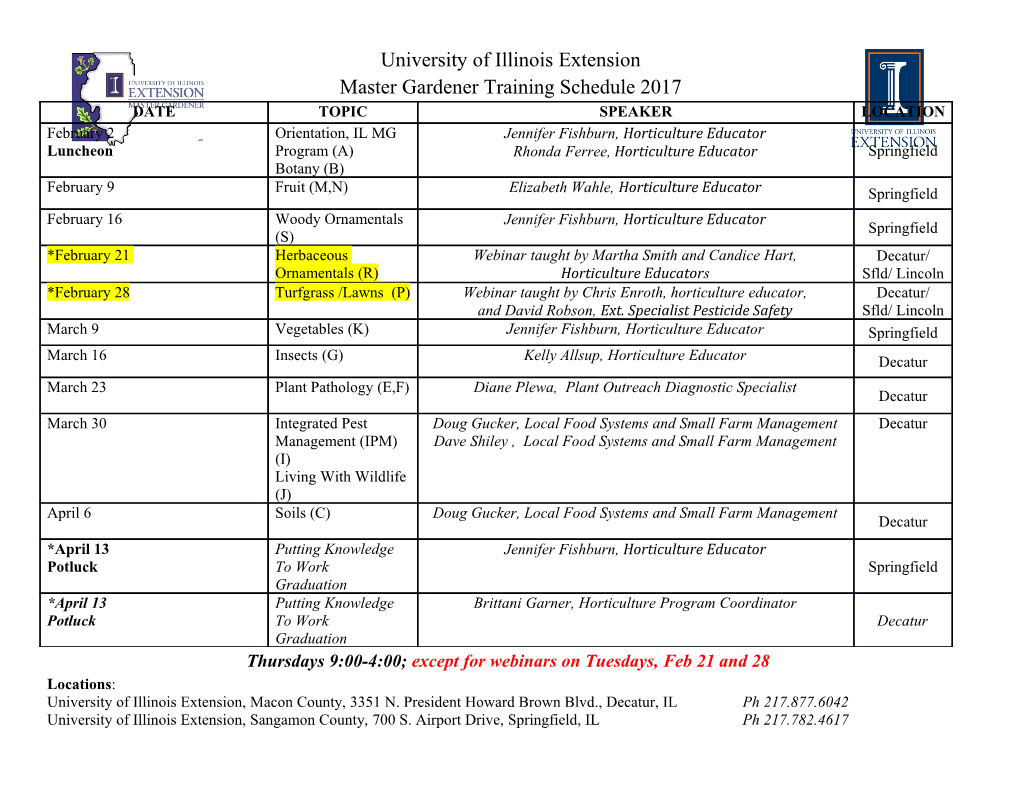
ME477 Fall 2004 NonTraditional Processes (NTP) NONTRADITIONAL • Conventional Machining Processes (cutting, milling, MACHINING AND THERMAL drilling & grinding) use a sharp cutting tool • NTP - A group of processes that remove excess CUTTING PROCESSES material without a sharp cutting tool by various techniques involving mechanical, thermal, electrical, or chemical energy (or combinations) developed since 1. Mechanical Energy Processes World War II (1940’s). 2. Electrochemical Machining Processes • Motivations in Aerospace and Electronics Industries – to machine new (harder, stronger & tougher) materials difficult 3. Thermal Energy Processes or impossible to machine conventionally – for unusual & complex geometries that cannot easily 4. Chemical Machining machined conventionally – to achieve stringent surface (finish & texture) requirements not possible with conventional machining 1 2 Classification 1. Mechanical Energy Processes • Ultrasonic Machining (USM) • Mechanical - Erosion of work material by a high – Abrasives (20-60 volume %) in a slurry are driven High-frequency oscillation velocity stream of abrasives and/or fluid at high velocity by the tool vibrating at low Flow – Ultrasonic machining, Water jet cutting (WJC), Abrasive water amplitude (0.05-0.125mm) and high frequency Flow jet cutting (AWJC) and Abrasive jet machining (AJM) (20kHz). • Electrical - Electrochemical energy to remove material – Tool oscillation is perpendicular to work surface – Electrochemical machining (ECM), Electrochemical deburring – Tool: soft and stainless steels fed slowly into work. (ECD) and Electrochemical grinding (ECG) – Abrasives (Grit size 100 (rough) to 2000(fine)) – BN, BC, Al O , SiC & Diamond • Thermal - Thermal energy applied to small portion of 2 3 – The vibration amplitude equals to grit size, which work surface, removing by fusion and/or vaporization also determines the resulting surface finish. – Electric Discharge Machining (EDM), Wire EDM, Electron – Time of contact: 10-100µs Beam, Laser Beam, Arc Cutting – Shape of tool is formed into a part • Chemical - chemical etchants selectively - using a – Work materials – Hard, brittle materials such as MRR frequency mask - remove a portion of a workpart ceramics, glass and carbides and stainless steel – Chemical Milling, Blanking, Engraving and Photochemical and titanium Amplitude Machining – Shapes include non-round holes (holes along a curved axis) and “Coining operations” (the pattern 3 on tool is imparted to a flat work surface). 4 Water Jets Water and Abrasive Jets • Water Jet Cutting (WJC) or Hydrodynamic machining – • Abrasive Water Jet Cutting (AWJC) – Use of abrasive particles (grid sizes between 60 and 120) into the jet use a fine, high-pressure and high velocity stream of stream water. – Process parameters: abrasive type, grit size, & flow rate – A small nozzle (made of sapphire, ruby or diamond) opening of – Other parameters: Nozzle office diameter(0.25 to 0.63 mm) diameter (0.1 to 0.4 mm) – Abrasives: aluminum oxide, silicon dioxide & garnet. – Pressure up to 400MPa and velocity up to 900m/s. – Standoff distance is ½ and ¼ of those of WJC. – A typical standoff distance is 3.2mm. • Abrasive Jet Machining (AJM) – Feed rates between 5mm/s to 500mm/s depending on material – Usually finishing process (deburring, polishing, cleaning) not cutting and thickness – Grid size between 15 and 40 µm – CNC or industrial robots to cut along desired trajectory – Usually performed manually by operator who directs nozzle – Used to cut narrow slits in flat stock such as plastic, textiles, – Normally used as a finishing process rather than cutting process composites, floor tile, carpet, leather, and cardboard – Use for deburring, trimming & deflashing, cleaning, and polishing – Not suitable for brittle materials (e.g., glass) – Work materials: thin flat stock of hard, brittle materials – Advantages: no crushing or burning of work surface, minimum material loss, no environmental pollution, and ease of automation Standoff distance 5 6 Kwon 1 ME477 Fall 2004 2. Electrochemical Machining Electrochemical Machining (ECM) Processes • Material is deplated from anode workpiece (positive pole) and transported to a Cathode • Electrical energy in combination with chemical reactions cathode tool (negative pole) in an to remove material - Work material must be a conductor electrolyte bath • Reverse of electroplating • Electrolyte flows rapidly between the two – Part is the anode (+) and the tool is the cathode (-) poles to carry off deplated material, so it – Metal is “pulled” away from work does not plate onto tool • Advantage • Electrode materials: Cu, brass, or stainless – Hard to soft materials made of conductive material can be steel Tool feed Electrolyte flow machined • Tool has inverse shape of part – Cutting tool can be made from soft material – Tool size and shape must allow for the gap – Low heat generated during process – No cutting forces • No surface damage, no burr, low tool wear, high removal rate for hard-to- -- – Excellent surface finish machine materials + • Processes: – Electrochemical machining (ECM) – Electrochemical deburring (ECD) 7 8 – Electrochemical grinding (ECG) Process Physics Electrochemical Machining gr g= gap IN ECM, Resistance: R = • ElectroChemical Machining (ECM) A r = resistivity of electrolyte – Gap distance needed to be controlled without touching. E EA Current: I = = A=surface area between work & tool – Water with salts is used as electrolyte R gr V = Volume of metal removed; • Remove debris, heat and hydrogen bubbles CEAt Faraday's First Law: V = CIt = C = specific removal rate depending on – Disadvantages gr work material (mm3/amp-s); • Disposal of the electrolyte V CE • Large amounts of electric power required = f = t = time (s) – Advantages: At r gr E=voltage • Used on very hard or difficult to machine CI • Die sinking, multiple holes, irregular holes and deburring Feed rate: fr = η = the current efficiency (0.9-1) A • ElectroChemical Deburring (ECD) Work material C(mm3/amp-sec) Material Removal Rate: MRR = CIη Al 3.44x10-2 – Adaptation of ECM to remove burrs and round sharp corners Cu 7.35x10-2 Fe 3.67x10-2 - Steel 3-2.5x10-2 -2 + Ni 3.42x10 9 10 Ti 2.73x10-2 Electrochemical Grinding (ECG) 3. Thermal Energy Processes Very high local temperatures remove material by Special form of ECM in which a grinding wheel with conductive bond material is used to augment anodic fusion or vaporization. Physical and metallurgical dissolution of metal part surface damage to the new work surface • Applications: • Electric Discharge Processes – Sharpening of cemented carbide tools – Surgical needles, other thin wall tubes, and fragile parts – Electric Discharge Machining (EDM) • Advantages: •Wire EDM – Deplating removes 95%, and abrasives remaining 5% of metal – Electron Beam Machining removal - grinding wheel lasts much longer (much higher • Laser Beam Machining grinding ratio, less frequent dressing) • Arc Cutting Processes - – Plasma Arc Cutting – Air Carbon Arc Cutting + – Other Arc Cutting Processes • Oxyfuel Cutting Processes 11 12 Kwon 2 ME477 Fall 2004 Electric Discharge Machining (EDM) Work Materials and Applications • Most widely used among nontraditional processes • Sparks (lightening: 500 - 5,000 sparks per second) across a small • Tooling for many mechanical gap between tool and work to remove material, thus slow (MRR= 1 •Only electrically processes: molds for plastic in3 to 15 in3 per hr.) conducting work injection molding, extrusion materials • Electrode (made of Brass, Copper and Graphite) is (+) and the part dies, wire drawing dies, is (-) • Hardness and • Requires dielectric fluid, which creates a path for each discharge as forging and heading dies, and strength of the work fluid becomes ionized in the gap sheetmetal stamping dies • Dielectric fluids: hydrogen oil, kerosene and water material are not factors in EDM • Production parts: delicate KI Tool parts not rigid enough to Dielectric fluid MRR = 1.23 • Material removal rate Electrode Tm is related to melting withstand conventional cutting where K = 39.86in SI units point of work material forces, hole drilling where rough frequency hole axis is at an acute angle Low frequency Current to surface, and machining of High frequency hard and exotic metals Overcut Surface finish Surface smooth 13 14 Discharge current Current/ frequency overcut Wire EDM Operations and Applications • A special form of EDM that uses small diameter wire as electrode to cut a • Work is fed slowly past wire along • Ideal for stamping die narrow kerf in work desired cutting path, like a components • Wire diameter range from 0.076 to bandsaw operation – Since kerf is so 0.3mm kef • CNC used for motion control narrow, it is often possible to fabricate • Overcut in a range of 0.02 to 0.051mm • While cutting, wire is continuously punch and die in a advanced between supply spool single cut and take-up spool to maintain a • Other tools and parts constant diameter with intricate outline • Dielectric required, using nozzles shapes, such as lathe directed at tool-work interface or form tools, extrusion submerging workpart dies, and flat templates 15 16 From Schey [ Thermal Energy Processes Laser and Its Applications • Electron Beam Machining High-voltage Light amplification by stimulated emission of – Uses a high-velocity stream of cable radiation electrons capable to remove any material • A laser converts electrical energy into a – EB gun accelerates a continuous stream of electrons to about 75% of light speed. highly coherent light beam with
Details
-
File Typepdf
-
Upload Time-
-
Content LanguagesEnglish
-
Upload UserAnonymous/Not logged-in
-
File Pages6 Page
-
File Size-