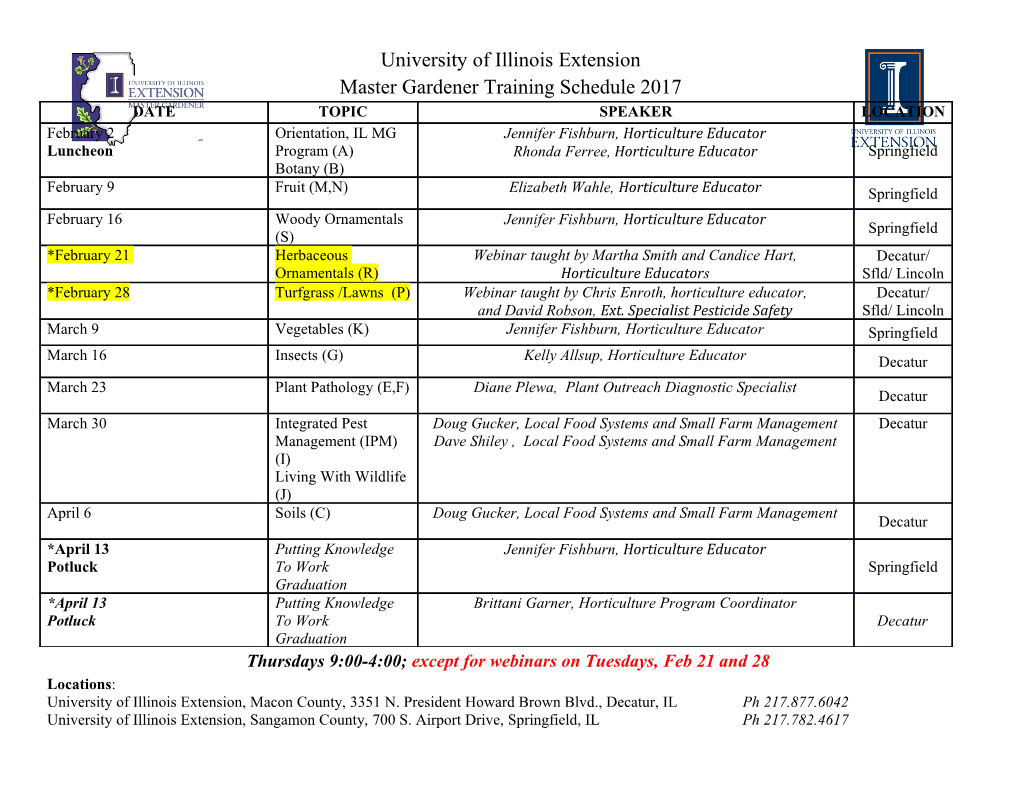
Sumitomo Chemical Co., Ltd. Polypropylene Compounds for Petrochemicals Research Laboratory Automotive Applications Satoru MORITOMI Tsuyoshi WATANABE Susumu KANZAKI Engineering plastics and metals have been extensively replaced by polypropylene (PP) based materials in auto- motive parts in order to achieve weight reductions and cost savings. To accomplish this, PP compounds which are made from PP and other components are under intense investigation. In this paper, we review the progress of re- search into compounding technology, improvement of mechanical properties and functionalization. Some problems and solutions for injection molding are also summarized. Furthermore, material developments for environmental load reduction are shown. This paper is translated from R&D Report, “SUMITOMO KAGAKU”, vol. 2010-I. Introduction tion. Therefore, it is expected that PP consumption will continue to increase in the future. Because polypropylene (PP) is low in cost but has out- Fig. 1 shows an example of a general constitution of standing mechanical properties and moldability, it ac- PP compounds for automotive applications. The impact counts for more than half of all the plastic materials used strength of the “impact PP,” which is composed of homo in automobiles. PP compounds are used for a variety of PP and ethylene propylene copolymer (EP copolymer), parts, including bumper facias, instrumental panels and is improved by adding an ethylene-based elastomer such door trims. Several grades of PP compounds, with their as ethylene-butene or ethylene-octene copolymer, to diverse performance characteristics, have been devel- which inorganic filler such as talcum is added for en- oped by compounding PP with various other materials hanced rigidity. according to the performance requirements of the in- The growth of PP compounds for automotive applica- tended parts. As of 2007, 3.75 million tons of PP (8% of tions has thus far been supported by the improved per- the world’s total PP consumption of 45.5 million tons) formance of PP resins—which serve as the base of PP and 690,000 tons of PP (approximately 23% of the total compounds—and advancements in compound technol- domestic PP consumption of 2.94 million tons) are used ogy. With respect to the former, catalysts and the poly- for automotive applications.1) In recent years the envi- merization process have been continually, energetically ronmental adaptability of PP has drawn significant atten- improved in order to control the primary and higher- Impact Reinforcement (Colorant) Block PP (Impact PP) modifier filler Additives Homo PP EP Copolymer (P part) (EP part) Process stability Weatherability Stiffness, Mold shrinkage Flowability, Stiffness Impact resistance, Mold shrinkage, paintability, Surface appearance (Flow mark, Weld line, Gloss) Fig. 1 Component of PP compound for automotive application SUMITOMO KAGAKU (English 2010-I Edition) 2010-I, Report 1 Copyright © 2010 Sumitomo Chemical Co., Ltd. 1 Polypropylene Compounds for Automotive Applications order structures of polymers. Regarding the latter, im- Currently, several unique process methods (such as a provements in the performance and dispersibility of elas- loop-type reactor method having two polymerization tomers, as well as the control of particle size, dispersion zones) are being developed in order to expand the mo- and interface of inorganic fillers, have been attempted up lecular weight distribution and control the composition to the present time. distribution of copolymers in an effort to achieve higher Generally, the catalyst currently used for industrial functionality and performance in PP.2) purposes is the Mg-Ti type, otherwise known as the With respect to resin-based automotive parts, lower Ziegler-Natta (ZN) catalyst. Subsequent to the discovery weight is demanded for the sake of reduced environmen- of ZN catalyst in 1953 (and 1954), the improvement of tal burden and better design and higher moldability are its performance has been continuously attempted. In the also required. In response to that demand, various course of such development the polymer activity, stere- phases of PP compounds for automotive applications oregularity and morphology of polymer particles have have been improved. The improvements made thus far been improved, thus contributing greatly to the simpli- include greater rigidity, impact strength, fluidity and fication of the polymerization process as well as to the crystallization. Such enhancements of PP compounds improvement of PP performance (Fig. 2). Since the be- have been achieved by compounding PP with additives ginning, the development of PP catalyst has been con- such as elastomers and/or various inorganic fillers, as ducted with focus on two areas: polymer activity and well as through higher stereoregularity, fluidity and stereoregularity. The standards of these properties are rubberization which have been achieved with the afore- becoming extremely close to the ultimate. In recent mentioned improvements in catalysts and the manufac- years catalyst developments have been conducted with turing process. Thanks to these improvements, a wide increased emphasis on control over molecular weight range of performance requirements in automotive parts, (distribution) and copolymerization reactivity. for which various engineering plastics were convention- ally used, can now be covered by PP compounds alone (Fig. 3). As a result, PP-based material consumption in : Atactic-PP cont. (wt%) 100 automotive applications has continued to increase. The 10 3 details of the compound technology will be described in 4 Ti/Mg Hybrid 10 Catalyst the following section. 3 1 5 TiCl3 Catalyst 1 100 PC PP compounds ) 10 Gas phase process 2 Bumper facia (Long glass fiber) Bulk process Slurry process Instrumental Panel Catalyst activity (kg-PP/g-Cat) 0.1 Engine Room 1960 1970 1980 1990 ABS m-PPE Year m-PPE/GF 10 Pillar Fig. 2 Development history of Ziegler-Natta catalyst and polymerization process for PP PA PA/GF The PP manufacturing process, accompanied by im- Impact PP provements in the performance of ZN catalyst, has tran- Izod Impact Strength at 23deg. (kJ/m PP compounds 1 sitioned from the slurry polymerization method, which 0 2000 4000 6000 8000 contains the residual catalyst removal process and the Flexural Modulus (MPa) by-produced amorphous polymer removal process, Fig. 3 Mechanical properties of PP compounds through the bulk polymerization method, which utilizes liquefied propylene as a solvent, and then to the gas phase polymerization method, which doesn’t use the Compound Technology amorphous polymer/residual catalyst removal system. This transition has propelled the streamlining of the PP Twin-screw extruders are most commonly used for the manufacturing process while promoting energy conser- production of PP compounds for automotive applications. vation. It is essential that the twin-screw extruder has high pro- SUMITOMO KAGAKU (English 2010-I Edition) 2010-I, Report 1 Copyright © 2010 Sumitomo Chemical Co., Ltd. 2 Polypropylene Compounds for Automotive Applications ductivity as well as the ability to disperse the additives 500 such as elastomers and fillers within PP and prevent the Average diameter 10µm degradation of the material during the manufacturing 400 6µm process. In recent years, accompanied by increased ap- 1.1µm plications in light-weight vehicles, materials having high fluidity (which facilitates thin-wall molding) have been 300 in demand. Because this type of material has the low melt viscosity of PP, which is the main component, the 200 design of the extruder’s screws is important in order to adequately disperse the additives. Maximum feed rate (kg/h) 100 Table 1 History and development of extruder 0 0 200 400 600 Number Outer/Inner Shaft torque Maximum Generation of screw diameter ratio screw Screw speed (rpm) threads (Do/Di) (Md/a3) speed Fig. 4 Effect of talcum diameter on maximum 2 Nm/cm rpm feed rate 1 3 1.22 3.7 150 2 2 1.44 5.0 300 3 2 1.55 8.7 600 4 2 1.55 11.3 1200 To address this issue, screws having the design shown 5 2 1.55 13.6 1200 in Fig. 5 are used. In this design the screws maintain the Md: Torque, a: Shaft and axle distance resin in the semi-molten state in the primary mixing sec- tion, maintaining the space between the cylinder and the Do Do resin passing through the section, and then discharge the air that was brought in along with the talcum through Di Di a vent port located on the extruder’s downstream side. Compared to the conventional extruder, which melts Triple flight Double flight resin entirely within the primary mixing section, this system can significantly improve the productivity of the Table 1 shows the history and development of twin- extruder by allowing the air to escape toward the down- screw extruders. The productivity and performance of stream of the extruder. twin-screw extruders can be characterized by the groove depth, the rotational speed of the screws and the motor’s performance. It can be observed that the groove depth, Conventional Compounding rotation speed and torque have increased along with the generational progress. Air Raw Materials As previously described, talcum is added to PP com- Air Sealed by fully molten resin pounds to give them more rigidity. The use of talcum having finer particles has become the mainstream, ac- companied by more demanding performance require- ments. Fig. 4 depicts the effect of talcum particle size on Improved Compounding the discharge rate.3) When using talcum at a minute par- Raw Materials Ventilation ticle size, the discharge rate significantly decreases at Air the same screw rotational speed. This is because when supplying the granulator with talcum having a minute particle size, the air between the particles is also brought Semi- molten resin: incompletely-filled into the machine, which causes the backflow of air to- ward the upper stream of the screws and results in the Fig. 5 Concept of screw pattern for high deterioration of material supply performance. throughput compounding SUMITOMO KAGAKU (English 2010-I Edition) 2010-I, Report 1 Copyright © 2010 Sumitomo Chemical Co., Ltd.
Details
-
File Typepdf
-
Upload Time-
-
Content LanguagesEnglish
-
Upload UserAnonymous/Not logged-in
-
File Pages16 Page
-
File Size-