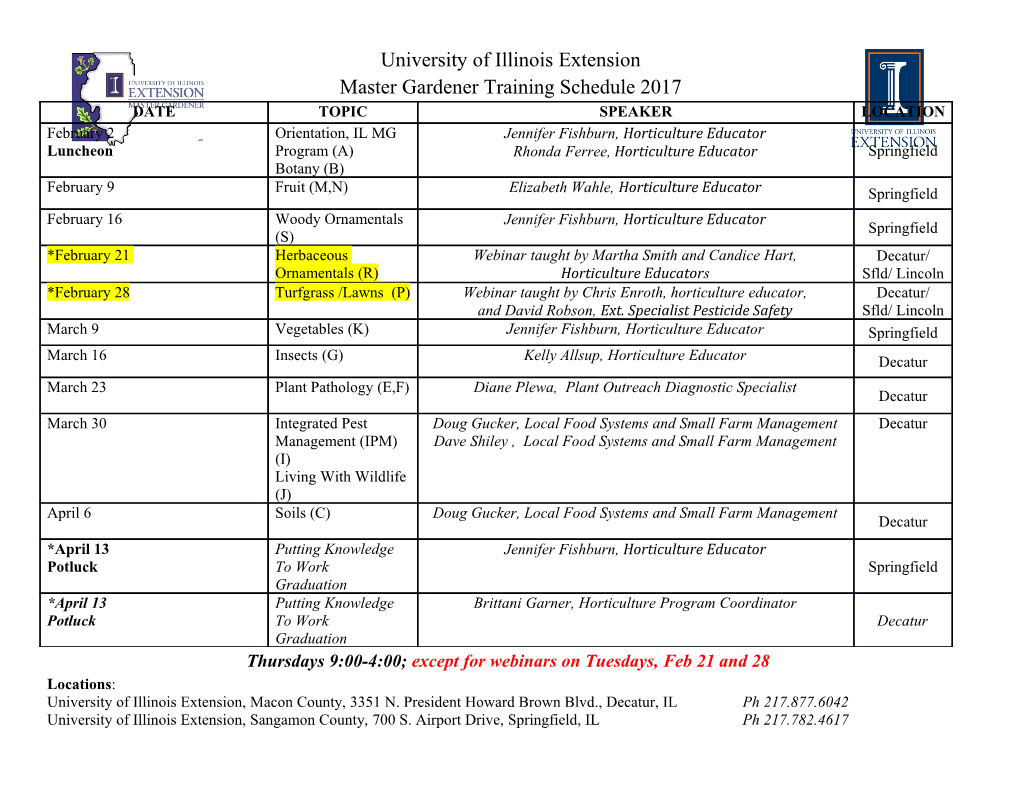
Advances in Science and Technology Received: 2019.10.18 Revised: 2019.11.15 Research Journal Accepted: 2019.11.30 Volume 13, Issue 4, December 2019, pages 270–275 Available online: 2019.12.21 https://doi.org/10.12913/22998624/111694 An Optimization Study for Bridge Design of a Porthole Extrusion Die Önder Ayer1*, Burcu Gizem Özmen2, İsmail Karakaya2 1 Trakya University, Muhendislik Fakultesi Makina Muhendisligi Bolumu, 22100, Edirne, Turkey 2 “eksenAL” Aluminum Extrusion Die Factory, Istanbul, Turkey * Corresponding author’s e-mail: [email protected] ABSTRACT In this study, a porthole die extrusion simulation was carried out for a box profile by using HyperXtrude Inspire Extrude Metal 2019 which is a FEM based software. Aluminum AA6063 material was the billet material, tempera- ture of the billet was 450 °C and ram speed was selected as 5 mm/sec. The die design was obtained according to the shape of the bridges of the porthole die. Finally, the design optimization was achieved by analyzing FEM results. It was obtained that the dies which have curved bridges offer optimum process conditions. Keywords: Porthole Die Extrusion, FEM, Aluminum 6063, stress distribution, die deflection. INTRODUCTION more often in the last decade. The goal of using FEM simulations is simulations is to predict the Aluminum is the second most plentiful me- temperature distribution, exit velocity of extruded tallic element and has great attention from many product, material flow and the tool deformation. field of industry because of its superior proper- Jie et al. [2] carried out FEM simulations and ties such as recyclability, corrosion resistance, experiments for porthole die to optimize mate- high specific strength and especially for its light rial flow. He et al. [3] investigated the effects of weight. The aluminum has been used increasing- die pockets in the porthole die on the metal flow, ly in the last two decades for various industries. temperature distribution and the extrusion load by Thin-walled with multi-cavity profiles, intricate using two different multi-hole porthole dies with shapes, large cross-sections, with lower weighted and without pockets in lower die. Engelhardt et products were required mostly by aerospace, au- al. [4] used Finite Element method to optimize the tomotive and transportation industries. Hot extru- extrusion process for multi-hole hollow profile sion method is a useful tool to obtain complicated extrusion. They carried out simulations by Hyper- profiles with high productivity and porthole dies Xtrude software for optimum material flow. Yu are generally preferred for this purpose. There are et al. [5] investigated different types of welding various studies relating with extrusion process us- defects from millimeter scale to nanometer scale ing porthole dies. for porthole die extrusion for different extrusion Qamar et al. [1] studied possible die defects die structures and process parameters. Yu et al. and die correction operations for metal extrusion. [6–9] investigated the relation of leg design with They proposed a list of definitions for die defects welding chamber of the porthole die. They used and their preventive measures and die correction different die parameters to observe welding qual- methods. The design phase is generally based on a ity of extruded profiles by means of microstruc- trial and error method and which is an unefficient ture observation, tensile test and fracture analysis. way in terms of time and the amount of scrap. However, there are still empty areas to be studied In order to eliminate trial and error method, finite in terms of die design for more efficient extrusion element based softwares have been getting used process and better product quality. 270 Advances in Science and Technology Research Journal Vol. 13(4), 2019 MATERIAL AND METHODS Extrusion is a process where the material is pushed through a die to obtain a desired a shape The FEM simulation was carried out for stan- which is generally complicated. Manufacturers dard box profile by using porthole extrusion die prefer the hot extrusion method for porthole dies. with the support of HyperXtrude software. In Figure 1 shows the view of a porthole die with its this study, it was aimed to propose an optimum dimensions. It can be seen from the figure that the leg design of a porthole die for better material upper die part has 4 portholes. The bridge designs flow. The welding quality is highly related with of four different porthole die were given in Figure material flow behavior and solid state bonding 2 in detail. The material is forced to flow into port- process. The macro voids are reffered to material holes around the porthole legs to obtain desired flow when microvoids are referred to insufficient shape. The portholes are used to balance the metal solid state bonding. Consequently, the optimum flow with the suitable distribution. The number of design will lead longer service life for the die and portholes determine the extrusion load and mate- will prevent wasting resources and result more ef- rial flow. When the profile is so complicated, the ficient production cycle. number of the porthole is important because of the In the simulations, a standard box profile was obtaining better material flow and better longitudi- used as exit profile with the extrusion ratio of 127. nal and transverse weld quality. Aluminum 6063 material was selected as a work- Four different bridge design were modelled and piece material and billet diameter was Ø220 mm simulated. The effect of the bridge design on materi- and billet length was 700 mm, butt length was al flow, die deflection, exit speed and temperature of selected as 25 mm. Billet temperature was set as the product and forming load were investigated. The 450 °C, die and container temperature was 430 °C angle and radius was changed comparing the initial and punch velocity was set to 5 mm/s. H13 type die design which has sharp corners. The detailed steel material was used as die material. The Cou- view for the design study was given in Figure 2. lomb friction model was selected for the FEM The FEM simulations were carried out for the model with the coefficient of 0.3 at the die bear- same process conditions but for different die de- ing zone. For more accurate results, the tetragonal signs. Results were analyzed to obtain optimum mesh distribution was applied to the model. bridge design for efficient extrusion process. Fig. 1. A view of a porthole die 271 Advances in Science and Technology Research Journal Vol. 13(4), 2019 Fig. 2. A view of design of porthole die bridges RESULTS AND DISCUSSIONS accuracy of the extruded profile. When the deflec- tion is higher than the permissible tolerances, the The model of the study was built in a com- dimensions of the final product could be different mercial CAD software and it was then uploaded that the desired shape which means that the product to HyperXtrude Inspire Extrude Metal 2019. The is scrapped. It could be seen from the figures that die calculated results were given in Figures 3–8. set I gives the highest deflection comparing to other The Figure 3 shows the stress distribution die sets. The deflection is especially high at the man- results of the given models. The stress distribu- drel section. The deflection decreases when the ra- tion is an important parameter for determining dius and angle is implemented to the design hence, the service life of the die because of affecting the the deflection on the mandrel is related with the de- wear of a die. The service life of a die is defined sign of the bridge of the die. It could be observed that according to the amount of extruded material in the deflection value is in the range of 1.48–1.98·10-4 tons. The low and homogenous stress distribution mm. The deflection distribution for the die set ofII, promises longer service life. III and IV is different comparing to the initial de- The die sets are numbered from I to IV with sign where the deflection is accumulated only on the roman letters. It can be seen from the figure that the nose of the mandrel section. highest stress values were obtained at die set I. The The temperature of the profile is important for maximum stress value was calculated about 122.8 the dimensional accuracy and mechanical properties MPa for the die set I and die set IV gives the mini- of the product. Therefore, it is necessary to predict mum stress value which is calculated as 85.2 MPa. the exit temperature of the profile. The profile tem- It is also observed that stress at the zone A perature distribution was given in Figure 5. The exit for die set I was calculated between 54–82 MPa temperature was calculated as 555 °C on the profile when other die sets (II, III and IV) have lower and it is clearly seen that temperature is uniform at values. The calculated stress range was between the every point of the profile. Initial temperature was 41–68 MPa for die designs II, III and IV at zone 450 °C and its value decreased because of the heat B that is significantly lower than that of the die I. transfer between billet and container hence the bil- Stress distribution Zone B also shows similarity let temperature was calculated about 442 °C at the for the die designs of II, III and IV. It could be beginning of the process. The temperature of the observed that the stress at zone C is highly con- AA6063 material reached about 555 °C because of centrated on very small area for die set I and its the frictional and stress conditions.
Details
-
File Typepdf
-
Upload Time-
-
Content LanguagesEnglish
-
Upload UserAnonymous/Not logged-in
-
File Pages6 Page
-
File Size-