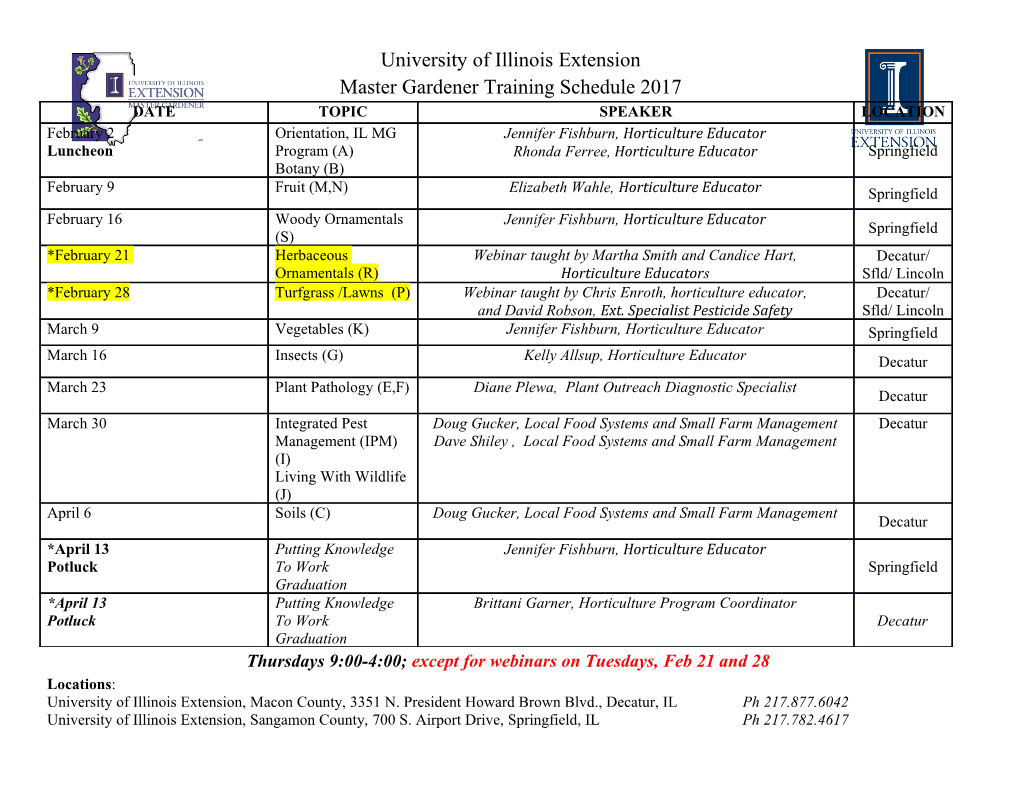
e-book An Engineer’s Guide to Industrial Robot Designs A compendium of technical documentation on robotic system designs ti.com/robotics Q2 | 2020 Table of Contents/Overview 1. Introduction 3. Robot arm and driving system (manipulator) 1.1 An introduction to an industrial robot system. 3 3.1.1 How to protect battery power management systems from thermal damage. 45 2. Robot system controller 3.1.2 Protecting your battery isn’t as hard as 2.1 Control panel you think.....................................46 2.1.1 Using Sitara™ processors for Industry 3.1.3 Position feedback-related reference designs 4.0 servo drives.......................9 for robotic systems............................47 2.2 Servo drives for robotic systems 4. Sensing and vision technologies 2.2.1 The impact of an isolated gate driver. 13 4.1 TI mmWave radar sensors in robotics 2.2.2 Understanding peak source and applications..................................48 sink current parameters . 17 4.2 Intelligence at the edge powers autonomous 2.2.3 Low-side gate drivers with UVLO versus factories .....................................53 BJT totem poles ......................19 4.3 Use ultrasonic sensing for graceful robots. 55 2.2.4 An external gate-resistor design guide for 4.4 How sensor data is powering AI in robotics. 57 gate drivers.......................... 20 4.5 Bringing machine learning to embedded 2.2.5 High-side motor current monitoring for systems .....................................61 overcurrent protection. 22 4.6 Robots get wheels to address new 2.2.6 Five benefits of enhanced PWM rejection for challenges and functions. 65 in-line motor control. 24 4.7 Vision and sensing-technology reference 2.2.7 How to protect control systems from thermal designs for robotic systems. 66 damage............................26 5. Technologies for robotic tools (end effector) 2.2.8 How high precision in motor-drive control enables industrial advances. 29 5.1 Achieving accuracy in bin picking with TI DLP® technology-powered structured 2.2.9 Getting the most out of your power stage light systems..................................67 at the full temperature range. 33 2.2.10 Anything but discrete: how to simplify a 48-V 6. Industrial communications for robotics to 60-VDC-fed three-phase inverter design. 35 6.1 Selecting the right industrial communications 2.2.11 Selecting amplifiers for shunt-based current standard for sensors...........................69 sensing in three-phase motor drives. 38 6.2 Enabling robots to achieve new levels of factory 2.3.1 Servo drive-related reference designs for automation...................................73 robotic systems.......................44 6.3 Is your factory smarter than a fifth grader?........76 6.4 Industrial communications-related reference designs for robotic systems.....................78 An Engineer’s Guide to Industrial Robot Designs 2 2Q 2020 I Texas Instruments Chapter 1: Introduction Analog and embedded technologies and reference designs 1.1 An introduction to an industrial robot system from Texas Instruments (TI) enable engineers to develop Before describing the different technologies that go into a intelligent, autonomous and collaborative robots. This typical robotic system, let’s discuss the different parts of a e-book is intended to be a one-stop shop for robotics- robot system, as shown in Figure 1. As you can see, the related content. system is split into the different building blocks: the controller Our technologies let you build numerous types of industrial system, manipulator, teaching pendant, vision and sensors, robots with precise motor control, differentiated sensing and end effector (robot tools). technologies and processing at the edge, all with robust real-time communication. The primary types of robots discussed in this e-book are collaborative robots (cobots) and factory robots: • Cobots work side by side with humans to improve work quality. A cobot can sense and stop movement, helping create a safer working environment. • Factory robots perform automated programmable movements in manufacturing. In order to create a safer working environment, mechanical or sensor technologies can help keep robots from interfering with human activity. There are six types of industrial robots: • Vertically articulated. • Cartesian. • Cylindrical. • Polar. • Selective compliance assembly robot arm (SCARA). Figure 1. A robotic system featuring a cobot. • Delta. All of these robot types offer a different axis configuration of The International Organization for Standardization (ISO) the manipulator and include electronic content that enables 8373:2012 standard describes each of the building blocks the robot to manage its tasks. Task management is driven shown in Figure 1 and defines terms used in relation to by advances in software, sensors and electronics, and has robots and robotic devices operating in both industrial and enabled the market for industrial robots to evolve over the nonindustrial environments as: last 50 years. • The controller system. The ISO 8373 standard states, This e-book is a compilation of technical articles, white “A set of logic control and power functions which allows papers and application notes featuring TI’s technologies monitoring and control of the mechanical structure of suited for these industrial robot system building blocks: the robot and communication with the environment [equipment and users].” This is the robot’s brain, and can • The robot controller system. include a motion controller, both internal and external • The manipulator (robotic arm)/driving system. communication systems, and any potential power stages. • Sensing and vision technologies. • The end effector (robot tools). An Engineer’s Guide to Industrial Robot Designs 3 2Q 2020 I Texas Instruments Chapter 1: Introduction • The manipulator. The ISO 8373 standard also states • Cartesian. These are also called rectilinear or gantry “A machine in which the mechanism usually consists of robots. Cartesian robots have three linear axes that use the a series of segments, jointed or sliding relative to one Cartesian coordinate system (x, y and z). They may have another, for the purpose of grasping and/or moving objects an attached axis that enables rotational movement. Three (pieces or tools) usually in several degrees of freedom or prismatic joints facilitate linear motion along the axis. axes. A manipulator does not include an end effector.” • Cylindrical. This robot has at least one rotary axis at The manipulator is commonly known as the robotic arm. the base and at least one prismatic axis to connect the It’s the part of the robot that defines how many axes the links. The rotary axis uses a rotational motion along robot is implementing to achieve the movement required the axis, while the prismatic axis uses linear motion. to perform a task. Cylindrical robots operate within a cylindrical-shaped work • The teaching pendant. Multifunctional portable environment. equipment used to program and teach an industrial robot. • Polar. Polar robots are also called spherical robots. For The pendant typically consists of an LCD touch panel, an these types of robots, the manipulator connects to the enable button and an e-stop button. The teaching pendant base with a twisting axis and a combination of two rotary connects to the robot controller system. axes and one linear axis. The axes form a polar coordinate • The robotic end effector. A device connected on the system and create a spherical-shaped work environment. robot “wrist” or end-of-arm tooling (EOAT). The system • Selective compliance assembly robot arm (SCARA). controller controls the robotic end effector by using either Commonly used in assembly applications, this selectively discrete input/output (I/O) for simple tools or industrial compliant manipulator for robotic assembly is primarily communication protocols for more advanced tools. cylindrical in design. It features two parallel axes that • Vision and sensors. These parts of the robot have the provide compliance in one selected plane. ability to scan the surrounding environment and stop (in • Delta. These spider-like robots are built from jointed the case of an industrial robot) or reduce (in the case of a parallelograms connected to a common base. A delta cobot) a robot’s speed when humans approach. Vision/ robot has three axes for the parallelograms; for the end sensing is implemented with light detection and ranging effector, it can have one to three axes. The parallelograms (LIDAR), a radar-based safety area scanner or 3D cameras. move a single EOAT in a dome-shaped work area. Heavily In addition to the safety area scanner, cobots sometimes used in the food, pharmaceutical and electronic industries, wear a sensor-based “safety skin” that stops the robot arm this robot configuration is capable of delicate, precise when a human touches it or is in proximity. movements. When designing the building blocks of a robotic system, there are mechatronics, robot functions and electrical What amount of payload (weight) and reach will considerations that you need to understand and obtain the robot have? specifications for before beginning the actual design. If the robot has to move heavy objects, it needs to have Let’s discuss some typical considerations when defining the enough force on the motors to enable that capability. This system architecture of a robot. force is generated with electric energy and is provided to the motor from the power stage. This power requirement is part What type of task is the robot supposed to do? of deciding
Details
-
File Typepdf
-
Upload Time-
-
Content LanguagesEnglish
-
Upload UserAnonymous/Not logged-in
-
File Pages80 Page
-
File Size-