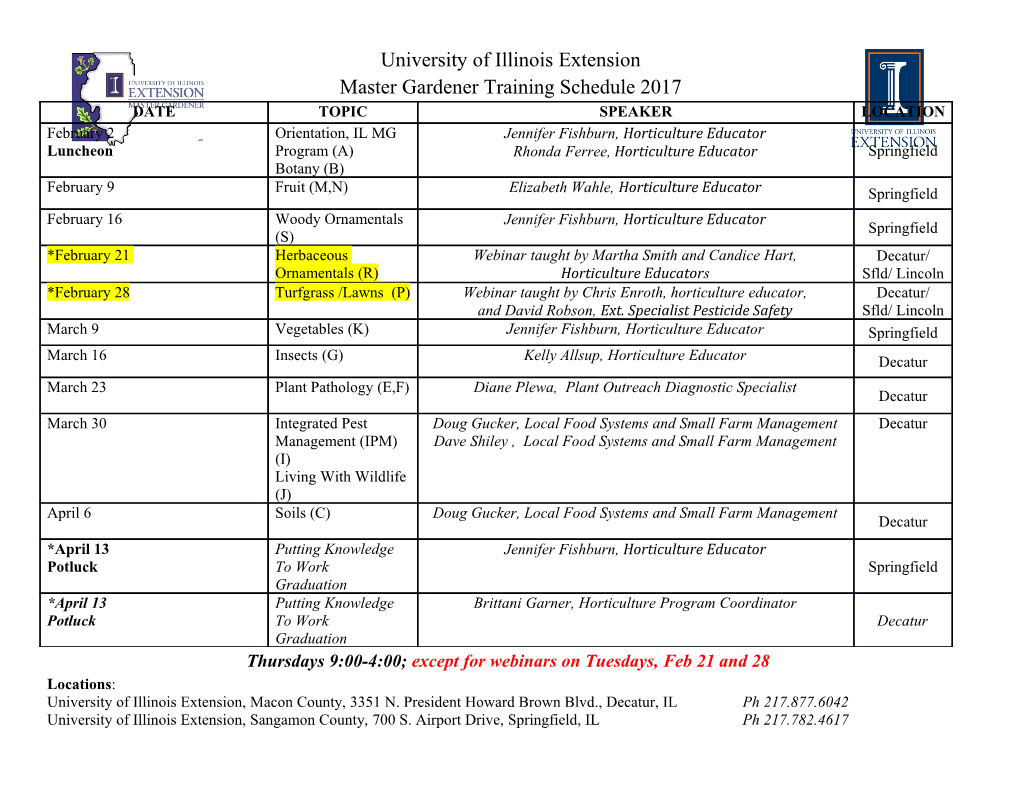
ON Semiconductor Is Now To learn more about onsemi™, please visit our website at www.onsemi.com onsemi and and other names, marks, and brands are registered and/or common law trademarks of Semiconductor Components Industries, LLC dba “onsemi” or its affiliates and/or subsidiaries in the United States and/or other countries. onsemi owns the rights to a number of patents, trademarks, copyrights, trade secrets, and other intellectual property. A listing of onsemi product/patent coverage may be accessed at www.onsemi.com/site/pdf/Patent-Marking.pdf. onsemi reserves the right to make changes at any time to any products or information herein, without notice. The information herein is provided “as-is” and onsemi makes no warranty, representation or guarantee regarding the accuracy of the information, product features, availability, functionality, or suitability of its products for any particular purpose, nor does onsemi assume any liability arising out of the application or use of any product or circuit, and specifically disclaims any and all liability, including without limitation special, consequential or incidental damages. Buyer is responsible for its products and applications using onsemi products, including compliance with all laws, regulations and safety requirements or standards, regardless of any support or applications information provided by onsemi. “Typical” parameters which may be provided in onsemi data sheets and/ or specifications can and do vary in different applications and actual performance may vary over time. All operating parameters, including “Typicals” must be validated for each customer application by customer’s technical experts. onsemi does not convey any license under any of its intellectual property rights nor the rights of others. onsemi products are not designed, intended, or authorized for use as a critical component in life support systems or any FDA Class 3 medical devices or medical devices with a same or similar classification in a foreign jurisdiction or any devices intended for implantation in the human body. Should Buyer purchase or use onsemi products for any such unintended or unauthorized application, Buyer shall indemnify and holdonsemi and its officers, employees, subsidiaries, affiliates, and distributors harmless against all claims, costs, damages, and expenses, and reasonable attorney fees arising out of, directly or indirectly, any claim of personal injury or death associated with such unintended or unauthorized use, even if such claim alleges that onsemi was negligent regarding the design or manufacture of the part. onsemi is an Equal Opportunity/Affirmative Action Employer. This literature is subject to all applicable copyright laws and is not for resale in any manner. Other names and brands may be claimed as the property of others. TND6041/D DC Motor Driver Fundamentals http://onsemi.com TECHNICAL NOTE INTRODUCTION Electric motors have been with us since the early 19th commutator is a set of contacts attached to the armature shaft century, when Hungarian physicist Ányos Jedlik produced that keeps reversing the direction of current flow in the the first continuously rotating DC motor, made possible by armature as it turns, thus ensuring that the motor continues his invention of the commutator. By the early 20th century to turn. electric motors revolutionized industry and agriculture and While motors are mechanically rather simple, the terms made possible such labor saving consumer applications as that describe them can be confusing. In mechanical terms washing machines and refrigerators. Today electric motors the rotating part of motor is called the rotor; the stationary power everything from giant cruise ships to implantable part is the stator. In electrical terms the power producing medical devices. part of the motor is called the armature; depending on the There are many different types of motors, but they all design the armature can be either the rotor or the stator. The contain three basic elements: an armature, a field magnet, field is a magnetic field component of the motor; again this and a commutator. The armature is a conductive coil that in can be either the rotor or the stator and it can be either an most cases is attached to a rotating shaft and surrounded by electromagnet or a permanent magnet. In general literature a field magnet, which can be either a field winding or these terms are often used interchangeably, which can be permanent magnets. Current passing through the armature confusing. creates a magnetic field that is opposed to the field current, There are two basic types of DC motors: brushed and resulting in an electromotive force (EMF) that causes the brushless, with subsets of each (Figure 1). We’ll discuss shaft to rotate, generating mechanical torque. The each in turn. Figure 1. Motor Components BRUSHED DC MOTORS The brushed DC motor is the simplest and the earliest more coils connected to a segmented commutator which is electrical motor design. While it has a number of contacted by brushes connected to the DC power supply disadvantages, is inexpensive and is still used widely for (Figure 2). torque control and variable speed applications. DC power is conducted through the brushes and The brushed DC motor consists of a few simple commutator, and the current through the coil creates components: stationary stator composed of field coils a magnetic field. This field is opposite to the magnetic field (wound field) or two hemispherical permanent magnets of the permanent magnets in the stator, causing the armature (PM); an internal rotating armature consisting of two or to rotate. Mechanical commutation changes the direction of © Semiconductor Components Industries, LLC, 2014 1 Publication Order Number: March, 2014 − Rev. 1 TND6041/D TND6041/D the current and a rotational motion is generated. With perform better. However, extreme drops in temperature can a two-pole motor the commutator causes the current to potentially increase the viscosity of the lubricants, causing reverse in direction every half cycle, causing the motor to the motor to run at a higher current. continue to rotate. The speed of the motor is directly proportional to the Wound-field Brushed DC Motors voltage applied, while the torque is proportional to the There are two basic types of brushed DC motors: those current. You control the speed of a brushed DC motor by whose stator consists of field coils and those that use simply varying the voltage applied to it; to reverse it, just permanent magnets in the stator instead. There are three reverse the polarity of the applied voltage; and to stop it turn types of wound-field coils (Figure 3): off the voltage. • Shunt wound, in which the field coils are connected in parallel with the armature coils via the brushes (Figure 3A); • Series wound, in which the field coils are in series with the coils in the armature (Figure 3B); and • Hybrid, with separate field coils where one is in series and the other is in parallel with the armature coils (Figure 3C). AB C f f M f f M M 1 2 Figure 2. Brushed PM DC Motor Figure 3. Field Coils: (A) Shunt, (B) Series, (C) Hybrid Brushed DC motors have some advantages over other designs: • Brushed PM DC Motors They are simple and inexpensive; Until the development of neodymium magnets brushed • They don’t require complex drive electronics; permanent magnet (PM) DC motors were only able to • Their speed is a direct, linear function of the armature handle small loads. Today they are commonly used in fairly voltage; large commercial and industrial applications and are • Because of their simplicity and low cost − typically half dominant in fractional-horsepower applications. In the cost of brushless DC motors of the same size − commercial use since 1886 they are still the most commonly design cycles are shortened. used DC motors in the world. However, they’re not without some notable drawbacks: Driving Brushed DC Motors • The brushes tend to wear out because of continuous Driving brushed DC motors is straightforward in friction. The brushes and springs need replacing from principle but not quite so simple in practice. For the simplest small applications you can run the motor directly from time to time; a power source and use a potentiometer to control the speed • The commutator needs periodic cleaning or and a switch to reverse its direction. If the motor is to be part replacement; • of an embedded application you need a driver IC and some Arcing is ever present and causes EMI that can interfere control logic. with nearby electronics; Figure 4 is a block diagram of ON Semiconductor’s • The rotor’s inertia may be an issue, and the commutator LB1938FA single-channel, forward/reverse brush motor makes the motor larger than its brushless counterpart; driver IC that provides low-saturation outputs for use in • Heat generated by coil rotation is always an issue. low-voltage applications. The motor is driven by an H bridge that is protected by ‘spark killer’ diodes, since this is The environment in which a brush DC motor is used can a brushed motor. The logic circuitry in the control block also greatly affect the lifetime of the motor. Dry, warm determines the speed and direction of the motor as dictated environments may increase the wear of the brushes and by the CPU. The LB1938FA provides forward, reverse, quicken the breakdown of the commutator and bearings. brake, and standby modes controlled by two input signals. Running a brush DC motor in a cooler environment along It’s designed for use in notebook computers, digital cameras, with external cooling by forced air may cause the motor to cell phones, and other portable equipment. http://onsemi.com 2 TND6041/D C1 = 0.1 to 10 mF VCC 1 W IN1 60 k 2 W OUT1 7 CPU 80 k M 60 kW IN2 6 3 CONTROL BLOCK OUT2 W 80 k S-GND 4 8 P-GND Figure 4.
Details
-
File Typepdf
-
Upload Time-
-
Content LanguagesEnglish
-
Upload UserAnonymous/Not logged-in
-
File Pages10 Page
-
File Size-