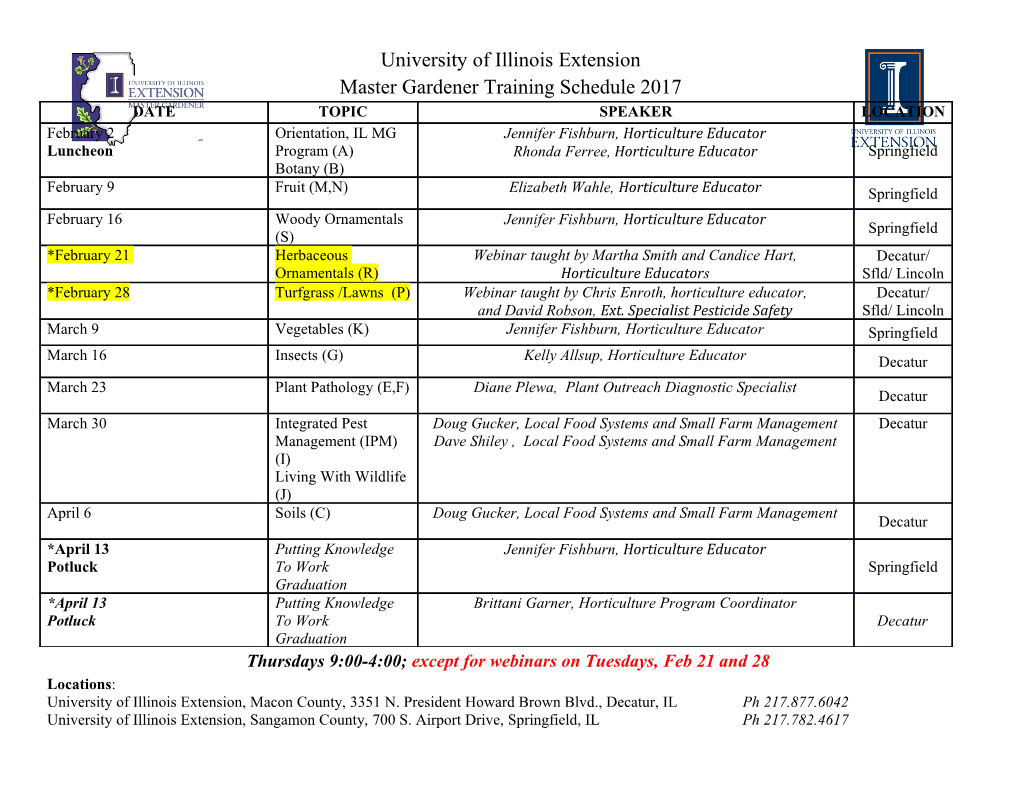
Robotics and Remote Systems Topics 837 Performing Neutron Imaging of Mock Uranium Fuel Rods with a Robotic Manipulator Joseph Hashem University of Texas at Austin, 1 University Place R9925, Austin, TX 78752 Los Alamos National Laboratory, P.O. Box 1663, Los Alamos, NM 87545 [email protected] for advanced non-destructive imaging abilities and INTRODUCTION applications. Robotic systems have been used and theorized for a This paper describes an effort under way at the wide variety of imaging purposes, from medical imaging University of Texas at Austin (U.T. Austin) with to tomography using dual-arm robotic systems [2]. In collaboration from Los Alamos National Laboratory depth repeatability tests have been performed on the (LANL) to implement a robotic manipulator as the motion Motoman SIA5 robot in [3] and demonstrate that the control system for neutron imaging tasks. This effort robot’s repeatability is sufficient for these types of includes taking robotic technologies and using them to imaging tasks. automate non-destructive imaging tasks in nuclear facilities. To illustrate the advantages of using a robotic DESCRIPTION OF THE ACTUAL WORK manipulator with neutron imaging, mock-up depleted uranium fuel rods, each consisting of five pellets prepared Imaging Source and System from urania (UO2) powder, were characterized by thermal neutron radiography. The neutron imaging was performed in beam port 3 To simulate cracks and voids resulting from at U.T. Austin’s TRIGA Mark II research reactor. In this irradiation and burn-up in a fuel pin, tungsten and beam port, there is a thermal neutron flux of 5.3x106 gadolinium inclusions were embedded in the mock-up n/cm2/s and thermal-to-epithermal ratio of 8.1x104 ± 10% pellets. A Motoman SIA5 7 Degree Of Freedom (DOF) n/cm2/s at a reactor power of 950 kW. The neutrons in industrial manipulator [1] handled the fuel rods and this beam port are cooled, due to the function of a beam provided advanced and flexible motion capabilities and wave guide, to an effective beam temperature of 39 ± 6 K. imaging techniques that would be difficult to achieve with A scintillator-mirror-camera system was utilized to only linear and rotary motion stages. The robotic acquire digital radiographs. The scintillator used was a manipulator provides the following capabilities and copper, aluminum, and gold doped 6LiF ZnS neutron advantages over ordinary motion stages with regards to detection screen [4]. The reaction that occurs is 6Li + n → imaging and motion control: autonomously image He + triton + 4.8 MeV, where the ejected triton interacts multiple samples without worker intervention, computed with phosphor in the scintillator to create a scintillation tomography scanning, helical scanning, orientation of the event. The camera used was an Andor iXon+ EMCCD, sample in 3D space, reduced radiation dose to workers, with a 90 mm macro lens, 1004 x 1002 pixel size, and an and increased sample throughput. effective pixel pitch of 35 μm [5]. A stainless steel The ultimate goal of this research and development enclosure, along with lead bricks, surrounded the camera, work is to implement robotics for automation in non- mirror, and scintillator to shield against x-ray hits and destructive imaging applications. The tasks involved background noise. The experimental setup is shown in required the precision and repeatability of traditional Figure 1. motion stages and the flexibility made possible by the advanced motion planning capabilities of the robotic manipulator. Another goal of this effort is the characterization of irradiated fuel pins or even spent fuel, as well as offer better guidance for expensive destructive examination of irradiated fuel pins by the non-destructive evaluation techniques. By imaging fuel rods, one can see the effect of the development of irradiation and burn-up damage in nuclear fuel over time. To date, the integrated system has successfully demonstrated imaging of the mock-up uranium fuel rods with the necessary precision and repeatability. These early demonstrations serve as a proof-of-concept that flexible automation can be valuable Transactions of the American Nuclear Society, Vol. 112, San Antonio, Texas, June 7–11, 2015 838 Robotics and Remote Systems Topics 235 Fission Reaction Rate of U = φNσf VU (1) where φ is the thermal neutron flux (5.3x106 n/cm2/s), N 3 is the atom density (atoms/cm ), VU is the volume of the 235 U in fuel pellets and σf is the thermal fission cross- section of 235U (5.82x10-22 cm2). A neutron activation analysis was performed looking at the fuel pellets, fuel rod cladding, beam sensitivity indicator, robotic arm, and gripper. The elemental breakdown of each of these components, along with their masses, was determined. It was determined that there was no neutron activation risk Fig. 1. Photograph of experimental setup with robot of concern for this work. picking up first of three fuel rods to image (left) and robot bringing second of three fuel rods into the neutron beam Robotic Software for imaging (right). The Robot Operating System (ROS) [7], which is a Mock-Up Depleted Uranium Fuel Rods flexible framework for writing robot software, was used for motion planning of the robot as well as a tool for The UO2 is made from depleted uranium (d-UO2 facilitating interprocess communication between the powder). The uranium content is 99.648% 238U, 0.002% imaging acquisition device and the robotic manipulator. 234U, 0.35% 235U, and < 0.001% 236U. The tungsten is ROS is a peer-to-peer system in which system metallic tungsten in natural isotopic composition. The fuel components run as nodes on a distributed network. These pellets are enclosed in a 304 stainless steel tube [6]. nodes interact with each other through a standardized Figure 2 illustrates the difference in neutron attenuation messaging system. This provides a strong separation coefficients for the main components in the fuel pellets. between the interface and implementation that simplifies The neutron energy in the beam port is 3.3.x10-3 eV, due code reuse and collaborative system development. ROS to cooling of the neutrons by the beam wave guide. At also provides visualizations of the system components as this energy, gadolinium’s neutron attenuation coefficient well as the communication and interdependencies. is roughly three orders of magnitude greater than that of ROS includes several simulation capabilities. RViz tungsten, and tungsten’s neutron attenuation coefficient is [8] (Figure 3) was used to simulate the testing roughly one order of magnitude greater than that of environment and evaluate proposed trajectories for depleted uranium. Materials with higher attenuation collision detection and kinematic feasibility. coefficients will attenuate neutrons more than materials with lower attenuation coefficients. Fig. 3. RViz simulation of example radiography application. Fig. 2. Neutron attenuation coefficients of the main The architecture ensures that the paths proposed components of the fuel pellets as a function of neutron by the operator are collision free and kinematically energy. feasible. Thus safety and robustness are assured without adding a significant burden on the operator who may not The depleted UO2 fuel rod fission reaction rate was be a robotics expert. calculated to be 420 neutrons/sec, using the following equation: Transactions of the American Nuclear Society, Vol. 112, San Antonio, Texas, June 7–11, 2015 Robotics and Remote Systems Topics 839 EXPERIMENTS AND RESULTS Neutron imaging consisted of a radiograph of five fuel rods. The focus is on the fuel pellet region with various exposure times (5-10 min.). Multiple experiments were conducted including a vibration analysis (i.e. comparison of the resulting radiograph with the robot holding and not holding a fuel rod), a repeatability test, a computed tomography scan, a helical scan, and radiographs of the fuel rods at various orientations. A beam sensitivity indicator was imaged first in order Fig. 4. Neutron transmission image of the sensitivity to qualitatively determine the relative quality of indicator. The darker regions indicate areas with higher radiographic images produced by direct, thermal neutron neutron attenuation coefficients. radiographic examination (see Figure 4) [9]. The sensitivity indicator is constructed of cast acrylic resin (methyl methacrylate), lead, and aluminum. It provides a measure of spatial resolution by means of gaps formed by the varying thicknesses of aluminum spacers between plastic supports. Images of the holes in plastic shims give a measure of radiographic contrast and resolution by means of images of small holes as differing percentages of material thickness penetrated. The neutron radiographs of the five fuel rods are shown in Figure 5. The process for acquiring these images was the robot picked up a fuel rod, brought the fuel rod into the beam path, acquired an image, placed the fuel rod Fig. 5. Neutron transmission image of the five pellet back down, picked up the next fuel rod, and repeated assemblies. The white oval indicates a void, the black these steps until all fuel rods were imaged. oval indicates a gadolinium inclusion, and the red oval The vibration test consisted of a radiograph taken indicates a tungsten inclusion. The spring is seen in the while the robot was holding the fuel rod with the robot’s top of each assembly. servos on and another radiograph taken with the fuel rod placed on a flat surface, with an exposure time of 5 min. Comparing the two cases in Figure 6 (focusing on the circled regions), one can see that blurriness is not introduced when the robot is holding the part, meaning that no significant vibration is introduced when the robot is powered on. A repeatability test was also performed, which consisted of taking an image with the robot holding the fuel rod in a specified location in the beam, moving the robot away from the beam, bringing the robot back to the same specified location, taking another image, and then comparing the two images using MATLAB’s Image Processing Toolbox [10].
Details
-
File Typepdf
-
Upload Time-
-
Content LanguagesEnglish
-
Upload UserAnonymous/Not logged-in
-
File Pages4 Page
-
File Size-