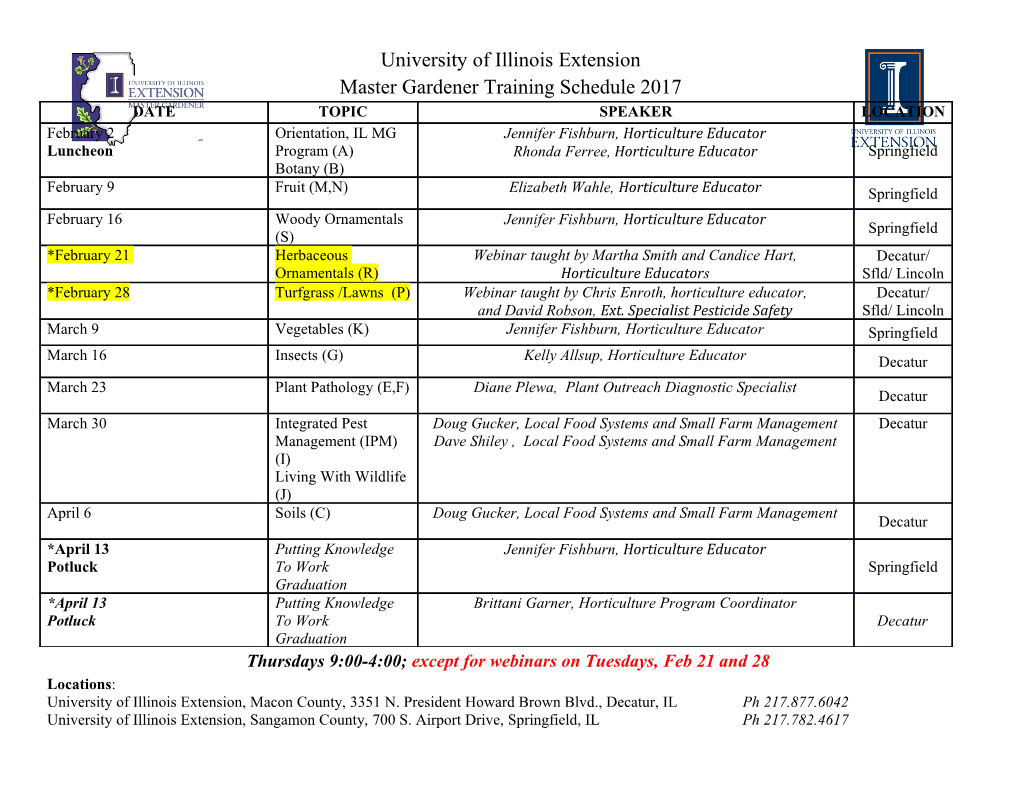
View metadata, citation and similar papers at core.ac.uk brought to you by CORE provided by Covenant Journals (Covenant University) Covenant Journal of Engineering Technology (CJET) Vol. 1, No. 1, March 2018 An Open Access Journal Available Online Analysis and Application of Natural Fiber Reinforced Polyester Composites to Automobile Fender Benjamin Ufuoma Oreko1*, Omonigho B. Otanocha1, Eyere Emagbere1, Christopher Chukwutoo Ihueze2 1Dept. of Mechanical Engineering, Federal University of Petroleum Resources, Effurun, Delta State, Nigeria 2Dept. of Industrial & Production Engineering, Nnamdi Azikiwe University, Awka, Anambra State, Nigeria Abstract – In Nigeria, little attention has been given to the analyses and applications of natural fibers for automobile body parts production. Hence in this work, an attempt is made to evaluate the compressive and impact strength of plantain fiber reinforced polyester composites (PFRC) and to develop an automobile fender using plantain fiber reinforced polyester composites. The PFRC automobile fender was constructed using the hand lay-up technique. The method adopted to achieve the PFRC fender involved fiber extraction, fiber surface treatment, laminates development for impact and compressive test experiment and the development of automobile fender. Experimental investigations for compressive and impact tests were carried out on the laminates which were prepared according to the ASTM D256 and ASTM D1621 standards, respectively. The impact strength result of the PFRC with volume fraction 0.25 and 0.3 was 12.22J/m2 and 12.83J/m2, respectively. The compressive strength, shear stress and resultant stress results of PFRC laminates with volume fraction 0.25 and 0.3 were 62.52MPa, 31.26MPa, 69.99MPa and 68.98MPa, 34.49MPa, 77.12MPa, respectively. From the results, it was observed that the strength of the plantain fiber reinforced polyester composites depend on the fiber volume fraction. The constructed automobile fender was simulated in a Solidworks software environment and was found that the edges, especially the circular part of the automobile fender have high stress concentrations. The production of the automobile fender using PFRC was done at low cost. Keywords: Plantain fiber, polyester, volume fraction, automobile fender, product development 1 Benjamin U. Oreko, et al CJET Vol.1 No.1, March. 2018 (Special Edition) 1-12 I. Introduction hydroxide, and mold. Plantain The state of the art in material pseudostems were locally sourced technology advocates for from fully matured plantain environmental-friendly materials for plantation, located at Agbarho, Delta engineering applications. In recent state, Nigeria. The resins and other times, advances in natural fibers chemicals were purchased at Warri syntheses have made the application main market, Delta State, Nigeria. of these materials suitable for The fibers form the reinforcement in automobile parts and body work. the composites. Methyl Ethyl Ketone Plantain fibers possess moderately Peroxide (MEKP) was used as a high specific strength and stiffness catalyst while cobalt naphthenate and can be used as reinforcement in was used as an accelerator. The polymeric matrix to make useful release agent was debonding wax. composite materials. Natural fibers The inorganic filler was calcium have been used due to their trioxocarbonate (IV). advantages such as low density, low cost, acceptable specific strength to Equipment/Tools. The equipment weight ratio, and biodegradability [1, /tools used includes; Paintbrush, Pair 2]. In Nigeria, there are abundant of scissors, Hand gloves, rollers, natural fibers that could be obtained grinding and filing machine. from plant, such as plantain, bamboo, raffia, coir fibers, etc. An attempt Methods. The method adopted had been made by several includes; the extraction and treatment researchers to optimize some (Mercerization) of plantain fibers, mechanical properties such as tensile experimental analysis of the impact strength, impact strength, flexural and compressive strength. and hardness of plantain fiber as reinforcement in polymer composites Extraction and Treatment of [3 - 8]. However, little attention has PFRC. The plantain pseudo stems been given to the application of were soaked in water for a period of plantain fibers for automobile body four weeks and were manually parts production, especially in extracted (retting method, figure 1). Nigeria. To remove the lignin (de- lignification), pectin and others non- II. Materials and Methods fibrous materials, the plantain fibers Materials Selection. The materials were subjected to surface chemical employed in this study include modification by mercerization plantain pseudostem fibers, polyester (soaked in NaOH solution of 5% resins, accelerator (Cobalt concentration for 60 minutes) in naphthenate), catalyst (Methyl ethyl Figure 2. Thereafter, washed with ketone peroxide), inorganic filler distilled water and sun-dried as (Calcium trioxocarbonate IV), shown in Figure 3 and 4. release agent (wax), sodium 2 Benjamin U. Oreko, et al CJET Vol.1 No.1, March. 2018 (Special Edition) 1-12 Fig.1: Manual extraction of plantain fibers Fig. 2: Plantain fiber mercerization Fig.3 Plantain fibers washed with distilled water Fig.4 Extracted plantain fibers The chemical reaction for the fiber (4) and sodium hydroxide solution could be express as; (5) (1) Also, (6) Volume Fraction Analysis. Applying (7) Archimedes principle to determine the volume fraction of the plantain Hence, fraction of the applied force fibers, we have absorbed by the fibers in the composites could be expressed as; = (2) (8) Volume of composite, Stress and Strain Analysis. The (3) force applied (load) on the composite (Fc) is shared by both the fiber and 3 Benjamin U. Oreko, et al CJET Vol.1 No.1, March. 2018 (Special Edition) 1-12 the matrix. Let the forces on the fiber shear stress will be maximum on the 0 0 and the matrix be FF and FM. planes inclined at 45 and 135 . Therefore, Hence, (9) (20) The strain, ϵ is the same in the fiber Therefore, the magnitudes of the (ϵF) and the matrix (ϵM) and is equal shear stress is half of the to the composite strain (ϵC.). Hence, compressive, hence the resultant stress, could be obtained from the (10) relation; And let, Modulus of elasticity Е, of the fiber = E and matrix = E f m. Hence, Experimental Evaluation. Impact (11) and compressive strength were evaluated. (12) Impact Test. The impact test specimens of plantain fiber Thus, (13) reinforced polyester composites were prepared according to ASTM D256. (14) The dimensions of the test samples were 63.5 × 12.7 × 3.2 mm and it (15) was v-notched (2mm) deep with the aid of a triangular file, at an angle of (16) 450 with 0.25mm radius along the So, (17) base. Five (5) samples each of Shear Stress Analysis. It is expected volume fraction 0.25 and 0.3 that the fender would experience respectively, were prepared at a shear stress other than direct stresses curing pressure of 30N/mm2 and such as compression, when in 250C temperature. The test was service. From [9], Normal stress carried out in a charpy setup using could be expressed as; the Brooks impact testing machine. The energy required to break each sample was measured. The impact And shear or tangential stress; strength of the specimen was the energy absorbed per unit cross- 2 From equation (18), the normal stress sectional area at the notch (J/m ) and across the fender face will be it was determined using the formula: maximum when =1 or (22) or , hence, the face where, I = Impact strength (J/m2), K of the fender will carry the maximum = Energy required to break the direct stresses. Similarly, from specimen (J), A = cross-sectional equation (19), the shear stress across area (m2). the face of the fender would be maximum when = 1 or Compressive test. The compressive that is, the test specimen was prepared according to ASTM D1621 standard. Squared specimens of dimension 4 Benjamin U. Oreko, et al CJET Vol.1 No.1, March. 2018 (Special Edition) 1-12 5.2cm x 5.2 cm x 25.4mm were Development of Auto Fender Made prepared for five (5) samples of of Natural Composite Materials volume fraction 0.3 and 0.4, Selection. The matrix employed in respectively at a curing pressure of the construction of fender was 30N/mm2 and 250C temperature. The unsaturated polyester (mixed with compressive test experiment was cobalt naphthenate, and methyl ethyl performed using the Universal ketone peroxide, MEKP initiator). Testing Machine (UTM) which The methyl ethyl ketone peroxide act comprised of a digital load meter for as the catalyst or initiator, cobalt reading the applied load, a dial gauge naphthenate as an accelerator, along or extensometer for reading the with inorganic filler (calcium deflection. The force and trioxocarbonate IV, CaCo3) and deformation data were then recorded. ammonium chloride (NH4Cl) as The expression in equation (23) was curing agent were added to the used to determine the compressive unsaturated polyester resins. Hand strength of the specimen: layup technique was employed. First, Compressive stress, (23) a gel coat prepared from the resin was applied on the mold and then, = compressive strength, Pc = the matted plantain fibers were load/force, A= cross-section area placed on the gel coat. There after a sequential impregnation of fiber – (24) matrix (resin) ratio proportion of volume fraction 0.3 was employed until a thickness of 2.54mm was Simulation of the Fender. The obtained. The finished composite performance of the automobile fender was allowed to cure at a fender made of plantain fiber pressure 30N/mm2 and 250 Celsius, reinforced polyester composite was for 24 hours. Thereafter, the product simulated using Solidworks software, was de-molded and surface finish with the constraint that the fender techniques such as filing and was fixed at all edges and the forces spraying were done. or loads were applied on the entire surface of the fender. III. Results and Discussion The Impact test result shows that the J/m2. Plots of stress-strain for strength of the plantain fiber compression of PFRC with volume reinforced composite depends on the fraction 0.25 and 0.3 are shown in volume fraction.
Details
-
File Typepdf
-
Upload Time-
-
Content LanguagesEnglish
-
Upload UserAnonymous/Not logged-in
-
File Pages12 Page
-
File Size-