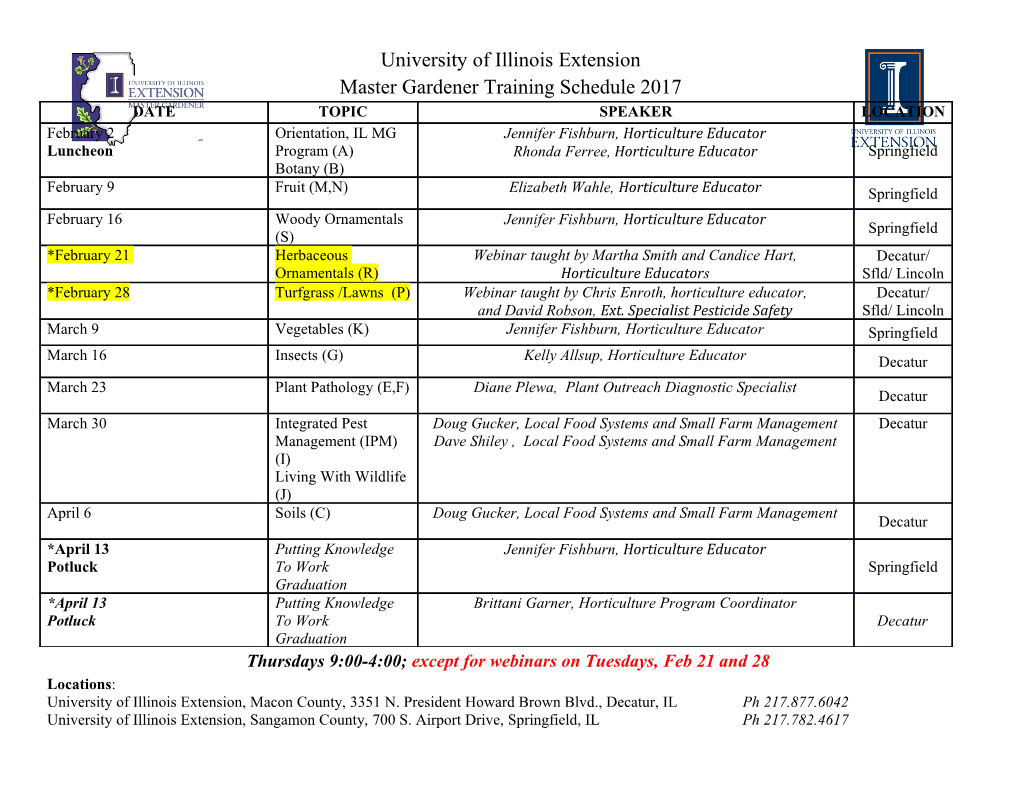
materials Article High Strength X3NiCoMoTi 18-9-5 Maraging Steel Prepared by Selective Laser Melting from Atomized Powder Angelina Strakosova *, Jiˇrí Kubásek, Alena Michalcová, Filip Pr ˚uša,Dalibor Vojtˇechand Drahomír Dvorský Department of Metals and Corrosion Engineering, Faculty of Chemical Technology, University of Chemistry and Technology, Technická 5, Praha 6—Dejvice, 166 28 Prague, Czech Republic; [email protected] (J.K.); [email protected] (A.M.); [email protected] (F.P.); [email protected] (D.V.); [email protected] (D.D.) * Correspondence: [email protected] Received: 21 November 2019; Accepted: 10 December 2019; Published: 12 December 2019 Abstract: Maraging steels are generally characterized by excellent mechanical properties, which make them ideal for various industrial applications. The application field can be further extended by using selective laser melting (SLM) for additive manufacturing of shape complicated products. However, the final mechanical properties are strongly related to the microstructure conditions. The present work studies the effect of heat treatment on the microstructure and mechanical properties of 3D printed samples prepared from powder of high-strength X3NiCoMoTi 18-9-5 maraging steel. It was found that the as-printed material had quite low mechanical properties. After sufficient heat treatment, the hardness of the material increased from 350 to 620 HV0.1 and the tensile yield strength increased from 1000 MPa up to 2000 MPa. In addition, 3% ductility was maintained. This behavior was primarily affected by strong precipitation during processing. Keywords: maraging steel; atomized powder; selective laser melting; heat treatment; precipitation hardening 1. Introduction Selective laser melting (SLM) is one of the best-known methods of additive production of materials. In everyday life, the most commonly encountered name for this method is 3D printing [1]. The aim of this method is to produce a three-dimensional metal part. The principle of manufacturing these parts lies in the use of a laser for melting metallic powders and subsequent layer-by-layer application of these powders. Due to the high cooling rate, rapid solidification and material transformations occur in the material. The advantage of this method is that the product is already made into the desired shape and size without the necessity for secondary machining [1]. The most useful applications of SLM technology are found in medicine, aviation, the automotive industry, and also in the work of architects [2]. The main advantages of 3D printing over conventional methods of manufacturing metallic materials are as follows. First, it provides the ability to produce components with various complex surface and volume shapes. This means that details can be produced during a single operation. Secondly, it requires minimal surface machining of the finished product and thus minimizes waste [1]. Third, SLM technology allows us to work with a wide range of materials. The most extensively studied are steels, Al alloys, Ti alloys, and Ni superalloys [1,3]. The microstructure of 3D printed material is almost non-porous, reaching up to 99.9% of theoretical density [1]. It is also very different from the microstructure of the materials produced by other methods. Thanks to the high cooling rate and Materials 2019, 12, 4174; doi:10.3390/ma12244174 www.mdpi.com/journal/materials Materials 2019, 12, 4174 2 of 10 Materials 2019, 12, x FOR PEER REVIEW 2 of 10 solidification of the alloy during the SLM process, we get a material with a very fine-grained cell microstructure.microstructure. Grain Grain size size reduction reduction has has a a beneficial beneficial effect effect on on the the mechanical mechanical properties properties of of 3D 3D printed printed productsproducts [4–8]. [4–8]. MaragingMaraging steels steels are are widely widely used used in in the the aerospace aerospace in industry.dustry. Also, Also, they they are are widely widely used used in in tooling tooling applicationsapplications and and in in the the production production of ofweapons. weapons. Maraging Maraging steels steels are also are well-known also well-known thanks thanks to their to excellenttheir excellent mechanical mechanical properties. properties. The Themost most import importantant properties properties are are very very high high hardness, hardness, good good weldability,weldability, high high ductility, ductility, and easy machinability after solution annealing. Spatial Spatial stability stability during during agingaging is is one one more more positive positive feature feature of of the the maragi maragingng steels steels [8–13]. [8–13]. Their Their properties properties and and range range of of applicationsapplications are are one one of of the the reasons reasons for for the the interest interest in in their their production production by by using using modern modern technologies, technologies, includingincluding 3D 3D printing. printing. MaragingMaraging steelssteels exertexert these these very very good good mechanical mechanic propertiesal properties after theafter application the application of heat treatment of heat treatmentinvolving involving solution annealing solution annealing and aging. and The aging. first stateThe first after state quenching after quenching is the martensitic is the martensitic structure structureof the material. of the material. This structure This structure may be causedmay be by ca diusedfferent by different means. Inmeans. maraging In maraging steels, the steels, creation the creationof martensite of martensite is supported is supported by the highby the Ni high content Ni co inntent an alloy.in an Inalloy. contrast In contrast to this, to in this, other in steels,other steels,the martensitic the martensitic structure structure is due tois due a relatively to a relati highvely carbon high content.carbon content. Aging at Aging a temperature at a temperature between between480 ◦C to 480 510 °C◦C to causes 510 °C intermetallic causes intermetallic precipitation precip [13itation,14]. Several [13,14]. phases Several were phases identified were identified in maraging in maragingsteels like steels Ni3(Ti, like Mo) Ni3(Ti, [13], Mo) Ni3 [13],X (X Ni= 3Ti,X (X Al, = Ti, Mo) Al, [10 Mo)], (Fe, [10], Ni, (Fe, Co) Ni,3 (Ti,Co)3 Mo),(Ti, Mo), (Fe, (Fe, Ni, Co)Ni, Co)3(Mo,3(Mo, Ti), Ti),and and (Fe, (Fe, Ni, Ni, Co) Co)7Mo7Mo6 [156 [15].]. SeveralSeveral major major works works have have been been carried carried out out to to get get a a better better idea idea of of the the prop propertieserties of of X3NiCoMoTi X3NiCoMoTi 18-9-518-9-5 maraging maraging steel steel made made by by 3D 3D printing. printing. Kempen Kempen et et al. al. [1] [1] investigated investigated how how impact impact and and tensile tensile propertiesproperties depend depend on on aging aging treatment treatment and and process process parameters. parameters. Tensile, Tensile, fracture, fracture, and and fatigue fatigue crack crack growthgrowth of of maraging maraging steel steel was was st studiedudied by by Suryawanshi Suryawanshi et et al. al. [4]. [4]. Some Some researchers researchers [7,16] [7,16] have have investigatedinvestigated the the effect effect ofof didifferentfferent heatheat treatments treatments on on microstructure microstructure and and mechanical mechanical properties. properties. In In all allthe the work work mentioned mentioned above, above, the the aging aging treatment treatment significantly significantly improvedimproved thethe properties due to to the the formationformation of of precipitates. precipitates. However, However, only only limited limited information information is is known known about about the the precipitates precipitates which which formform during during the the treatment treatment of of 3D 3D printed printed steel. steel. For For example, example, the the formation formation of of a a Ni3X Ni3X (X (X == Ti,Ti, Al, Al, Mo) Mo) precipitatesprecipitates after after heat heat treatment treatment wa wass described described by references [10,15]. [10,15]. TheThe aim ofof thisthis work work is tois investigateto investigate the impactthe impact of the of 3D the printing 3D printing process process and two and heat two treatment heat treatmentmodes on modes microstructure on microstructure and mechanical and mechanical properties properties X3NiCoMoTi X3NiCoMoTi 18-9-5 maraging 18-9-5 steel.maraging steel. 2.2. Materials Materials and and Methods Methods SamplesSamples in in the the shape shape of of a a dog dog bone bone (Figure (Figure 1.)1) werewere producedproduced byby 3D3D printingprinting on SLM solution 280HL280HL (NETME Center,Center, Brno, Brno, Czech Czech Republic) Republic) from from the powder the powder X3NiCoMoTi X3NiCoMoTi 18-9-5 alloy.18-9-5 The alloy. chemical The chemicalcomposition composition (Table1) was(Table found 1) was using found XRF usin analysisg XRF on analysis spectrometer on spectrometer ARL 9400. ARL 9400. Figure 1. Dimensions of 3D-printed sample for a tensile test. Figure 1. Dimensions of 3D-printed sample for a tensile test. Table 1. Chemical composition of X3NiCoMoTi 18-9-5 maraging steel. Table 1. Chemical composition of X3NiCoMoTi 18-9-5 maraging steel. Element Ni Co Mo Ti C Al Cr Mn Si Fe Element Wt/%Ni 19Co 9.3Mo 5 0.64Ti 0.03C 0.06Al 0.08Cr 0.04 Mn 0.07 Bal.Si Fe Wt/% 19 9.3 5 0.64 ≤≤0.03 0.06 0.08 0.04 0.07 Bal. The powder morphology structure and size distribution are shown in Figure 2. Particle size analysis was performed using a scanning electron microscope (TESCAN VEGA 3 LMU, Brno, Czech Republic) and the ImageJ program. Materials 2019, 12, 4174 3 of 10 The powder morphology structure and size distribution are shown in Figure2. Particle size analysis was performed using a scanning electron microscope (TESCAN VEGA 3 LMU, Brno, Czech Republic) and theMaterials ImageJ 2019, 12 program., x FOR PEER REVIEW 3 of 10 b) 65 60 55 50 45 40 35 30 Count 25 20 15 10 5 0 0 5 10 15 20 25 30 35 40 45 50 55 Diameter, µm Figure 2.
Details
-
File Typepdf
-
Upload Time-
-
Content LanguagesEnglish
-
Upload UserAnonymous/Not logged-in
-
File Pages10 Page
-
File Size-