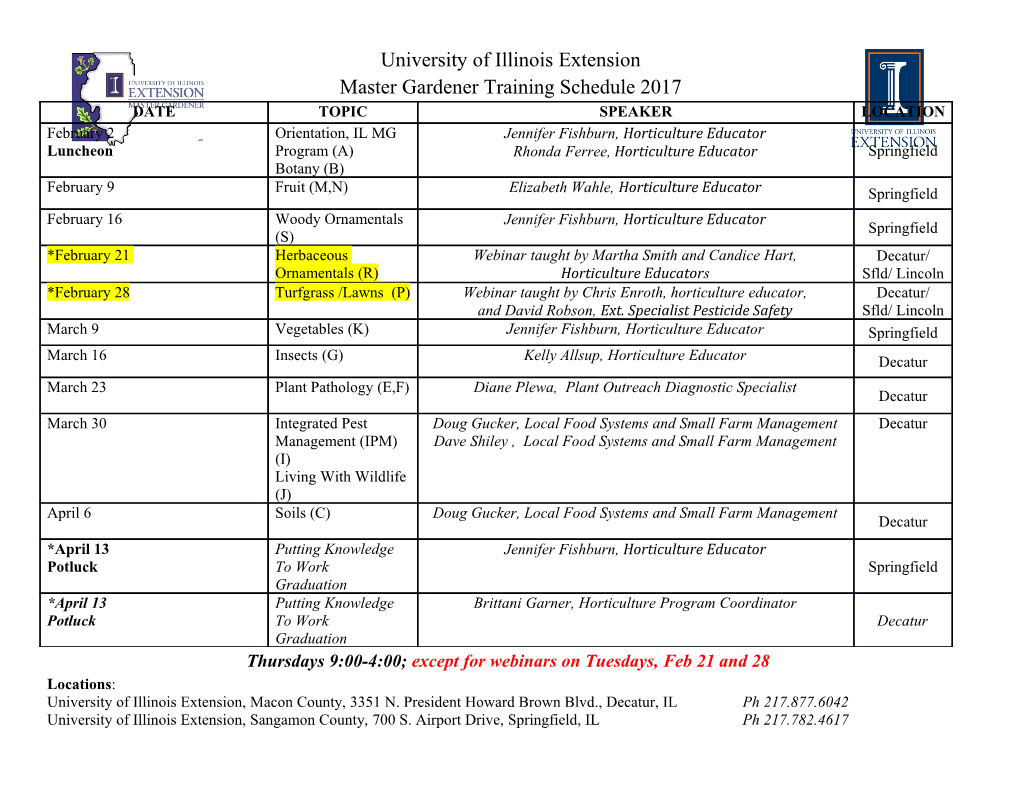
The Open Industrial & Manufacturing Engineering Journal, 2010, 3, 1-6 1 Open Access Compoforging of Al-Si Metal Matrix Composites Reinforced with -SiC: An Alternative Technique M. F. Valencia García1,*, H. V. Martínez2 and A. Morales Ortiz2 1Escuela de Ingeniería de Antioquia; Grupo Productividad hacia la Competitividad GPC – A.A. 7516 Medellín, Colombia 2Universidad Pontificia Bolivariana; Facultad de Ingeniería Mecánica. Grupo de Investigación sobre Nuevos Materiales GINUMA – A.A. 56006 Medellín, Colombia Abstract: This paper reports the -SiC particles surface modification by copper Electroless Plating (EP), as well as a morphological characterization of Al-Si reinforced composite obtained with such modified particles and consolidated by compoforging. The -SiC particles were obtained by thermal degradation of organic waste. The compoforging technique is a hybrid between the compocasting process and semi-solid forging. The properties of the obtained composite material derive from its globular structure, which is achieved by mixing the semi-solid alloy and the reinforcing particles. This method produced an almost perfect distribution of the reinforce particles. Furthermore, it is possible to achieve minimum defects (i.e. porosity) by applying pressures up to 60MPa. Keywords: Silicon carbide, electroless plating, superficial modification, mechanical mixing, compoforging. INTRODUCTION Table 1. Process Conditions for -SiC Synthesis About 35 years ago, semi-solid metallurgy, or semi-solid processing of alloys (SSM and SSP, respectively), was origi- Variable Value Unit nated. This technology combines the advantages of tradi- o tional forging and foundry processes. Nowadays such tech- Process temperature 1370 C nology and the development of Metal Matrix Composites Atmosphere process 1.5 L/min (MMC’s) have been strong, combining dispersion process to obtain Particulate reinforced Metal Matrix Composites Processing times 40 min (PRMCs). Catalyst FeCl2.4H2O - The foundry techniques in which the metal matrix is in the semi-solid state are of particular interest in the produc- Superficial Modification of -SiC tion of PRMC’s, because they gather energy savings and good particle dispersion. One of these techniques is Compo- Several possibilities are available to improve wetting, be- casting. This technique is actually a variation of the Stircast- tween SiC and Al such as reactive elements, i.e. Li, Mg, Si ing process, in which the metal is not completely melted [1]. [4] or using metallic coatings to generate a metal-metal inter- Stirring can be followed by die-casting to obtain ingots [2]. face, and hence a higher wettability. EXPERIMENTATION Previous investigations have shown that the usage of Ni or Cu coatings is effective, resulting in an increase of the -SiC resistance of the composite, its toughness and a better disper- -SiC microparticles were obtained as reported in [3]. sion of the reinforce particles within the molten metal [5, 6]. Rice husk (RH) was immersed in a FeCl ·4H O bath for one In this work, the -SiC particles were coated with Cu as it 2 2 follows. hour, and immersion in a NH4OH solution was done to pre- cipitate the remaining Fe. Afterwards, the RH was washed Electroless Plating (EP) with distillated water at 25ºC and dried at 80ºC for 12 hours; then the RH was subjected to controlled pyrolysis. Table 1 The plating process was adapted from that of Sharma shows the most important variables of the process. et al. [7]. In their work, the authors studied the effects of pH and temperature of the plating bath on the quality and quan- tity of the deposited Cu for ceramic nanoparticles. Pretreatment *Address correspondence to this author at the Escuela de Ingenieria de Antioquia, Grupo Productividad hacia la Competitividad GPC, A.A. 7516 Since the EP technique is a chemical reduction process, Medellin- Colombia, Tel: (57) 4 3549090, Fax: (57) 4 3861160; the preparation of the surface where the metal will be depos- E- mail: [email protected] ited is essential. That is why the particles were immersed in 1874-1525/10 2010 Bentham Open 2 The Open Industrial & Manufacturing Engineering Journal, 2010, Volume 3 Valencia García et al. SnCl2 and PdCl2 solution, respectively. Table 2 lists the de- Drying tails of the pretreatment of the particles. As soon as the coating reaction was ended, the particles Coating were washed with water and then subjected to vacuum (-1 bar) at 60ºC for one hour, to dry them. Once the particles were catalyzed, they were taken to the plating bath, which is constantly stirred, in which the reduc- tion reaction took place. This bath consists of a metallic ions Table 3. Parameters for the EP of -SiC solution of cupric sulfate, formaldehyde as a reducing agent and sodium-potassium tartrate (Rochelle’s salt) as a com- Solution Chemical Role in Time [ ] Operation plexing agent, which stops the metallic salt from precipitat- (mL) Species the Bath (min) ing. Metal CuSO .5H O 10 g/L ions coa- Table 2. Superficial Pretreatment of -SiC 4 2 ting CH O NaK.4H Com- Chemical 4 6 2 50 g/L Mechani- To Solution Concentration Operation Time Coating O plexing Species cal stirring comple- 3000 mL te reac- HCHO 15m/L Reducer 1200 rpm Mechani- tion Sensitization SnCl2.2H2O 20g/l cal Buffer 30 To ml HCl 0.5 ml/l stirring solution adjust (400 rpm) for PH NaOH pH control Wash water PH 7.0 and vacuum filtration 5 Wash water PH 7.0 and vacuum filtration 5 Mechani- Activation HCl 5.5 ml/l cal 35 Morphology of Modified -SiC 2000 ml PdCl2 0.25 g/l stirring (400 rpm) Fig. (2a) is a SEM image of -SiC particles after the sen- sitization bath. Fig. (2b) shows the qualitative analysis, indi- Wash water PH 7.0 and vacuum filtration 5 cating the presence of Sn, which was used as catalylist in the SnCl2 bath. Fig. (3a) shows the coated -SiC particles. Stirring was maintained and, as the reaction run out, the Again, elemental analysis shows the presence of Sn and Pd solution color changed until it gets a transparent appearance from the pretreatment process. On the other hand, a high (Fig. 1), as soon as the Cu from the solution was deposited amount of Cu can be seen due to the plating process. on the surface of the ceramic particles as metallic Cu. Si_C Si IDENTIFICATION IDENTIFICATION 000-05 000-05 08-213-01 08-213-01 c Sn Sn 20 KV X10, 000 1 mm 15 30 SEI 1234567 8910 Full Scale 5114 cts Cursor: 10.185 keV (4 cts) keV PYREX 10L PYREX 10L (a) (b) Fig. (2). -SiC particles without Cu: (a) SEM image, (b) field EDS. ( ) (a) b Si_C con Cobre_2 Si 000-05 08-213-01 IDENTIFICATION 000-05 08-213-01 PYREX PYREX 10L 10L Cu Cu Sn Sn C Pd Pd Sn Cu 20 KV X10, 000 1 mm 15 24 SEI 12345678910 Full Scale 894 cts Cursor: 10.205 keV (4 cts) keV ( ) ( ) c d (a) (b) Fig. (1). Evolution of the plating bath: (a) 0 min., (b) 10 min., (c) Fig. (3). Modified -SiC particles: (a) SEM image, (b) field EDS. 30 min., (d) 40 min. Fig. (4a) is an image of coated particles. From punctual The temperature of the bath was kept at 80ºC while pH EDS in three different zones (Fig. 4b), C, Si, Sn and Cu can was kept at 12.0. Table 3 summarizes the details of the plat- be found, being Cu the most abundant, with an average of ing process. 79.27% wt (Table 4). Compoforging of Al-Si Metal Matrix Composites Reinforced The Open Industrial & Manufacturing Engineering Journal, 2010, Volume 3 3 + + Spectrum 2 Spectrum 1 + Spectrum 3 Fig. (6). Model of Kim and Lee: (a) Composite (b) CuO (Cu2O) CENIM SEI 15.0kV 10mm WD 10:1mm 90mm Electron Image 1 transformation, volume and contact increase, training necks at the (a) point of contact, (c) geometry adopted to reduce the surface energy (b) Fig. (4). Cu coated -SiC particles: (a) SEM image, (b) punctual [8]. EDS. coalescence into bigger grains and forming agglomerations Table 4. Chemical Composition as Shown in figure 4b. during their growing phase. Electrochemical corrosion could also occur, forming Cu2O [10]. Element % (wt) % (at.) Morphology Of Coated Particles C 4.83 16.05 During the coating process, small microscopic particles of Cu start to adhere to the surface of -SiC, layer by layer. O 12.04 30.00 The process is then repeated until all the Cu in the solution has been deposited onto the -SiC. Additionally, it is prob- Si 2.67 3.79 able that not all the -SiC surface be coated, since the over- Cu 79.27 49.75 lapping of Cu layers could cover small pores (Fig. 7). Sn 1.19 0.40 COVER EP LAYERS 1 g 2 Total 100.00 2 1 Susbtrate Cu/-SiC Microcomposites with pore Powdered Cu/-SiC microcomposites were obtained as shown in Fig. (5). As stated before, the pH maintained in the plating bath was 12.0, even though Sharma et al. suggest an optimum of 12.5. An increase in the weight of the initial - COVER EP SiC particles of 32% was achieved. COVER EP LAYERS 1,2,3,4 g5 LAYERS g 5 1,2 3 4 3 2 1 Susbtrate with pore Fig. (7). Monolayer coating mechanism as seen in the EP process [7]. Fig. (8) evidences the globular monolayer coating proc- ess in the modified particles, as proposed by Sharma et al. [7]. Note the spherical shape of the small Cu globules on the Fig. (5). -SiC particles without coating (left) compared to the surface of the -SiC. It is also important to note that this Cu/-SiC microcomposite (right).
Details
-
File Typepdf
-
Upload Time-
-
Content LanguagesEnglish
-
Upload UserAnonymous/Not logged-in
-
File Pages6 Page
-
File Size-