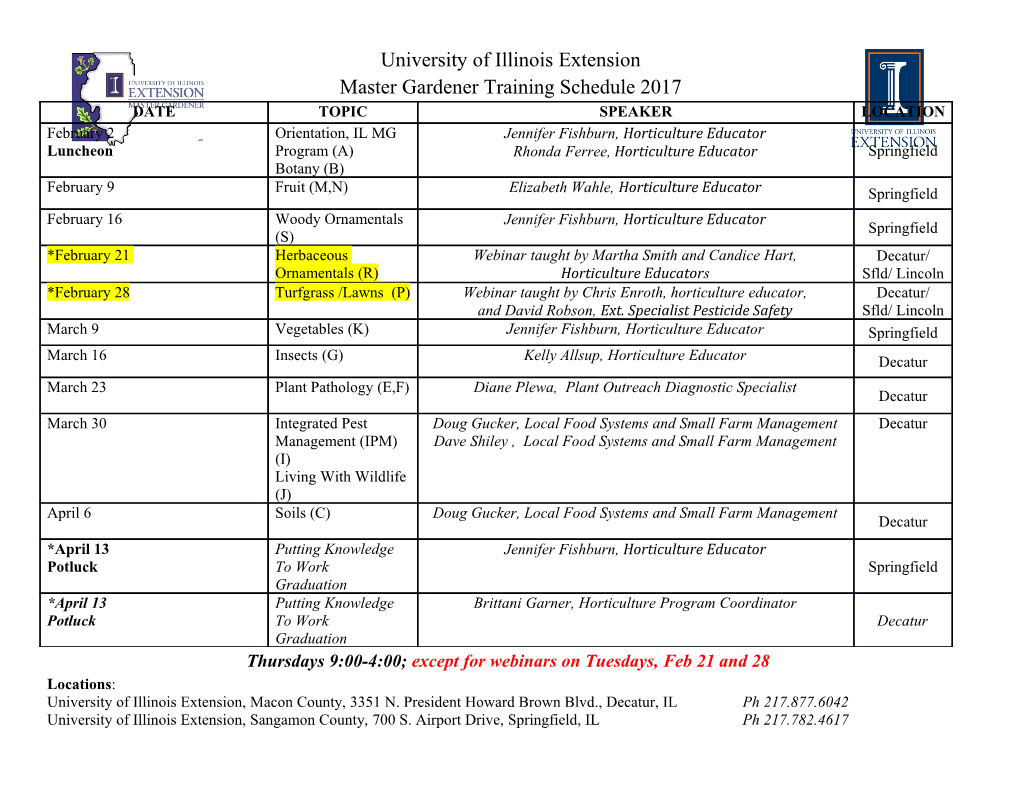
Materials Transactions, Vol. 48, No. 8 (2007) pp. 2194 to 2201 #2007 The Japan Institute of Metals Improvement of Casting Speed and Billet Quality of Direct Chill Cast Aluminum Wrought Alloy with Combination of Slit Mold and Electromagnetic Coil Hai Hao, Xingguo Zhang, Shan Yao and Junze Jin State Key Laboratory of Materials Surface Modification by Laser, Ion and Electronic beams, School of Materials Science and Engineering, Dalian University of Technology, Dalian, 116023, P.R. China A mold with slits and external cooling water channels was designed for the direct chill casting processing. By imposing a high frequency magnetic field, the surface quality and microstructure of the direct chill cast billets are improved. The casting speed could be improved by the simultaneous use of mold and electromagnetic coil. In the case of one kind of Al-Cu-Mg alloy with a wide freezing range, the critical casting speed to break-out can be improved 60%. The microstructure of the billet cast with electromagnetic field is more fine and uniform than that of the conventionally cast billet, and the subsurface segregation usually observed in the conventional billets is eliminated. [doi:10.2320/matertrans.MRA2007030] (Received February 5, 2007; Accepted May 14, 2007; Published July 11, 2007) Keywords: direct chill casting, aluminum wrought alloy, electromagnetic casting, casting speed 1. Introduction front is limited in the certain zone of the inductor acting. A novel technique is described in this paper, which combines As the premier process for producing aluminum shapes the DC mold and the electromagnetic coil and leads to high suitable for subsequent processing in extrusion, rolling or quality aluminum billet with smooth surface, fine structure, remelt operations, the direct chill casting (DCC) technolog- especially, under an improving casting speed. ical method produces over ten million tonnes of aluminum per annum worldwide. 2. Experiments In the past, ingot surface quality has been a strong impetus in the development of new versions of the process. On the A newly developed mold is schematically shown in Fig. 1, other hand, process productivity and versatility will drive which has closed slits to make sufficient high penetration of change in the future. Increasing casting speed will be an the electromagnetic field to the melt. The mold with an effective method for improving productivity. If casting speed interior diameter of 100 mm, 10 mm thickness of mold wall could be increased, greater tonnages could be cast with less and 200 mm of height, does not have a complicated inside capital cost.1) water channel, which reduces the cost and is easier to design In order to improve production, increasing casting speed is and manufacture. 12 pieces of slits with each width of 0.3 mm necessary. However, some problems need to be solved. As were fabricated around the circumference inside the mold casting speed increases, the UCD (upstream conduction wall, and the mica sheets were used to fill the spacing of the distance) decreases. If the UCD is very small, it means that the liquid front is getting very close to the bottom of the mold and possibility of bleedouts increases.2) Moreover, the cracking, porosities and other solidification defects may Mold appear with the increasing casting speed.3) Despite thermal Flange X treatment and mechanical working, many ingot defects may O persist through to the end product. Clearly, metallurgical defects must be eliminated at the ingot casting stage if high 4) quality end products are to be produced. Charge Fortunately, electromagnetic casting (EMC) of aluminum Coil Cooling alloys has been the subject of considerable development in water pipe recent decades, mostly as a result of an improved under- Z standing of the magnetohydrodynamics in metallurgy. The electromagnetic casting mold uses an inductor coil through which a high frequency (typically a few kHz) current is passed. The currents induced in the liquid metal interact with Slit the magnetic field of the coil. This produces a restraining Segment force on the liquid which acts against the metallostatic head pushing the metal away from the mold. Lack of contact between liquid and mold eliminates mold cooling and the problem of reheating, producing a very good surface and 5) microstructure. However, it is very difficult to increase the Fig. 1 Schematic illustration of the mold, coil, cooling water system and casting speed in the EMC process because the solidification coordinate system of magnetic field measurement. Improvement of Casting Speed and Billet Quality of Direct Chill Cast Aluminum Wrought Alloy 2195 slits. The copper coil was installed to apply a high frequency 100.0 30 current in 3 turns and 40 mm of height. The cooling water 90.0 magnetic flux density 25 pipes have their own separate manifolds, and their positions 80.0 coil power along the vertical direction may be moved freely. Therefore, 70.0 20 the distribution and the intensity of the cooling water are 60.0 adjustable. 50.0 15 The experimental materials were pure Al and 2024 alloy. 40.0 10 The compositions along with casting parameters are summa- 30.0 Coil power, P/kW rized in Table 1. 20.0 Magnetic flux density, Bz/G 5 During the measurement of the magnetic flux density in the 10.0 mold, cold charges of aluminum were inserted in the mold as 0.0 0 simulating materials for casts and they were cooled inde- 0 200 400 600 800 1000 1200 pendently. The coordinate system and the schematic illus- Coil current, I/A tration of magnetic field measurement are shown in Fig. 1. As for the measurement points, at segment means on the Fig. 2 Relationship of coil current with coil power and magnetic flux density (without charge, z ¼ 80, center of mold). centerline of inner surface of segment, at slit means on the centerline of inner surface of slit, and at center means at the centerline of the mold. The magnitude of magnetic flux 120 density in axial direction was measured by using a magnetic probe of the small coil type. 100 center The sump depth of the melt was probed by immersing steel segment rod during the casting process. The sump profile was obtained 80 slit by tracer method. The macrostructure at transverse and 60 longitudinal section of the billets were analyzed. The microstructural specimens were cut from edge to center at 40 the transverse section and analyzed by optical microscopy. Magnetic flux density, Bz /G 20 3. Results and Discussion 0 3.1 Measurement of electromagnetic field 0 50 100 150 200 Figure 2 shows the linear relationship between coil current Distance from the mold top, d/mm and magnetic flux density, the measurement point is the Fig. 3 Distribution of magnetic field along the axial direction (I ¼ 800 A, center of the mold. With a higher coil current, a stronger without charge). electromagnetic force could be obtained. Generally, the latter is in favor of the surface quality of billet. However, the critical power and other negative effects should be consid- below the mold top about 80 mm. ered before choosing the suitable coil current. A peak value is observed between the mold top and the As shown in Fig. 3, the greatest value of the magnetic flux start of slit as indicated in Fig. 3. It is because of the density along the vertical direction is observed at the position superposition of the magnetic flux between the mold top and 75 mm below the mold top at the slit and the segment. For the the start of the slits. The more magnetic flux penetrates the center position of the mold, the strongest magnetic field is slits readily and meets the other magnetic flux skipping the Table 1 Chemical compositions and casting parameters of pure Al and 2024 alloy. Material Casting parameters EMC coil current: 1000 A, frequency: 20 kHz Compositions (mass%) Al 99.9 Pure Al Water flow (L/min) 40 Casting speed 0.2 0.3 0.4 0.5 (m/min) Compositions Al Cu Mg Si Fe Mn Ti Cr Zn (mass%) 92.05 4.4 1.5 0.5 0.5 0.6 0.1 0.1 0.25 2024 alloy Water flow (L/min) 25 Casting speed DCC 0.1 0.15 0.2 0.25 (m/min) Casting speed EMC (m/min) 0.1 0.2 0.3 0.4 2196 H. Hao, X. Zhang, S. Yao and J. Jin 250 120 Zcharge=40 Zcharge=50 100 200 Zcharge=60 Zcharge=70 80 150 60 100 40 50 Magnetic flux density, Bz/G 20 Magnetic flux density, Bz/G 0 0 ° ° ° ° ° 0 50 100 150 200 0 100 200 300 400 Distance from the mold top, d/mm Circular angle Fig. 4 Variation of magnetic field on segment surface along axial direction Fig. 6 Circular magnetic field around the mold wall at the level below with different charge positions, I ¼ 800 A(Z means the distance of charge mold top 75 mm, I ¼ 800 A. charge below the mold top). 250 descend to the water cooling zone quickly, which decreases the tendency of re-melting and formation of exudations. segment However, it should be mentioned that with casting speed 200 slit increasing, the billet shell which is solidified in contact with 150 the mold wall becomes thinner and thinner, with an increasing tendency toward horizontal cracking and bleed- 6) 100 out. Compared with the pure Al billet, the 2024 alloy billet 50 surface is bad, as shown in Fig. 8. Bleed bands (periodic surface segregation) and cold shut can be seen on the billet Magnetic Flux density, Bz/G 0 surface. Surface segregation occurs when molten metal 0 50 100 150 200 ‘‘bleeds’’ through the partially solidified shell, driven mainly Distance from the mold top, d/mm by the metallostatic pressure of the liquid metal above.
Details
-
File Typepdf
-
Upload Time-
-
Content LanguagesEnglish
-
Upload UserAnonymous/Not logged-in
-
File Pages8 Page
-
File Size-