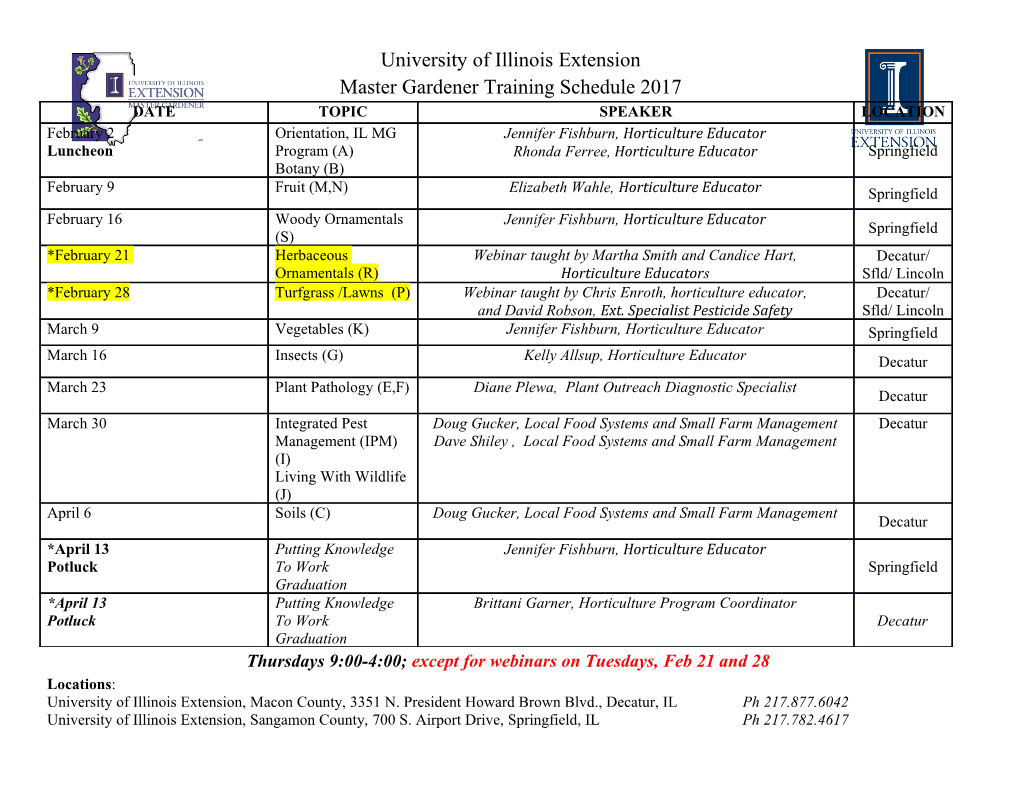
WIRELESS AND BATTERYLESS SURFACE ACOUSTIC WAVE SENSORS FOR HIGH TEMPERATURE ENVIRONMENTS T. Aubert1, O. Elmazria1,2, M.B. Assouar1 1Institut Jean Lamour (IJL), UMR 7198 CNRS-Nancy University 54506 Vandoeuvre lès Nancy, France 2Ecole Supérieur des Sciences et Techniques d’Ingénieurs de Nancy, 54506 Vandœuvre-lès-Nancy, France e-mail : [email protected] Abstract I. INTRODUCTION Surface acoustic wave (SAW) devices are Surface acoustic wave (SAW) devices are used for widely used as filter, resonator or delay line in several years as components for signal processing in electronic systems in a wide range of applications: communication systems. SAW devices are for mobile communication, TVs, radar, stable resonator example widely used as bandpass filter and resonator for clock generation, etc. The resonance frequency and in mobile phones [1,2]. Far from being confined to the delay line of SAW devices are depending on the properties of materials forming the device and could be this single use, SAW are or may find applications in very sensitive to the physical parameters of the many other areas. The SAW can be used to generate environment. Since SAW devices are more and more movement in microfluidics leading to mixe move, and used as sensor for a large variety of area: gas, pressure, heat very low quantities of liquid in the range of force, temperature, strain, radiation, etc. The sensors nanoliter [3]. They can also be used in chemistry, based SAW present the advantage to be passive where some properties of the SAW in terms of (batteryless) and/or wireless. These interesting heterogeneous catalysis could be identified. properties combined with a small size, a low cost radio Applications in the cleaning and decontamination request system and a small antennas when operating at surface (desorption controlled ejection of drops, dust high frequency, offer new and exiting perspectives for and fragments of coatings ...) are also possible. wireless measurement processes and IDTAG applications. When the materials constituting the Finally, SAW offer very interesting prospects in the devices are properly selected, it becomes possible to use field of sensors. It is indeed quite possible to achieve those sensors without embedded electronic in hostile with these devices small size and very robust sensors environments (as high temperature, nuclear site, …) for deformation [4,5], temperature and gas [6,7]. Also where no solutions are currently used. General note that in addition to being small, simple and principle of the SAW sensor in wired and wireless robust, these devices have the advantage of being configurations will be developed and a review of recent passive (batteryless) and remotely requestable works concerning the field of high temperature (wireless) [8,9] and are inexpensive if fabricated on a applications will be presented with specific attention large scale. given to the choice of materials constituting the SAW The use of SAW devices as passive and wireless device. sensors allows them to operate in extreme conditions Key words: such as those with high levels of radiation, high SAW sensors, Wireless, High temperature, LGS, AlN temperatures, or electromagnetic interference, in which no other sensors can operate. This is obviously conditioned by the fact that the materials constituting the device permit. In this paper we focus our interest on SAW sensor for high temperature environment by given a review of main works performed in this field. disturbance resulting in a variation of the electrical The study will be started by explaining the operating response of the device (frequency, amplitude ...). principle of SAW sensor and particularly the wireless SAW systems are no exception to this rule and are SAW sensors. Note that the SAW sensors capable of sensitive to three major types of disturbances: the operating in high-temperature environments will find change in temperature, deformation and in gaseous, applications in aerospace, power, nuclear, steel liquid or solid species deposited on acoustic wave industry, automotive, chemical, and petrochemical travel surface. The change in temperature and processes plants [10,14]. deformation induces an effect on both a variation of speed (alteration coefficients elastic and piezoelectric) II. SAW SENSOR PRINCIPLE and a change of length to cross. The gas species deposition (adsorption/ The SAW devices bring into use the electro- absorption) varies the speed of waves. This variation acoustic properties of piezoelectric substrates such as may result from a change of inertia mechanical quartz, lithium niobate, zinc oxide, to generate surface (increase in a move masse), a modification of surface acoustic waves. The mechanical vibrations elastic coefficients (resulting from the spread of generated propagate at velocity depending on the chemical species adsorbed in the propagation media) crystalographic direction of material and its elastic, or a disruption of the electric field surface. In the case piezoelectric and dielectric constants [1,2]. of the liquid or solid species their deposition affect The generation of acoustic wave is done with two and modify mode of wave propagation. Adding a electrodes, also called Interdigital transducers (IDT). layer of liquid or viscoelastic film on the surface may The IDT consist on a structure of overlapping metal cause the emergence of guided modes at frequencies. fingers that is fabricated on the piezoelectric substrate The velocity of these modes depends on the physical by a photolithographic process (Fig. 1). When an parameters of the guide layer and it is therefore alternative voltage is applied to the IDT input, it possible to measure them by monitoring the evolution follows alternating cuts and horizontal and vertical of the frequency response of the devices. These expansion of underlying material, which can generate parameters are the viscosity, density, stiffness, surface acoustic waves. Different propagation modes thickness, etc. can be generated, in this case and the commonly used All SAW sensors on the market operate one or a is the Rayleigh wave that is similar to waves that combination of these three sensitivities. spread on the surface of the material. III. WIRLESS SENSOR PRINCIPLE Output IDT Two principles could be considered to use SAW Imput IDT devices as wireless sensor, delay lines or resonators. Both principles are described below: III-1 Delay line The operating principle of such a sensor system is sketched in figure 2. The reader unit (local radar transceiver) sends out a radio frequency (RF) electromagnetic read-out signal. This read-out signal Acoustic is picked up by the antenna of the passive SAW wave transponder and conducted to an IDT. The IDT Figure 1: Optcal Photograph of SAW device (Aluuminum converts the received signal into a SAW signal by the IDT on Quartz substrate. In insert, a scanning electron converse piezoelectric effect. The SAW propagates micrograph shows a zoom of the IDTs. towards several reflectors distributed in a characteristic pattern. A small part of the wave is The acoustic wave devices are sensitive to any reflected at each reflector. The micro acoustic wave disturbance that may affect the velocity, distance packets now returning to the IDT are re-converted travel or even the mode of wave propagation. A into electrical signals by the IDT and retransmitted to the radar [10]. Radio IDT Reflected SAW waves Reader Unit Reflector Antenna s Figure 2: SAW wirless sensor in delay line configuration. Same principle is used when SAW device is considered as RFID Tag. The mesurand (temperature, pressure, strain, …) signal is switched off, energy still is present in the affects the velocity of the micro acoustic wave and form of the SAW. The IDT converts a portion of the thereby also the time distances of the RF transponder mechanical energy back to electrical energy now response. The evaluation of this response signal in the because the process of energy conversion is partially radar unit thus allows the determination of the reversible. The electrical energy is transmitted as an environmental temperature or pressure of the passive electromagnetic wave back to the interrogation unit SAW transponder. and can be analyzed. Typical response obtained at the input of interrogation unit is shown in figure 4. III-2 Resonator The technological advances in the field of SAW have allowed the achievement resonator with a Reflector 2 IDT Reflector 1 high quality factor (Q) which allows design sensor based SAW resonator (SAWR) with high sensitivity, accuracy, long-term stability and the possibility of storing electromagnetic energy, A SAW resonator consists of the piezoelectric substrate, an interdigital transducer (IDT), and two reflectors in the direction of the propagating wave (Fig. 3). The IDT is connected to an antenna. It receives energy for the excitation of the SAW by an electromagnetic wave coming from the interrogation unit. The IDT converts electrical energy to Figure 3: One port SAW resonator architecture mechanical energy of the surface acoustic wave. The two reflector gratings form a resonating cavity in which a standing wave is generated in the case of resonance. Duration of oscillations is of course depending on A portion of the stimulating electromagnetic energy is quality factor of the resonator. Resonance frequency stored in this standing wave. After the stimulating of the sensor, directly linked to the mesurand, could be extracted from this signal using Fourrier semiconductor application. Antenna should
Details
-
File Typepdf
-
Upload Time-
-
Content LanguagesEnglish
-
Upload UserAnonymous/Not logged-in
-
File Pages11 Page
-
File Size-