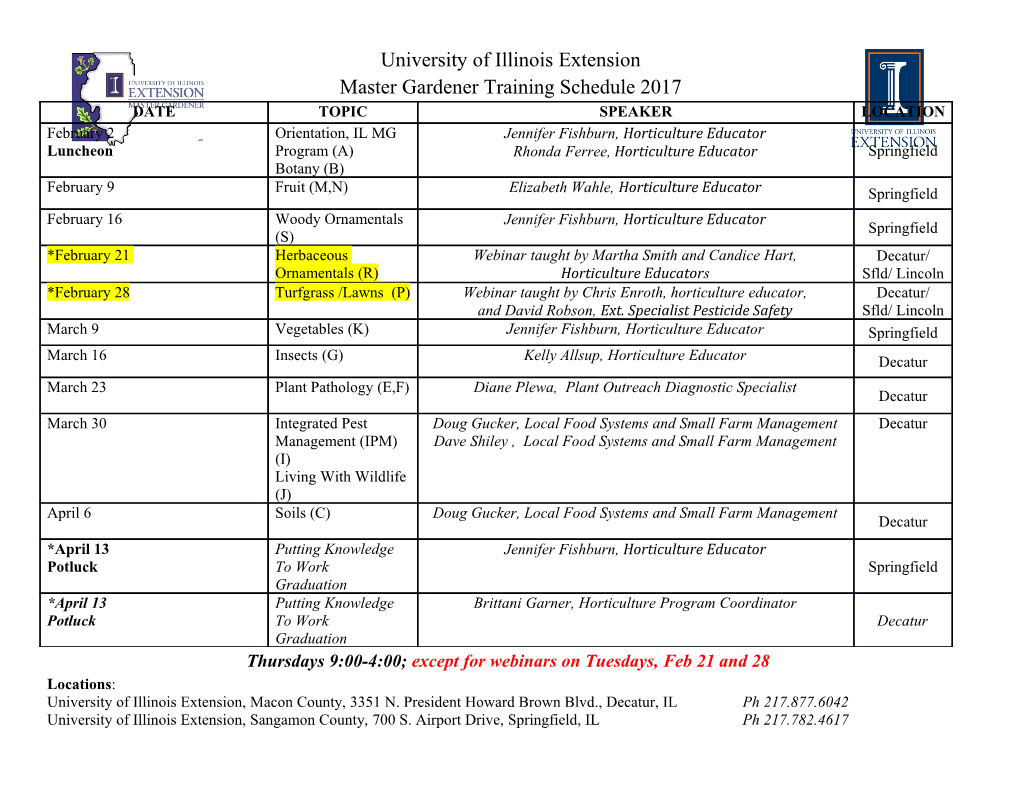
EXOS Aerospace Systems & Technologies, Inc. PAYLOAD USER GUIDE (PUG) 1 SARGE – Payload User Guide – Rev. 3 SARGE FAMILY OF VEHICLES INDEX 1. INTRODUCTION 1.1. Corporate Information Page 3 1.2. Purpose & The NASA Flight Opportunities Program Page 3 2. THE SARGE VEHICLE 2.1. Heritage Page 4 2.2. Description Page 4 2 SARGE – Payload User Guide – Rev. 3 2.3. Mission Profile Page 6 2.4. Launch Site(s) Page 7 2.5. Launch Windows Page 7 2.6. Reusability & Frequency Page 8 3. EXOS FACILITIES 3.1. Headquarters Page 8 3.2. R&D Center Page 8 4. PAYLOAD PROVIDER INFORMATION 4.1. Payload Mass & Physical Size Page 8 4.2. Payload Environment Page 9 4.3. Standard Integration Services Page 10 4.4. Non-Standard Integration Services (Optional) Page 10 5. PAYLOAD INTEGRATION 5.1. Procedure for Approval Page 11 5.2. FAA /AST Payload Approval Page 11 5.3. Combined Systems Test Page 11 5.4. Physical Integration Page 11 5.5. Launch Operations Page 11 6. ITAR 6.1. Introduction Page 12 6.2. ITAR Integration & Launch Protocol, Telemetry Data Page 12 7. REVISION HISTORY Page 13 3 SARGE – Payload User Guide – Rev. 3 1. INTRODUCTION 1.1. EXOS Aerospace Systems & Technologies, Inc. (hereinafter EXOS or (E.A.S.T. for legal purposes)) is the successor company to Armadillo Aerospace LLC. (Hereinafter AA (the EXOS team)). EXOS acquired AA’s mission critical physical assets in early 2015 to take this technology commercial with the development of the SARGE platform. AA was a leading developer of reusable rocket powered vehicles and continuing the tradition EXOS is immediately focused on suborbital research rockets, with the vision of launching microsatellites and, eventually progressing to autonomous spaceflight. Founded in 2000, AA had an unequaled experience base with more than two hundred test flights spread over two- dozen different vehicles. Projects were undertaken for NASA, the Air Force, and vehicles were flown at every X-Prize Cup event. AA performed the very first flight under the new FAA/AST experimental permit regulatory regime, and made over two dozen additional permitted flights since then, all fully insured and observed by on-site AST personnel. AA (the EXOS team) pioneered the tethered flight test regime in conjunction with FAA)/AST and is the only company in the world to test sounding rockets in this manner. AA also flew the first flight under the Class III waiver, and flew more than twenty-four waivered flights since then at two different locations. In 2011 AA was one of only seven companies selected by the NASA Flight Opportunities Program (aka CRuSR) to provide launches for scientific payload providers on reusable vehicles. AA was also selected by NASA Johnson Space Center to build its Project Morpheus Lunar Lander Terrestrial Analog vehicle and to develop the LOX-LCH4 (Liquid Methane) propulsion technology to power it. Morpheus has now completed thirteen successful flights at Johnson Space Center and Kennedy Space Center ❑ AA also had experience with manned rocket powered flight through its involvement with Rocket Racing Inc and its rocket racer program. AA developed, manufactured, installed and tested the propulsion systems for their T1 and T2 prototypes based on the Velocity airframe and provided launch assistance for more than seventy test flights including the world’s first two rocket plane side-by-side demonstration flight. EXOS is very proud to have been able to reassemble most of the AA team at EXOS and will further refer to the AA “history events” referenced to our EXOS team synonymously to honor them and their continued commitment to this endeavor. It is EXOS’s intention to give credit to John and Anna Carmack for building a team that could carry on the effort, and that, is the mark of any truly great visionary. E.A.S.T. CORPORATE ADDRESS MANUFACTURING & ENGINEERING Building A, Caddo Mills Municipal Airport Building A, Caddo Mills Municipal Airport Caddo Mills, TX 75135 Caddo Mills, TX 75135 POINT OF CONTACT: Engineering & Technical Russell Blink 972-974-4779 Chief Technology [email protected] Officer Commercial John Quinn 972-740-8355 Chief Operating [email protected] Officer 4 SARGE – Payload User Guide – Rev. 3 1.2. The SARGE family of vehicles was developed to test a wide range of technologies that EXOS requires for its suborbital vehicles. The SARGE vehicle highlighted in this PUG is based on the successful STIG B platform and predating technologies developed during AA’s lunar lander program. More details follow in the next section. 2. SARGE VEHICLE 2.1. As previously mentioned, the SARGE vehicle is based on tried and proven technologies developed by the AA (the EXOS team) over the past fifteen years. The reliable LOX-Ethanol propulsion module is based on the successful LE23000FC series engines that have hundreds of flights and more than seventy manned flights to their credit. One specific engine has undergone more than one thousand ignition events, including in-air restarts and run for more than two hours. This engine has therefore already demonstrated it is reusable for over 75 SARGE flights to space. The avionics (main flight computer) is in-house designed, developed and manufactured incorporating all modern electronics. The flight safety system associated with this avionics package is also in-house developed hardware that has been flight-tested hundreds of times with 100% reliability. In its fifteen year history, the team has never had a single lost time accident or injury for any reason. AA built the very first VTVL for the NASA / Northrop Grumman Lunar Lander Challenge and is the only company to have flown vehicles in every event through its conclusion. The company won prizes at both levels and was the first company to conduct both a “Level I” and, more arduous, “Level II” mission … Back-to-back three minute flights with precision landing on a simulated lunar surface in less than 150-minutes. As a result of the company’s success in this competition, AA was chosen by NASA Johnson Space Center to build their very first Lunar Lander analog vehicle since the LLRV (Lunar Lander Research Vehicle aka “Flying Bedstead”) developed during the Apollo era. This was subsequently campaigned by NASA under the Project Morpheus banner. Following the successes with the lander program AA opted for an unconventional reusable sounding rocket program, STIG (Suborbital Transport with Inertial Guidance) using the proprietary technologies developed but on a much more capable vehicle. 2.2. SARGE, the successor to STIG, is a reusable sounding rocket based on a 20” (50-cm) diameter airframe. It utilizes the LE23000FC LOX-Ethanol propulsion technology and the proprietary avionics and flight control hardware developed over the prior fifteen years. VEHICLE PURPOSE: R&D Flights followed by scientific payload flights under an FAA/AST Operator License VEHICLE DESCRIPTION: SARGE (High Pressure Helium tank w/ Regulated to Blowdown Pressurization Transition) DIMENSIONS MASS BUDGET HEIGHT 36 FT DRY MASS 800 LBM WIDTH 20 INS OD PAYLOAD & BALLAST 0 – 50 LBM DEPTH (Tubular) 20 INS OD LOX (6.5-FT TANK) 970 LBM PROPULSION FUEL (6.5-FT TANK) 670 LBM MAX ULLAGE PERCENTAGE 5% EA. LOX & FUEL GLOW 2,440–2,490 LBM 5 SARGE – Payload User Guide – Rev. 3 PRESSURANT HELIUM REGULATED HP He VOLUME (WATER) 7.00** CU.FT. INITIAL PRESSURE (TANK) 400 PSIG HELIUM INITIAL PRESSURE ~2,250 PSIG INITIAL THRUST 5,420 LBF T/W INITIAL 2.22 : 1 FINAL PRESSURE (TANK) 400 PSIG MASS RATIO 2.93 : 1 FINAL THRUST 6,680 LBF T/W FINAL 7.85: 1 6 SARGE – Payload User Guide – Rev. 3 SARGE (FULLY REUSABLE SUBORBITAL ROCKET) STACK 7 SARGE – Payload User Guide – Rev. 3 8 SARGE – Payload User Guide – Rev. 3 A typical stack, from the ground up, comprises; LE23000 FC Propulsion Module w/ Single Gimbaled Engine enclosed in Fin Can for Aerodynamic Stability Post-Boost w/ Thrust Termination System LOX (Liquid Oxygen) Oxidizer Module Ethanol Fuel Module High Pressure Helium Module for Propellant Pressurant and Cold Gas Thruster ACS Flight Computer Module w/ Power Supply Payload Module Recovery Module w/ Two-Stage Recovery System (Potential Alternate Payload Location) Nose Cone w/ Deployment System The main flight computer provides attitude control during the boost phase via the gimbaled engine. Cold gas thrusters (using residual helium pressurant gas) provide attitude control for pitch-roll-yaw, and ultimately pointing capability. The boost profile is nominally full thrust for the entire burn to achieve maximum altitude but, unlike a solid rocket motor, the boost profile can be infinitely modified, if required, by the main flight computer at the expense of reduced altitude. Helium pressurant gas is used to push the propellants into the engine feed system. No pumps are used for simplicity, ruggedness of design and reliability of operation. Thrust can be regulated by operation of the Main Propellant Feed valves controlled by the main flight computer. A separate set of Master Cut-Off valves are controlled by the Watchdog Computer and the Thrust Termination System. The avionics module houses the main flight computer and its power supply. Based on vector inputs from the Inertial Navigation System, an Inertial Measurement Unit (IMU) and GPS, it flies a near vertical trajectory all the way to suborbital space, monitors the health of the vehicle and ensures that the vehicle remains within the Flight Hazard Area. Recovery is provided by a two-stage system. First, a supersonic ballute is deployed together with the nose cone during the descent phase to provide base stable but fast descent through the upper atmosphere and jet stream winds. Then, as the vehicle enters the denser air, a Wamore GPS steerable main chute is deployed which glide-flies the vehicle back to the launch area.
Details
-
File Typepdf
-
Upload Time-
-
Content LanguagesEnglish
-
Upload UserAnonymous/Not logged-in
-
File Pages18 Page
-
File Size-