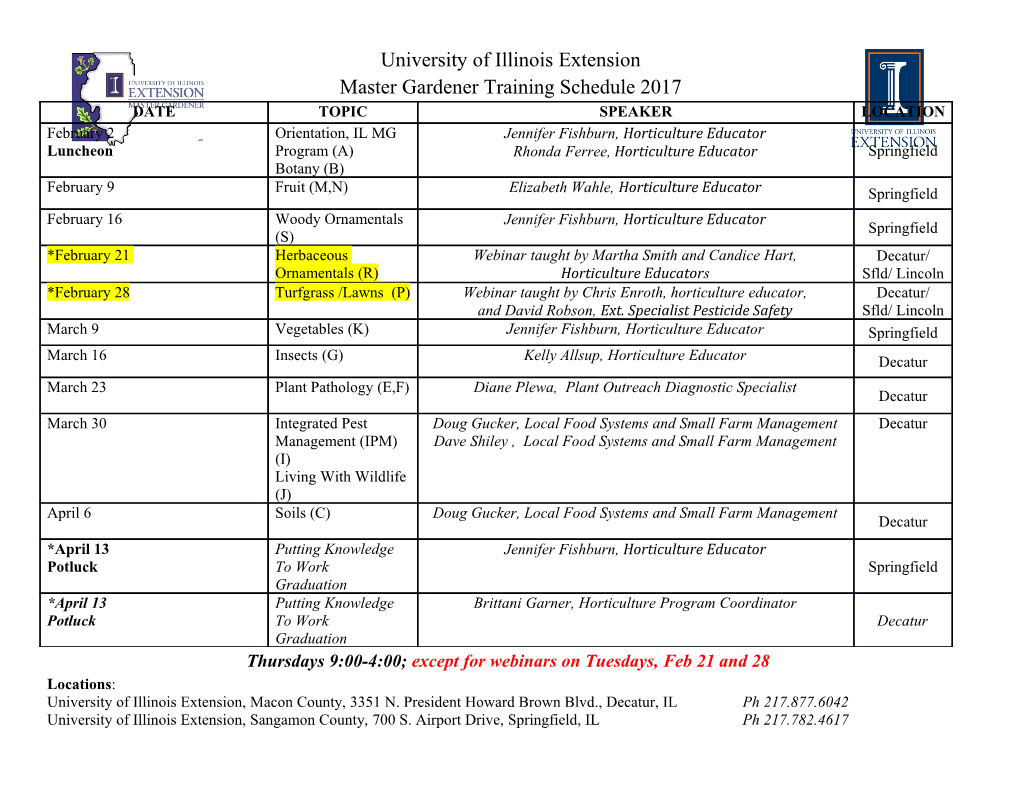
VTT WORKING PAPERS 187 Päivi Aakko-Saksa, Päivi Koponen, Johanna Kihlman, Matti Reinikainen, Eija Skyttä, Leena Rantanen-Kolehmainen & Ari Engman Biogasoline options for conventional spark-ignition cars ISBN 978-951-38-7529-9 (URL: http://www.vtt.fi/publications/index.jsp) ISSN 1459-7683 (URL: http://www.vtt.fi/publications/index.jsp) Copyright © VTT 2011 JULKAISIJA – UTGIVARE – PUBLISHER VTT, Vuorimiehentie 5, PL 1000, 02044 VTT puh. vaihde 020 722 111, faksi 020 722 4374 VTT, Bergsmansvägen 5, PB 1000, 02044 VTT tel. växel 020 722 111, fax 020 722 4374 VTT Technical Research Centre of Finland, Vuorimiehentie 5, P.O. Box 1000, FI-02044 VTT, Finland phone internat. +358 20 722 111, fax +358 20 722 4374 Series title, number and report code of publication VTT Working Papers 187 VTT-WORK-187 Author(s) Päivi Aakko-Saksa, Päivi Koponen, Johanna Kihlman, Matti Reinikainen, Eija Skyttä, Leena Rantanen-Kolehmainen & Ari Engman Title Biogasoline options for conventional spark-ignition cars Abstract The purpose of this study is to explore feasible gasoline biocomponents supplemen- tary to ethanol, and to assess their exhaust emissions performance. Although ethanol is the dominant liquid biofuel globally, technical restrictions limit its use in convention- al gasoline cars to 10–15 v/v% (bio-energy 7–10%). Since current conventional cars will continue to take the major share of gasoline car fleets for at least the next 10–20 years, it is necessary to establish and assess biocomponent options for them. Today, higher ethanol blending ratios are possible only with the use of flexible fuel vehicle (FFV) technology. The European Union requires renewable energy to have at least a 10% share of transport energy by 2020, and even higher shares are being attempted regionally. Biocomponents alternative or supplementary to ethanol are therefore desired in the gasoline pool. Interesting gasoline biocomponents are bioethers, biobutanols and biohydrocarbons. Oxygenated and non-oxygenated biocomponents can be combined to increase the bio-share of gasoline. This study consists of a literature review of the production processes, and an eval- uation of the end-use performance of gasoline biocomponents. The results show that there are many options for increasing the bio-energy content of gasoline to 20% or more without increasing the gasoline oxygen content to a higher level than can be tolerated by E10-compatible gasoline cars. ISBN 978-951-38-7529-9 (URL: http://www.vtt.fi/publications/index.jsp) Series title and ISSN Project number VTT Working Papers 1459-7683 (URL: http://www.vtt.fi/publications/index.jsp) Date Language Pages December 2011 English 200 p. + app. 9 p. Name of project Commissioned by TransEco – Korkeaseosteiset biokomponentit Ministry for Employment and the Economy henkilöautojen polttoaineisiin Keywords Publisher biogasoline, ethanol, butanol, NExBTL, MTG, FT, VTT Technical Research Centre of Finland exhaust emissions, CO, HC, NOX, PM, particles, P.O. Box 1000, FI-02044 VTT, Finland aldehydes, 1,3-butadiene, benzene, PAH, Ames Phone internat. +358 20 722 4520 Fax +358 20 722 4374 Executive summary The purpose of this study is to explore feasible gasoline biocomponents supplementary to ethanol, and to assess their exhaust emissions performance. Although ethanol is the dominant liquid biofuel globally, technical restrictions limit its use in conventional gasoline cars to 10–15 v/v% (bio-energy 7–10%). However, cur- rent conventional cars will continue to take the major share of gasoline car fleets for the next 10–20 years at least, and it is therefore necessary to establish and assess biocom- ponent options for them. Today, higher ethanol blending ratios are possible only with the use of flexible fuel vehicle (FFV) technology. The European Union requires renewable energy to have at least a 10% share of transport energy by 2020, and even higher shares are being attempted regionally. Bio- components alternative or supplementary to ethanol are therefore desired in the gasoline pool. Interesting gasoline biocomponents are bio-ethers, biobutanols and biohydrocar- bons. Oxygenated and non-oxygenated biocomponents can be combined to increase the bio-share of gasoline. This study consists of (a) a literature review of the production processes, and (b) an evaluation of the end-use performance of gasoline biocomponents, based on the litera- ture and experimental work. PROCESS OPTIONS The current interest in renewable fuels has led to a substantial investment in the re- search, development and commercialization of biofuel processes. For biogasoline, ef- forts have been devoted almost solely to ethanol. However, there are several pathways other than fermentation towards biocomponents for gasoline (Figure 1). This study focused on the thermochemical routes for the production of gasoline com- ponents from biomass. Traditional fermentation routes, as well as etherification, are described briefly as references. 5 Isobutylenes isoamylenes Ethanol, Sugars Fermentation butanol Starches Enzyme conv. Synthesis Ethers Acid or enzyme hydrolysis Lignin, Gasoline Cellulose & Direct conversion Biohydro- Hemisellulose Fischer-Tropsch carbons Gasification MTG Pyrolysis Oxygenate synthesis Natural Hydrotreatment oils and fats Refinery processes, e.g. FCC Unconventional Alcohol oil mixtures Figure 1. Overview of biogasoline production options (Aakko-Saksa, based on Holmgren et al. 2007, Huber et al. 2006). Solid, liquid or gaseous hydrocarbon-rich feed- Bio-oxygenates, e.g. ethanol, stock can be gasified to synthesis gas (CO and H2), biobutanol, higher alcohols, bio- which can be further refined to higher value prod- ethers. ucts. The most prominent thermochemical technol- Biohydrocarbons via gasifica- tion/FT or MTG, hydrotreatment ogies for gasoline production from fossil feed- (HVO), refinery co-processing, stocks had already been developed by the 1980s. for example. Biomass-based processes, however, require addi- tional steps such as more thorough gasification gas cleaning. ExxonMobil MTG: gasification and methanol–DME–gasoline Thermochemical pathways for producing gaso- synthesis. line from synthesis gas include the methanol-to- o Fossil natural gas-based gasoline (MTG) and Fischer-Tropsch liquefaction MTG plant in New Zealand routes. New processes are also under development. 1986–1996. o Fossil coal-based MTG plants under consideration. Methanol to gasoline (MTG) Haldor Topsøe TIGAS: The methanol and DME synthesis are combined. ExxonMobil MTG process – Mobil (currently Exx- o Fossil natural gas-based onMobil Research and Engineering Company) demonstration in 1980s. developed their ZSM-5-catalyzed, fixed-bed MTG o Biomass wood-based process in the 1970s. The process included gasifi- demonstration in Des Plaines, USA. cation to synthesis gas, the methanol synthesis, 6 methanol dehydration to form dimethylether (DME), and further dehydration in the MTG synthesis to form a variety of hydrocarbons. The first industrial-scale natural gas-based MTG plant operated in New Zealand from 1986 to 1996, with production up to approxi- mately 800 000 t/a of gasoline. The conversion of synthesis gas to methanol was approx- imately 75%, and the methanol to gasoline conversion 100%. Approximately 85–90% of the product hydrocarbons were suitable gasoline components. The MTG process is exo- thermic, and therefore requires effective heat removal. The catalyst requires frequent re- generation, and is eventually destroyed. An additional distillation step is required to sepa- rate methanol from water. However, the process does produce a high yield of sulphur- and nitrogen-free gasoline. The energy efficiency of the process is 50–60% from natural gas and higher if heat is utilized. The fluidized-bed MTG process was demonstrated in Wes- seling in 1982–1984. Several operators have announced their plans to utilize ExxonMobil's MTG technolo- gy in fossil coal-to-liquid processes. These include Shanxi Jincheng Anthracite Coal Mining Co. Ltd. (JAM), DKRW Advanced Fuels, and Synthesis Energy Systems. Haldor Topsøe’s MTG process – Haldor Topsøe’s integrated gasoline synthesis pro- cess (TIGAS) produces gasoline from methanol using ExxonMobil’s HZSM-5 catalyst. However, in the TIGAS process, the methanol and DME syntheses are combined in a single synthesis loop. Less steam and a lower pressure are required in the TIGAS pro- cess than in the MTG process. A natural gas-based TIGAS process was demonstrated in 1983–1986 in Houston. A biomass-based TIGAS demonstration plant in Des Plaines, USA, start-up in 2012, will convert wood (25 tpd) to gasoline. In future, Topsøe plans to build industrial plants that will use more than 1 000 tpd of wood. The energy effi- ciency of the wood-based TIGAS process is about 60% and higher if heat is utilized. Topsøe’s partners in the project include UPM Kymmene. Lurgi’s MtSynthesis is one option to produce hydrocarbons from methanol, gasoline as a side product. Fischer-Tropsch process (FT) One route for converting a variety of feedstocks to Gasification and Fischer- Tropsch (FT) liquefaction liquid fuels is a combination of gasification and Fisch- can be optimized for gasoline, er-Tropsch liquefaction. Currently, many companies diesel or even methane. are utilizing or planning to utilize Fischer-Tropsch o Fossil coal-based gaso- line is produced by Sasol technology in diesel production from coal, natural gas in South Africa (up to or biomass. Only Sasol has an FT-based production 875 000 tons/a). line specially designed for gasoline production. o Fossil natural
Details
-
File Typepdf
-
Upload Time-
-
Content LanguagesEnglish
-
Upload UserAnonymous/Not logged-in
-
File Pages212 Page
-
File Size-