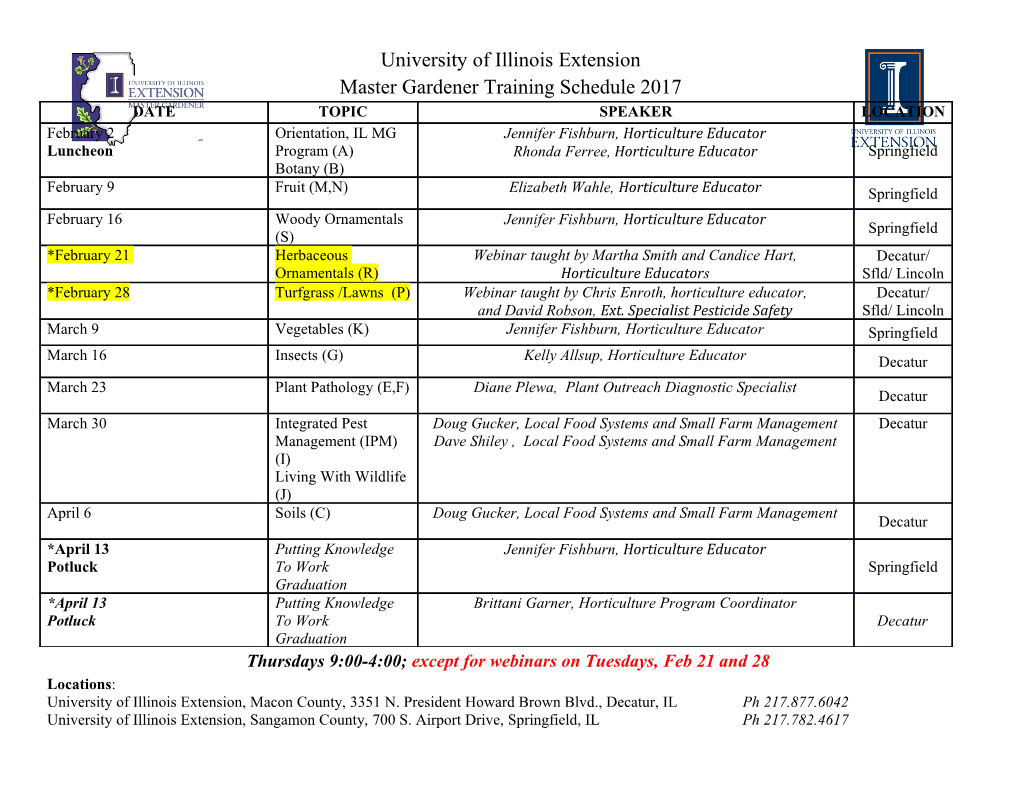
PARTICLE JAMMING DURING THE DISCHARGE OF FLUID-DRIVEN GRANULAR FLOW by Patrick G. Lafond c Copyright by Patrick G. Lafond, 2014 All Rights Reserved A thesis submitted to the Faculty and the Board of Trustees of the Colorado School of Mines in partial fulfillment of the requirements for the degree of Doctorate of Philosophy (Chemical Engineering). Golden, Colorado Date Signed: Patrick G. Lafond Signed: Dr. Amadeu K. Sum Thesis Advisor Signed: Dr. David T. Wu Thesis Advisor Golden, Colorado Date Signed: Dr. David W. M. Marr Professor and Head Department of Chemical Engineering ii ABSTRACT When a stream of granular material attempts to flow through a small opening, the particles may spontaneously form a strong arch-like arrangement of particles capable of supporting the weight of the overhead particles. This arching of particles, referred to as a \jam," stops all particle flow and must be removed if flow is to resume. This work presents observations of particle \jamming" where fluid is the driving medium for the granular flow. I use two experimental systems - an open-channel flume, and a bench-scale flowloop - and a series of computer simulations jamming to study this random event. In the experimental systems I focus on three pieces of jamming: 1) jamming with a dilute stream of particles, 2) the transition of a dilute to dense flow of particles (i.e., when particle accumulation or \backlogging" occurs), and 3) jamming with a dense flow of backlogged particles. In backlogged particles I see the instantaneous per-particle jamming probability, 1 − p, 2 scales as ln(1 − p) / R − 1, where R is the ratio of the opening diameter, do, to the particle diameter, dp. I also observe that 1 − p is only constant after the particle backlog is sufficiently deep, and relate this depth to the number of particles that have discharged. Knowing how a system acts after backlog information, I focus on when particle backlogs form by modeling particle discharge rates, N_ . I model discharge rates with free-fall arch _ 2 2 theory and experimentally observe N ≈ 3φC β vf (R−1) =2dp, where φC ≈ 0:585 is the outlet concentration, β is the ratio of the pipe diameter, dpipe to opening diameter, and vf is the fluid velocity. The main finding is that particles appear to match the fluid velocity at the orifice exit. The final experimental findings were measurements of the instantaneous per-second jam- ming rate, r(t). I generalize the time-to-jam distribution in terms of a dynamic jamming rate, and find the characteristic time, tc = dp=vf eliminates fluid velocity effects. This corresponds to a dimensionless jamming rate σ(τ) = r(t)tc. I also measure σ as a function iii of the particle volume fraction, φ, in pre-backlogged systems. Lastly, I look at the origin of jammed configurations through the use of DEM simulations. I hypothesize that an infinitely long (periodic) slit will have per-particle jamming probability, 1 − p, that scales with ln(1 − p) / L where L is the length of the explicitly simulated system. I extend this theory to simple openings (circles, squares, and triangles) and develop −2 2 a \universal" approximation for small openings where I observe ln(1 − p) / Ao(1 − RL )=dp, where Ao is the total area of the opening, and RL is the characteristic length of the opening, Lc, divided by the particle diameter, where Lc ! dp when the restriction shape circumscribes exactly 1 particle. I show this fit gives good approximation to 16 openings of different sizes, and geometries. iv TABLE OF CONTENTS ABSTRACT . iii LIST OF FIGURES . ix LIST OF TABLES . xvi LIST OF SYMBOLS . xvii LIST OF ABBREVIATIONS . xxi ACKNOWLEDGMENTS . xxii CHAPTER 1 INTRODUCTION . 1 1.1 Jamming During Granular Discharge . 2 1.2 Granular Discharge Rates and Accumulation . 10 1.3 Thesis Conclusions . 12 1.4 Thesis Outline . 13 CHAPTER 2 METHODS AND MATERIALS . 15 2.1 Open-Channel Flume . 15 2.2 Bench-Scale Flowloop . 19 2.2.1 Loop Jamming Measurements . 25 2.2.2 Loop Concentration Measurements . 31 2.3 Discrete Element Model . 34 2.4 Conclusions . 36 CHAPTER 3 OPEN CHANNEL FLUME MEASUREMENTS AND MODELING . 38 3.1 Generalized Particles-to-Jam Probability Distribution . 38 v 3.2 Results . 42 3.3 Modeling . 44 3.3.1 Modeling NT as a Backlog Accumulation . 44 3.3.2 Modeling Jamming Frequency . 47 3.4 Conclusions . 52 CHAPTER 4 PARTICLE DISCHARGE RATE: MEASUREMENTS AND MODELING . 54 4.1 Background . 54 4.2 Modeling . 57 4.2.1 Estimates of vexit in Fluid-Driven Flow . 57 4.2.2 Estimates of φexit in Fluid-Driven Flow . 59 4.3 Results . 64 4.4 Conclusions . 68 CHAPTER 5 LOOP JAMMING MEASUREMENTS . 70 5.1 Generalized Time-to-Jam Probability Distribution . 70 5.2 Light-Gate Jamming Measurements . 73 5.3 Fluid Velocity Effects . 75 5.4 Dilute Jamming . 76 5.5 Conclusions . 82 CHAPTER 6 SIMULATING JAMMING IN GRAVITY-DRIVEN FLOW . 85 6.1 Non-Circular Restriction Jamming Probabilities . 86 6.1.1 Sub-Ensemble Jamming Probabilities and Theory Development . 87 6.2 Periodic Simulations . 89 vi 6.3 Mixed Systems . 91 6.4 Conclusions . 98 CHAPTER 7 MODEL USE AND APPLICATION . 100 7.1 Economics of Jamming . 101 7.2 Jamming as a Phase Diagram: Design Application . 103 7.3 Conclusions . 105 CHAPTER 8 CONCLUSIONS AND SUGGESTIONS FOR THE FUTURE . 107 REFERENCES CITED . 110 APPENDIX A - LIGHT GATE CALIBRATION . 118 A.1 Probabilistic Interpretation of the Light Gate . 118 A.2 Experimental Light Gate Calibration . 119 A.3 Monte Carlo Simulation Calibration . 122 A.3.1 Monte Carlo Simulation Details . 122 APPENDIX B - STATISTICAL INDEPENDENCE . 128 B.1 Memoryless Behavior in an \Avalanche" Model . 128 B.2 Relating p∗ to Avalanche Model . 130 APPENDIX C - LOOP VELOCITY CALIBRATION . 133 APPENDIX D - DEM SIMULATION ALGORITHM . 135 APPENDIX E - LOOP MANUAL . 137 E.1 Controller Program . 137 E.2 Manual Loop Control . 141 E.3 Loop Filling and Draining . 142 E.3.1 Draining the Loop . 145 vii E.3.2 Filling the Loop . 145 E.4 Adding Salt . 146 E.5 Starting and Stopping the Pump and Air . 147 E.6 Starting the Loop . 147 E.7 Stopping the Loop . 149 E.8 Preparing System for Velocity Calibration . 149 viii LIST OF FIGURES Figure 1.1 Sample arch-like arrangement of 2D particles over an opening. 1 Figure 1.2 Decision tree representing the path a system must follow in order to arrive at any final state. The path to observe pjam(2) is highlighted for demonstration. 5 Figure 1.3 The jamming decision tree for a vibrated silo. The circles represent flowing states, where the prime indicates a transient jam formed. The red is one path to arrive at pjam(1), and the blue highlights an alternate path, where a weak jam was observed at 0 particles. 8 Figure 2.1 Open channel flume, originally constructed for 2D jamming work. 16 Figure 2.2 Sample restriction used in the flume measurements. 17 Figure 2.3 Image sequence of the experiments performed on the flume. The yellow highlights particles that have stopped (from backlogging) as the particles accumulate. 18 Figure 2.4 Statistics of 150 measurements of 600 5/8" particles jamming a 1.5" opening. 19 Figure 2.5 The starting concept for jamming experiments. 20 Figure 2.6 The second iteration for jamming loop design. 21 Figure 2.7 The final jamming loop design with instrumentation. Main loop components for particle jamming under fluid-driven flow. Computer and controls omitted from drawing. B- are fluid bypasses, V- are pneumatic valves, C- are check valves, P- are pressure transducers, L- are light gates, E- are fluid entry points, and G- are globe valves. 21 Figure 2.8 Reduced schematics for the two modes of the jamming loop. All lines with stagnant fluid are removed to depict the core functions of the two modes. 23 Figure 2.9 Typical orifice plate. The left opening is the test opening (do in diameter) the right opening is 4 inches in diameter to clear the tube if a jam has occurred. The plate is moved with a small piece of plastic attached to a piston. 24 ix Figure 2.10 Typical ∆P trace for large particles flowing through a 1.25" restriction. A 7-point median filter is applied to the raw data (grey points) resulting in a much smoother trace (black points). 26 Figure 2.11 Distributions of ∆P at t = 0 and t = 60 s for 1,500 jamming measurements of a diluted stream of 5/8" particles through an 11/8" hole. 28 Figure 2.12 Survival probability and jamming probability density functions for the system shown in Figure 2.11. S(t) and pjam are calculated using Equations 2.1 and 2.2b respectively. The calculations use ∆Pjam =1, 1.5, 2, and 2.5 psi. 29 Figure 2.13 Survival probability.
Details
-
File Typepdf
-
Upload Time-
-
Content LanguagesEnglish
-
Upload UserAnonymous/Not logged-in
-
File Pages175 Page
-
File Size-