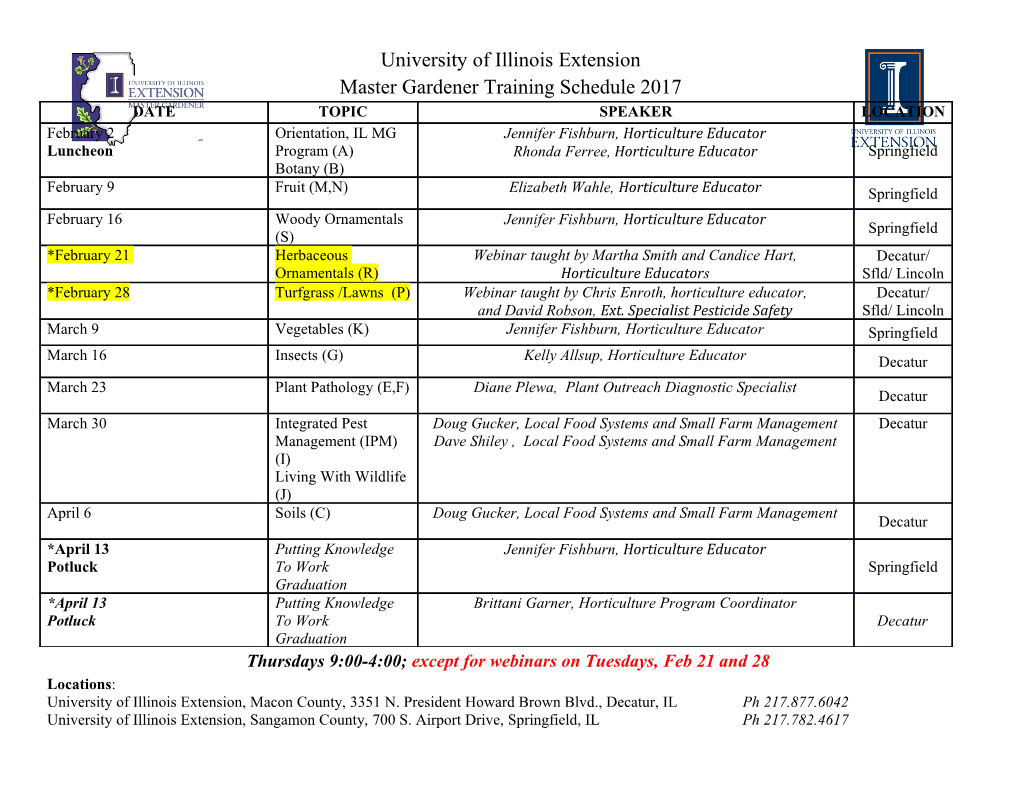
THE VAPOR PRESSURES OF MOLYBDENUM OXIDES AND TUNGSTEN OXIDES DISSERTATION Presented in Partial Fulfillment of the Requirements for the Degree Doctor of Philosophy in the Graduate School of The Ohio State University By PAUL EDWARD BLACKBURN, B. A. The Ohio State University 1954 Approved by* 1 ASMQMtfMlgMI The writer wishes to express his appreciation for the helpful guidance and criticism of Professor Herrick L. Johnston, under whose supervision this work was oarried out. He is also most appreciative to Dr, Michael Hoch for their many useful discussions and for his sugges­ tions . The author is very grateful to Mr. Janes Jones and Mr, L. £. Cox of the laboratory shop for their fine work on the apparatus used in this study. THE VAPOh PRESSURES OF MOLYBDENUM OXIDES AND TUNGSTEN OXIDES IflTBQPgCTIQM Although earlier investigations on the vapor pressures of molybdenum trioxide and tungsten tri- oxide have been reported in the literature (1,2) there is some doubt about the accuracy of the data. For this reason, and in order to extend the work to the other oxides, a study of the solid-vapor equili­ brium of the molybdenum-oxygen and tungsten-oxygen systems vas undertaken. The study was carried out by measuring the vapor pressures of the oxides using the Knudsen rate of effusion method. THEORY Sato of fiffmlga Hitfaad The Xnudaen (3) rate of effusion method consists of measuring the rate at which gas molecules escape through an orifice in the wall of a cell in which the gas la in equilibrium with a solid sr liquid. The equation for the pressure of a gas determined by the rate of effusion method is (4 ) p - » ^ * 5 “ , a ) where m is the rate of effusion in grams per square centimeter per second, R is the gas constant, T is the absolute temperature and M is the moleoular weight. In order for this equation to hold true, two conditions must be met. The pressures measured must be low enough that the mean free path exceeds the di­ mensions of the orifice (5), and the area of the orifice must be small compared to the area of the solid to maintain conditions close to equilibrium. This equa­ tion also assumes a hole of Infinitely small wall thickness so that molecules passing through the surface pierced by the orifice will not enoounter the walls of the orifice (6). for this reason many investigators use knife edged holes. If a knife edged orifice is not used, the amount gas passing through the orlflee Is diminished by a factor K 1 “ 1 ♦ 0.5 1/a ^ in which 1. la equal to the depth of the hole and a la the radius of the hole (7). Thermodynamics According to the Clasius-Clapeyron equation the logarithm of the pressure of a gas in equilibrium with a solid or liquid is related to the heat of vapori­ sation (AH) by the following equation, lnp - ♦ C (3) where T is the absolute temperature and C is a constant* The value obtained for AH in this equation is the average heat of vaporisation for the temperature range covered by vapor pressure measurements* It is usually not possible to extrapolate the ex­ perimental curve without error. However if heat capacity data are available, or if values may be reasonably estimated, the vapor pressure curve may be extended over the range for which the heat capacity data apply (8,9). If the difference la heat capacities of the gas and the solid or liquid is expressed in an equation -4- auoh as ACp - Aa ♦ AbT - ACT”2 U ) than the standard ohangs in free energy (&F°) nay be expressed as follows, . -Ri,p . £5a - 4. 1.T - * ♦ ffcr-2* I (5) T T 2 2 The equation nay be rearranged to giTe —RlaP ♦ AalaT + - 4 £ t ~2 , + I (6) Since the left aide of equation (6) oan be calculated from experinental data, a least squares fit will giTe the best values for 4H 0 and I, the integration con­ stant. APPARATUS All heating was done by induction, using a General Electric or a Westlnghouse 20 kilowatt elec­ tronic heater. Three furnaoea were uaed for the vapor pressure determinations. A furnace for temperatures below the optical range {Figure 1) was uaed for vapor pressure runs on molybdenum trioxide and molybdenum dioxide- molybdenum trioxide mixtures. The vapor pressure runs on molybdenum dioxide, molybdenum-nolybdenum dioxide mixture, tungsten trioxide and tungsten dioxide were made in either a high temperature pyrex glass furnace (Figure 2) or in a metal furnace (Figure 3). A Furnace for Temperatures Below 800°C. This furnace, shown in Figure 1, consisted of a water cooled pyrex glass cell connected to the vacuum system by means of a flat ground glass joint sealed with a dry "0" ring. Stopcocks and a 20 liter Distilla­ tion Products oil diffusion pump were separated from the furnace by a trap refrigerated with liquid nitrogen. -5 The vaouum in the system was of the order of 1 x 10 mllllmetars of meroury or less, as measured with a cold cathode ionisation vaouum gauge placed between the furnace and the trap. -6- C = D ^ 3 D KN'J DSFN WA 7 ER CUD CELL JACKET radiatio n SHIELD THERMOCOUPLE TABLE TO VACUUM STUPAKOFF SEALS AN INDUCTION FURNACE FOR TEMPERATURES BELOW 8 0 0 ° C FIGURE I -7- PLANE LENS RING TO VACUUM o r o r KNUDSEN CELL o r o WATER JACKE T — ii—' PYREX GLASS EURNACE FIGURE 2 -8- TT FLAT LENS u u V S / A TO VACUUM GAUGE fla r KNUDSFN CELL LENS O VACUUM QUARTZ PI ATE METAL INDUCt ILN f u r n a c e FIGURE 3 -9- Temperatures in this apparatus vara aaasurad with a .010 inch platinum to platinum-10$ rhodium thermo­ couple, lntroduead into the system by maana of Stupa- koff Beals. The eight inches of the thermocouple extending from the hot Junction were insulated with porcelain protection tubes. They were further encased in an Invar tube 3/32 inch in diameter, which was mounted vertically from a brass baae resting on the bottom of the vapor pressure furnace. Tne tip of the thermocouple was wrapped with a small piece of platinum to increase the thermal contact with the Knudeen cell. A platinum cylinder the same size as the Knudeen cell was placed Just below the position occupied by the cell in order to reduce any losses of heat through the Invar tube. The thermocouple leads were shielded from the hot junction to the potentiometer. In order to filter out radio frequency currents, a filter consisting of three 0.02 microfarad condensers was connected across the thermocouple leads and from each lead to ground. The cold junction was immersed in a bath of crushed ice and distilled water. A Leeds and Northrop White Double Potentiometer with a capacity of one hundred thousand mlorovolts was used to measure the voltage of the thermocouple. - 1 0 - Before installing tbs thermooouple in ths furnaes it was carefully annealed by suspending it in a strain- free fashion and passing a ourrent through it. The temperature of the leads was held at 1A50°C. for one hour. It was then calibrated against a platinum to platinum-10£ rhodium thermocouple which had been stan­ dardised using lead, oopper, aluminum and sine melting point samples furnished by the Bureau of Standards. The calibration of the thermooouple used in the vapor pressure measurements against the standardised thermo­ couple consisted of joining the two couples at their Junctions and placing them in a quarts tube frosen in a cylinder of copper in a small resistance furnace. Temperature was measured with the standardised thermo­ couple, and both the differences between the voltage of the platinum leads of eaoh thermooouple and the differ­ ences between the platinum—2.0% rhodium leads were found by means of a switchboard. When the differences ware added and plotted against the tenperature of the stan­ dardised thermocouple a calibration curve was obtained. As a final check of the aecuracy of the thermocouple, it was calibrated under the conditions which existed during the runs. A tantalum bucket containing a thermo­ couple wall, which was lined with platinum to eliminate - 1 1 - bimetal effects, was filled with aluminum (National Bureau of Standards sample) and placed In the furnace. The system was evacuated to 1 x 10~^ millimeters of mercury. The aluminum was melted and an attempt was made to get a cooling curve through the freeaing point. Due to the small masa of aluminum, however, the rate of cooling was so great that the plateau expected in the curve did not appear. More aluminum was added in the form of small chips and the system was again evacuated. The temperature was Increased very slowly while the ch lpe were observed. The first indication of melting occurred at 660.0°C. as computed from the calibration curve de­ scribed above, and the whole sample was molten at 661.2°C. This compared very well with the melting point of 659.7°C. quoted by the Bureau of Standards. A High Temperature fjcrex Glass furnace The pyrex glass furnace ahown in Figure 2 consisted of a water Jacketed tube connected through a trap to a 10 liter Distillation Products vacuum pump backed by a Velah Duoaeal fore pump. Pressure was measured with a 3C-24 vaouum gauge and was leas than 1 x 10“^ milli­ meters of mercury. The sample rested on a tripod of •060 inch tungsten rode projecting from a base which was held in place by a .060 inch molybdenum wire frame. The top of the furnaoe was sealed to the furnace by a dry - 1 2 - "0" ring between the flat ground glaaa aaals.
Details
-
File Typepdf
-
Upload Time-
-
Content LanguagesEnglish
-
Upload UserAnonymous/Not logged-in
-
File Pages76 Page
-
File Size-