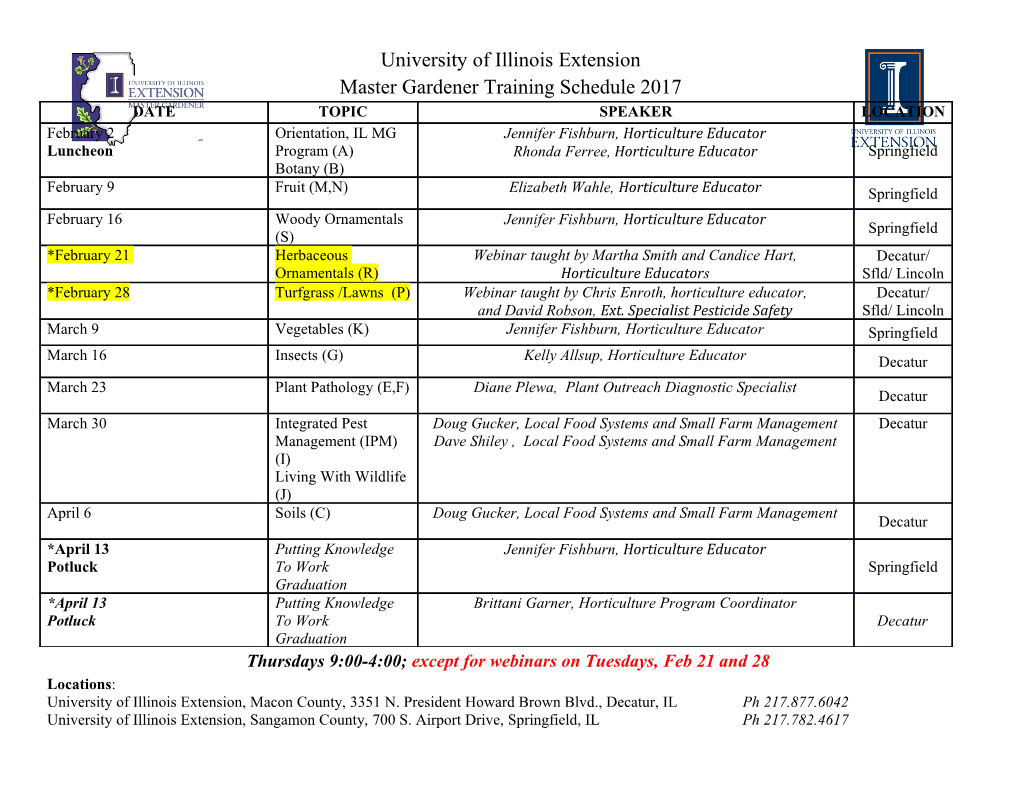
Weldability Evaluation of High-Cr Ni-Base Filler Metals using the Cast Pin Tear Test THESIS Presented in Partial Fulfillment of the Requirements for the Degree Master of Science in the Graduate School of The Ohio State University By Eric Przybylowicz Graduate Program in Welding Engineering The Ohio State University 2015 Master's Examination Committee: Boian Alexandrov, Advisor John Lippold Copyright by Eric Thomas Przybylowicz 2015 Abstract High chromium, nickel-base filler metals have been commonly used throughout the nuclear power industry for the weld overlay repair of dissimilar metal welds (DMW) affected by primary water stress corrosion cracking (PWSCC). These alloys provide optimum resistance to PWSCC in nuclear power plant cooling systems. However some of these nickel alloys present weldability challenges including susceptibility to solidification cracking and ductility dip cracking. There is a current need to incorporate the evaluation of weldability into the alloy development process. The Cast Pin Tear Test may provide a viable means for evaluating alloy susceptibility to solidification cracking in a timely and economical manner. The first objective of this study was to optimize the new generation CPTT procedure in order to improve the reproducibility and reliability of the test. The second objective was to generate solidification cracking susceptibility rankings using the CPTT in a series of high-Cr Ni-base filler metals: ERNiCrFe-7A (52M), ERNiCrFe-13 (52MSS), and ERNiCr-3 (82) filler metals, including two heats of 52M, two heats of 52MSS, and one heat of filler metal 82 and 690Nb. The effect of dilution with cast stainless steel substrate on solidification cracking was then investigated in alloys 52MSS-E and 52i-B at levels of 10% and 40% dilution. ii An optimized testing procedure was developed for the CPTT. Procedural improvements in mold and sample cleanliness, the purge procedure, and the casting procedure have resulted in improved testing reproducibility. A reproducibility study was conducted on the CPTT using alloy 52M (ERNiCrFe-7A). The new generation CPTT was capable of successfully casting 0.197 inch diameter pins ranging from 0.5-2.5 inches in length and 9.5-17.5 grams in mass. From the reproducibility study low standard deviation at pin lengths by which alloy susceptibility to solidification cracking are ranked (max. pin length with 0% cracking, min. pin length with 100% cracking) indicates good test reproducibility. The generation of solidification cracking susceptibility curves by visual evaluation of circumferential cracking produced the following ranking of the tested filler metals, from least to most susceptible: 82(A), 52i-B [187775], 52MSS-E [HV1500] and 52M [NX7206TK] and TG-SN690Nb [FBH2280], 52M [NX0T85TK], 52MSS-C [NX77W3UK]. The rankings produced using the new generation CPTT are in agreement with those obtained using the previous generation: Filler metal 82; least susceptible to solidification cracking followed by filler metals 52M, and 52MSS-C. A new procedure was developed for more reliable evaluation of cracking response in cast pin samples. Solidification cracking susceptibility curves were developed through tensile testing of CPTT samples. A new ranking criterion, UTS threshold reduction, was found to produce results similar to those determined by visual evaluation of circumferential cracking. The ranking of the tested filler metals by tensile inspection, from least to most susceptible to solidification cracking, is: 52MSS-E [HV1500], 52i-B iii [187775], TG-SN690Nb [FBH2280], 52M [NX7206TK], 52MSS-C [NX77W3UK]. The difference between inspection method rankings lies in the more resistant ranking of alloy 52MSS-E which was determined by tensile inspection. It was concluded that tensile inspection offers a more objective and comprehensive evaluation of cracking in cast pin samples due to the inability of visual circumferential cracking measurement to account for crack depth. Dilution of alloys 52MSS-E and 52i-B at 10% CF8A resulted in a slight increase in solidification cracking susceptibility, as indicated by CPTT results. A dilution level of 40% resulted in a dramatic increase in cracking susceptibility in both alloys. Thermodynamic simulation results suggest that as the dilution level increases in alloys 52i-B and 52MSS-E from 0% to 40% the partitioning coefficient of Nb decreases due to an elevated nominal iron content. This increase in Nb partitioning results in increased eutectic formation in the form of laves phase. Among all the alloys studied it was determined that a larger amount of eutectic promotes solidification cracking resistance in the presence of a sufficiently high NbC/laves ratio. Metallurgical characterization using light optical microscopy, scanning electron microscopy (SEM), and energy dispersive spectroscopy (EDS) in the SEM was performed in order to identify solidification cracking mechanisms, and to study the effect of liquid film formation and backfilling on cracking susceptibility. Nb-rich eutectic type constituents were identified at crack tips in each of the studies alloys. Eutectic “backfilling” was observed most abundantly in alloys 52MSS-C and 52MSS-E by a Mo and Nb-rich eutectic constituent. iv Dedication This document is dedicated to my family. v Acknowledgments I would like to acknowledge Dr. Boian Alexandrov and Dr. John Lippold, my advisors, for supporting and guiding my research here at The Ohio State University. Tim Luskin for the work he did in creating this new generation cast pin tear test, providing me with a basis for my research. I would also like to thank Geoff Taber and Ken Copley for their help and support in conducting my research and troubleshooting testing equipment with me. I would also like to acknowledge the Electric Power Research institute for sponsoring this research. Specifically I would like to thank Steve McCracken for his time and direction over the last two years of my research. vi Vita June 2009 .......................................................R. L. Thomas High School 2013................................................................B.S. Welding Engineering, The Ohio State University 2015................................................................M.S. Welding Engineering, The Ohio State University Field of Study Major Field: Welding Engineering vii Table of Contents Abstract ............................................................................................................................... ii Dedication ........................................................................................................................... v Acknowledgments.............................................................................................................. vi Vita .................................................................................................................................... vii Table of Contents ............................................................................................................. viii List of Tables ..................................................................................................................... xi List of Figures .................................................................................................................. xiii Chapter 1: Introduction ...................................................................................................... 1 Chapter 2: Background & Objectives ................................................................................. 6 Welding Metallurgy of Ni-Base Alloys .......................................................................... 6 Weldability ...................................................................................................................... 8 Ductility-Dip Cracking ................................................................................................ 8 Solidification Cracking .............................................................................................. 11 Weldability Testing ....................................................................................................... 21 The Varestraint Test .................................................................................................. 22 The Transvarestraint Test .......................................................................................... 24 viii The Cast Pin Tear Test .............................................................................................. 25 The Threaded Copper Mold Test ............................................................................... 30 The Grooved Copper Mold Test ................................................................................ 31 The Cast Pin Tear Test (OSU) ................................................................................... 33 Summary ....................................................................................................................... 37 Objectives ...................................................................................................................... 39 Chapter 3: Materials & Experimental Procedure .............................................................. 41 Introduction ................................................................................................................... 41 Materials ........................................................................................................................ 41 Weldability Testing Procedure
Details
-
File Typepdf
-
Upload Time-
-
Content LanguagesEnglish
-
Upload UserAnonymous/Not logged-in
-
File Pages153 Page
-
File Size-