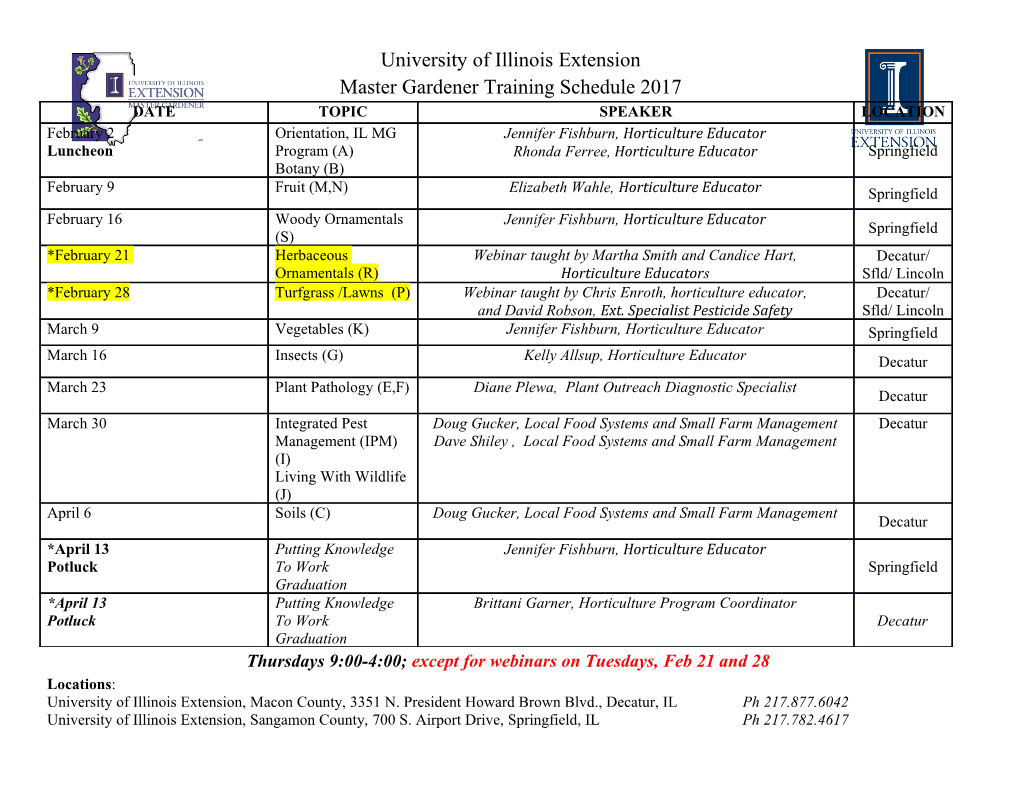
USOO73870 18B2 (12) United States Patent (10) Patent No.: US 7,387,018 B2 Wies (45) Date of Patent: Jun. 17, 2008 (54) DISCRETE VARIABLE VALVE LIFT (56) References Cited DAGNOSTIC SYSTEMS AND METHODS U.S. PATENT DOCUMENTS (75) Inventor: Matthew A. Wiles, Royal Oak, MI (US) 7,047.924 B1* 5/2006 Waters et al. ............ 123.90.16 rsr rr 7,146,851 B2 * 12/2006 Wakahara et al. .......... 73/117.3 (73) Assignee: E. Slobal shots Operations, 2004/0129249 A1* 7/2004 Kondo .............. ... 123,346 2005/0204805 A1* 9, 2005 Wakahara et al. ... 73/118.1 (*) Notice: Subject to any disclaimer, the term of this 2007/0265805 A1* 11/2007 Lee et al. .................... 7O2,187 patent is extended or adjusted under 35 U.S.C. 154(b) by 0 days. * cited by examiner (21) Appl. No.: 11/561,041 Primary Examiner Eric S McCall (22) Filed: Nov. 17, 2006 (57) ABSTRACT (65) Prior Publication Data A diagnostic system for a discrete variable valve lift system of US 2008/O12OO18A1 May 22, 2008 an internal combustion engine is provided. The system includes: a Fast Fourier Transform (FFT) module that gener (51) Int. Cl. ates a frequency content signal based on a FFT method and a GOIM I5/00 (2006.01) valve impact sensor signal; and a malfunction module that (52) U.S. Cl. ...................................................... 73A118.1 selectively diagnoses a malfunction of a discrete variable (58) Field of Classification Search ................... 7.3/116 valve lift system based on the frequency content signal. 73/117.2, 117.3, 118.1, 119 R See application file for complete search history. 20 Claims, 5 Drawing Sheets OW DEAGNOSC O A2 Ai Chy O CEE SACKGROUN NCSE FEER ANCO: i. U.S. Patent Jun. 17, 2008 Sheet 1 of 5 US 7,387,018 B2 U.S. Patent Jun. 17, 2008 Sheet 2 of 5 US 7,387,018 B2 Ca sS. Craik Position, CA) FG. 2A O - 3. 2.3 5 2. 13 8 i y 5 ... r. ya a . A " "... " " ... ' fi. 318i, 3.8 .S. •' . * . * w ." s eannam pepperpetraepapg ww. aw 3 1. 30 4f) SOC 80 Crafik Position, CAD FIG. 2B U.S. Patent Jun. 17, 2008 Sheet 3 of 5 US 7,387,018 B2 OW DEAGNOSC MODE 42 AID CONVERTER MO) FFT dO). ACKSRON NOSE FER NCO: E MALFUNCTION MOile U.S. Patent Jun. 17, 2008 Sheet 4 of 5 US 7,387,018 B2 8x10 5 x 4. d 3. 3. 2 S} ido 1so 260 250 Frequency, Hz FG. 4A o'. 50 100 150 200 25 Frequency, hiz FIG. 4B U.S. Patent Jun. 17, 2008 Sheet 5 of 5 US 7,387,018 B2 32 Output knock signa 338 - - Convert knock signat to a digital signal 33 Generate signature frequency signal based on Fif analysis of digitat Siga 3:30 alteroise from signature frequency signal 38 is frequency components withi; a frequency threshoid range? 38 Set DW. Maifunction Flag to FALSE Set OVW. Maifurctic Flag to RUE US 7,387,018 B2 1. 2 DISCRETE VARIABLE VALVE LIFT powertrain, compromises are made to provide the best overall DAGNOSTIC SYSTEMS AND METHODS (based on load regimes) performance. Performance metrics may include specific torque and or fuel consumption. At these FIELD part-load operating conditions a significant amount of work is required to throttle the engine to insure that the properamount The present disclosure relates to vehicle diagnostic sys of air into the engine to meet the desired road load. tems and more specifically to diagnostic systems that detect A variable lift valvetrain can be described as one that has malfunctions of components in discrete variable lift val the capability of selecting multiple profiles (with variable Vetrains of internal combustion engines. duration and lift capability) associated with each intake and or 10 exhaust valve(s). These profiles may be optimized for various BACKGROUND load regimes and are specifically chosen to minimize the amount of work required for the gas exchange process and or Common modes of vehicular transportation may include to support multiple combustion modes. internal combustion engines that generate drive torque based A discrete variable valve lift (DWL) system enables the on a two or four stroke cycle. These internal combustion 15 engine to operate on more than one intake and or exhaust engines typically have a poppet valve arrangement to facili valve lift schedule. More specifically, a DVVL engine system tate the induction and Subsequent exhaust of combusted air switches between different valve lift schedules based on the and fuel. desired load of the engine. This has been shown to minimize For example, engines can operate based on the Otto air pumping losses of the engine and or to Support multiple standard thermodynamic cycle with real working fluids. The combustion modes. engine includes a poppet valve system coupled to a slider A malfunction of a DVVL engine system may occur when crank mechanism that forms variable Volume in the rotational a component of the DVVL system fails to change to a differ domain. A piston is stationary at the top of its travel (Top Dead ent valve schedule on command. For example, a malfunction Center TDC) and begins to travel downward. An intake may occur when a switchable roller finger follower (SRFF) of valve is selectively opened such that air can be inducted into 25 the DVVL system switches from a low-lift (LL) valve sched the cylinder by the downwardly moving piston. During the ule to a high-lift (HL) valve schedule thus causing one or induction process the inducted air mixes with a predeter more of the valves to fail to switch from the LL schedule to the mined amount of fuel to form a combustible mixture. The HL schedule. intake valve closes at the bottom of the piston's cyclical travel (Bottom Dead Center BDC). The piston reverses direction 30 and then travels upward. The fuel-air mixture is compressed SUMMARY within the cylinders and is combusted when appropriate. Accordingly, a diagnostic system for a discrete variable Once at TDC, the piston reverses direction. Pressure rise valve lift system of an internal combustion engine is pro during the quasi-fixed Volume combustion process acts over vided. The system includes: a Fast Fourier Transform (FFT) the area of the piston and creates a differential force (this can 35 module that generates a frequency content signal based on a be described as boundary work). This force is transmitted via FFT method and a valve impact sensor signal; and a malfunc the slider to the cranktrain. When coupled to a moment arm, tion module that selectively diagnoses a malfunction of a this force forms motive torque. Once at BDC the piston stops discrete variable valve lift system based on the frequency and reverses direction. An exhaust valve is selectively opened content signal. (specifically the timing and lift) to allow the combustion 40 products to be expelled from the cylinders by the upwardly In other features, a method of diagnosing a discrete vari able valve lift (DWL) system of an internal combustion moving piston. Once at TDC, the exhaust valve closes and the engine is provided. The method includes, receiving an impact intake valve opens. The piston reverses direction and the signal indicating an impact of a valve closing event; perform mechanical cycle begins anew. ing a FFT analysis on the valve signal to generate a frequency The rotation of a camshaft regulates the opening and clos 45 ing of the intake and exhaust valves. On a multi-cylinder signature signal; and diagnosing a malfunction of the DVVL engine, the camshaft includes a plurality of cam lobes (typi system based on the frequency signature signal. cally one for each valve) that are affixed to the camshaft. The Further areas of applicability of the present disclosure will profiles of the cam lobes determine the profile of the valve lift become apparent from the detailed description provided here and are kinematic-ally related by the geometry of the val 50 inafter. It should be understood that the detailed description Vetrain. Important parameters associated with valve lift pro and specific examples, while indicating the preferred embodi files include the period that the valve is open (duration) as ment of the disclosure, are intended for purposes of illustra well as the magnitude that the valve opens (lift). In the tion only and are not intended to limit the scope of the dis mechanical configuration described herein, these two param closure. eters have significant influence on the gas exchange processes 55 of ICEs. BRIEF DESCRIPTION OF THE DRAWINGS Manufacturers typically incorporate a fixed valve lift schedule for the engine due to design complexity, cost, and The present disclosure will become more fully understood durability constraints. From a gas exchange process perspec from the detailed description and the accompanying draw tive, a fixed valve lift schedule may not be optimal for all 60 ings, wherein: engine operating conditions encountered. For example, dur FIG. 1 is a functional block diagram of an exemplary six ing steady-state highway travel a vehicle may typically cylinder engine including a discrete variable valve lift (OWL) require a motive torque that is significantly less than the full system; capacity of the powertrain. In typical fixed duration and lift FIG. 2A illustrates an exemplary valve lift schedule of the valvetrain systems, this demanded load is usually meet via 65 OWL engine operating in high lift (HL) mode: throttling of the engine. When a single (exhaust and intake) FIG. 2B illustrates an exemplary valve lift schedule DVVL valve profile (duration and lift) are chosen for a particular engine operating in HL mode and a single valve lift failure; US 7,387,018 B2 3 4 FIG.
Details
-
File Typepdf
-
Upload Time-
-
Content LanguagesEnglish
-
Upload UserAnonymous/Not logged-in
-
File Pages10 Page
-
File Size-