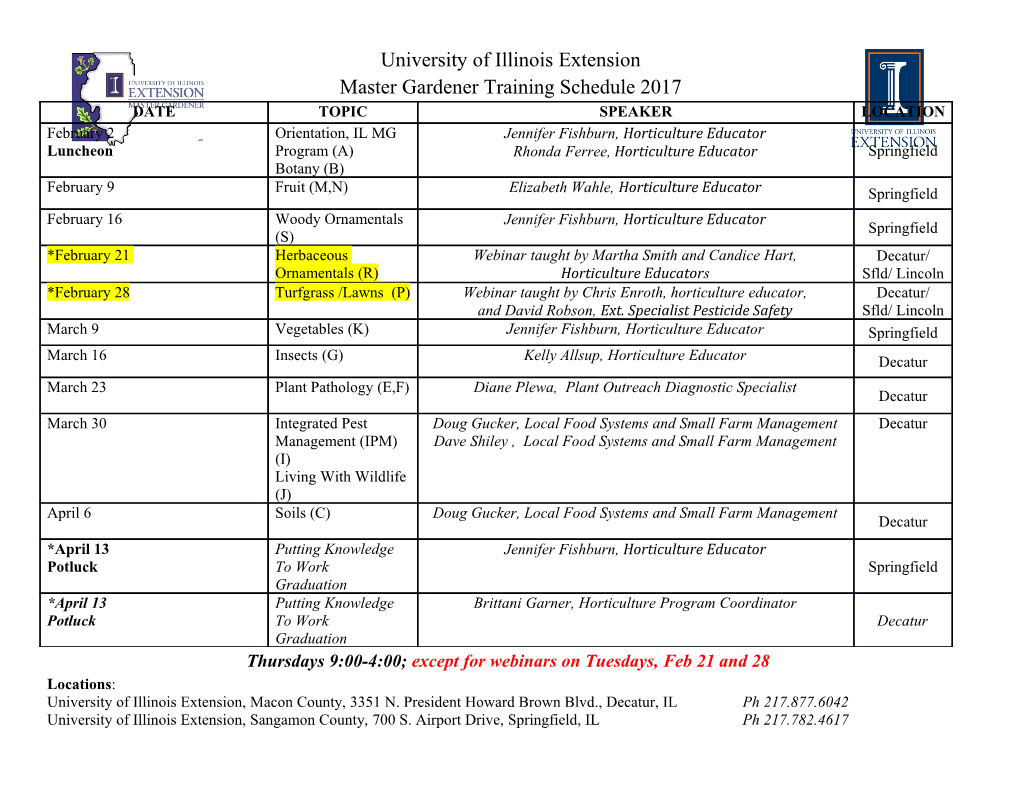
Computers in Foundries Dr Thoguluva Raghavan Vijayaram* and Dr Paolo Piccardo** * Principal Lecturer, Faculty of Engineering and Technology, FET MMU, Multimedia University, Melaka Campus Melaka, Malaysia ** Professor, Dipartimento di Chimicae Chimica Industriale, DCCI, Sezione di Chimica Inorganicae Metallurgia, Genoa University, Genoa, Italy ABSTRACT RIASSUNTO Computers have now entered into the foundry I computer sono entrati prepotentemente nella fonderia, engineering. Foundry mechanization and modernization un’arte antica che si è evoluta in una scienza moderna. La are of considerable importance today when the foundry fonderia è oggi completamente monitorata e controllata has evolved from an ancient art into a modern science dal computer, che assume un’importanza primaria per and it is fully controlled and monitored by computers. migliorare la qualità dei getti e la produttività. Dal punto Modernization is the only key to improve casting quality di vista industriale, i PC sono da tempo utilizzati nelle and productivity. From industrial point of view, they aree amministrative della finanza, contabilità, gestione have been in use in the administrative areas of finance, del personale, salari, stipendi, gestione del magazzino. accounting, personnel records, wage, salaries, and Attualmente molti sistemi di macchine per fonderia sono inventory control for a long period. Many foundry machine computerizzati. Grazie al computer la fatica e lo stress systems are computerized. Due to the entry of computers per i lavoratori e lo staff si sono ridotti notevolmente. La in foundries, fatigue and strain on the workers and staffs cultura del lavoro è notevolmente migliorata, e con essa si have been considerably reduced during working and sono sviluppati il coinvolgimento, la creatività e il senso di work culture has improved tremendously. Improved work partecipazione. Questo articolo di rassegna presenta ruolo, culture can lead to a sense of participation, involvement, prospettive e applicazioni del computer nella fonderia; in and creativity. This review paper discusses on the role, particolare si sofferma sulla progettazione degli stampi, prospects, and application of computers in foundries. sulla simulazione numerica del complesso processo di Besides, an introduction on the computer aided foundry solidificazione e sulle linee di produzione computerizzate e model design and computer aided foundry die design are automatizzate. Vengono infine prospettate le applicazioni presented precisely in this paper. It also discusses on the dei sistemi esperti e son passati in rassegna vari tipi di numerical simulation of casting solidification performed in pacchetti software comunemente adottati nella fonderia. foundries and a brief information about the computerized and automated foundry line have been provided in this technical paper. The applications of expert systems in foundries and various types of foundry software packages commonly used in the metal casting industries are explained in detail in this review paper. KEYWORDS Computer aided foundry model, Computer aided foundry die-design, casting design and numerical simulation, foundry expert systems, foundry software packages. 28 Metallurgical Science and Technology Vol. 30-2 - Ed. 2012 INTRODUCTION emission in foundries are monitored and controlled by computers. Computers with the aid of imaging Foundry technology deals with the processes of systems perform micro structural characterization producing castings in molds made in either sand and capture photomicrographs since software is or some other material. Metal casting is the oldest available in them [2, 4]. manufacturing processes. Today, a variety of molding processes and melting equipment are available to cast different types of metals and alloys in foundries. However, the methods and techniques of III. COMPUTER AIDED FOUNDRY production of castings have changed considerably, MODELS DESIGN the fundamental principles remain almost the same. The traditional approach to resolve the design and Castings have several characteristics that clearly the process planning tasks, commonly used in a define their role in modern equipment used for foundry, is that the plans are handed over to the transportation, communication, power, agriculture, experts who specify the procedures to make the construction and in industry. Cast metals are required cast product and draw it. The designers, using their in various shapes and sizes and in large quantities for experience and knowledge, generate projects and making machines and tools, which in turn work to instructions for manufacturing the foundry products provide all necessities and comforts of life. However, based on the design specifications and the available certain advantages inherent in castings such as design installations and operators [1]. Consistent designing and metallurgical advantages and in the casting and planning require knowledge of casting process itself, endow them with superiority over other processes and experience. This has led to the manufacturing methods. Foundry mechanization and development of Computer Aided Process Planning modernization are of considerable importance today (CAPP) systems, which are becoming more and when the foundry has evolved from an ancient art more important in this field. CAPP systems are into a modern science. Computers have entered beginning to be developed as a link between design into all industrial applications, and more so in foundry and manufacturing, filling the existing gap between technology [1, 4]. CAD (Computer Aided Design) and CAM (Computer Aided Manufacturing). CAPP allows the user to develop an integrated structure that deals with the II. PROSPECTS flow of information between CAD, CAPP, MRP and numeric control (NC) activities within the company Nowadays, casting quality is considered as [2,3]. There are two approaches to computer-aided an important one. This satisfies the customer process planning. The first is the variant approach, in requirements in many ways. To achieve and maintain which a new process plan is generated using existing quality, it is necessary to control the production standard process plans stored in the database. The process firstly. Manual control does not fulfill to attain second is the generative approach, in which a new the expected quality of castings. So, computers process plan is generated from scratch, i.e. it will are introduced to manage and control the process not use any standard existing process plan. The efficiently. Application of computers plays a vital role basic requirement for a generative process planning to control the entire casting process, quality, metal system is to interpret the given component model composition, liquid metal handling, and to perform drawing in terms of manufacturable features. The casting defect analysis with the aid of expert main objective is the realization of a computer-aided systems. Besides, computers help to simulate the system to help, automatically select and finally define casting solidification during processing. This paves the parameters of a foundry models. In the applied the way to design the casting correctly and hence methodology, the steps are divided into three parts: to avoid major defects like hot spots and also to knowledge acquisition, the activity modification and identify and locate the stress concentration zones. finally development and implementation of the tool It provides the temperature history of castings, [2-4]. detailed information on the temperature contours, Foundries represent an important sector of the and distribution inside the solidifying casting can be casting manufacturing industry. One of the most understood. At present, different types of software important aspects is the designing of the models packages are available to perform analysis on with their equipment. The successful casting of a various aspects. pre-designed shape is heavily dependent on the skill Among them, finite element analysis is an important and experience of the foundry engineer and this is tool to study the temperature, the stress distribution a time consuming step in a production environment. and micro structural evolution. Modern foundries are Thus, the main objective is the realization of a automated and absolutely controlled by computers computer-aided system to define the models with minimal manual assistance. Pollution and parameters as machining allowance, draft corner, Vol. 30-2 - Ed. 2012 Metallurgical Science and Technology 29 radius, dimension, feed head, flask and pouring simulating the solidification of the molten metal in system. The software tool used for the prototype the ceramic mold. system is an object-oriented programming In recent years, Computer Aided Design has language called Visual Basic, used to create the become an essential tool for designing metal parts. main functional modules. The computer system CAD eliminates the manual drafting process, and starts with the geometrical definition of the part. allows the engineer to design more sophisticated Based on the geometrical dimensions, the program parts with greater precision. However, the ultimate executes the calculations of the model parameters output of expensive software and computing power in order to obtain a correct design. The result gives is a two-dimensional paper drawing. the parameters for model and a proposal for the dimensions, which can be modified. The main Foundries must interpret the part's design feature of the proposed integrated approach is drawing into a pattern design,
Details
-
File Typepdf
-
Upload Time-
-
Content LanguagesEnglish
-
Upload UserAnonymous/Not logged-in
-
File Pages11 Page
-
File Size-