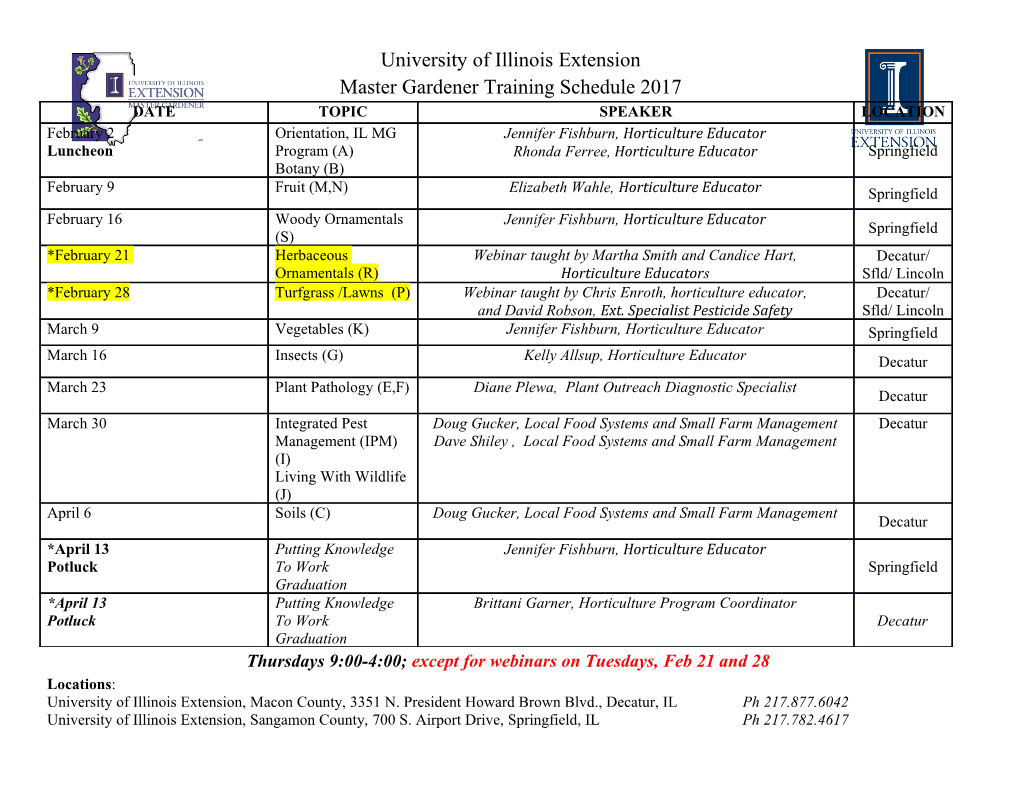
} Woody Biomass in Humboldt County Select Alternative Uses } Jameson Catlett Benjamin Goldberg Roger Turlington Riley Whipkey Prepared for: Redwood Coast Energy Authority Capstone - Spring 2020 Environmental Resources Engineering Humboldt State University May 12, 2020 Alternative Uses for Woody Biomass in Humboldt County - Team Jamo Jameson Catlett, Benjamin Goldberg, Roger Turlington, Riley Whipkey Executive Summary A large portion (23%) of the Redwood Coast Energy Authority’s (RCEA) electricity portfolio for Humboldt County is sourced from two local biomass incineration plants, using local logging and mill waste as feedstock. Because the biomass that is sourced for incineration meets California’s sustainable forestry requirements, the biomass plants are considered GHG neutral, renewable power sources to the state. Despite this, the community has mixed opinions on the local air quality impact and actual climate change contribution resulting from the biomass plants. As a result, RCEA has commissioned the authors to provide a technical, economic, and environmental assessment of alternative uses of biomass feedstock in Humboldt County. The team developed four alternative use cases for the biomass feedstock, subject to the following constraints: 1. The alternative must meet or exceed all federal, state, and local water and air pollutant standards concerning criteria pollutants and CO2. 2. The alternative must not create a demand for imported biomass or use a non-waste source of biomass. Alternative One proposed the creation of a composting facility to convert the woody biomass into a valuable organic soil amendment. Alternative Two used the woody biomass as raw material for the production of particleboard. Alternative Three consisted of a gasification and refining facility that would produce a substitute natural gas for local residential gas customers. Alternative Four proposed the construction of a 500 thousand ton per year wood pellet facility, creating a valuable export product from the waste biomass. The four proposed alternatives were evaluated against nine different criteria, themselves separated into four categories: Economic, Environmental, Technical, and Social. Each criterion was given a weight from 1-10, based on recommendations from RCEA. The sole Economic criteria was the payback period of the project, in years. The Environmental criteria included the net GHG emission difference between implementation of the alternative and the current baseline. The Technical criteria examined included system robustness, technological maturity, and overall operator skill level required. The Social criteria considered consisted of the amount of new criteria air and water pollutants, and number of jobs provided by the alternative proposal. The preferred alternative was determined using the Delphi matrix method, and a Wood Pellet manufacturing facility was chosen. This alternative would use all of the available biomass currently being used by the two biomass power plants in Humboldt. The facility is proposed to be sited at the Redwood Marine Terminal 2, the site of a former pulp mill, with access to a dock for loading finished pellets onto cargo ships, shown in Figure1. The recommendation of the report is an optimized production line with an output capacity of 72 tons of pellets per hour. The economic analysis performed indicated a payback period of 2.4 years for this proposed facility. The emissions, including criteria and GHG pollutants, were calculated for each of the power generation facilities, the manufacturing of pellets, and the combustion of the pellets. Figure2 represents the proportionate effect of each process in respect to criteria pollutant emissions, including ii Team Jamo, May 22, 2020 Fig. 1. Location of Redwood Marine Terminal 2 and surrounding parcels for proposed site (California Air Resources Board 2020a; Reed et al. 2012; California Air Resources Board 2020b) the combined effect of the two power generation facilities. The manufacturing of pellets does not produce any carbon monoxide (CO) or particulate matter (PM). Furthermore, emissions from the pellet manufacturing is lower than the two power generations combined, especially in regards to CO. The combustion of pellets, however, appears to significantly increase all emissions, resulting in significantly higher emission values. Carbon dioxide (CO2) emissions can be seen in Table1. Pellet manufacturing, when compared to the combined power generation facilities, is estimated to produces approximately 82% less CO2 emissions. If including the combustion of pellets, the amount of CO2 produced is roughly 44% higher than that of the combined power generation facilities. However, because it has the same "renewable" source material, pellets made from the biomass are considered to be carbon neutral to the state of CA. Depending on which governmental jurisdiction the pellets are combusted in, the emissions could be ruled carbon neutral, a GHG source, or even a carbon credit. iii Team Jamo, May 22, 2020 Fig. 2. A stacked chart of criteria pollutants and GHG emissions associated with DG Fairhaven, Hum- boldt Sawmill Company, pellet manufacturing, and pellet combustion (United States Environmental Protection Agency 1996; California Air Resources Board 2020a; Reed et al. 2012). TABLE 1. Carbon dioxide emissions for the power generation facilities, pellet manufacturing, and pellet combustion. Source of CO2 Emission Emissions (kton/yr) DG Fairhaven 200 Humboldt Sawmill Company 218 Combined Power Generation 419 Pellet Manufacturing 77 Combustion of Pellets 666 A sensitivity analysis was performed on several economic inputs to determine the effect on the payback period for the facility. The operation costs, transportation costs, and capital costs of the facility all had a significant effect on the payback period, but the most significant change was caused by reducing the sale price of the finished pellets. A 35% reduction in the pellet price results in more than a 1000% increase in the payback period, and a reduction of more than 40% in price results in a negative yearly net profit. Sensitivity was also performed on the amount of pellets sold annually, which had a slightly weaker effect on the payback period, and is compared to the pellet sale price in Figure3. iv Team Jamo, May 22, 2020 Fig. 3. Sensitivity Analysis of sale price of pellets and amount sold. Further feasibility studies would be required to implement the preferred alternative. Topics of future research would investigate overseas or domestic bulk pellet customers, particularly in states and countries with favorable carbon credit programs. Additionally, rigorous testing would need to be performed to optimize the pelletizing process with the specific biomass material available. More intensive economic analysis is also needed for accurate long-term planning, including feedstock pricing and availability projections, as well as demand and price sensitivity analysis. v Team Jamo, May 22, 2020 Contents 1 Introduction1 2 Objective Statement1 3 Background2 3.1 Overview of Client and Project............................2 3.2 Biomass as a Resource................................2 3.3 History of Biomass Production, Use, and Disposal in Humboldt County......4 3.4 Potential Biomass Technologies and Uses......................5 3.4.1 Biomass Conversion to Energy........................6 3.4.2 Composting.................................. 10 3.4.3 Consumer Products.............................. 11 3.4.4 Restoration Ecology............................. 14 3.4.5 Mycoremediation............................... 15 3.5 Regulations and Permitting.............................. 17 4 Constraints & Criteria 19 4.1 Constraints...................................... 19 4.2 Criteria........................................ 20 4.2.1 Economic................................... 20 4.2.2 Environmental................................ 21 4.2.3 Technical................................... 21 4.2.4 Social..................................... 22 5 Alternatives 22 5.1 Particleboard Production............................... 22 5.1.1 Inputs and Outputs.............................. 23 5.1.2 Primary Processes.............................. 23 vi Team Jamo, May 22, 2020 5.1.3 Proposed Scale................................ 24 5.1.4 Relation to Constraints and Criteria..................... 24 5.2 Wood Pellet Manufacturing.............................. 26 5.2.1 Inputs/Outputs and Process.......................... 26 5.2.2 Proposed Scale................................ 28 5.2.3 Relation to Constraints and Criteria..................... 28 5.3 Thermal Gasification................................. 30 5.3.1 Inputs and Outputs.............................. 30 5.3.2 Primary Processes and Reactions...................... 31 5.3.3 Proposed Scale................................ 32 5.3.4 Relation to Criteria and Constraint...................... 33 5.4 Composting Facility.................................. 34 5.4.1 Inputs/Outputs and Processes........................ 34 5.4.2 Proposed Scale................................ 35 5.4.3 Relation to Constraints and Criteria..................... 35 6 Alternative Analysis 38 6.1 Particleboard Production............................... 39 6.1.1 Economic Criteria.............................. 39 6.1.2 Environmental Criteria............................ 40 6.1.3 Technical Criteria............................... 41 6.1.4 Social Criteria................................ 42 6.2 Wood Pellet Manufacturing.............................. 42 6.2.1 Economic Criteria.............................
Details
-
File Typepdf
-
Upload Time-
-
Content LanguagesEnglish
-
Upload UserAnonymous/Not logged-in
-
File Pages122 Page
-
File Size-