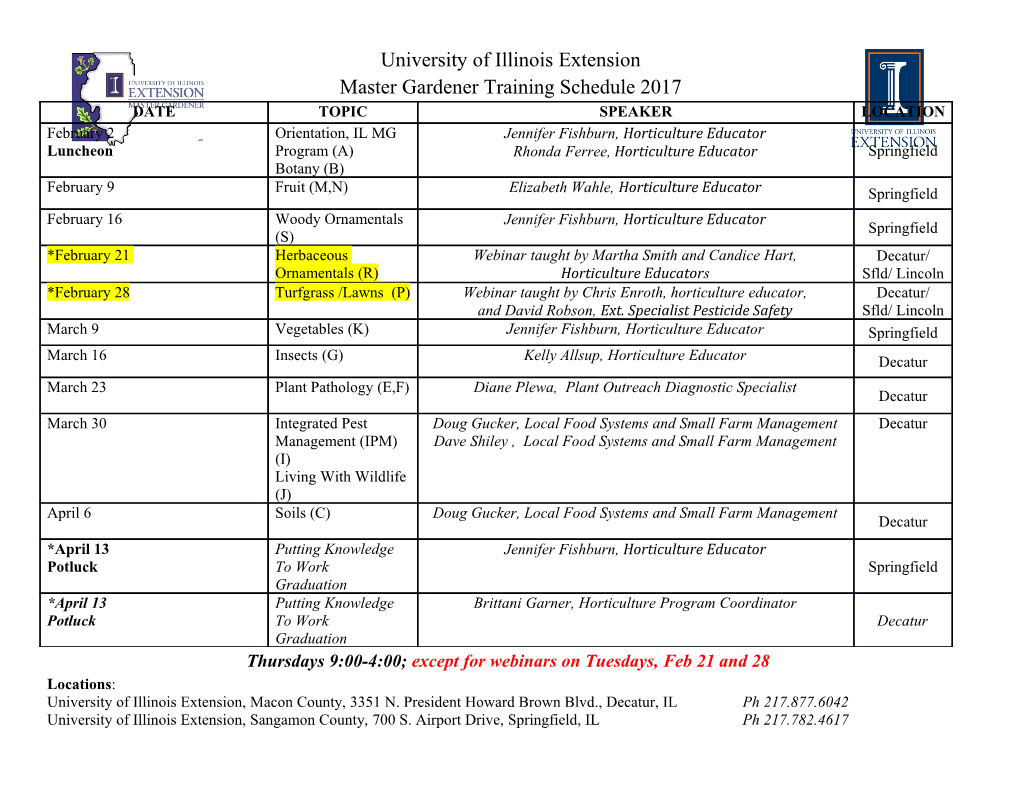
International Research Journal of Engineering and Technology (IRJET) e-ISSN: 2395 -0056 Volume: 03 Issue: 09 | Sep-2016 www.irjet.net p-ISSN: 2395-0072 DESIGN MODIFICATION AND ANALYSIS OF ENGINE EXHAUST MANIFOLD S.B.Borole1, Dr. G.V.Shah2 [email protected] [email protected] Mechanical Engineering Department, P.V.P.I.T. Bavdhan, Pune University, Pune, Maharashtra, India ---------------------------------------------------------------------***--------------------------------------------------------------------- Abstract - This study focuses on the development of a thermal stresses while welding [4]. This stresses weakens reliable approach to predict failure of exhaust system fitting the materials, produces the defects, which can take shape of and on the removal of structural weaknesses through the small pieces of material, weld spatter, may loose and end up optimization of design. The task with this project was to find a destroying the catalytic converter [5]. Other defects can new solution concept for the connection of pipes into flanges in occur in the welding seam and they must be repaired manifolds. The concept that uses today for their manifolds is manually. However, the manifold should not be based on welding the pipes into place in the flange. The manufactured by casting, because the high temperatures in product development model that is used in this project is present combustion engines demand more expensive and written by Fredy Olsson. For this project have the parts high quality materials that causes problem when casting [7] “Principal construction” and” Primary construction” been [2]. The goal in the development of exhaust system fitting is used. to analyze several solutions weldless. The solutions that are The Objective is to present experimentation, modeling subject for further development are prepared during the and analysis of exhaust system fitting weldless by using FEA. primary construction with for example CAD. Different Modeling is done using PRO/Engineer Creo. Analysis is carried solution concepts are result from this thesis work. All of the out by using ANSYS. The optimization of cast and fabricated solution concepts contain end shaped pipes that provides the manifolds (single or dual wall design) requires different sealing area against the engine. The main difference between techniques, due to the production restrictions. The locations them is that the flange is designed in different ways. where failures occur, on both the exhaust manifolds (cast or 1.1 Failure Modes of Exhaust Systems fabricated) and exhaust manifold gaskets, are predicted with Failures of exhaust manifolds are mainly caused by high degree of accuracy. the extreme temperature gradients the part has to From the study it is seen that the different solution withstand. A secondary cause for failures is the dynamic concept is result from this work. All of the solution concepts excitation of the exhaust subsystem, especially if not contain end shaped pipes that provides the sealing area negligible masses of attached parts like turbocharger or against the engine. The main difference between them is that close-coupled-catalyst are driven into resonance. Typical the flange is designed in different ways. Different techniques structural failure modes are manifold cracking and leakage. are needed for the optimization of cast and fabricated Those are related to the design and boundary conditions if a manifolds, because of production restrictions. This problem is proper material choice was done initially. Understanding already been addressed and a procedure has been the root cause of a failure is the most challenging part on implemented. the way to a solution. The manual and automatic optimization methods have distinct advantages and disadvantages. A cost effective Understanding Failures solution is delivered by a combined methodology, which also results in a failure-free exhaust manifold design. TMF Cracking – An initial thermal loading of exhaust manifolds can cause the material to exceed the Key Words: Development Project, Manifold, Flange, Pipe, yield stress in large areas of the exhaust t manifold. Cyclic End Shaping, Weldless FEA temperature loading causes a few areas to exhibit local . cyclic plastic straining of the material, which may cause a 1. INTRODUCTION crack initiation. Depending on the location of the high Noise & vibrations are major responsible factors towards loaded areas, individual design parameters need to be human comfort level. To enhance the human comfort, it is considered in order to find a target-oriented optimization very necessary to reduce noise & vibration level due to strategy. It becomes obvious that a detailed knowledge of fitting of exhaust system, where noise and vibrations are the system behavior is needed, in order to interpret results more due to weld connections [6].The welding process is correctly. expensive due to high technology welding robots and time Leakage – Besides cracking of exhaust manifold consumption. The pipe and flange are exposed to large systems, the leakage problem is very often also related to © 2016, IRJET | Impact Factor value: 4.45 | ISO 9001:2008 Certified Journal | Page 210 International Research Journal of Engineering and Technology (IRJET) e-ISSN: 2395 -0056 Volume: 03 Issue: 09 | Sep-2016 www.irjet.net p-ISSN: 2395-0072 cyclic plastification of exhaust manifolds. Once leakage sealing material is placed between the pipe and the inside occurs, a partial destruction of the gasket and the flange of the hole. occurs, which may lead to an ensuing manifold crack due to a changed force flow in the exhaust manifold. Also here a detailed knowledge of the influencing parameters like bolt pretension, friction between adjacent parts and nonlinear gasket behavior is needed to get an initial understanding of the problem. High Cycle Fatigue – High cycle fatigue (HCF) Figure 2: Solution 2 problems at the exhaust manifold are caused by dynamic excitation. This kind of problem is not discovered very often, Solution 3 and is mainly related to unfavorable bracket design [3]. 2. OPTIMIZATION AN PRODUCT DEVELOMENT OF EXHAUST SYSTEM This pipe is connected to the flange with a screw thread, see Figure 3 below. The pipe and the flange are threaded. 2.1 Solution Concept- Several suggestions to solve the problem have been found after brainstorming and solution search. The collection of concurrent manufacturer’s products has also been examined. Information about working up materials Figure 3: Solution 3 and motorcycle repair manuals has been searched for in libraries. Solution 4 The solutions are divided into two groups, one were the connection of the pipe has been analyzed. The other group contains some different types of flanges. The hole in the flange is shaped as a cone. The The second group is to be subject for a short evaluation pipe is passed through the flange before its end shaped where the best flange for the solution is to be chosen [5]. also as a cone, see Figure 4 below. It is important that the end of the pipe stays a few millimeters outside the flange; Pipe Connection this enables a tension between pipe and flange when it’s mounted. In this chapter a search for principal solutions that are fulfill the criterions for the product take place. Solution 1 The pipe has larger diameter than the hole in the flange, see Figure 1 below. The pipe is squeezed into the hole and stays in the hole only because of the tension between the pipe and the flange. Figure 4: Solution 4 Solution 5 Solution 2 Figure 1: Solution 1 This solution is similar to solution 4, except that the pipe is end shaped to follow the edge of the flange see Figure 5 below. The sealing area is moved to the pipe end between the flange and the Engine The pipe is connected to the flange with some kind of sealing material. The flange is designed with an edge in the hole; see figure 2 below, the pipe rests on this edge. The Figure 5: Solution 5 © 2016, IRJET | Impact Factor value: 4.45 | ISO 9001:2008 Certified Journal | Page 211 International Research Journal of Engineering and Technology (IRJET) e-ISSN: 2395 -0056 Volume: 03 Issue: 09 | Sep-2016 www.irjet.net p-ISSN: 2395-0072 Solution 6 This solution is similar to solution 5, except for the Flange 2 cone shape see Figure 6 below. Solutions like this have been done in test series before at Extencore Solution This flange consists of only one piece, see Figure Exhaust System AB, but in slightly different design of the 10 below. Flanges like this are most common today. This flange. design does not permit thermal expansion as the others. Figure 10: Whole Flange Figure 6: Solution 6 Flange 3 Solution 7 This flange consists of one piece, but permits thermal expansion because of the weak points between the This solution is similar to solution 6, except that pipes sees figure 11 below. the sealing area is moved into the flange that is formed to fit the pipe end see Figure 7 below. Figure 11: Slotted Flange Figure 7: Solution 7 Solution 8 Table 1: Direct Grouping Method, Solution Judgment against Demands [1] This solution has a two-step end shape and the No. Solutio TD ED Pass flange is designed so that the pipe fits into the hole see The pipe is squeezedn into 1 0 2 No Figure 8 below. It is important that the end of the pipe the flange. stays a few millimeters outside the flange; this enables a Connection with 2 0 2 No tension between pipe and flange when it’s mounted. sealing material. The pipe and the flange 3 1 2 No are threaded. The pipe and flange are 4 2 2 Yes shaped as a cone. The pipe is shaped as a 5 2 2 Yes cone and follows the flange. Figure 8: Solution 8 A small end shape on the 6 2 2 Yes pipe. Flanges Connection A small end shape on the 7 pipe that fits a track in the 2 2 Yes flange.
Details
-
File Typepdf
-
Upload Time-
-
Content LanguagesEnglish
-
Upload UserAnonymous/Not logged-in
-
File Pages11 Page
-
File Size-