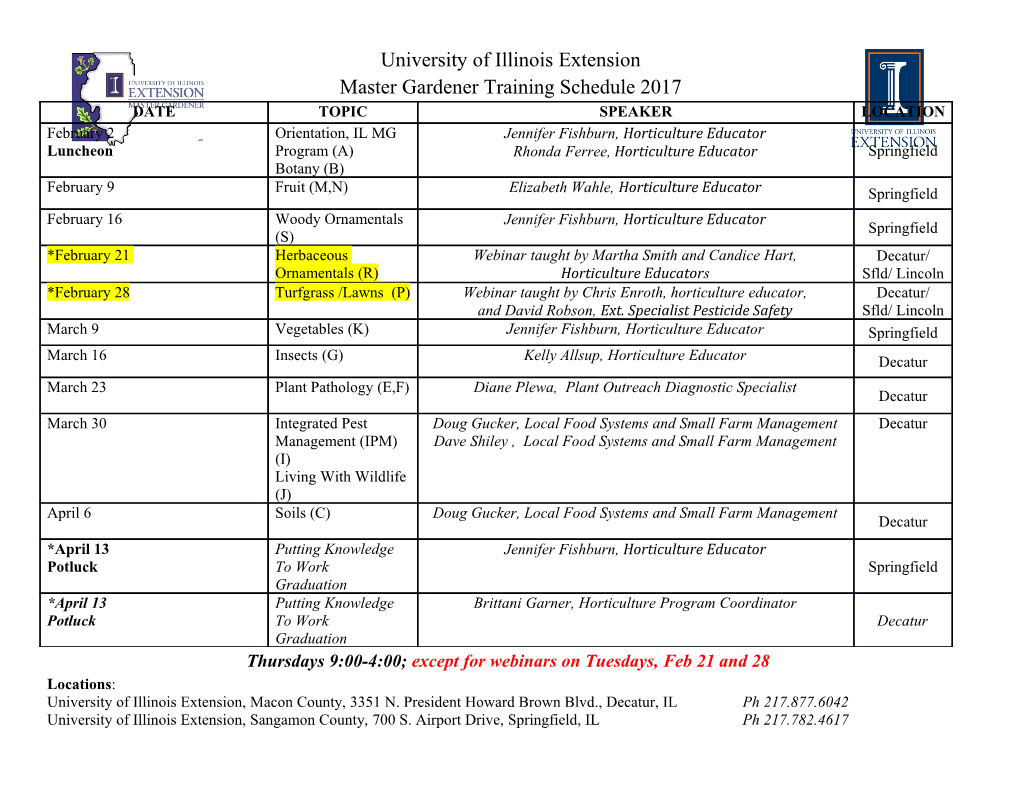
~.. STUDY OF A COUNTER-ROTATING, INTERMESHING EXTRUDER AS A POLYCONDENSATION REACTOR /" A Thesis Presented to the Faculty of The College of Engineering and Technology Ohio University In Partial Fulfilment of the Requirements for the Degree Master of Science by Edward R. Crowe November, 1992 LIBRARY. This Thesis has been approved for the Department of Chemical Engineering and the College of Engineering and Technology Associate Prof Chem1cal Engineering Dean of the College of Engineering and Technology iii Abstract An experimental study and model development have been performed to better understand the reactive extrusion of polyethylene terephthalate. A process was developed using a 34 mm counter-rotating twin screw extruder to depolymerize a commercial grade of polyethylene terephthalate into an acceptable pre-polymer for reactive extrusion experiments. Residence time d Ls'tr Ibut.Lon experiments were conducted at different screw speeds and feed rates to characterize the flow patterns of the extruder. Based on these results an idealized plug-flow model was developed to simulate this process. An experimental design using the controllable process variables of zone temperature, feed rate and nitrogen flow sweeping across the surface of the polymer melt was developed to stUdy the individual effects of each of these variables as well as any interactive effects. The results indicate that the feed rate and nitrogen flow have an effect on the degree of polymerization of the product. However, the stUdy clearly shows the dominant effect to be ,the average residence time of the polymer melt in the vent zone. The idealized plug-flow model presents a reasonable representation of this process. The predicted product degree of polymerization is slightly higher than the experimental results due to the exclusion of any degradation reactions. The model reinforces the importance of residence time and devolatilization effectiveness in the condensation reaction. iv Acknowledgements I would like to take this opportunity to express my appreciation to the faculty of the Department of Chemical Engineering for providing a challenging and enjoyable experience and for making a "non-traditional" student feel welcome. My advisor, Dr. K. J. Sampson, deserves a special thanks for his valuable advice and guidance during the course of this research. Mere words cannot adequately express my feelings of gratitude and affection for my wife, Sarah, for her unselfish. support and encouragement. v Table of Contents Page Abstract iii Acknowledgements. iv List of Figures vi List of Tables vii Chapter 1: Introduction. 1 Chapter 2: Theoretical and Experimental Background . 5 2.1 Reactive Extrusion with Twin-Screw Extruders . 5 2.2 Co-rotating vs. Counter-rotating Configuration 13 2.3 Processing of Polyethylene Terephthalate 18 Chapter 3: Experimental Methods and Equipment. 25 3.1 Extruder Equipment and Set-up . 27 3.2 Residence Time Distribution Measurement 32 3.3 Depolymerization Procedure . 37 3.4 Polymerization Procedure. 40 3.5 Polymer Characterization. 46 Chapter 4: Results. 54 4.1 Residence Time Distribution Results . 54 4.2 Depolymerization Results. 57 4.3 Polymerization Results 64 Chapter 5: Reactive Extrusion Modelling. 73 5.1 Idealized Plug-Flow Model 74 Chapter 6: Conclusions and Recommendations. 89 6.1 Conclusions . 89 6.2 Recommendations for Future study . 91 References. 94 Appendix A: Dilute Solution Viscosity Test Method 98 Appendix B: Program Listing of Reactive Extrusion Model 104 vi List of Figures Figure Page 2.1 Classification of Twin-Screw Extruders . 15 2.2 Stages of PET Synthesis • 20 3.1 Schematic Diagram of Experimental Apparatus 26 3.2 Configuration of Screw Elements 29 3.3 Molecular Weight vs Intrinsic Viscosity 53 4.1 Response Curve for Depolymerization Experiment 54 4.2 Response Curve for Polymerization Experiment • 55 4.3 Response Curve for Polymerization Experiment . 55 4.4 Results of Post-processing Experiment 60 4.5 Results of Experiment #1. 65 4.6 Normal Probability Plot of Effects 70 4.7 AC Interaction Plot 70 5.1 . Flow Diagram for Devolatilization Algorithm 84 A.1 Cannon-Ubelohde Dilution Viscometer . • 103 vii List of Tables Table Page 3.1 Description of Screw Elements . 30 3.2 2 3 Factorial Design for Experiment #2 46 4.1 Comparison of Residence Time Distributions. 56 4.2 Individual Results of Depolymerization Runs 58 4.3 Test Results from continuous Depolymerization. 59 4.4 Post-processed Test Results from continuous Depolymerization 61 4.5 Test Results from Alternate Depolymerization Process 62 4.6 Post-processed Test Results from Alternate Depolymerization Process. 63 4.7 Results of Experiment #2. 66 4.8 Measured Deviation of the Degree of Polymer­ ization of the Extrudate Compared to the Feed. 66 4.9 Analysis of Variance of Degree of Polymer- ization Data. 68 4.10 Calculated Data for Normal Probability Plot 69 4.11 Calculated DP Values and Residuals 72 5.1 comparison of Theoretical and Experimental Mean Residence Time 79 5.2 Comparison of Model and Experimental Results. 86 5.3 Example of output from Reactive Extrusion Model 88 1 Chapter 1: Introduction Traditionally, extruders in the plastics industry, whether designed with single or mUltiple screws, have been used to melt and homogenize blends of different polymeric materials as well as to mix polymers with performance enhancing additives or pigments. Although this traditional view of extrusion technology is still dominant in the industry, reactive extrusion is now being viewed as an efficient means of continuously polymerizing monomers as well as chemically modifying existing polymers [1]. As a result of the rapid growth of the polymer industry, the increasing demand for high performance thermoplastic materials and the need for cost competitiveness and manUfacturing flexibility, reactive extrusion has been evolving as a process for efficient continuous polymerization. The reactive extrusion process effectively combines two traditionally separate manUfacturing operations; the synthesis of the polymeric material and final processing into a finished product. For polymerization processes, extrusion equipment has certain distinct advantages over other continuous and batch processes. First, the intense mixing in an extruder, particularly a twin-screw extruder, continuously creates new, thin surface layers. This surface renewal action facilitates the mass and heat transfer effects. This capability of heat and mass transfer can not be achieved with a high viscosity 2 polymer mixture in a stirred tank reactor. As a result, the equivalent residence time in an extruder is lower, thus avoiding a long exposure to high temperatures that can cause polymer degradation. Also, the ability of an extruder to process polymers of high viscosities without the need for solvents results in a lower raw material cost as well as eliminating the capital costs needed for solvent recovery equipment. Although all of these processing characteristics offer specific advantages over stirred tank reactors, the most attractive advantage for reactive extrusion is the ability to offer a flexible manufacturing alternative. As the polymer industry continues to search for ways to meet the challenge of increased competition and need for cost efficiency, the mechanics of an extruder production line is such that ease of set-up and relatively quick change-over to new products provide a flexibility that can increase small order effectiveness. This research is a study of the suitability of a counter­ rotating, fUlly-intermeshing twin screw extruder to reactively process polyethylene terephthalate. Using a Leistritz 30.34 laboratory extruder, de-polymerization trials are performed to manufacture a low molecular weight polymer which is then used as the raw material for the polymerization experiments to test the extruder's performance in reactive extrusion. In addition, this research requires the implementation of a test method to estimate the molecular weight of the extruded 3 polymer. Finally, a theoretical reactor model is presented that correlates the empirical results. The focus of Chapter 2 is the discussion of previous experimental work found in the open literature. Published literature under the general SUbject of reactive extrusion is discussed, as well as other pertinent material, such as the characteristics of co-rotating versus counter-rotating twin screw extruders. ConclUding this chapter is an introductory discussion of condensation polymers with a specific focus on polyethylene terephthalate. The chemistry of PET will be presented along with a discussion of manUfacturing processes. Chapter 3 discusses the experimental methods and equipment used in this research. A detailed description of the Leistritz laboratory extruder and peripheral equipment is presented as well as an overview of the operating parameters. In addition a discussion of the method and results of the residence time distribution experiments is presented. Also in this chapter, the two experimental processing methods are discussed. Beginning with a general purpose grade of PET with a number average molecular weight of approximately 23,000, a process for adding ethylene glycol for de-polymerization to obtain a lower molecular weight polymer is presented. The product of this process is the feed material for the polymerization experiments where the investigation focuses on the synthesis of a higher molecular weight polymer. Concluding Chapter 3 is a discussion of the test method used 4 to characterize the polymer products as well as the correlations
Details
-
File Typepdf
-
Upload Time-
-
Content LanguagesEnglish
-
Upload UserAnonymous/Not logged-in
-
File Pages121 Page
-
File Size-