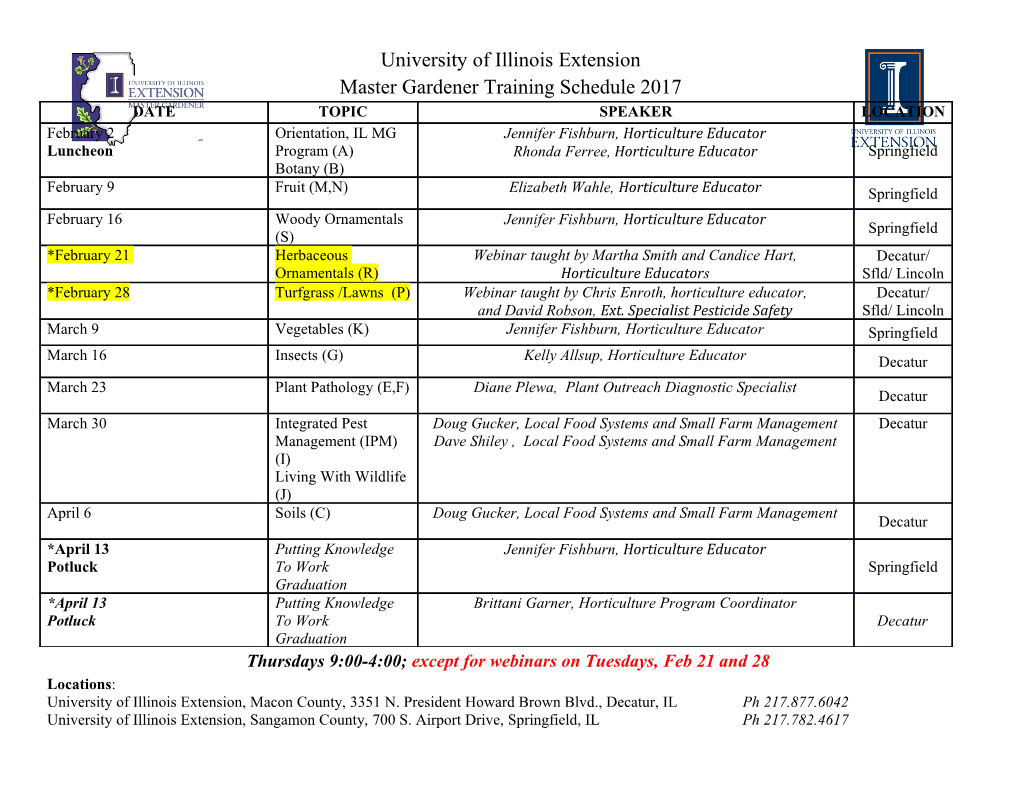
Review Status of Pure Electric Vehicle Power Train Technology and Future Prospects Abhisek Karki 1,2,* , Sudip Phuyal 3,4,* , Daniel Tuladhar 1, Subarna Basnet 5 and Bim Prasad Shrestha 1 1 Department of Mechanical Engineering, Kathmandu University, Dhulikhel 45200, Nepal; [email protected] (D.T.); [email protected] (B.P.S.) 2 Aviyanta ko Karmashala Pvt. Ltd., Bhaktapur 44800, Nepal 3 Department of Electrical and Electronics Engineering, Kathmandu University, Dhulikhel 45200, Nepal 4 Institute of Himalayan Risk Reduction, Lalitpur 44700, Nepal 5 International Design Center, Massachusetts Institute of Technology, Cambridge, MA 02139, USA; [email protected] * Correspondence: [email protected] (A.K.); [email protected] (S.P.) Received: 14 July 2020; Accepted: 10 August 2020; Published: 17 August 2020 Abstract: Electric vehicles (EV) are becoming more common mobility in the transportation sector in recent times. The dependence on oil as the source of energy for passenger vehicles has economic and political implications, and the crisis will take over as the oil reserves of the world diminish. As concerns of oil depletion and security of the oil supply remain as severe as ever, and faced with the consequences of climate change due to greenhouse gas emissions from the tail pipes of vehicles, the world today is increasingly looking at alternatives to traditional road transport technologies. EVs are seen as a promising green technology which could lead to the decarbonization of the passenger vehicle fleet and to independence from oil. There are possibilities of immense environmental benefits as well, as EVs have zero tail pipe emission and therefore are capable of curbing the pollution problems created by vehicle emission in an efficient way so they can extensively reduce the greenhouse gas emissions produced by the transportation sector as pure electric vehicles are the only vehicles with zero-emission potential. However, there are some major barriers for EVs to overcome before totally replacing ICE vehicles in the transportation sector and obtain appreciable market penetration. This review evaluates the technological aspects of the different power train systems of BEV technology and highlights those technological areas where important progress is expected by focusing on reviewing all the useful information and data available on EV architecture, electrical machines, optimization techniques, and its possibilities of future developments as green mobility. The challenges of different electric drive trains’ commercialization are discussed. The major objective is to provide an overall view of the current pure electric vehicle powertrain technology and possibilities of future green vehicle development to assist in future research in this sector. Keywords: electric vehicle; control algorithms; electric propulsions; transmission; optimization; future EV 1. Introduction An electric vehicle (EV) is a road vehicle which involves motion with electric propulsion. The electric vehicle utilized the features of traction provided by an electric motor consuming the portable and electro chemical energy source. The electrochemical energy conversion linkage system between the vehicle energy source and the wheels is the powertrain of the vehicle. The powertrain of an electric vehicle has electrical as well as mechanical linkage. Passenger vehicles constitute an integral Appl. Syst. Innov. 2020, 3, 35; doi:10.3390/asi3030035 www.mdpi.com/journal/asi Appl. Syst. Innov. 2020, 3, 35 2 of 28 part of our daily life, but due to tail pipe emission of conventional internal combustion vehicles (ICEVs), these vehicles generate urban air pollution causing greenhouse gas effect which leads to global warming [1,2]. Air quality around the globe has been found to be deteriorating and the emissions from the vehicles have been one of the main sources. The increase in vehicular emissions is because of growing population, urbanization, and socio-economic development and the resulting usage of vehicles [3,4]. The fuel engines emit the greenhouse gases like nitrous oxides (N2O), methane (CH4), carbon dioxide (CO2), and many pollutants such as oxides of nitrogen (NOx), sulfur dioxide (SO2), hydrocarbon (HC), and particulate matter (PM) [5–11]. The transport sector contributed 23–26% of the world’s CO2 emissions and 74% on-road CO2 emissions in 2004 and 2007 respectively [12]. Increasing emissions levels continue due to aging vehicles, a lack of adequate maintenance of road vehicles, high traffic congestion, fuel adulteration, and poor road infrastructure. Although heavy-duty diesel vehicles (HDDV) represent a lesser proportion, their emissions contribute significantly to air pollution problems [13]. Road vehicle emissions have been partly contributing to acid deposition, stratospheric ozone depletion, and climate change [14]. The developed countries adopted strong legislation to reduce the automobile emissions and enhancing better air quality [15]. The concern about climate change has reached a high level and has triggered the agreements between EU countries to drop their emissions by 80% by 2050 to stabilize atmospheric CO2 at 450 ppm so that they can work out to keep global warming under 2 ◦C. The effort to drop the emission and global warming has been shared between different sectors, and the road transport sector is expected to reduce its emissions by 95% [16–20]. This trend also exists in other countries like Brazil, for one which through Regulations 418/2011 and 315/2002 set new emissions limits for CO (carbon monoxide), HC (hydrocarbon), and NOx (nitric/nitrogen oxides) [21]. According to Steinberg [22], the cost of reducing each gram of CO2/km has already risen from $17.03 (¿13) to $65.50 (¿50) before the 2020 target of 159 g of CO2/km has even been reached [23]. Pure electric vehicle has incomparable advantage over conventional ICE vehicles in terms of energy conservation, zero emissions, and ensuring oil supply security, etc., leading to attraction of wide range of automobile manufacturers and governments. The major advantage of electric mobility over ICE vehicles are their ability to conserve energy, zero tail pipe emission, independent from oil supply [24,25]. Figure1 describes key parts of the di fferent subsystems and their contribution to the overall system. Synergy of all these systems that helps to run electric vehicles. Pure electric vehicle or battery electric vehicles utilize the electrical energy stored in batteries as a source of energy and their motor drive system translates output power of battery into rotational energy of wheel, so it can drive the operation of the electric vehicle [26–31]. The working principle of pure electric vehicle utilizes use of an electric machine (electric motor) utilizing an energy source (battery) by replacing the internal combustion engine (ICE) and the associated fuel tank, and the energy source of the vehicle gets recharged as they are used to regain their energy source [32–35]. Different subsystems combine in EVs like that of internal combustion engine powered vehicles keeping the fossil fuel engine and tail pipe aside. Interaction and connection of these subsystems makes the EV work, and multiple technologies can be employed to operate the subsystems. Basically, two different approach are followed while producing electric vehicles—most EVs get converted from existing designs based upon traditional ICE vehicles styling [36–38]. Engineers have the freedom to coordinate and integrate various EV subsystems so that the subsystem can work together efficiently when the EVs are developed using ground up design methodology [39]. As the packaging requirements of an electric car are different because of an empty space that can be used as baggage storage. This overall body system could be analyzed to improve the outcome of the electric car design process. To make mass appeal that an EV is really different from as an ICE vehicle, the elements in the vehicle body should be designed as per the ‘EV technology’ that has been used and with the progressive development, further improvement should be expressed in the formal design [40–45]. Appl. Syst. Innov. 2020, 3, 35 3 of 28 Appl. Syst. Innov. 2020, 3, x FOR PEER REVIEW 3 of 28 FigureFigure 1. DifferentDifferent subsystems and their inte interactionraction with electric vehicles [36]. [36]. TheDifferent overall subsystems performance combine of EVs in can EVs be like improved that of internal by utilizing combustion design concepts engine powered like light vehicles weight bodykeeping structure, the fossil low fuel drag engine aerodynamic and tail bodypipe design,aside. Interaction and lower rollingand connection resistance. of The these vehicle subsystems weight hasmakes a direct the EV impact work, on and the multiple range and technologies gradeability can performance. be employed Lightweight to operate the materials subsystems. like aluminum, fiberglass,Basically, or carbon two different fiber can approach be utilized are to bodyfollowed and chassiswhile producing structure so electric as to reduce vehicles—most the curb weight EVs get of theconverted vehicle. from Improving existing the designs body aerodynamicbased upon traditio by optimizingnal ICE thevehicles airflow styling of the [36–38]. vehicle Engineers body can helpshave tothe reduce freedom the to aerodynamic coordinate resistance.and integrate Tires various with lowerEV subsystems rolling resistance so that helpthe subsystem in reducing can running work resistancetogether efficiently and help inwhen dynamic the EVs modeling are
Details
-
File Typepdf
-
Upload Time-
-
Content LanguagesEnglish
-
Upload UserAnonymous/Not logged-in
-
File Pages28 Page
-
File Size-