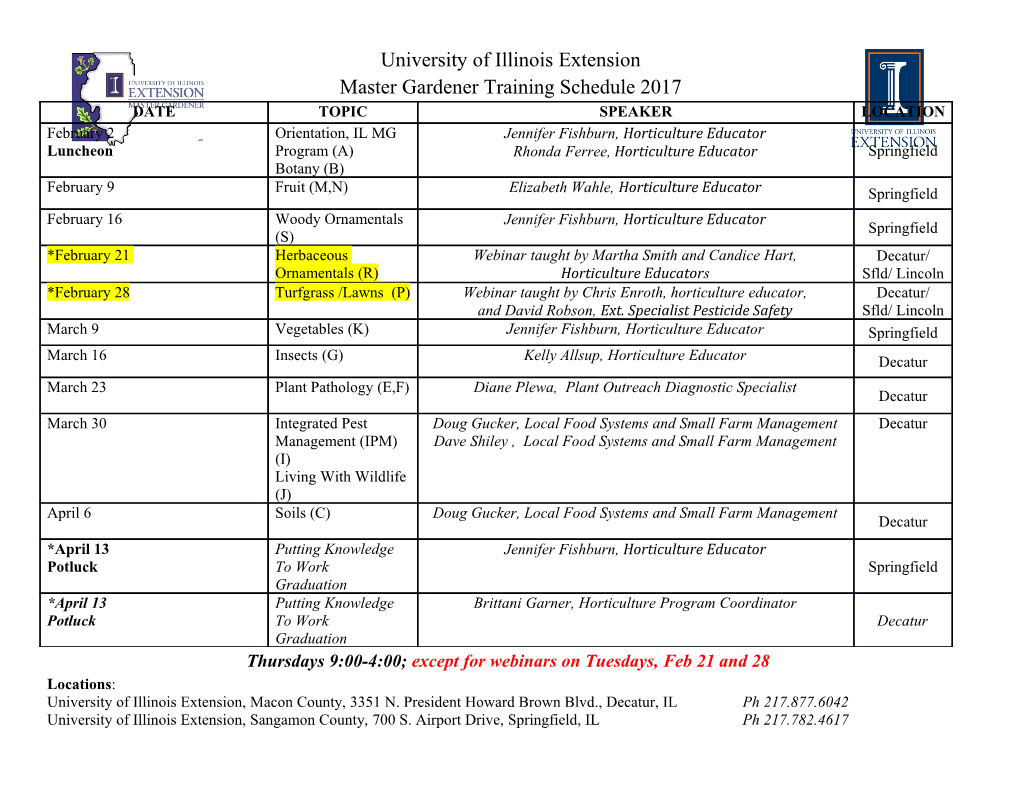
Chapter 2 General Aspects of Carbonylation Catalysis 2.1 Introduction: A chance observation by Ludwig Mond in 1884 led to an important advance in the nickel refining industry. When he found his nickel valves were being eaten away by CO, he deliberately heated Ni powder in a stream of CO to form a volatile compound, Ni(CO)4, the first known metal carbonyl. The Mond refining process was based on the fact that the carbonyl can be decomposed to give pure nickel by further heating, see Figure 2.1. Lord Kelvin was so impressed by this result that he remarked that Mond ‘gave wings to nickel’. OC CO ∆ ∆ Ni + 4CO Ni Ni + 4CO Ore OC CO Pure Figure 2.1 Mond process to refine nickel ore. The development of organometallic chemistry has over the past years gained impetus, arising from the ability of transition metals to catalyse various kinds of organic transformations1. Since 1938 when Otto Roelen discovered the oxo synthesis2,3, work in the area of homogeneous catalysis has increased greatly due in part to work done by Adkins and Krsek4, Storch et al.5, Berty and Marko6 and Natta7. 1 B. Douglas, D.H. McDaniel, J.J. Alexander, “Concepts and Models of Inorganic Chemistry”, 2nd Ed., John Wiley & Sons, New York, 1983. 2 O. Roelen, ChED Chem. Exp. Didakt., 3, 1977, 119. 3 (a) B. Cornils, W.A. Herrmann, M. Rasch, Angew. Chem., 106, 1994, 2219. (b) B. Cornils, W.A. Herrmann, M. Rasch, Angew. Chem., Int. Ed. Engl., 33, 1994, 2144. 4 H. Adkins, G. Krsek, J. Am. Chem. Soc., 70, 1948, 383. 5 H.H. Storch, N. Golumbic, R.B. Anderson, “The Fischer-Tropsch and Related Syntheses”, Wiley Chapman and Hill, New York, London, 1951. Chapter 2 General Aspects of Carbonylation Catalysis Acetic acid is an important industrial commodity chemical, with a world wide demand of about 7 million tons per year and many industrial uses8. Originally, acetic acid was produced by aerobic fermentation of ethanol, which is still the major process for the production of vinegar. The first major commercial process for the production of synthetic acetic acid was based on the oxidation of acetaldehyde, followed by oxidation of butane or naphtha. Novel acetic acid processes and catalysts have been introduced, commercialized, and improved continuously since the 1950s. The objective of the development of new acetic acid processes has been to reduce raw material consumption, energy requirements, and investment costs. Significant cost advantages resulted from the use of carbon monoxide (derived from natural gas) and of low-priced methanol (from synthesis gas) as feedstocks. At present, industrial processes for the production of acetic acid are dominated by methanol carbonylation. The carbonylation of methanol is catalyzed by Group VIII transition metal complexes, especially by rhodium, iridium, cobalt, and nickel9. All methanol carbonylation processes need iodine compounds as essential co-catalysts, the reaction proceeding via methyl iodide, which alkylates the transition metal involved. Apart from acetic acid, the carbonylation of methanol (Eq. 2.1) also gives rise to the formation of methyl acetate, according to Eq. 2.2. In some carbonylation processes (Cativa), methyl acetate is also used as a solvent. CH3OH + CO → CH3COOH ...2.1 CH3COOH + CH3OH → CH3COOCH3 + H2O ...2.2 Homogeneous catalysis presents a great opportunity in that, unlike heterogeneous catalysis, there is a far better understanding of the micro process mechanism (catalytic cycle) with the possibility of influencing steric and electronic properties of these molecularly defined catalysts10. It is thus possible to optimise the homogeneous 6 J. Berty, L. Marko, Acta Chim. Acad. Sci. Hung., 3, 1953, 177. 7 G. Natta, Brennst. Chem., 36, 1955, 176. 8 M.J. Howard, M.D. Jones, M.S. Roberts, S.A. Taylor, Catal. Today 18, 1993, 325. 9 (a) R.T. Eby, T.C. Singleton, in: B.E. Leach (Ed.), Applied Industrial Catalysts, vol. 1, Academic Press, 1983, 275; (b) N. von Kutepow, W. Himmele, H. Hohenschutz, Chem. Ing. Technol. 37, 1965, 297. 10 B. Cornils, W.A. Herrmann, “Applied Homogeneous Catalysis with Organometallic Compounds”, VHC Publishers, Weinheim, 1996. 9 Chapter 2 General Aspects of Carbonylation Catalysis catalyst, tailoring it to the specific problem involved by adapting the chemical and structural basis of the catalyst. Discussed in the rest of this chapter is the general application of carbonylation catalysts, with a focus on homogeneous catalytic systems. Since the field of catalysis is so broad only certain areas or systems will be covered that has relevance to the study on hand. 2.2 Carbonylation Systems: 2.2.1 The Cobalt-Based BASF Process: The first methanol-to-acetic acid carbonylation process was commercialized in 1960 by BASF. It used an iodide-promoted cobalt catalyst and required high pressures (600 atm.) as well as temperatures (230 °C), but gave acetic acid in ca. 90 % selectivity. By-products of the catalytic system were methane, acetaldehyde, ethanol and ethers. The active species, HCo(CO)4, is formed according to Eq. 2.3 and 2.4.. 2CoI2 + 2H2O +10CO → Co2 (CO)8 + 4HI + 2CO2 ...2.3 Co2 (CO)8 + H2O + CO → 2HCo(CO)4 + CO2 ...2.4 The hydrido carbonyl cobalt complex, HCo(CO)4, as active species is verified by the observation that small amounts of H2 enhances the catalytic activity of the system. The mechanism of the catalytic reaction proposed is shown in Figure 2.2; the intermediates postulated are, however, not well characterized. The substrate of carbonylation in the cobalt catalytic cycle is methyl iodide11, since uncertainty existed as to the active substrate. 11 D. Forster, M. Singleton, J. Mol. Catal. 17, 1982, 299. 10 Chapter 2 General Aspects of Carbonylation Catalysis HCo(CO)4 I- H2O CH3COI CH3I H2O CH3COCo(CO)4 CH3Co(CO)4 HI CH3COOH CH3OH CH3COCo(CO)3 CO Figure 2.2 BASF catalytic cycle for the synthesis of acetic acid from methanol. Given that the rate of the process depends on the carbon monoxide pressure, high pressures of 600-700 bar are required for good conversion. Slightly lower pressures are possible in the presence of Ru, Ir, Pd, Pt, or Cu salts as activators12,13. Cobalt catalysts can also be used for the carbonylation of higher alcohols, such as benzyl alcohol14. 2.2.2 Nickel-Based Processes: Nickel carbonyl, as well as a variety of nickel compounds, is also catalytically active for the carbonylation of methanol in the presence of iodine. Ni(CO)4 is formed from NiI2 according to Eq. 2.5. NiI2 + H2O + 5CO → Ni(CO)4 + 2HI + CO2 ...2.5 The hydrogen iodide formed in Eq. 2.5 is used to transform the alcohol into an alkyl halide, which adds oxidatively to nickel, as described in Figure 2.315. The resulting acetyl iodide is hydrolyzed either by water or alcohols. 12 K. Nozaki, Chem. Abstr. 81, 1974, 120023d. 13 N. von Kutepow, F.-J. Muller, Chem. Abstr. 81, 1974, 135473z. 14 T. Imamoto, T. Kusomoto, M. Yokoyama, Bull. Chem. Soc. Jpn., 55, 1982, 643. 15 (a) F.E. Paulik, A. Hershman, W.R. Knox, J.F. Roth, Chem. Abstr. 72, 1970, 110807y; (b) J.S. Kanel, S.J. Okrasinski, US Patent to Eastman, 1999, 5900504. 11 Chapter 2 General Aspects of Carbonylation Catalysis OC CO CH I CH3COI 3 Ni OC CO 2CO 2CO OC COCH3 OC CH3 Ni Ni OC I OC I CO Figure 2.3 Catalytic cycle of the nickel-catalyzed methanol carbonylation. Nickel catalysts usually operate under high pressures and temperatures16 but with high methyl iodide concentrations, carbonylation occurs readily under milder conditions17. Molar ratios of CH3I:CH3OH of at least 1:10, pressures as low as 35 bar can be 18 applied at 150 °C, using Ni(OAc)2⋅4H2O and Ph4Sn as catalyst systems . The activity of nickel catalyst systems can be increased, and the volatility of nickel carbonyl compounds can be lowered by the introduction of stabilizers such as phosphines, alkali metals, tin, and molybdenum19,20,21,22. The active catalysts are thought to be Ni(0) complexes. For the phosphine-containing nickel catalysts, 14- electron species such as Ni(PR3)2 are considered as catalysts, in addition to Ni(CO)4 . Although nickel systems can approach the reaction rates and selectivities of rhodium based catalytic systems, and nickel is much cheaper than rhodium, commercialization of these systems has not been achieved to date. This can be attributed to the very toxic and volatile nature of the Ni(CO)4 compound. 16 R.F. Heck, J. Am. Chem. Soc. 85, 1963, 2013. 17 J. Gauthier-Lafaye, R. Perron, European Patent to Rhone-Poulenc, 1981, 35458. 18 H.J. Hagemeyer, Chem. Abstr. 50, 1956, 16835d. 19 K. Fujimoto, T. Shikada, K. Omata, H. Tominaga, Ind. Eng. Chem. Prod. Res. Dev., 21, 1982, 429. 20 N. Ritzkalla, Industrial chemicals via C1 processes, ACS Symposium Series 328, 1987, 61. 21 J.D. Holmes, US Patent to Eastman, 1979, 4133963. 22 (a) W.R. Moser, B.J. Marshik-Guerts, S.J. Okrasinski, J. Mol. Catal. A Chem. 143, 1999, 57; (b) W.R. Moser, B.J. Marshik-Guerts, S.J. Okrasinski, J. Mol. Catal. A Chem. 143, 1999, 71. 12 Chapter 2 General Aspects of Carbonylation Catalysis 2.2.3 The Rhodium-Based Monsanto Process: The Monsanto Acetic Acid process is commercially an important process since it produces 50 % of the annual world acetic acid capacity of 7 million metric tons23. The process involves the homogeneous catalysis in the carbonylation of methanol to yield acetic acid, Figure 2.4. Furthermore, the effect of the rhodium metal centre on the catalytic system is very strong, since the metal centre facilitates both the oxidative addition and reductive elimination steps with ease compared to the cobalt catalyst, see § 2.2.1.
Details
-
File Typepdf
-
Upload Time-
-
Content LanguagesEnglish
-
Upload UserAnonymous/Not logged-in
-
File Pages14 Page
-
File Size-