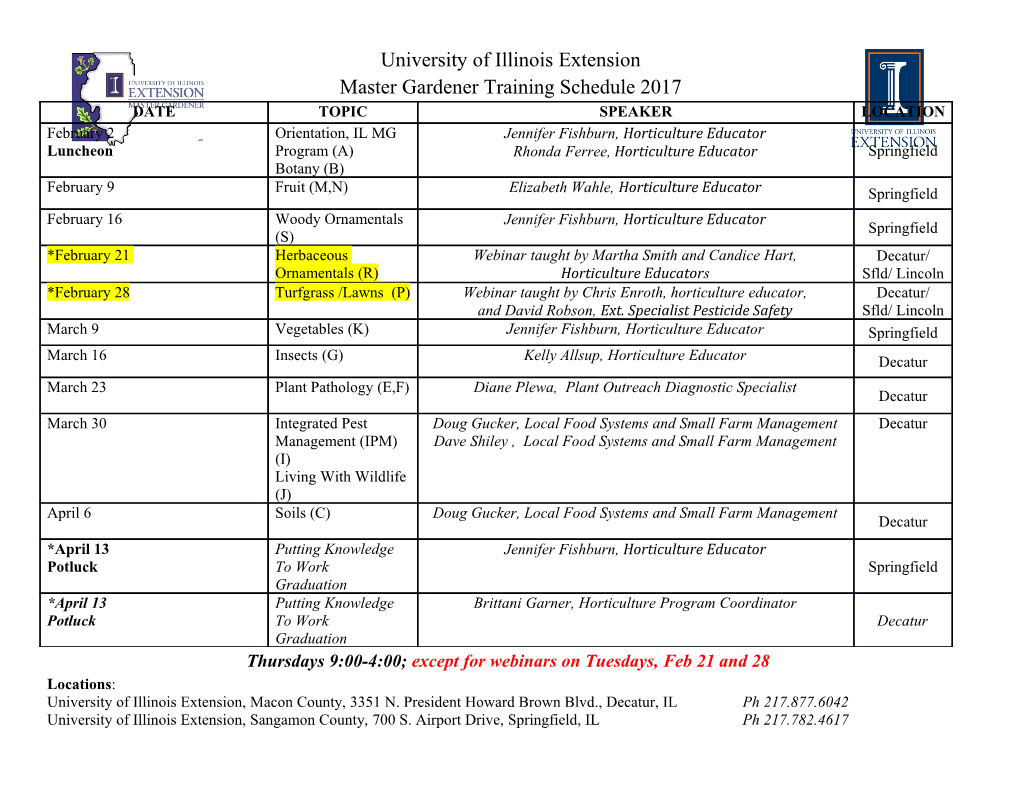
The Repointing Of Historic Masonry Buildings Robert C. Mack, AIA and James S. Askins Historic Structures Consultant Published by SERMAC Industries Inc. PROLOGUE CONTENTS The restoration and rehabilitation of older buildings is one Prologue 2 of the most interesting, yet challenging, trends in architec­ Introduction 3 ture today. This work not only heightens our awareness of our past while preserving the character of our cities and WhyRepoint 3 neighborhoods, it also makes good practical sense. Re-use Logistic Planning 4 of existing structures saves building materials and energy Scaffolding 4 while providing usable space more quickly and at a lower cost than new construction. In addition, restoration and Contracts 5 rehabilitation efforts are creating many new jobs throughout Types 5 the country. Bonds 5 For many years. SERMAC Industries Inc. has been Scheduling 5 assisting in the maintenance of buildings; good maintenance Measurement & Payment 5 has given these buildings longer life while making them more pleasant places in which to work and live. More recently, Contract Documents 6 SERMAC has been active in the exterior cleaning and im­ Scope 7 provement of masonry buildings. We are gratified to have Temperature 7 had a role in the restoration of many significant buildings. Job Layout 7 In the interest of providing our clients and licensees with Final Tests 7 basic information concerning the repointing of masonry Technical Specifications 7 buildings, we are pleased to publish this booklet. Written by Robert C. Mack, a restoration architect, it is based in Test Panels 8 large part on material presented by James S. Askins, a masonry restoration specialist, during a symposium spon­ Planning & Research 8 sored by SERMAC on July 15, 1977; Mr. Askins also took Pointing Styles 8 the photographs. We hope you find it interesting and useful Replacement Bricks & Stones 10 in your work. Materials 11 Masonry Units 1 ] Mortar 12 Storage 12 Durability 12 Color and Texture 13 Working Properties 13 Mortar Mix .14 Execution of The Work . .' 15 Joint Preparation 15 Mortar Preparation 17 Mortar Application 19 Aging the Mortar 20 Curing 20 Cleaning 21 Conclusion 21 INTRODUCTION This information has been written to assist building owners and their restoration contractors understand the purposes, techniques, and potential problems of re­ pointing historic masonry buildings. No book can hope to teach a skill such as repointing; that skill can be gained only through experience. It can, however, form Figure la) Note area of deterioration near cornice return; this a sound basis for beginning to learn a new skill, as well deterioration is related to movement within the wall and cannot as a basis for effectively dealing with masonry contrac­ be corrected by repointing. tors, and with the masons themselves. Simply stated, repointing is the process of removing deteriorated mortar from a masonry joint and replacing the old mortar with new, sound mortar. This process sometimes is referred to as "tuck pointing"; to the purist, however, "tuck pointing" more properly refers to a decorative treatment rather than a method of repair; true tuck pointing is the process of adding a finish layer of mortar, occasionally tinted, to the outer portion of a newly laid joint. Repointing also is simply known as pointing. Why Repoint? Figure lb) Mortar in this wall is generally deteriorated and is in All buildings and building materials are in the con­ need of replacement. stant process of deterioration. The speed with which this deterioration takes place depends upon the quality of the original construction, the original design of the building, the wear to which the building is subjected, and the quality of the maintenance and repair program for the building. Masonry has an advantage over many other building materials because it has areas which are designed to absorb many of the stresses which lead to deterioration, and these areas can be readily replaced as they deteriorate. A masonry wall has mortar joints which, if a building was properly designed, absorb the stresses of deterioration and then are replaced by re­ pointing. If properly done, this process can be repeated many times without causing any damage to the masonry units themselves. Figure Ic) Detail of circled area in the previous photo; note depth A building needs repointing if observations point to to which original mortar has deteriorated. outward signs of deterioration (Figure 1). Loose bricks, falling mortar, or damp walls may well result from de­ teriorated mortar. They also can relate to a variety of other problems such as leaking gutters, settlement, or structural deterioration. It is important, therefore, to fully investigate the possible causes for deterioration prior to concluding that repointing is necessary. Repoint­ ing cannot solve other problems! It may be that the services of a consultant will be required at this stage, frequently saving money in the long run by preventing unnecessary work from being undertaken. Figure Id) Spading of brick from use of high cement (hard) mortar. Logistical Planning Once the decision to repoint has been made, consid­ eration must be given to the timing of the work. In the case of a project involving more than just repointing, for example, the proper sequence of the different aspects of the project must be determined in advance, preferably under the direction of an architect or a qualified gen­ eral contractor. It also is important to remember that the repointing will be a lengthy process, so it may need to be scheduled around special activities planned for the building. Similarly, many projects will require scaffolding, which may make access to the building dif­ ficult. In addition, the project must be planned for a time of year in which the mortar will neither freeze nor bake before it is properly cured. Scaffolding Nearly all projects will require some type of access to masonry above the ground level. The two most com­ mon means of providing this access are fixed tubular scaffolding and swing stage scaffolding (Figure 2). Each Figure 2a) Tubular metal scaffolding. type has advantages and limitations, so the choice will depend upon the particular job requirements. Fixed scaffolding: If all other factors are equal, fixed scaffolding is preferred because it does not move, thereby permitting masons to exert pressure more firmly against the wall during cleaning and filling operations. Fixed scaffolding also permits several operations with one erection, thus is less expensive for projects involving many operations. It also allows inspection of all areas of the work rather than only the area of current opera­ tions. There is no need to enter the building with fixed scaffolding, which may be more convenient for the ten­ ants. On the other hand, machinery and equipment are less mobile with fixed scaffolding. The required climb­ ing may be tiring for the masons. In addition, fixed scaffolding generally is practical for use only on low and moderate height buildings, although scaffolding of up to twenty stories is not impossible. Swing stage scaffolding: On projects involving only limited work, swing stage scaffolding normally is less expensive. In addition, it is more quickly installed and permits more rapid movement of equipment and mate­ rials. It also causes less interference with ground level movement. On the other hand, for involved projects Figure 2b) Swing stage scaffolding. several passes with a swing stage will be more expensive than fixed scaffolding. It also frequently is necessary to enter the building to install the swing stage, which may be undesirable for the tenants. 4 CONTRACTS Contracts form the legal basis for the relationship between the building owner and the contractor, and the Bonds contractor and subcontractors. As such, it is essential The requirement for bonds, if any, should clearly be that contracts be clearly written, understood by all stated in the contract. Bonds generally are recommended parties, and enforceable in court, should the need arise. for all jobs over $5,000. The three types of bonds which The contract normally consists of the construction docu­ are used most frequently are bid bonds, performance ments (plans and specifications), a schedule for the bonds, and labor and materials bonds. work, a statement of the contract price, provision for Bid bonds are used to insure that the low bidder on progress payments, and other miscellaneous informa­ a project will actually sign a contract to perform the tion. The contract documents will be discussed more work. fully later in this booklet. Performance bonds are used to insure that the work will be carried out in conformance with the plans and Types of Contracts specifications. Labor and materials bonds (payment bonds) are used There are three types of contracts in common use for construction projects. The primary difference between to insure that the contractor will pay for all the labor them is in the method of computation of the price for and materials used on the job; these bonds frequently the work. are combined with the performance bonds. In each type of bond, a surety company pledges to 1. Stipulated sum (also known as lump sum or fixed pay the client for any expenses incurred by the con­ price) contracts are the most commonly used form tractor's failure to perform the task covered by the of construction contract. Under this type of agree­ bond. ment, the contractor agrees to perform a specified amount of work for a specific fee. Although this type of contract works well for a new construc­ Scheduling tion project, where the work can be clearly The contractor should be required to meet any sched­ defined, it frequently is not suited to a restoration uling requirements stated by the client in the bid docu­ project because ofthe uncertainties involved. When ments. If the client has no particular schedule require­ unanticipated work is discovered, necessitating a ments, the contractor should includea proposed schedule change to the contract, the contractor is in the as part of the bid.
Details
-
File Typepdf
-
Upload Time-
-
Content LanguagesEnglish
-
Upload UserAnonymous/Not logged-in
-
File Pages22 Page
-
File Size-