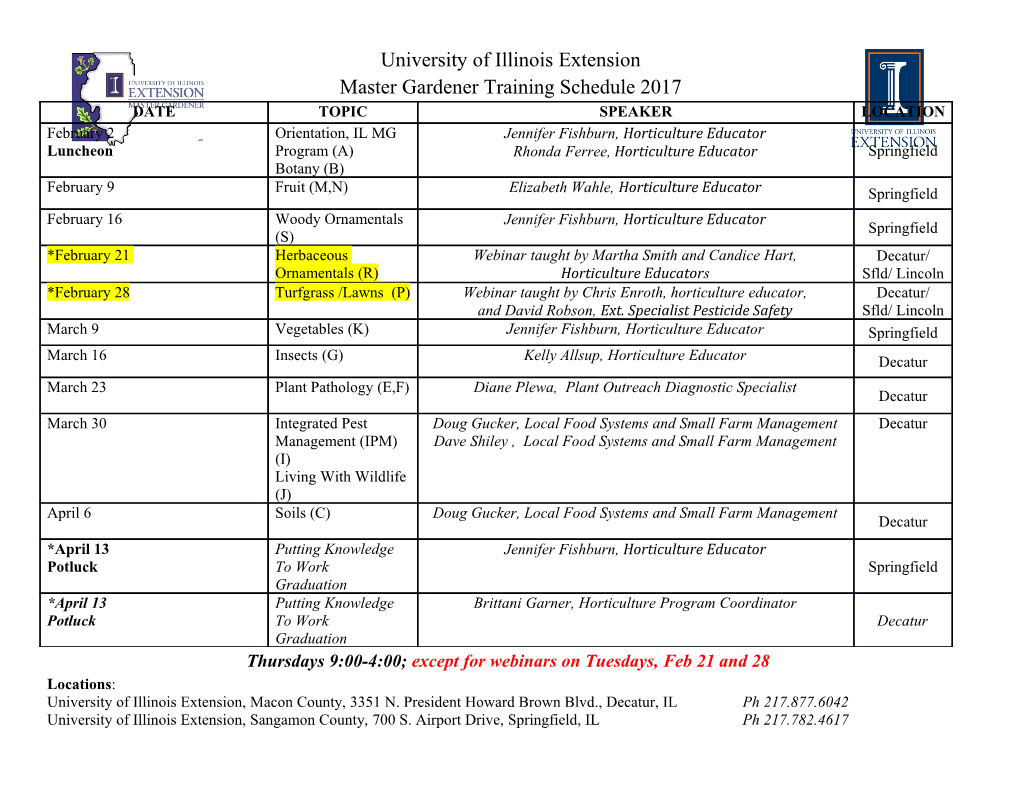
CONSTITUTIVE MODELING OF ENGINEERING MATERIALS - THEORY AND COMPUTATION The Primer by Kenneth Runesson Lecture Notes, Dept. of Applied Mechanics, Chalmers University of Technology, G¨oteborg Preface There seems to be an ever increasing demand in engineering practice for more realistic models as applied to metals as well as composites, ceramics, polymers and geological materials (such as soil and rock). Consequently, a vast amount of literature is available on the subject of “nonlinear constitutive modeling”, with strong emphasis on plastic- ity and damage. Such modeling efforts are parallelled by the development of numerical algorithms for use in Finite Element environment. For example, implicit (rather than ex- plicit) integration techniques for plasticity problems are now predominant in commercial FE-codes. I am indebted to a great number of people who have contributed to the present volume: Mr. M. Enelund, Mr. L. Jacobsson, Mr. M. Johansson, Mr. L. M¨ahler and Mr. T. Svedberg, who are all graduate students at Chalmers Solid Mechanics, have read (parts of) the manuscript and struggled with the numerical examples. Mr. T. Ernby prepared some of the difficult figures. Ms. C. Johnsson, who is a graduate student in ancient Greek history at G¨oteborg University, quickly became an expert in handling equations in LATEX. The contribution of each one is gratefully acknowledged. G¨oteborg in March 1996. Kenneth Runesson 2nd revised edition: I am grateful to Mr. Lars Jacobson and Mr. Magnus Johansson (in particular) for their help in revising parts of the manuscript. G¨oteborg in March 1997. Kenneth Runesson 3rd revised edition: Ms. EvaMari Runesson, who is a student in English at the University of Gothenburg (and also happens to be my daughter) did an excellent job in mastering LATEXfor this edition. iv G¨oteborg in March 1998. Kenneth Runesson 4th revised edition: Mr. Lars Jacobsson and Ms. EvaMari Runesson were of great help in typing the manuscript. G¨oteborg in January 1999. Kenneth Runesson 5th revised edition: Some small changes were made to improve the manuscript. G¨oteborg in January 2000. Kenneth Runesson 6th revised edition: Ms. Annicka Karlsson was of great help in revising the manuscript, mainly concerning the notation. G¨oteborg in January 2002 Kenneth Runesson 7th revised edition: The help by Mr. Mikkel Grymer in revising the manuscript is greatly acknowledged. G¨oteborg in March 2005 Kenneth Runesson Vol0 March 7,2006 vi Vol0 March 7,2006 Contents 1 CHARACTERISTICS OF ENGINEERING MATERIALS AND CON- STITUTIVE MODELING 1 1.1 General remarks on constitutive modeling . ...... 1 1.1.1 Concept of a constitutive model . 1 1.1.2 The role of constitutive modeling . .. 3 1.1.3 General constraints on constitutive models . ...... 4 1.1.4 Approaches to constitutive modeling . ... 5 1.2 Modelingofmaterialfailure—Fracture . ..... 7 1.2.1 Continuum damage mechanics . 7 1.2.2 Fracturemechanics ........................... 8 1.3 Common experimental test conditions . ..... 8 1.4 Typical behavior of metals and alloys . ..... 12 1.4.1 Plastic yielding — Hardening and ductile fracture . ....... 12 1.4.2 Constant loading — Creep and relaxation . .. 13 1.4.3 Time-dependent loading — Rate effect and damping . ... 14 1.4.4 Cyclic loading and High-Cycle-Fatigue (HCF) . ..... 15 1.4.5 Cyclic loading and Low-Cycle-Fatigue (LCF) . ..... 16 1.4.6 Creep-fatigue and Relaxation-fatigue . ..... 20 1.5 Typical behavior of ceramics and cementitious composites ......... 21 1.5.1 Monotonic loading – Semi-brittle fracture . ...... 21 Vol 0 March 7, 2006 viii CONTENTS 1.5.2 Cyclicloadingandfatigue . 22 1.5.3 Creepandrelaxation . .. .. 22 1.6 Typical behavior of granular materials . ...... 22 1.6.1 Monotonicloading–Basicfeatures . .. 22 1.6.2 Constant loading – Consolidation . .. 23 1.6.3 Constant loading – Creep and relaxation . ... 23 2 THERMODYNAMICS — A BRIEF SUMMARY 25 2.1 Free energy and constitutive relations . ....... 25 2.1.1 General ................................. 25 2.1.2 Stress-strainresponserelation . .... 26 2.1.3 Materialclasses ............................. 27 3 VISCOELASTICITY 29 3.1 Introduction................................... 29 3.2 Prototype model: The Maxwell rheological model . ....... 30 3.2.1 Thermodynamic basis — Constitutive relation . ..... 30 3.2.2 Prescribed constant stress (pure creep) . ..... 32 3.2.3 Prescribed constant strain (pure relaxation) . ....... 32 3.3 Linear viscoelasticity — Constitutive modeling . .......... 33 3.3.1 Generalcharacteristics . 33 3.3.2 Laplace-Carsontransform . 35 3.3.3 Linear Standard Model (Generalized Maxwell Model) . ...... 37 3.3.4 Backward Euler method for linear standard model . ..... 40 3.4 Linear viscoelasticity — Structural analysis . .......... 42 3.4.1 Structuralbehavior. .. .. 42 3.4.2 Solutionstrategies ........................... 43 3.4.3 Analysisoftruss—Elasticanalogy . .. 44 Vol0 March 7,2006 CONTENTS ix 3.4.4 Analysis of truss — numerical integration . .... 47 3.4.5 Analysis of beam cross-section — Elastic analogy . ...... 49 3.4.6 Analysis of double-symmetric beam cross-section — Numerical in- tegration................................. 51 3.5 Nonlinear viscoelasticity — Constitutive modeling . ........... 53 3.5.1 Generalcharacteristics . 53 3.5.2 Nortoncreeplaw ............................ 54 3.5.3 Backward Euler method for the Norton creep law . ... 56 3.6 Nonlinear viscoelasticity — structural analysis . ........... 58 3.6.1 Structuralbehavior. .. .. 58 3.6.2 Analysisoftruss ............................ 58 3.6.3 Analysis of beam cross-section — Stationary creep . ....... 60 3.6.4 Analysis of double-symmetric beam cross-section — Numerical in- tegration................................. 63 3.6.5 Analysis of single-symmetric beam cross-section — Numerical inte- gration.................................. 64 3.7 Viscous damping and dynamic behavior . .... 67 3.7.1 Preliminaries .............................. 67 3.7.2 Forced vibration of discrete system . ... 68 3.7.3 Energydissipation ........................... 70 3.7.4 Evaluation of damping for the linear standard model . ...... 71 3.8 Appendix: Laplace-Carsontransform . .... 75 4 PLASTICITY 77 4.1 Introduction................................... 77 4.2 Prototype rheological model for perfectly plastic behavior.......... 79 4.2.1 Thermodynamic basis — Yield criterion . .. 79 4.2.2 Plastic flow rule and elastic-plastic tangent relation......... 80 Vol 0 March 7, 2006 x CONTENTS 4.2.3 Dissipationofenergy . .. .. 82 4.3 Prototype model for hardening plastic behavior . ........ 82 4.3.1 Thermodynamic basis — Yield criterion . .. 82 4.3.2 Plastic flow rule and elastic-plastic tangent relation......... 83 4.3.3 Dissipationofenergy . .. .. 86 4.4 Model for cyclic loading — Mixed isotropic and kinematic hardening . 86 4.4.1 Thermodynamic basis — Yield criterion . .. 86 4.4.2 Associative flow and hardening rules — Linear hardening...... 87 4.4.3 Characteristic response for linear hardening . ....... 88 4.4.4 Associative flow and nonassociative hardening rules — Nonlinear hardening ................................ 88 4.4.5 Characteristic response for nonlinear hardening . ........ 90 4.4.6 Backward Euler method for integration — Linear hardening .... 96 4.5 Structuralanalysis .............................. 101 4.5.1 Structural behavior — Limit load analysis . .101 4.5.2 Analysis of truss — Numerical integration . .101 4.5.3 Analysis of double-symmetric beam cross-section . .......103 4.5.4 Analysis of single-symmetric beam cross-section — Numerical inte- gration..................................106 5 VISCOPLASTICITY 109 5.1 Introduction...................................109 5.2 Prototype rheological model for perfectly viscoplasticbehavior . 110 5.2.1 Thermodynamic basis — Quasistatic yield criterion . .......110 5.2.2 Viscoplastic flow rule — Perzyna’s formulation . ......111 5.2.3 Bingham model — Perzyna’s formulation . 113 5.2.4 Norton model (creep law) — Perfect viscoplasticity . .......114 Vol0 March 7,2006 CONTENTS xi 5.2.5 Limit behavior — Viscoplastic regularization of rate-independent plasticity.................................115 5.3 Prototype rheological model for hardening viscoplasticity ..........115 5.3.1 Thermodynamic basis — Quasistatic yield criterion . .......115 5.3.2 Viscoplastic flow and hardening rules — Perzyna’s formulation . 116 5.3.3 Bingham model — Perzyna’s formulation . 117 5.3.4 Viscoplastic flow and hardening rules — Duvaut-Lions’ formulation 118 5.3.5 Comparison of Perzyna’s and Duvaut-Lions’ formulations. .119 5.3.6 Bingham model — Duvaut-Lions’ formulation . 120 5.4 Model for cyclic loading — Mixed isotropic and kinematic hardening . 121 5.4.1 Constitutive relations for linear hardening — Perzyna’s formulation 121 5.4.2 Backward Euler method for linear hardening — Perzyna’s formulation121 5.5 Structuralanalysis .............................. 123 6 DAMAGE AND FRACTURE THEORY 125 6.1 Introductiontothemodelingofdamage . .125 6.1.1 Conceptofdamage . .. .. .125 6.1.2 Physical nature of damage for different materials . ......127 6.1.3 The concepts of effective stress and strain equivalence........128 6.2 Prototype model of damage coupled to elasticity . ........130 6.2.1 Thermodynamics — Damage criterion . 130 6.2.2 Damagelawandtangentrelations. 133 6.3 Experimental measurement of damage . 135 7 DAMAGE COUPLED TO PLASTICITY 137 7.1 Prototype model for damage coupled to perfect plasticity..........137 7.1.1 Thermodynamic basis — Yield and damage criterion . .137 7.1.2 Plastic flow rule and damage law — Constitutive relations
Details
-
File Typepdf
-
Upload Time-
-
Content LanguagesEnglish
-
Upload UserAnonymous/Not logged-in
-
File Pages227 Page
-
File Size-