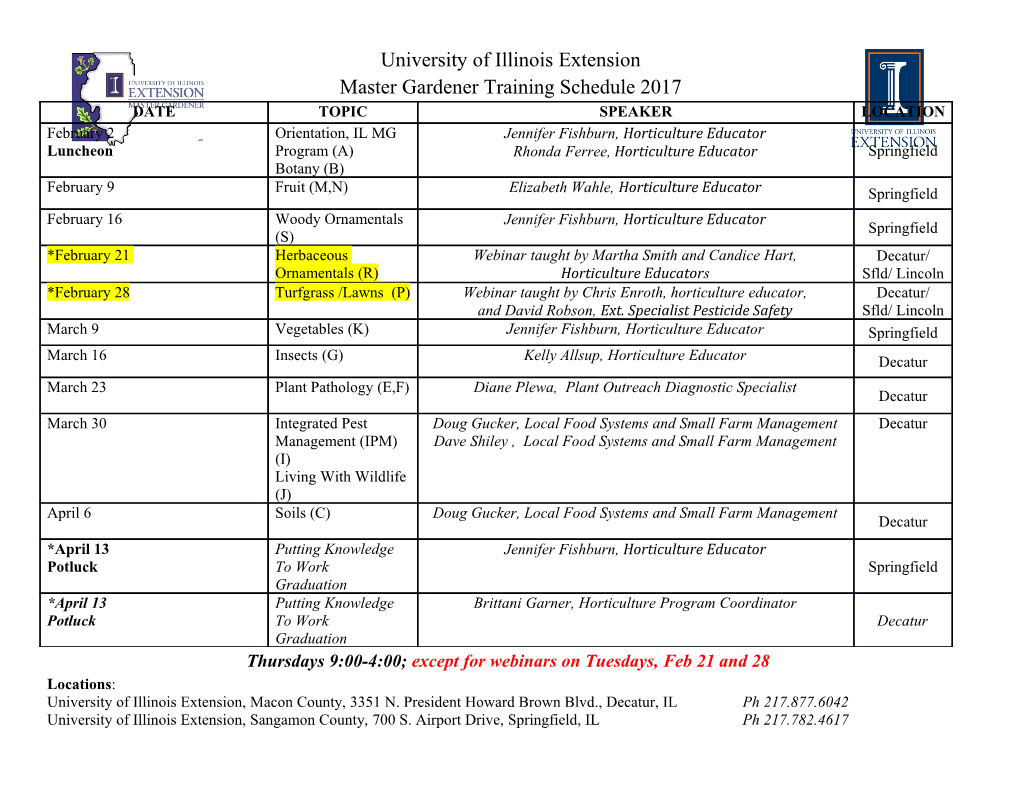
MFC for paper surface treatment Yselaure Boissard Materials Engineering, master's level 2017 Luleå University of Technology Department of Engineering Sciences and Mathematics Student: Yselaure Boissard EEIGM, European engineering school of material science Université de Lorraine, France Luleå University of Technology, Sweden Examiner: Professor Kristiina Oksman Division of Materials Science Luleå University of Technology, Sweden Supervisor: Silvia Viforr, MSc., Lic. Eng. Project Manager R&D Team Skärblacka BillerudKorsnäs AB i ii Acknowledgments I would like to thank Professor Kristiina Oksman for her thorough examination and constructive criticism of my work which pushed me to improve it immensely. My appreciation goes to all BillerudKorsnäs people who helped me in and out of the lab at Skärblacka, Beetham, Frövi and Gruvön. I am very glad that I could work alongside you during those 20 weeks. Finally, I am grateful to Silvia Viforr for allowing me to work on this project and for the great support and tutorship that she provided every day. Thank you. La Chapelle sur Erdre (France), June 2017 iii iv Abstract In this study, microfibrillated cellulose (MFC) was applied in an aqueous suspension as a coating material on paper substrates. Two different coating techniques were used: rod coating and size press. The MFC suspension used has a high water content and water is known to deteriorate the properties of the paper, so water treated paper substrates were prepared as references to give an indication of the effects that the processing has on the final properties of the coated papers. The structure of the MFC coating and associated surface properties were evaluated using scanning electron microscopy (SEM) and by measuring the thickness and the roughness of the coated substrates. A tool to visualise the distribution of the MFC was developed and the tensile properties of the MFC coated substrates were characterised. Resistance to air, oxygen and water vapour permeation as well as water and grease absorption were used to describe the barrier properties of the coated papers. The MFC coated paper substrates exhibited a higher roughness than the reference paper substrate. This was due to the sensitivity of the substrate to water and not from the coating material itself since the water treated paper substrates showed an even higher roughness than the MFC coated substrates. The latter showed slightly increased tensile properties compared to the reference paper substrates, and most importantly, reduced air permeance and grease absorption (-100% and -84% respectively); for the rod coated paper substrate with 3 g⁄m2 coat weight. The water vapour transmission rate was also decreased with the applied MFC coatings. Advantages and drawbacks were identified for the coating techniques. The rod coating allowed a good control of the coat weight in a range of 1 to 3 g⁄m2. However, the Mayer rod and the high viscosity of the MFC suspension caused poor MFC distribution and a coating which reproduced the rod pattern. With the size press, coat weights around 1 g⁄m2 were reached. The MFC did not build a coating layer on the paper substrate surface but was impregnated into the paper substrate by the rollers. v vi Table of contents Acknowledgments ................................................................................................................................... iii Abstract .................................................................................................................................................... v Table of contents .................................................................................................................................... vii 1. Introduction ..................................................................................................................................... 1 1.1. General introduction .................................................................................................................... 1 1.2. Objective of the thesis ................................................................................................................. 1 1.3. Limitations in scope .................................................................................................................... 2 1.4. Project plan .................................................................................................................................. 2 2. Literature review ............................................................................................................................. 3 2.1. Introduction ................................................................................................................................. 3 2.2. Cellulosic materials ..................................................................................................................... 3 Cellulose and paper ............................................................................................................................. 3 Cellulose nanofibres or microfibrillated cellulose .............................................................................. 5 MFC coatings on paper substrates ....................................................................................................... 6 2.3. Techniques................................................................................................................................... 7 Rod coating ......................................................................................................................................... 7 Size press coating ................................................................................................................................ 8 Drying method ..................................................................................................................................... 9 2.4. Summary of the literature review .............................................................................................. 10 3. Materials and methods ................................................................................................................... 11 3.1. Materials .................................................................................................................................... 11 3.2. Methods ..................................................................................................................................... 11 3.2.1. Characterisation methods ...................................................................................................... 13 4. Results and discussion ................................................................................................................... 17 4.1. Characteristics of the MFC suspension ..................................................................................... 17 vii 4.2. Influence of the coating parameters .......................................................................................... 17 4.2.1. Rod coating............................................................................................................................ 17 4.2.2. Size press coating .................................................................................................................. 19 4.3. MFC coatings structure and surface properties ......................................................................... 20 4.4. Mechanical properties ............................................................................................................... 24 4.5. Barrier properties ....................................................................................................................... 25 5. Conclusion ..................................................................................................................................... 29 6. Future work ................................................................................................................................... 30 7. List of references ........................................................................................................................... 31 8. Appendix ....................................................................................................................................... 33 viii 1. Introduction 1.1. General introduction In the packaging world, materials from natural fibres such as paper are gaining ground thanks to their recyclable and biodegradable characters. Paper is made from cellulosic fibres from wood and is therefore renewable and biodegradable [1]. However, for some types of packaging e.g. food packaging, paper shows its limits. It exhibits too low barrier properties to oxygen and moisture, a low resistance to grease and a sensibility to water, which make it an unsuitable choice. The products would not be protected enough and have a limited shelf life [2]. For this reason, paper is usually combined with coating polymeric layers such as PE, PVDC, EVOH and PVC derivatives as well as aluminium to improve its barrier properties. These materials however, are for the most part non-biodegradable and the final packaging is quasi impossible to recycle properly because the layers cannot be efficiently separated. [3] That is why recent studies have been focusing on finding biodegradable polymers to replace the conventional layers. One of these materials is microfibrillated cellulose (MFC), also called cellulose nanofibres / nanofibrils (CNF) or nanofibrillated cellulose (NFC). It consists
Details
-
File Typepdf
-
Upload Time-
-
Content LanguagesEnglish
-
Upload UserAnonymous/Not logged-in
-
File Pages42 Page
-
File Size-