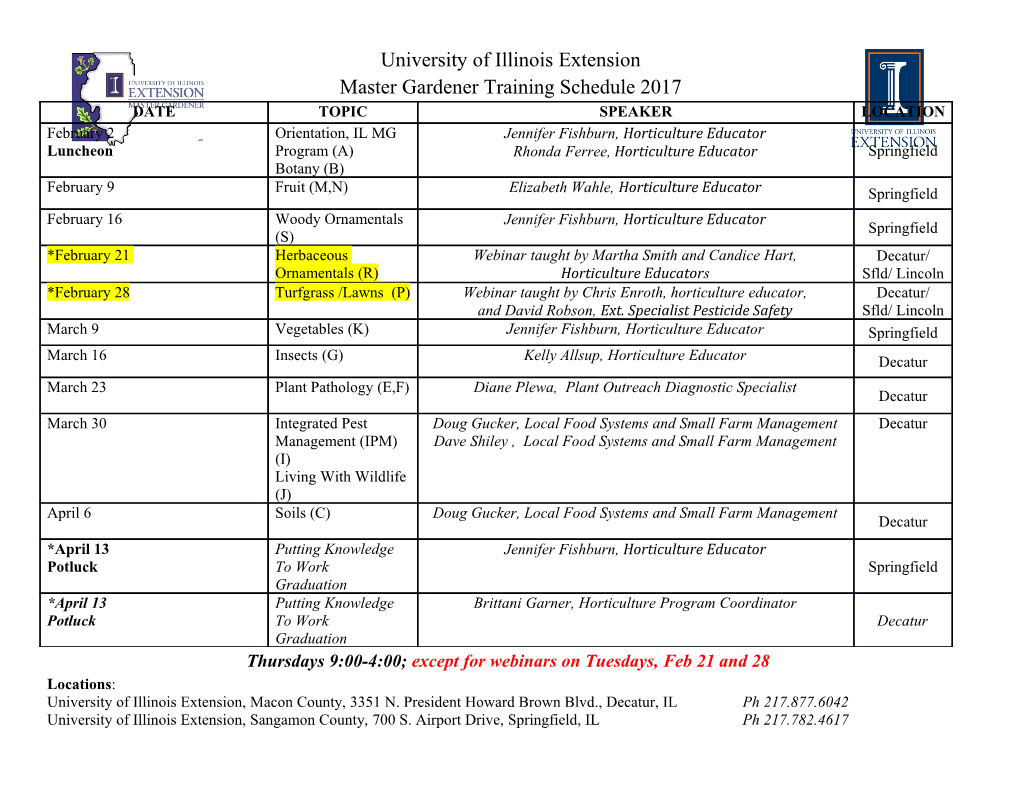
SepI- 13, I966 D F. HERMAN ETAL. 3,272,897 METHOD OF MAKING POLYMER COATED SUBSTANCES AND MOLDING THEM INTO AN ARTICLE Filed Nov. 1, 1962 ABSORBENT SUBSTRATE PARTICLES I FIRST DISPERSING THE SECOND REACTANT SUBSTRATE PARTICLES REACTANT SOLUBLE AT THE INTERFACES SOLUBLE IN FIRST FORMED BY INTER- IN SECOND SOLVENT MINGLING THE FIRST SOLVENT/AND SOLVENT CONTAINING REACTIVE THE FIRST REACTANT WITH FIRST AND THE SECOND REACTANT SOLVENT CONTAINING TO FORM THE SECOND REACTANT POLYMER AND REACTING THE FIRST FIRST AND SECOND SECOND SOLVENT REACTANTS TO FORM SOLVENT POLYMER IMMISCIBLE WITH FIRST SOLVENT SUBSTRATE PARTICLES INDIVIDUALLY ENCAPSULAT ED WITH POLYMER 3,272,897 United States Patent 0 'ice Patented Sept. 13, I966 1 2 Another object of the present invention is to provide 3,272,897 a process for encapsulating particulate substrates with METHOD OF MAKING POLYMER COATED SUB more than equal amounts, by weight of substrates, of STANCES AND MOLDING THEM INTO AN polyfunctional condensation polymers, such as poly ARTICLE amides, polyesters, polysulfonamides, polyurethanes and Daniel F. Herman, Princeton, N.J., and Albert L. Resnick, Jericho, N.Y., assignors to National Lead Company, polyphthalamides, including polyterephthalamides. New York, N.Y., a corporation of New Jersey Other objects will be apparent to those skilled in the Filed Nov. 1, 1962, Ser. No. 234,845 art from reading the following description taken in con 20 Claims. (Cl. 264-109) junction with the accompanying drawing in which the 10 single ?gure is a ?ow sheet embodying the process steps This invention relates to a process for polymerizing of the invention. materials directly onto the surfaces of absorbent sub The objects are accomplished by treating an absorbent strates, and to processes for forming useful articles from substrate material with a ?rst solvent containing dissolved the resultant products. therein a ?rst reactant capable of undergoing polyfunc More particularly, this invention is concerned with 15 tional condensation polymerization with a second re‘ a simple, inexpensive process for forming polymers such actant, and dispersing the treated substrate material in as polyamides, polyurethanes, polyphenyl esters, poly a second solvent which is immiscible in the ?rst solvent, sulifonam-ides, polyphthalamides, including polytereph thus forming a large number of discrete interfaces be thalamides, or the like, directly on absorbent substrate tween the two dispersed immiscible solvents on the sub particles or ?bers, such as carbon black, glass, silica, 20 strate. A second reactant soluble in the second solvent rayon, cellulose, wool, asbestos, and the like. Each in is added to the resultant mixture and is capable of un dividual substrate particle or ?ber is substantially en dergoing at each of the interfaces a polyfunctional con cased in a shell of the polymer that is chemically or densation polymerization with the ?rst reactant dissolved physically bonded thereto. in the ?rst solvent. The polymer thus formed is a?ixed Frequently, it is desired to impart plastic properties 25 into and on the substrate material due to the ?rst re to a non-plastic material, or to supplement the properties actant being retained in the substrate material. That is, of plastic materials. The result is accomplished by me the ?rst solution permeates the substrate material. Thus, chanically mixing the two materials to uniformly dis the ?rst reactant in the ?rst solution is ‘available in the perse one in the other. The procedure involves commi substrate material and reacts therein with the second nuting each of the starting materials, thoroughly mixing 30 reactant. Polymer is accordingly formed inside the sub. them, and then recombining them into a uni?ed product strate material and conforming to the voids of the sub by heat, pressure, etc. The products thus formed are strate material becomes ‘anchored thereto. As an alter frequently defective because of non-uniformity due to nate, the process may be carried out in two steps. In incomplete mixing of the materials. the two step process the second solvent contains the Likewise, many procedures have been proposed hereto 35 second reactant dissolved in it, thus eliminating the third fore for coating, impregnating, or otherwise treating step of dissolving the second reactant after dispersing wool, asbestos and cellulosic products, such as wood, the treated substrate material in the second solvent. paper, and various textiles to improve their water resist An essential feature of the invention includes the use ance, ?ame resistance, chemical resistance, physical prop of discrete particles or ?bers as a substrate material. erties, etc. For example, various kinds of wood, paper, 40 Each particle individually acts as -a polymerization site cloth and the like, have been impregnated 'with many and maintains its individuality throughout the process, different oils, waxes or resins to make the materials more thus resulting in a particulate free-?owing product. nearly waterproof. Such impregnated products have In the process of this invention, the interface of two disadvantages inherent in their method of manufacture. immiscible liquids is made to coincide with the outer In many cases, as with waxed paper, the impregnating 45 surface of a substrate particle. This is accomplished‘by material is essentially removed by heat, solvents, or the adding to the particle an amount of one of the liquids like. In other cases, the impregnated paper, wood, or which it can retain. Upon dispersing the substrate par cloth frequently is made brittle and is not able to With ticle in the other immiscible liquid, the interface is co stand ?exing without having the impregnant crack or extensive with the surface of the substrate particle. peel. 50 The substrate materials intended for use in the process Some ‘fabrics have been lightly plastic coated to water of the invention must be capable of retaining in voids, or proof them. For instance, wool has been nylon coated on their surfaces, or both, an amount of solvent contain by passing the ‘fabric through a ?rst dipping solution of ing one of the reactants. The amount of solvent re hexamethylenediarnine ‘and then through a second dip 55 tained is one of the determining factors in controlling ping solution of seb‘acoyl chloride. The cloth was then the amount of polymer formed on the substrate material. passed through a set of rollers, or padders, which aid in Other factors include the concentration of the reactants. placing the reacted material in and on the ‘fabric. Coat The more reactant retained the greater the amount of ings applied in this manner have been limited to 2% polymer that will be formed on the substrate material. by weight or less of the weight of the cloth. 60 However, if excess solvent is added free polymer will impregnation or coating, whether carried out by spray be formed that is not attached to the substrate material. ing, dipping, or other techniques, can be di?icult and The amount of the solvent which is desired to be re costly to perform because solvents which ‘are usually re tained is that amount of solvent which, when added to quired must be evaporated, or otherwise removed, after the free-?owing substrate material, just causes it to the impregnation. The impregnant is frequently non become non-free-?owing. The desired amount of solvent 65 uniformly distributed through the product. Much of the thus added, when saturated with the ?rst reactant, de impregnant is wasted by more or less ?lling all of the po termines the maximum amount of polymer which may rous spaces and other interstices in the base material. be formed ‘on the substrate material. The substrate ma One of the objects of this invention is to provide a terials must be non-reactive with the reactants, solvents, process whereby small particles of material may be easily 70 etc. and inexpensively encased individually in shells of a The desired amount of solvent may be determined by chemical condensation product af?xed to the particles. ascertaining the water absorbence of the substrate. Water 3,272,897 3 absorbence of substrates may be determined by adding terfacial condensation reaction, at least one of which is water from a burette to a weighed quantity of substrate, soluble in a ?rst solvent and another of which is soluble while stirring. The maximum absorbence may be taken in a second solvent, said second solvent being immiscible as that amount of water required to make the substrate with said ?rst solvent, may be used in the practice of this into essentially a single, coherent mass, which will start invention. to exude water when pressed lightly against the contain Any two solvents may be utilized which are mutually ing vessel. This test may be considered only roughly immiscible and which do not react with each other, with quantitative, since it may be dif?cult to uniformly wet the substrates, or with the reactants, and do not dissolve any given substrate. Typical results are shown in Table the polymer formed. A preferred solvent system consists I. Table I shows the maximum amount of water which of water and an organic solvent, such as benzene, toluene can be added to the substrate material before the sub or carbon tetrachloride. However, two non-aqueous sol strate material becomes non-free-?owing. The minimum vents, such as methanol and heptane, may be utilized to amount of water is the least amount of water that can provide a solvent system. Where the solvent system char be added to the substrate material. acteristics are described herein as a water-organic sys TABLE I.—ABSORPTION OF VgRTER BY VARIOUS 15 tem, it is to be understood that any other suitable sol SUB STRATE vent system may be substituted therefor. There is no upper limit on the ratio of the organic . Water Approxi Substrate Material ‘it Added mate Rat-i0 to the aqueous solution.
Details
-
File Typepdf
-
Upload Time-
-
Content LanguagesEnglish
-
Upload UserAnonymous/Not logged-in
-
File Pages11 Page
-
File Size-