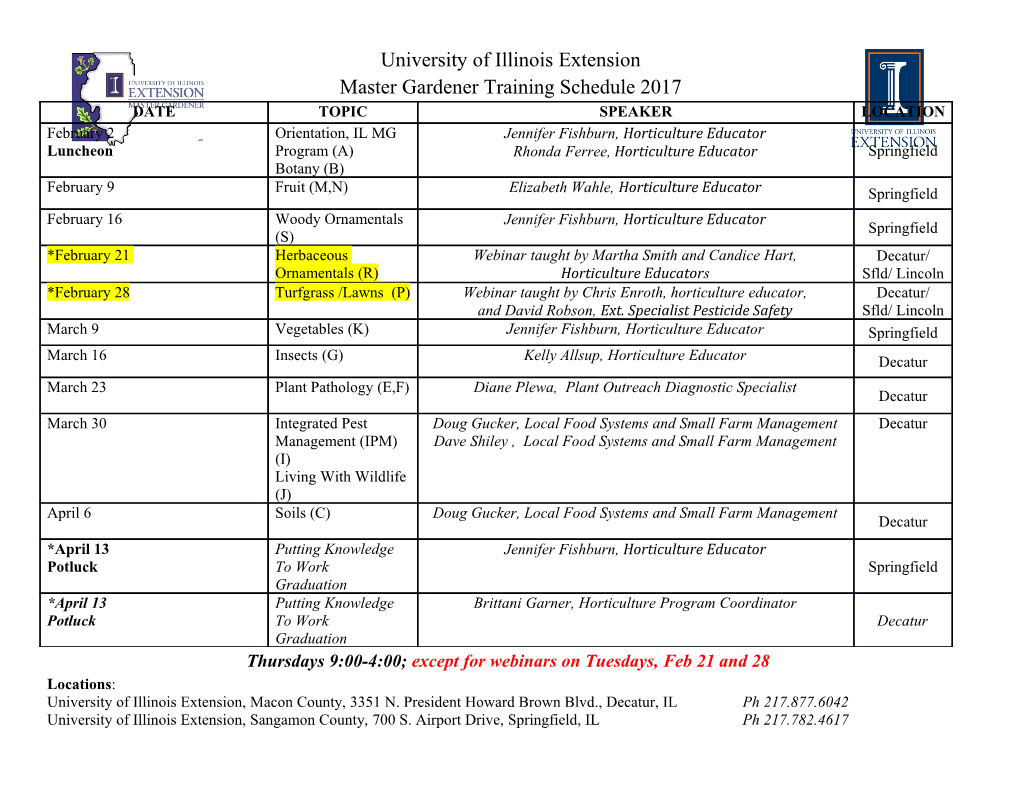
56 Technical Article Waste Heat Recovery for EAF — Innovative Concepts and Industrial Implementation Authors The development of a waste heat recovery plant requires extensive knowledge as well as long A. Fleischanderl experience of the entire plant. Primetals provides waste heat recovery solutions for EAFs, some of technology officer upstream, which are presented in this article. A waste heat recovery plant is introduced, which was installed Primetals Technologies Austria in Italy. Waste heat is used to produce steam for two pickling lines, which are a large distance GmbH, Linz, Austria [email protected] from the EAF. The substitution of the existing gas-fired boilers led to a decisive reduction of operating costs of the steel plant. A heat recovery plant was installed at a steel plant in Sweden, T. Steinparzer where hot water at high pressure is produced and utilized for the local district heating system. head of technology and innovation ECO solutions, Primetals The implementation of waste heat recovery systems for EAFs will be presented in detail, and Technologies Austria GmbH, operational results achieved will be discussed. Linz, Austria [email protected] P. Trunner n recent years, waste heat recov- decreased and the global steel indus- process engineer waste heat ery in the steel industry has try is dealing with overproduction. recovery, Primetals Technologies I Austria GmbH, Linz, Austria attracted more and more attention. Therefore, steel plant operators are [email protected] Environmental regulations, public forced to reduce production costs funding, as well as required revamps and to optimize their steelmaking of old dedusting systems lead steel processes. plant operators to discuss and to Furthermore, due to growing evaluate possibilities of recovering environmental consciousness and waste heat. tightened emission control by The development of a waste heat authorities, environmental technol- recovery plant requires extensive ogies and energy efficiency have knowledge as well as long experi- become more and more in the focus ence of the entire plant, including of steel plant operators. water-steam cycle as well as the elec- Energy is one of the most impor- tric arc furnace (EAF) process and tant cost factors for integrated iron dedusting system. Innovative waste and steel plants as well as for elec- heat recovery solutions are intro- tric steel mills.1 The vast amount duced and discussed in this article. of electric energy in electric steel Another challenge for waste heat plants forces operators to improve recovery at EAF plants is to identify the overall energy situation, in order a possible utilization for the recov- to reduce the specific costs per ton ered energy. Thus, possible applica- of steel and also to comply with legal tions for a heat consumer inside or requirements in terms of energy outside the steel plant are discussed. efficiency. Industrial implementations of There are various opportuni- waste heat recovery plants are pre- ties along the steelmaking route sented to demonstrate economic for implementing energy efficiency and reliable utilization of EAF waste measures. AIST.ORG I heat for different applications. Smaller improvements can be implemented in terms of process optimization. The identification of Introduction improvements requires a survey of the existing installations and elabo- In recent decades, global steel pro- ration of the individual improve- duction has increased continuously, ments in terms of feasibility, reliabil- IRON & STEEL TECHNOLOGY I driven by the big demand of grow- ity, as well as cost-benefit consider- 2018 ing markets and economic expan- ations. Such measures can be done JAN sion. Nowadays, steel demand has with low or moderate effort. 57 Figure 1 Typical measures to reduce energy consumption. However, for a more decisive impact on the energy This means the energy consumption per ton of the balance of a steel plant, bigger actions are required. final steel product is mainly caused by the EAF. By recovering waste heat, a large amount of offgas In Fig. 2, the energy balance of a typical scrap- energy can be utilized within the steel plant, leading based furnace is given. It is shown that about 50% of to a significant reduction of energy costs. The largest the required energy input is provided by electricity via amount of waste heat within electric steel mills can be the electrode. The residual energy is mainly related found at electric arc furnaces, where approximately to exothermic chemical reactions in the steel bath. 30% of the total energy input is emitted in the offgas. Additional energy input is provided by gas burners The economic feasibility of an EAF waste heat recov- in the furnace. Depending on the EAF operation ery solution is mainly driven by the type of waste heat and input materials, approximately 30% of the total utilization. Therefore, the waste heat utilization has energy input is dissipated to the offgas. to be a major focus during project devel- opment. In the following, economically feasible solutions will be presented even though the price of electric energy is low Figure 2 in current markets. JAN 2018 Waste Heat Recovery Solutions I IRON & STEEL TECHNOLOGY Waste Heat Potential of EAF — In most elec- tric steelmaking plants, the EAF is the main metallurgical unit for steelmaking, since it is used for melting and refining of the raw materials. Also, considering I the energy balance of electric steel plants AIST.ORG (mini-mills), the EAF is the biggest energy Energy balance (Sankey diagram) of a scrap-based electric arc furnace consumer along the steelmaking route. (EAF). 58 Technical Article However, EAF offgas does not correspond directly Furthermore, the offgas parameters from EAF off- with the energy input and the charged material in gas are more difficult compared to conventional heat terms of flow, temperature and composition. Sudden recovery boilers. The maximum offgas temperature occurring combustion processes and CO gas produc- exceeds the usual offgas temperature of comparable tion (e.g., combustion of oil from a collapsing scrap boilers of other industries. Also the high dust content bulk) within the furnace do not allow gas recovery in and the specific gas composition have to be consid- terms of downstream CO gas recovery. Thus it is state ered carefully.3 of the art to maintain a large amount of excess air in Apart from the above-mentioned issues, the steel the gap at the entry of the offgas system to ensure a plant situation is crucial for the design of the plant. complete combustion of the offgas during the whole A deep understanding of the plant layout, space melting period of the EAF.2 availability, infrastructure and interfaces is funda- In the offgas system, the offgas is cooled down by mental for the design of a waste heat recovery plant. a water-cooled duct, followed by a second-stage gas Depending on the plant situation, a tailor-made solu- cooler, which can be from a type of evaporation cooler tion has to be developed. or a forced-draft cooler. In this part, most of the An integral waste heat recovery approach is based energy is dissipated to the ambient. Offgas tempera- on a modular system, which is referred to the setup of ture is further decreased by dilution with air from a dedusting system. State-of-the-art dedusting systems, other suction sources before entering the filter plant. as shown in Fig. 4, consist of a water-cooled hot gas Eventually the offgas is emitted via the stack at tem- line followed by a second-stage cooler. After mixing peratures of approximately 100–130°C. This means with dilution air or air from other suction points, the that the remaining energy is emitted to the environ- offgas is cleaned in the filter and discharged via the ment. The energy balance along the offgas system as stack. well as the process flow diagram are shown in Fig. 3. Waste heat can be recovered by replacing the con- ventional water-cooled hot gas line by a heat recovery Waste Heat Recovery Systems for EAF — Even if the duct. In this case, the offgas cooling is done with pres- waste heat potential is high enough, there are several surized water at elevated temperatures. The hot water challenges for designing a waste heat recovery plant. is consequently used for steam or power generation or Due to the dynamic operation of the EAF process, as any other suitable application. well as idle periods of the furnace, the offgas param- Alternatively, the second-stage cooler can be eters are fluctuating intensively. This results in a dis- replaced by a waste heat boiler. Due to lower offgas continuous waste heat supply and thus a discontinu- temperatures, the boiler is from a type of bundle heat ous output. Therefore, heat recovery systems require exchanger to recover the waste energy and for cooling a buffer to equalize the heat supply for downstream of flue gas. Thus offgas is ducted through the boiler at consumers. moderate flow velocities, whereas water and/or steam are flowing inside the tubes. Figure 3 AIST.ORG I IRON & STEEL TECHNOLOGY I 2018 JAN Energy flow along offgas system. 59 Figure 4 EAF dedusting system setup. Depending on the plant situation, as well as on the Figure 5 operator requirements and downstream heat utiliza- tion, a proper waste heat recovery concept will be developed. Thus, either the first stage or the second stage will be incorporated in the heat recovery con- cept. For maximized heat utilization, the first and second stages can be combined. In Fig. 5, the layout of an EAF dedusting system including waste heat recovery system is shown. Offgas coming from the EAF is routed through the heat recovery duct and the second-stage waste heat boiler before entering the filter. It can be seen that the foot- print is similar to conventional dedusting systems.
Details
-
File Typepdf
-
Upload Time-
-
Content LanguagesEnglish
-
Upload UserAnonymous/Not logged-in
-
File Pages7 Page
-
File Size-